Robbie
UltimaDork
7/5/19 12:22 p.m.
I want to know all the things that have been outlawed by rule in different forms of Motorsports that are aero related. Usually, things are outlawed because they are too effective and give one team a giant advantage, or because they are downright dangerous. Aero fits both of these reasons and I can think of a few examples, but I'm curious to know what you all remember. Things like:
- wings should be connected to the body, not the wheels.
- ground effects tunnels outlawed in f1
Could be anything outlawed from any type of Motorsports. Go!
Do you want to get as minute as the dictated leading edge radius on front wing end plates. That was due to some drivers (Michael Andretti) using the end plate to cut competitors tires. The Tyrell 6 wheeled car was an attempt to reduce the tire effective frontal area near the front wings. Limitations on bodywork to tire clearances does basically the same thing. Aerotubing used for exposed structural components is generally dis-allowed for cost,but it is more likely that the analysis to make sure it is used properly (failure modes) is more difficult that square or round section. Mandating steel over carbon for th same reasons, when the carbon allows greater detail design variation.
I could go on for a while.
I will try to make a more logical list over beers this evening.
Porsche 917 (?) rear diffuser tunnels were so tall the drive shaft went through them.
Tunnels being single element, how far forward they start, etc.
Rear wings having one/two elements maximum.
Limiting things to Non-moveable surfaces (outside of DRS... although Toyota got away with it at LeMans a couple years ago)
”blowing” of any kind.
sucker-car
I’ve been mentally toying around with the idea of a Tyrrel T34 (6 wheeler) for challenge, using go-cart wheels/tires... but you’d probably have to start with a Lotus Europa or a Fiat to get the front-end load and RWD setup to pull it off.
I might as well get this done.
Chaparral 2J
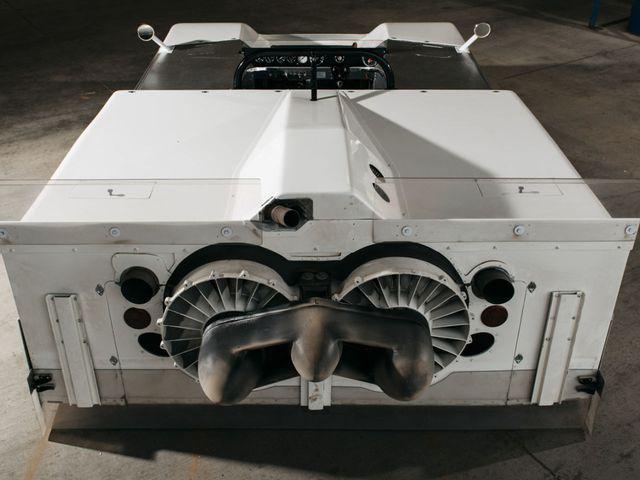
Floating Doc said:
I might as well get this done.
Chaparral 2J
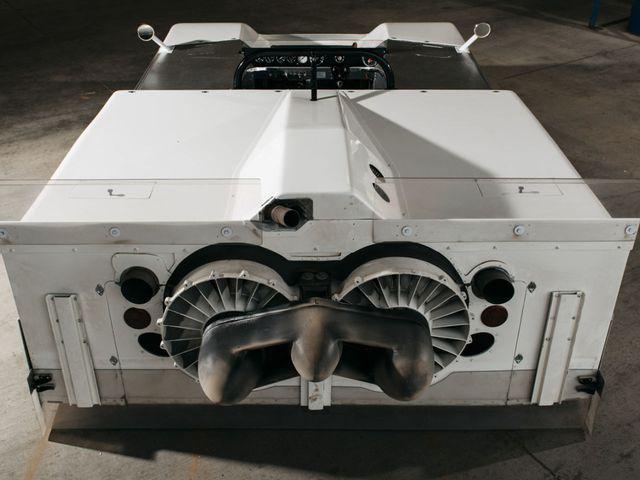
Better example because it actually won a race. Technically, it won every race it entered. I'm not sure the Chaparral ever finished one.
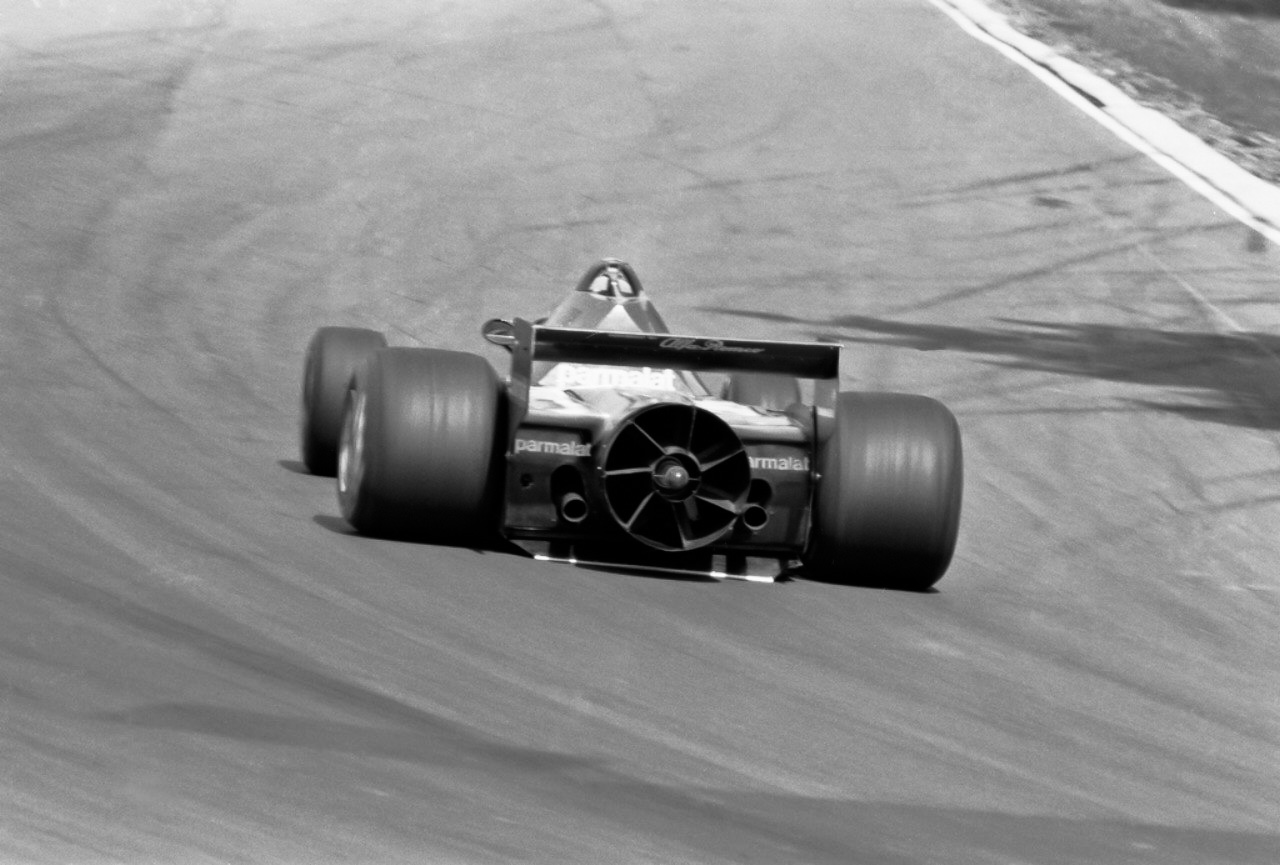
stafford1500 said:
I could go on for a while.
Hands up if you want stafford1500 to go on for as long as he can.
Robbie
UltimaDork
7/5/19 1:54 p.m.
Keith Tanner said:
stafford1500 said:
I could go on for a while.
Hands up if you want stafford1500 to go on for as long as he can.
I'm waiving both hands in the air like an idiot.
Keith Tanner said:
stafford1500 said:
I could go on for a while.
Hands up if you want stafford1500 to go on for as long as he can.
Since I can only give one thumbs up.






ShawnG
PowerDork
7/5/19 2:01 p.m.
The Brabham fan car was never banned. It was protested and found to be legal.
They agreed to stop running it.
Both hands up! It's a shame there's no resource for all the accumulated data on "outlawed" designs.
sleepyhead the buffalo said:
Porsche 917 (?) rear diffuser tunnels were so tall the drive shaft went through them.
Tunnels being single element, how far forward they start, etc.
That was the 956/962 of the group C era. 917 was pre underfloor aero and was an aerodynamic, almost undrivable disaster until JWA got their hands on it.
ShawnG
PowerDork
7/5/19 11:08 p.m.
The F-Duct in the McLaren cars...
What about the Lotus 88 twin chassis F1 car to try and get around the stupidly high wheel rates needed for skirted ground effect F1 cars. The springs were so stiff with the damper technology of the time it was beating up the drivers. It had one ‘chassis’ mounting the aero and reacting through the suspension with a second ‘chassis’ softly sprung within it for the driver module. It was outlawed before ever racing as it was deemed to contravene the movable aerodynamic rule.
Adrian's comment on the twin chassis'd Lotus 88 starts of the conversation about moveable aerodynamics. Let see, besides the F1 series having discrete components that are only allowed to move at specific locations and under specific conditions (following distance) there are no professional wheel to wheel series allowing moveable aero. Allowed and actively happening are two different things however. There was some discussion recently (last few years) over LeMans prototypes using interesting wing mounting scenarios to reduce wing angle at speed thtt seemed to be effective. Aero-elasticity is a real thing. next time you are on a commercial airliner, watch the wings load and lift the tips as you make your take off roll (747 wing tips move something like 8 feet from static to fully loaded). The same thing can happen on car parts. Hoods can blow/suck down at speed if not properly braced, but you may want it to change shape since the effect can change the pressure profile across the front of the car, which WILL affect what happens behind it and MAY affect what is happening in front of it. Simple moveable aero devices could be spring loaded dive planes (all the downforce at low speed and reduced drag penalties at higher speed).Pretty much any area of a car or its components can be considered for moveable aero and/or active aero. I recall Keith Tanner setup a DRS style wing for one of his cars. Simple and effective. More and more modern sports cars are getting similar features, but with more sophisticated controls. Wings and splitters that deploy based on car speed, brake and cornering conditions. Ride height adjustments made with the same sorts of inputs. A few years ago one of the forum members had a Fiero he was running in Southern California, with a rear bumper mounted wing. He had concerns about how much it flexed back at speed. I noted that at high speed the aero load was likely held constant or reduced at best as the wing angle was reduced due to the drag load. That could be built into the wing mounts themselves if someone wanted to reduced drag at high speed tracks but still retain max downforce at lower speeds. I have seen this on IRL cars in the mid 2000's. Most sanctioning bodies try to limit this with static weights applied to spot it.
Moving on from moveable aero, what about those things that hold our tires to the car. The wheel can be a very dynamic component is car aero. Consider, most of the time the bottom of the tire is effective not moving with respect to the ground. The top of the tire is moving at ~twice the car speed (with respect to the ground). The wheel and brake can be turned into fan type pumps to pull pressure below the car down, creating downforce. The BBS wheel fans from the 80's sportscars made use of the effect with a really simple hubcap type design. I personally witnessed a wind tunnel test ~20years ago where something similar was done to a NASCAR style wheel by just adding wickers/gurneys to the spokes of a steel wheel and saw a 10% increase in downforce. The last decades F1 cars went the opposite direction, they used effectively hubcaps to control airflow around the wheel to promote more controlled flow to the back of the car/sidepods/rear wing. Since they were attached to the end of the spindle they did not rotate (thereby avoiding the moveable aero device rule) and aligned with the brake ducting to make sure the flow did what was needed. The same thing can be said for the old moon hub caps used by salt lake racers for decades, smoother is faster for those conditions.
On the smoother is faster idea, if you have lots of little edges and steps on otherwise smooth surafces (upper body especially, but underbody too) the effect is basically drag first. There may be some downforce or power benefit (depends on how it impacts the rest of the car) but drag is the primary impact. If you are allowed, taping body seams is a great way to reduce the drag, since you are removing the extra work the air has to go through to get past the car. Rolling into and back out of every little crevice around the car takes energy. The flow may not even come back out of the same place it entered a body seam. Think about door seams, the pressure near a windshield is reasonbly higher than near the rocker. If air enters the area below a door/fender seam at the windshield it is very likely to exit closer to the rocker since the wake of the front tire is a fairly low pressure area.
Wow, how that for some stream of consciousness writing. It got long quick and only scraped the surface of POTENTIALLY illegal aero stuff. I will mrite some more shortly, need more cooffe this morning...
In reply to stafford1500 :
Good points. Also recall the ‘Red Bull’ rule mandating a maximum deflection of the front wing. At high speeds their front wing was flexing so much, it got close enough to the ground to lose effectiveness at high speed thus reducing drag on the straights. Most of the top teams have had issues with and run afoul of that rule over the last few years as they all try to brush up against the bleeding edge of legality.
Going to way back. At LeMans in the 50s Jaguar were the first company to race disc brakes. In an effort to keep up the Mercedes cars had a massive air brake that deployed when they hit the brakes at the end of the Mulsan straight as they were still running drum brakes. Very effective, very quickly band.
Round Two:
As I sit here I am wearing a shirt with a picture of a sucker car on it. The idea of using a powered fan to reduce pressure under a car is similar to the wheel fans mentioned earlier, but with possibly more effectiveness. The Chapparal sucker car ran a separate engine (so did the Challenge Corvette sucker car) to reduce pressure below the car. The Alfa powered Brabbham BT46 used the engine and ran the fan off the cam drive. A seperate power source gives the advantage of being able to control how much and when you want the extra suction. An engine driven fan changes the suction with engine speed and gear. That makes for a much less consistent downforce trend.
Similarly, exhaust blowing does something akin to suction fans but at least one magnitude less powerfully. If the exhaust can be directed to the top of diffuser tunnels or the underside of a wing, the energy of the hot exhaust can help drive those aero devices to higher efficiencies. It all comes down to energy balance. Air can only stay attached to high pressure gradient surfaces for so long before it gets tripped up. The extra energy from exhaust blowing can add some extra power since it still contains a significant amount of the fuel energy used to drive the wheels (mostly as heat).
Comparing back to the sucker cars and exhaust blowing, one way of getting some of that effect (again a fraction of the efficiency) is skirts. SCCA does not allow skirts that touch the ground, but getting them to run near the ground is a significant downforce benefit over nothing. The idea is that the air has to work much harder to go around the sharp edges of a skirt compared to the relative smooth rocker shapes on moist cars. On open wheel cars this car bee seen as sharp side pod bottom edges/floors. Some sportscar rules mandate a large radius at the rocker to reduce development in this area (also to provide lift off resistance if the get sideways).
Size is a major factor in every aero calculation. The frontal area or wing planform area drive forces in a very linear direction. The same shape, but 25% more frontal area gets you 25% more drag. Smokey Yunick's reduced scale NASCAR proved the point. Some say it was 7/8ths scale, some say it was 15/16ths scale, but the end result is it required less power to move through the air at the same speed, or more importantly, for the same power it could go faster.
Speaking of power, several series employ engine air inlet restrictors to balance power across multiple manufacturers. We started 2007 with the LeMans series Saleen S7 with two ~27mm inlet restrictors (for a 7 liter engine), because of some work that we did to overcome aero and handling challenges, we wound up with two ~24mm restrictors by the following season (and still managed to be just as, if not more comptetive). One way that has been used to overcome these restrictors is a mechanism that physically opens a bypass when the engine is running (a rally team in Europe). That was the reason some series went to the extreme of verifying the engine would stall if they plugged the inlet restrictors.
Allright, got lon-winded again.
Post up any other bits and pieces you think are banned and I will try to give some explanation of the reasoning behind them.
Adrian,
You hit on the active aero with the air brakes. High drag when you want/need it is easy. The loads are really big, so you have a lot of planning to make sure it works for the long term. Most folks think from the view of the car from the front/top/side, but aero-wise, they should really try to think about how the air is flowing along the body and then how to make it work for them. The flow along the side of a typical coupe/sedan rolls across the side of the hood from the windshield, down the door toward the rocker, then starts to come back up onto the trunk/deck. Same for hatches, but rolls up sooner across the doors.
Mercedes could have made a better mouse trap if the had employed their air brakes on the sides of the car as well as the truck/deck. The added benefit would have been a wider car that was harder to pass...
84FSP
SuperDork
7/7/19 10:36 a.m.
I think the F duct was one of the coolest recent ideas to be banned. It’s so simple and effective that I’m surprised is hasn’t trickled down to other racing/street cars by now.
Mclaren F duct goodness
ShawnG said:
The Brabham fan car was never banned. It was protested and found to be legal.
They agreed to stop running it.
Why did they agree to that?
ShawnG
PowerDork
7/7/19 1:26 p.m.
In reply to SnowMongoose :
Bernie Ecclestone was playing politics with the Constructors Association and they came to an agreement that Brabham would stop running the car because there was potential for things to get out of hand when everyone started doing it.
Steve, I watch races, time attack, etc. looking at aero stuff. I noticed the rear of the hoods on the C7R road race corvettes used in endurance racing lift at high speed a noticeable amount and wondered if it was intentional. It appears to be due to the increased pressure at the base of the windshield but.....movable aero? Any idea why they'd let (or want) the hood to rise up like that? Can see what I'm referring to in this video where we can see how much the hood rises compared to the angle of the center of windshield brace. https://www.youtube.com/watch?v=jaZM_rUdcOU
The reason the Brabham fan car used an engine driven fan rather than a separate constant speed or independently variable engine, other than the obvious weight, CofG and packaging concerns was that a separate engine would certainly have fallen afoul of the movable aerodynamic device rule. The reason it was deemed legal was that its ‘primary’ use was as a draw through radiator cooling fan. The percentage of airflow that went to ‘sucking’ was well under 10%. But don’t forget that you only need a couple of PSi to create hundreds of pounds of downforce.
As to why they needed to go down the sucker rout in the first place was because Bernie did a deal for the flat 12 Alfa engines instead of paying for the better V8 Cassie engines that were more flexible, if not powerful, and more importantly were a V so you could fit ground effect tunnels.
In reply to NOT A TA :
It may not be so much that the he hood trailing edge is being moved from the high pressure at the base of the windshield as much as the high speed/low pressure flow out of the radiator ducts. Those cars have the engine inlet in the nose (beside or above the radiator inlet duct. The air exiting the radiator duct at the hood has extra energy from the heat it brings along. That could result in a more significant suction at the back of the hood and being fairly wide and flat that panel would be harder to brace without a deep structure underneath.
The bigger question is how does it affect downstream flow at things like the rear wing???