GTXVette said:
Riddle me this.......So I have my airflow working for me and my rear wing is in Ground effect and placed Very Rearward and up or down ( I THINK HIGH WILL BE WORSE)would not say 150# Of Downforce also Lighten the front ? Having the rear wing Behind the CL of the rear wheels,Coming off the rear deck, Ya Know a Fulcrum Effect.
the Wing I want for the Challenge Vett Will be mounted on or Through the 'Halo' Bar (Topless Car) and Struts over the rear wheels, will be the Size if an Outlaw Sprint car, Without so Much Curve Aka Flatter, Looking For Sprint car Down force with out so much Drag,
In This Case A Giant Deflecter not really a Wing 'Cause It won't Fly.!
Mounting a downforce OR drag generating device outside of the wheel base will absolutely give the leverage/fulcrum effect you mentioned. The good news is most production cars are not downforce neutral at the front, so you are generating more total downforce and reducing the front effective grip at the tires. I say grip not downforce because the front is still doing its thing aero wise, just that it now has that lever connected to it, and the grip is a function of downforce an car weight for the most basic assumptions.
Sprint car wings will work great on a Challenge car, just keep in mind that the 'ground' effect it produces will be trying to pull up on the car below it, making it less effective than running it up higher out of ground effect. This is the Biplane effect, when a wing is pulling against the thing it is attached to. It always reduces the effectiveness. A Sprint car win will have quite a bit of drag, but at autocross speeds I would consider that drag to be zero. it is something, just not much. The bigger impact will probably be the height and weight of the wing. On the drag strip that drag will become significant at the top end of the run. It will be interesting to see how you sort out the end plates. Challenge rules dont limit the size of a wing, so if you have access to more than one Sprint car wing, run multiples, either doubled up width or one front/one rear.
I do have one of those Ricer Two wing Spoilers to Mount up /Out Front in 'Clean Air',
It Will be almost 2ft. From the 'Deck' to Halo Bar and you are Right I May Need to Be Higher, I mentioned it Will Be movible so Being Flatter I will lay it Back for the Drag Comp.
For the BIG wing, Still working on the air over Hydrolic W/Coil over and Air Shocks To Jack it into The air when I touch the brakes and Oh my The down Force, I'll Know How much When I See the compression of the Coil overs, I think Lo Riders use This Stuff
Starting To feel like I Want an Air Brake. Lol
If I build it up higher I may need to tilt the Nose down Rather than Raising the back for movement and It May take less force to move it there. We'll See
sleepyhead said:that first black shape is a really nicely shaped wing... or perhaps a really badly shaped car. and, of course, if it were a car, it'd be a lot closer to the ground... which means it can be a really inefficiently shaped wing and still make downforce...

Like many people, I thought the back end of the C5 looked dumb when it came out. Then I learned WHY it was shaped like that, and the engineer-nerd center of my brain thought it was the most beautiful car feature ever.
When I bought this c4 it had the Larry Shenoda Body kit installed , the rear piece has a Lip like Spoiler that extends straight Back like you See on a Drag car Very Cool Looking the front looks kinda c5-6 ish Also Kool.
The Cut off rear Is called a Kamm effect, Remember the old Can-Am Cars.
The C5 is not a Kamm style rear. Dr. Kamm (I assume) found that stubbing off a tail was just as good as a point as far as air was concerned. The C5, however, had a careful mix of curves and sharp edges that effectively turned the whole rear of the car into a wing. Maybe not a perfect wing, but it pulled air up and out from under the car with minimal extra drag or extraneous sticky-outy bits. That is why the top and sides end sharply without even tapering, while the rear face curves like that - the whole tail is designed to want to pull air from underneath and not the sides or top.
If I recall, this is a proper Kamm tail.
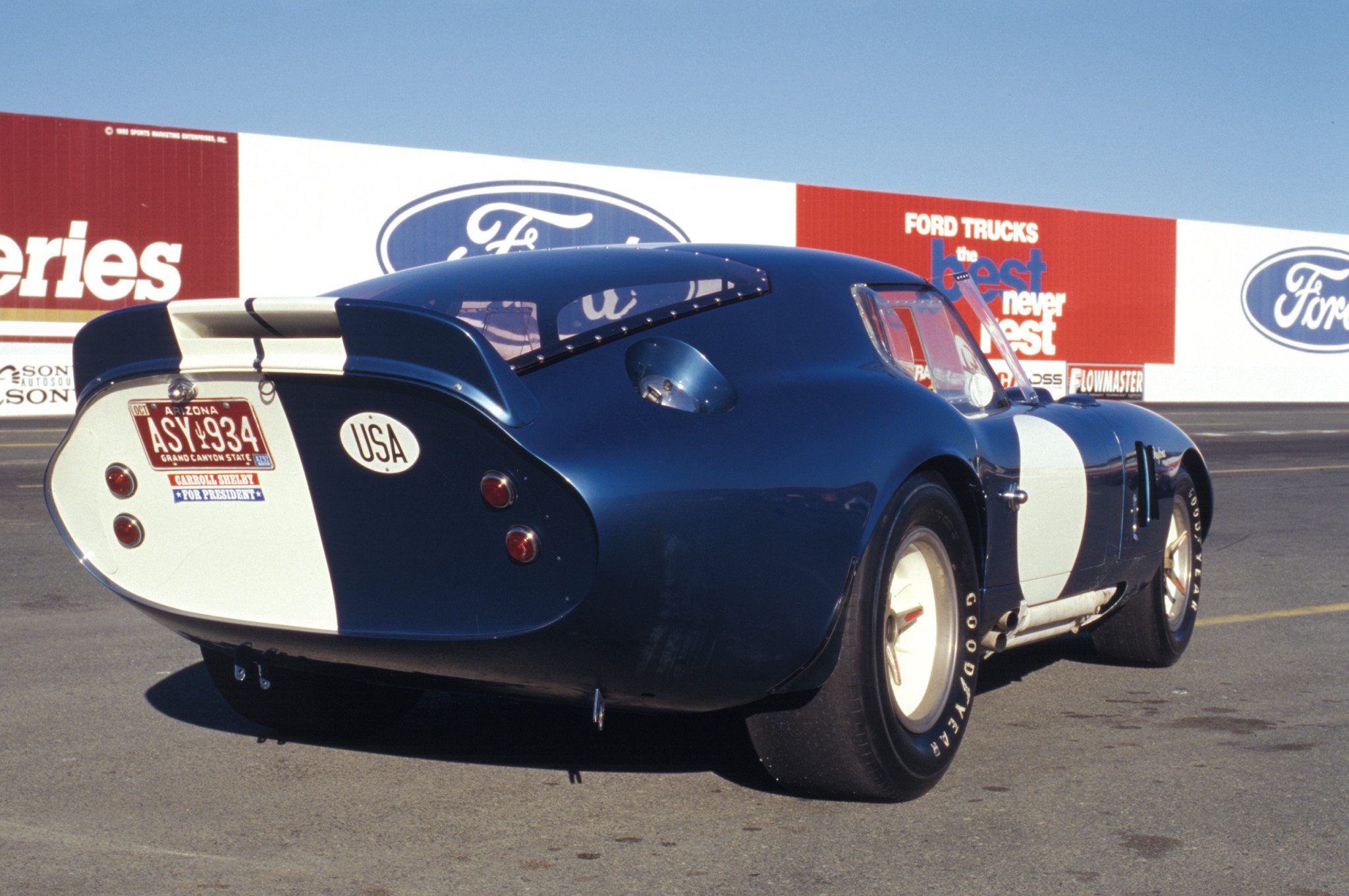
so, I thought I'd chime in here again...
talking about the MSHD, s1223, e423, and the cambered foils...
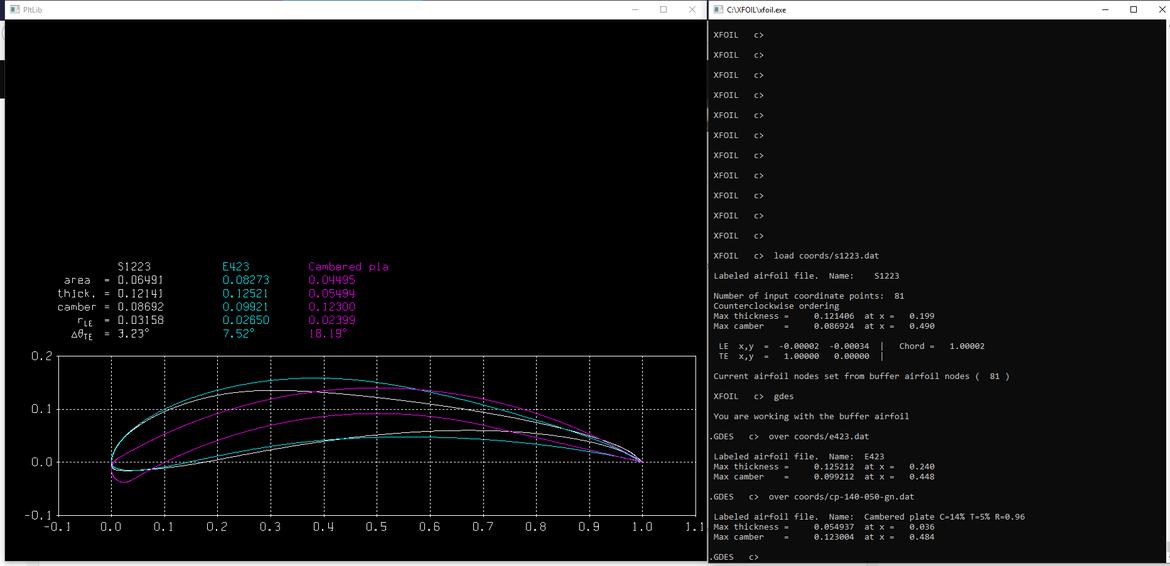
there's some interesting things to learn-from / think-bout from their "physical" properties, like maximum camber, and the x/c location of of that maximum camber.
I've been thinking more about how much a 3/4" thick piece of plywood supported across a ~6ft span is going to deflect with a distributed ~200lbf load. Maybe it'll be alright.
but the more I look at the s1223, the more I saw some potential... maybe you can see it after I did this:
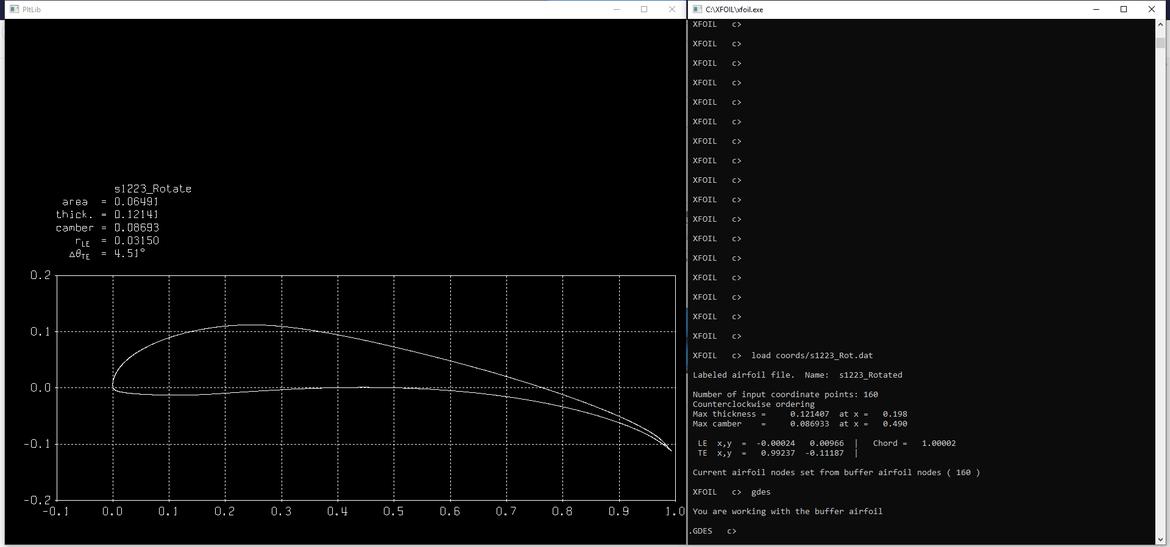
I'm still banging away at the calculations... and I'm going to try to get over the learning curve on JavaFoil... because I reckon multi-elements will benefit what I'm thinking about. But, I'm not there yet.
check out the Brock column in the recent classic motorsports mag for details on the kammback.
Invented by Baron Reinhard von Koenig-Fachsenfeld who was working under Dr. Wunibald Kamm at the time. Brock jokes that Kammback, Kamm tail and K-line were much easier for the media than "Koenig-Farchsenfeld-back tail".
In reply to sleepyhead :
I'm going to start playing with some of this software too if I can. I'm curious if putting more bend on the front of the foil and less at the rear would make it more effective. (keeping the constraint of 1 thickness of plywood)
I'm really not worried about strength right now, if I start breaking the plywood wings that will be a GOOD thing!
generally, we add camber through one of a couple of means... through increasing the "maximum camber" value (this is effectively a line that passes through the middle 50% of the foil at each step along the chord).
or, we can add a flap of some kind. Generally these are at the trailing edge, but can be at the leading edge... although Leading Edge Devices tend to be a smaller percentage of the chord, for a lot of reasons (i.e. Leading Edge devices will probably be in the 10% chord range, max; while trailing edge flaps could be 20-40%... depending on how you're counting).
another way of looking at flaps, is adding a second element... like a fowler flap. that adds both area and camber.
however, there are some details that might warrant some attention too. Like the fact that the leading edge shape, even on the 'cambered panel' is important. If we run some math, we'll see that the s1223 leading edge shape is substantially similar to an ellipse with minor axis of 11.2% of chord, and major axis of 25% of chord...
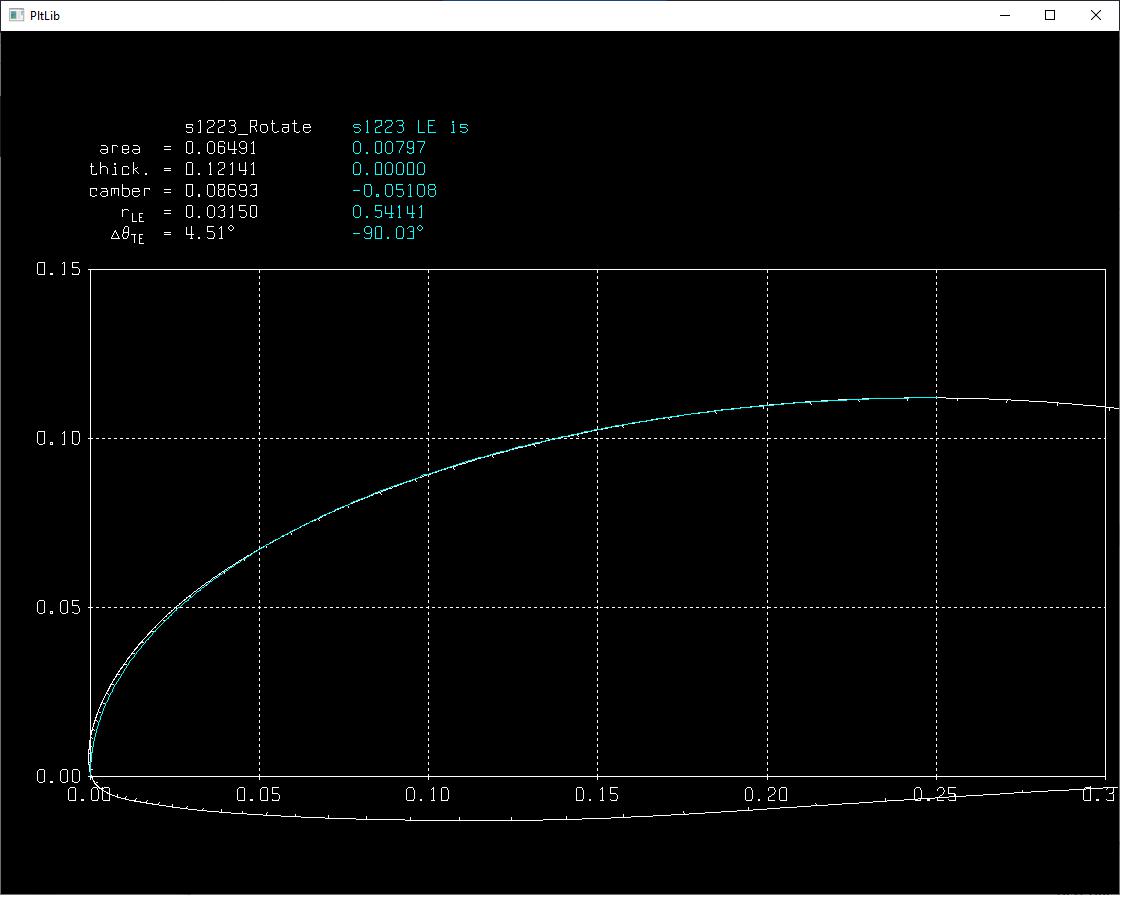
Loving this thread, but to play devil's advocate, convince me I'm wrong: Challenge cars benefit more from reducing drag than increasing downforce.
What's top speed during the autocross portion? 40, maybe 50 mph? And how many seconds are you at that speed? Compare the amount of downforce you can possibly generate at 50 mph to the amount of drag force you can reduce from 50 to 100+ mph. Aero forces become pretty significant above 50, and most Challenge cars will be above 50mph for at least 2/3 of their drag run. Keep in mind drag force (and therefore power required) squares with speed, which makes aero a pretty cheap power mod. Full disclosure I'm going full eco-modder this year.
Of course, why not both? Make it all quickly detachable. Drag kit + autoX kit.
it's a little easier to show how this applies if we use an ahem un-cambered, or flat plate, and give it some camber with a 20% flap, deflected 20deg...
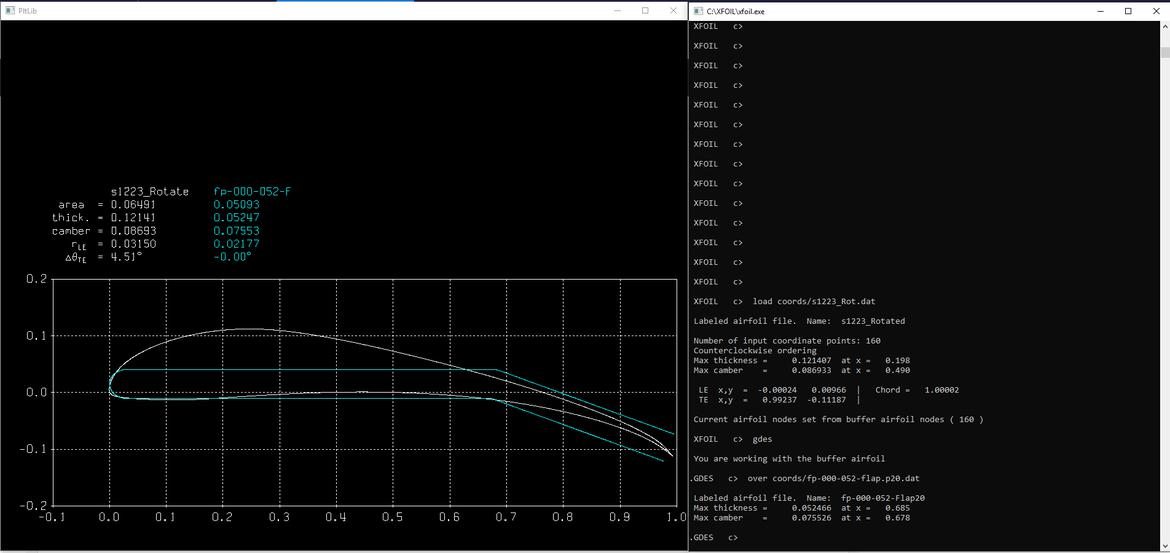
this base one has a circular leading edge... while the second one below, has an elliptical curve for the upper surface...
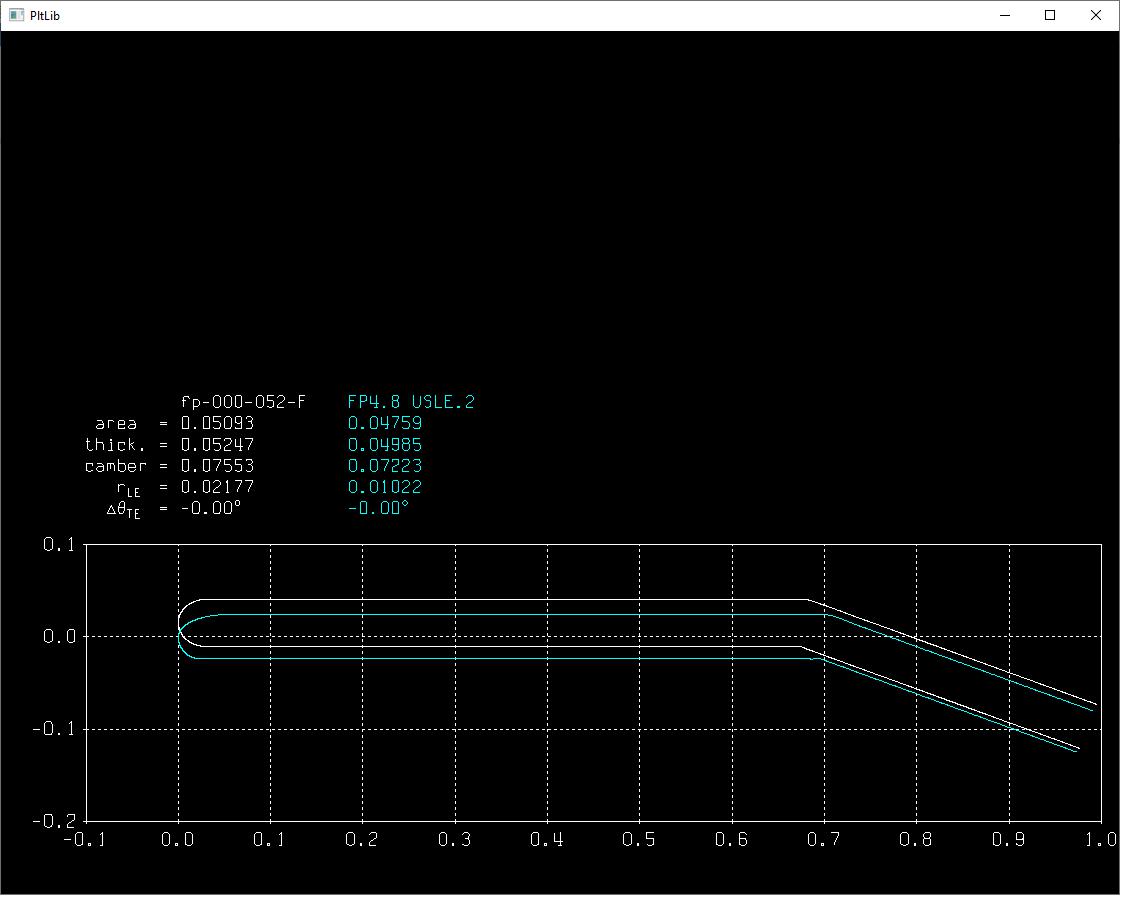
and here's what xfoil predicts at your upper speed:
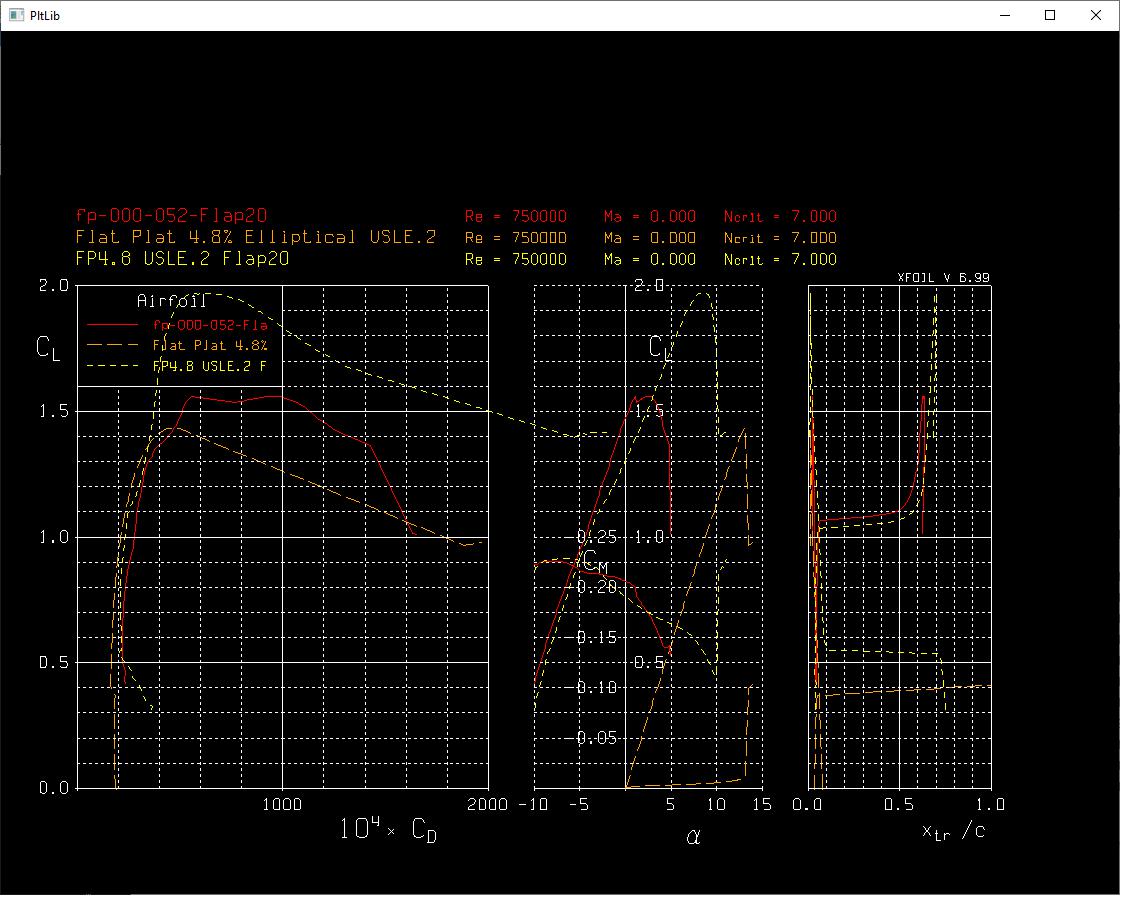
you can see that a flat plate, with no flap but the elliptical upper LE holds on pretty close to the flapped plate with a circular LE... and the elliptical upper LE with 20deg flap significantly outperforms the circular flapped plate.
now, I should probably go try and apply these ellipse to the cambered foils you found... although, that might be a non-trivial mathematical adventure 
maschinenbau said:
Of course, why not both? Make it all quickly detachable. Drag kit + autoX kit.
This is my assumption. Although, if you had a "tune-able" wing... where you could "dump" some camber... it might be beneficial in the drag. although, most OneLap cars that can, pull their wings before the drag event. ymmv
In reply to maschinenbau :
I did some calculations awhile ago and wish I could find them again. I bet I can re-create. But I feel like I had to make some pretty significant changes to Cd of the car in order to reduce the 1/4 mile time noticeably.
I have no idea how an addition of downforce changes your autox time or how to calculate an approximation*. BUT:
- you hit the nail on the head - remove draggy downforce before drags. (or, a super-adjustable spoiler could have autox mode and drag mode).
- I also want to do a matching splitter. Splitter can create downforce AND reduce drag if I understand correctly. But making a challenge car additionally tail-happy at speed doesn't sound like a good autox setup. So if we first develop a wing to keep the rear stable at speed and then add the splitter to match, we might end up with same drag AND more downforce overall.
*I'll try to approximate anyway: say you have a 30 second autox run, and a 3000 lbs car that can turn at .8 g with 0 downforce (that means its tires can produce 2400lbs of lateral force when turning only). Since you spend most of the autox in 2nd gear, let's assume at least 15 seconds is spent above 30 mph. Tire grip goes up with weight, but not at 1:1 ratio. So let's say you add 200 lbs of downforce but it really only adds 150lbs of grip. So now you have a car 3000 lbs car that can turn with 2550 lbs of force. That's .85 g. So, how far can you travel in 15 seconds at .8g? 0.545 miles. How long does it take to travel 0.545 miles at .85g? 14.55 seconds. So the 200lbs wing can save 0.5 seconds in a 30 second course. Note, this assumes you can build a wing that makes 200lbs of downforce at 30 mph. But I've been pretty conservative on my estimates so I think the improvement will be measurable.
also, according to this site: http://www.apexgarage.com/tech/horsepower_calc.shtml
a car with .35 Cd and 25 sqft frontal area requires 67 HP to maintain 100 MPH (ie at 100, the first 67 HP goes to keeping your car going and any surplus could be used to accelerate). The same car with a .3 Cd instead requires 59 HP to maintain 100 MPH.
Even if you had that whole 8 HP advantage over the entire drag run (but you would only have it at the very end, maybe you average 5-6) you're still not knocking off .5 seconds.
this site: http://www.wallaceracing.com/et-hp-mph.php
says that the ideal 14 second drag run in a 3000 lbs car takes 216 HP. If we add 8 HP and run it again at 3000 lbs it gives an ideal time of 13.83. So 0.17 seconds for reducing the Cd almost 20%.
That is very interesting...now I'm wondering if there is anywhere on the front of my car I'd feel comfortable putting 200 lbs lol
Rules don't say anything max envelope of the aero kit. If you can build a wing that generates 200 lbs, I bet you can build a frame that overhangs it a few feet ahead/behind the car for leverage
And precedent has already been set... check out page 23. This was just before my time on the team, but I remember sitting on that wing along with a few other freshmen.
http://www.wreckracing.gatech.edu/competition-cars/mazda-miata/
http://www.wreckracing.gatech.edu/wp-content/uploads/2019/03/2011-Miata-Build-Diary.pdf
Now you guys are starting to see the real-time effects instead of the theoretical downforce/drag. I have alluded to the lack of aero limitation in the Challenge rules and no one seems to have take it too seriously at the event so far. On the drag strip side of things, if you have sufficient power, some downforce may get you a better total time due to better traction early in the run (maybe allow you to use power adders earlier).
The next step is deformable aero. Let the wing lay back as the speeds increase to reduce drag and downforce. It may require a bit more engineering and testing, but the wing could be driven to it lowest drag position and still impart some donwforce for grip at the end of the 1/4 mile. Also dont loose sight of the ground effect I discussed earlier. The effects can become massive at low ground clearances.
Just because it shows some aero effects, and I like the photo:
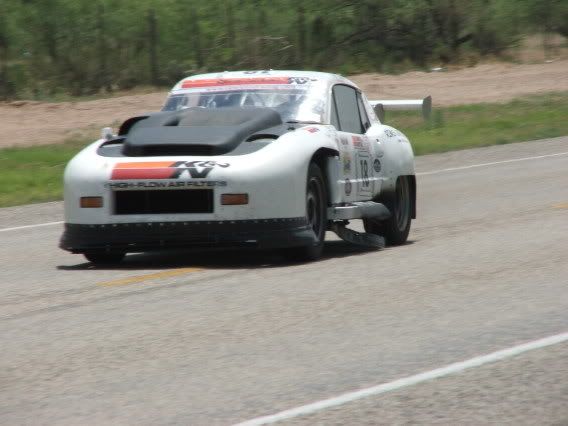
stafford1500 said:
Now you guys are starting to see the real-time effects instead of the theoretical downforce/drag. I have alluded to the lack of aero limitation in the Challenge rules and no one seems to have take it too seriously at the event so far. On the drag strip side of things, if you have sufficient power, some downforce may get you a better total time due to better traction early in the run (maybe allow you to use power adders earlier).
Thinking about it, and knowing that one of the frequent "cures" for FWD drag cars is a "weight plate splitter", I wonder if a FWD challenge car might particularly benefit from front downforce at the drag strip, since weight shift keeps them traction limited for so much of the run.
I'll also say there's a discussion/simulation of the benefits of downforce in the MSHD airfoil research paper, starting on page 91.
In reply to sleepyhead :
And based on that why not try to set up a FWD car with aero bits that are high downforce, but maybe low efficiency and have them deflect as speed increases to effectively give low speed downforce (and drag) while decreasing the effect of both as the speed down the track increases. Spring loaded/pivoting dive planes come to mind, as does a wing mounting system on a sprung 4-link to reduce angle of attack with speed/load. All that stuff that is specifically dis-allowed in the other series is the place to mine the benefits in an event like the Challenge. The sucker car from a few years back is a great example. With micro controllers becoming so easy to use, the possibilities get crazy pretty quick, if you have the time/skill to put it to use.
In reply to stafford1500 :
I'm trying to think of how I could use trunk lift struts to do this based on the pitching moment increasing... but I think the sign-flip on it is frying my noodle, and I can't decide if the "push" of the strut would never work with the nose-up tendency of the pitching moment?
similarly thought... aren't some of the older power rear door lift mechanisms showing up in junk yards? dunno if their power/rate is fast enough, though?
In reply to sleepyhead :
Its not just the pitching moment to consider, but the total Lift/Drag force and its effective vector that you are reacting. They always wind up in the same quadrant, but the magnitude will change based on speed and AOA... A sprung system will try to keep the wing at a constant wing loading (combined drag/lift), so a different spring (or preload) would probably be required for autocross vs drag strip. I can visualize a falling rate spring system that would provide a max low speed downforce condition that falls away to a low downforce/low dag configuration at higher speeds.