I've been reading about F1 aerodynamics and it seems they re always chasing outwash. For an open wheeler car, this seems mostly about getting rid of tire wash.
But the front defusers seem to outwash as well, and the front defusers on closed wheel prototypes seem to do the same.
Is underbody outwash an efficient way to create underbody low pressure? Is outer body outwash efficient? Is there any reason I wouldn't try to get the floor of my MX5 outwashing? Any reason I wouldn't try to dump cooling air out the sides for similar reasons?
In reply to DaewooOfDeath :

Something like this seems to combine two layers of outwash for, I assume, higher velocities along the centerline.
I think I could duplicate this on my MX5, and I think I could get the strakes to literally touch the ground if I made them from flexible bristles (like what they use for shop brooms).
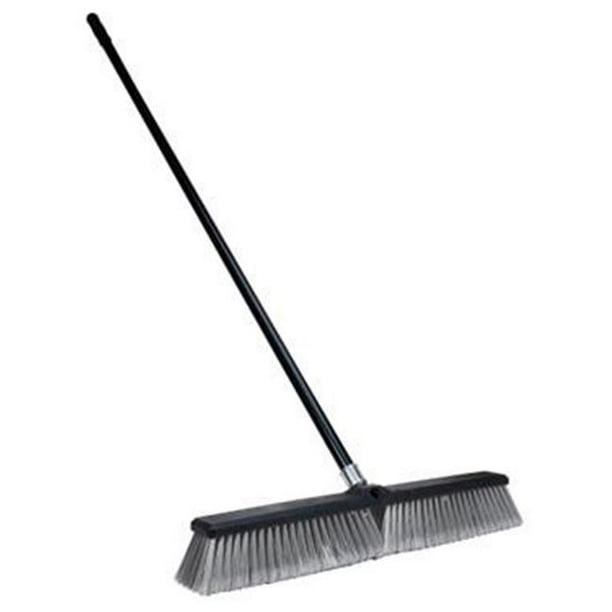
In reply to DaewooOfDeath :
I saw this when you first posted and intended to reply, but got squirreled with work stuff.
Outwash is a feature at the front of any object moving thru air (or any other fluid). The presence of the object means the air is forced away from the location the body want to move into. On cars the effect usually starts to reverse to inflow around the middle of the wheelbase, in order to fill the space the car is exiting. It happens vertically and laterally, but the ground poses an effect wall to the vertical outflow and we try to take advantage of that in creating downforce.
Open wheel cars are generally fighting with in/up wash at the front wing, out/up wash around the front tires and body, the out wash at the sidepods, and the in/up wash at the back of the car from the wing/wheels. The effect of each are affects the items behind, so there are efforts made to condition the flow for max downforce. A lot of those devices create a lot of drag to get that downforce.
For a production based car like the MX-5 or the image you posted, you can try to use the flow to create downforce, but will also create drag doing so. The turning vanes at the front of the floor in your linked image are progressively more extreme than the local flow and are trying to roll up vorticies along the bottom edge that effectively produce low pressure regions on the floor. Those vorticies also help direct the flow out from under the car and lowering the overall pressure. The turing vanes at the back of the car are trying to do the same thing for the relatively clean flow along the center of the floor. They are also set at progressively more extreme angles to the local flow for the same reasons noted above. The in wash at the back of the car means the rear turning vanes are at less agressive visual angles.
Using the sweep fences for turning vanes will work at low speeds (maybe less than 60mph), but will start to deflect at higher speeds. Since they are porous and flexible, they will sacrifice some efficiency over solid pieces. You don't want them to be too long (touching the ground) as they vortex spool up does require some airflow under the edge to make that happen. Also too long creates the vortex at a distance that is closer to the ground than the floor and will not relay all the effect as efficiently.
Thank you so much. :) This makes a lot of sense, though I do have a couple of questions.
1. How much does the mid-car inwash tend to get under the car?
2. Is this midcar inwash a considerable component of lift?
3. My thoughts about the bristles was that they'd survive curb strikes etc. In your experience, is it better to use rigid, non-porous materials and just replace them as they bend?
In reply to DaewooOfDeath :
Paging General Motors, Jim Hall, Colin Chapman and Peter Wright! The brush/bristles thing reminded me of what those guys went through when trying to get the Chaparral 2J, Lotus 78 and 79 ground-effect cars (and to be fair, all the F1 and other racing teams who also ran with the ideas) to get a seal between the pavement and the car, and IIRC what they ended up with (initially, before they were outlawed) were sliding skirts along the edges of the sidepods that slid along/close to the ground on vertical tracks that allowed the skirts on each side to slide up and down as the car went over bumps, pitched and rolled. As Steve says, underbody outwash is good and used a lot with open wheelers and prototype cars that have relatively minimal pitch and roll, but when you get to GTs and passenger vehicles, there seems to be more emphasis on reducing drag by pulling air out aft of the front wheels (see those big wheel arch vents in front of the doors) with rigid side splitter bodywork along the sill between the front and rear wheels to keep any inwash separated from the underbody flow while still allowing the chassis and suspension to do their thing and not having big variances in underbody pressure as the car moves around (which does not do a lot for driver confidence as Lewis Hamilton can attest), and worry less about perfect seals to the ground. To Steve's point, these cars tend to use moderate underbody fences to generate vortices to create that 'seal' to the ground rather than physical fences. Air is a lot more resilient than anything physical. IIRC Dan Gurney's AAR guys started to figure out using vortices for aero underbody seals for vastly improved ground effect with the BLAT Eagle IndyCars of the early 80s. People at the time couldn't figure out how they worked, because there were no physical fences around the diffusers...
On a historical note, in the late 70s-early 80s F1 rules legislated ground effect more and more, Chapman came up with the 'twin-chassis' Lotus 88, which had a full ground effect body that ran sealed to the ground (and at a constant height), on a separate suspension to the main chassis that supported the driver, powertrain, etc. with the aero 'chassis' suspension intersecting at the wheel hubs (IIRC). The theory was that the main chassis could pitch, roll, whatever, while the aero 'chassis' (OK, it was really a full-body wing) stayed relatively stable and flat to produce maximum attainable downforce. It turned out to not be very good in testing (that's twice as much suspension tuning to do, for starters), and the FIA legislated it out before it ever raced.
To Steve's point, depending on the speeds you're likely to see, using aero vortices to act as seals might be a better solution for you (and certainly more resilent to curbs).
I like your ideas! It will be interesting to see if you can come up with.
- Bill C
Or you could go to Mac's Hardware and buy some 1/4" conveyor belting and rivet it onto the body/floor weld flange. You could also cut it so that it literally touched the ground. Kind of like this.
A few years ago it was something like $7/foot.
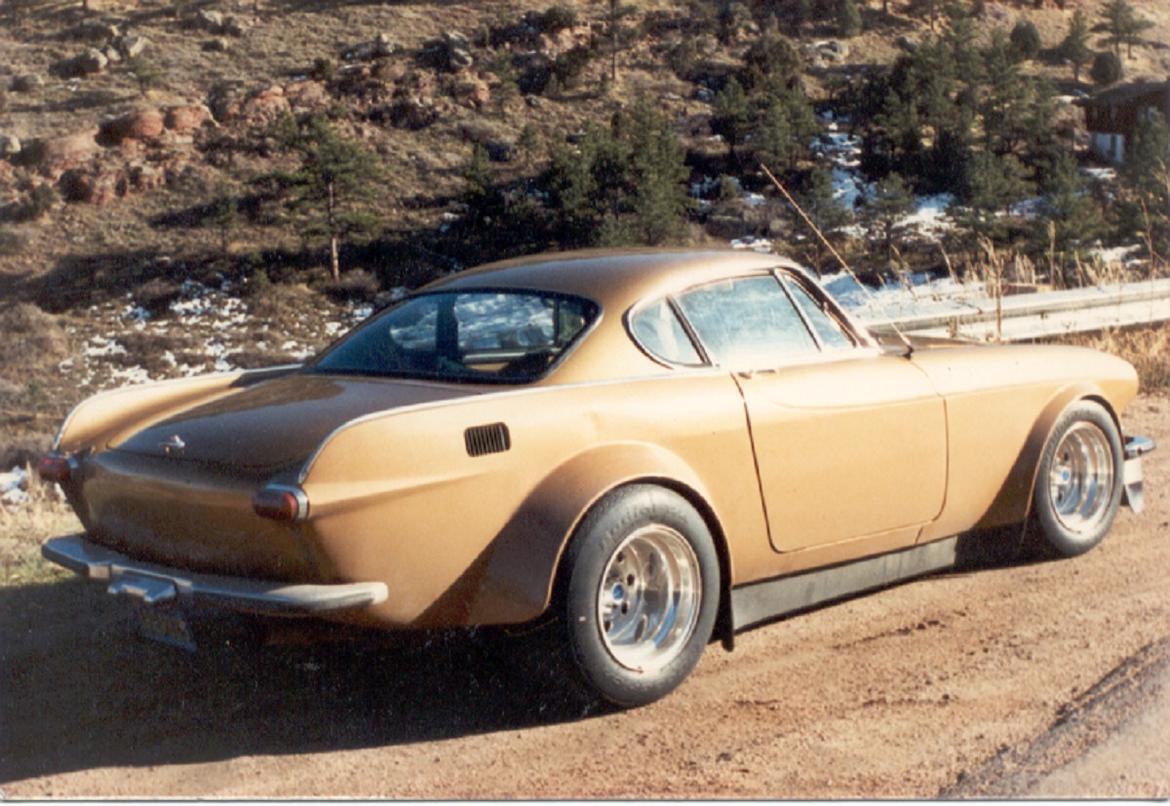
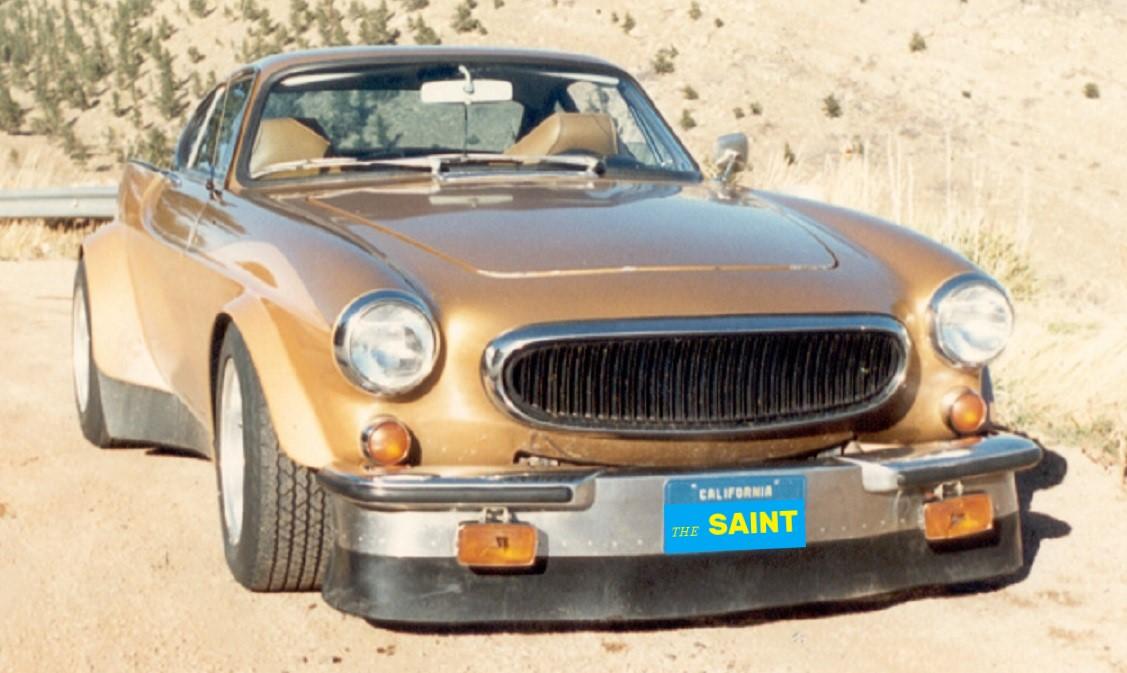