Please share your thoughts regarding intercooling, related to the following points:
1) I built two FI X1/9s in my time at MWB. One was the supercharged green K20 shown above, and the other was the one shown here: 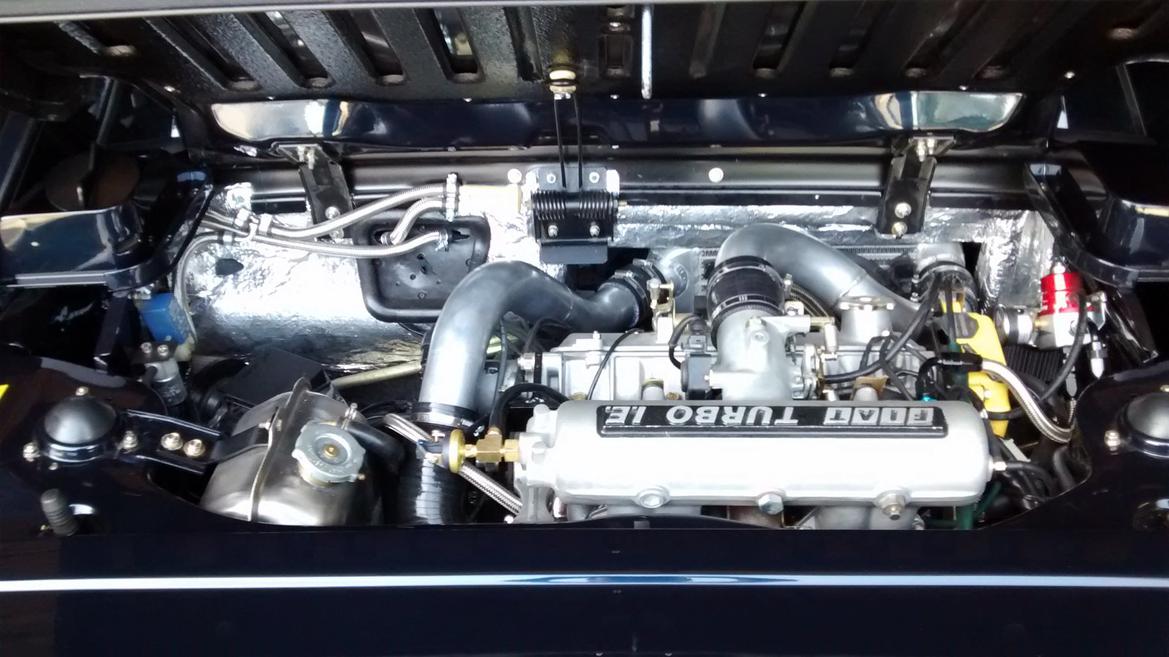
The K20 car used an ATW setup with a front mounted heat exchanger, whereas this turbo car used a conventional ATA intercooler installed just ahead of the engine with a slim line radiator fan installed on the core to keep it cool. The intercooler was in the same location in both cases regardless of the other differences in design.
2) As I see it, the location shown above or the space behind the driver on the engine bay side of the firewall are the only choices for the intercooler core. Above the transmission might be appealing for an ATW unit because the charge tubes could be very short, but that location makes my aesthetic eye twitch. Aesthetics might play a larger role for me than they should, but I like to make things look uncluttered and also minimize things being in the way of other things at maintenance time. If I am not going over the top of the engine, I would like to tuck the intercooler and have as tidy an engine bay as I can get.
3) ATW intercoolers are known for their thermal and airflow efficiency, but going ATW adds a lot of weight and complexity to the car, with a whole other fluid system (tank, pump, lines, electrics, and control over the pump.) I also wonder about latency in the system and whether that works for or against me or both depending on situation. I also would NOT be taking advantage of some of the neat options that open up with an ATW system such as ice boxes, using an AC system to chill the water, etc. This isn't a drag car.
-----------------------------------------------------------------------
The part of me that likes simple things would like to do what is shown above, but with a duct to the front of the core that draws air from under the car to help provide fresh air to the intercooler core before the air is drawn through the core by a good slim line fan. As on the car above, the fan would be actuated by a 1psi pressure switch. Unlike on the car above, the fan would be powered by a circuit that counted off a certain amount of time, let's say one minute, after the last time boost was detected before shutting off the fan. All of this could also be done with the intercooler on the driver side of the cavity instead of the passenger side. Charge tubes would be only a little bit longer (if any,) and the spark plug side of the engine would be kept clearer to make maintenance easier.
The duct design wouldn't have to be ultra efficient as long as it flowed air well enough not to become a restriction to the fan; the fan is what would drive air flow across the core. I am imagining an aluminum duct that could be welded directly to the intercooler with the whole assembly slotting in to the cavity in a similar way to how the original gas tank did. The X's side ducts are in the wrong position to help, so I'm not mentioning them (<--- except there.)
The way I see it is that the ATA idea should work about as well as an ATW could without the extra complication, but I would like to hear other opinions.