FB Rx-7s are hard to find recently so I jumped on this craigslist special when it came up.
I wanted to drive it for the summer and start building in the winter.
I gave it a tune up and drove it around for a few days but started hearing some clunking from the rear.
Long story short the rear wheel wells were rusted out to the point where the upper link mounts separated from the unibody.
(I gave it a look see when I bought it and the floors looked good but I didn't pull the bins) Somewhere along the lines someone 'fixed' the rust with kitty hair so from inside the wheelwells didn't look bad in the dark garage when I made an offer. 
So the build starts now.
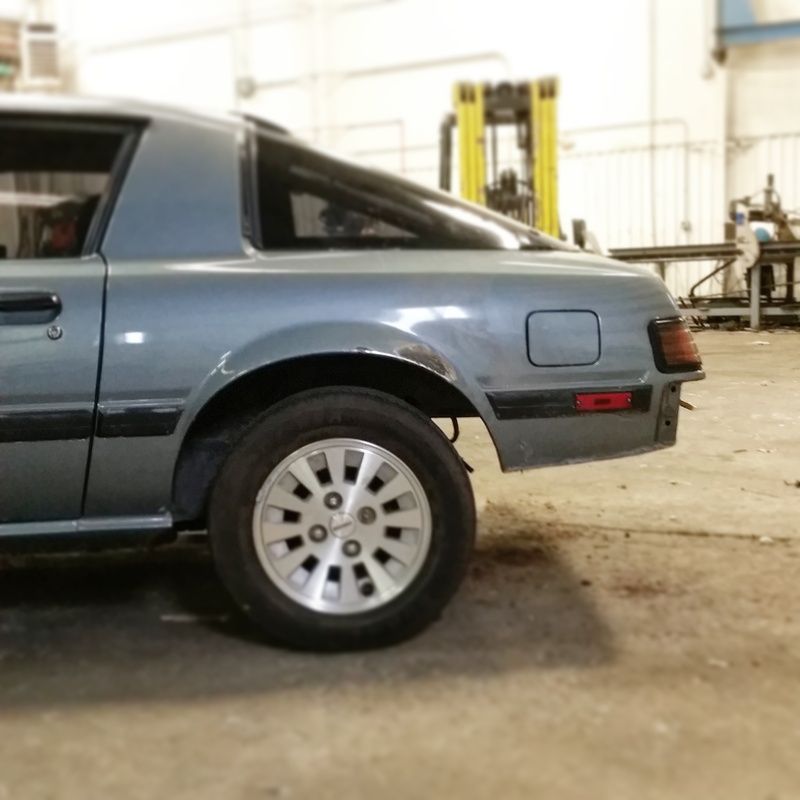
Rear valance under the bumper was shot and lower quarters were pretty shot on the inside. I cut the valance off and the quarters along the line of the factory 'undercoat'.
Then I made panels and welded the quarters back together.
I like the high and tight look on the rear.
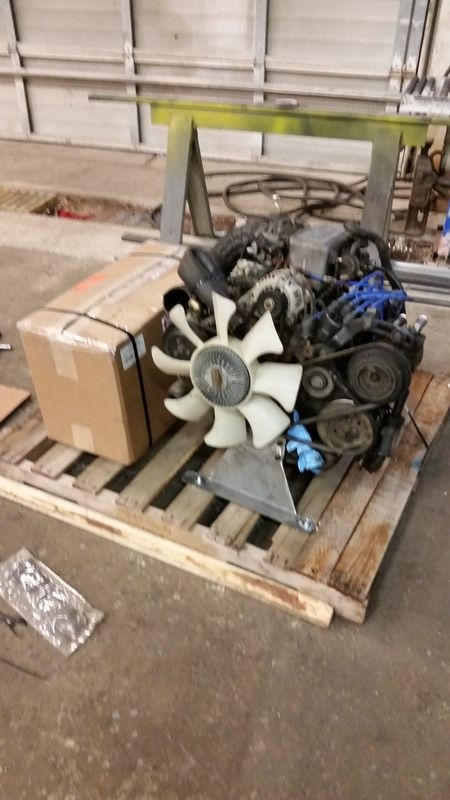
Sold the engine on ebay for almost as much as I paid for whole car.
Crated and ready to ship.
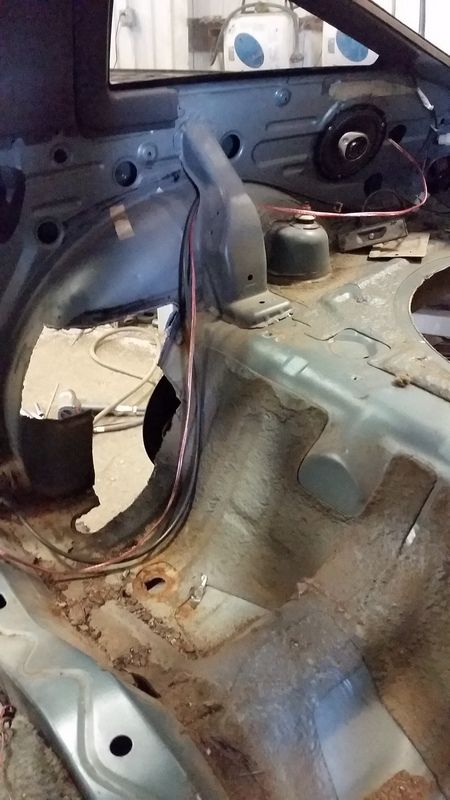
This was the good side. I'm going with a 3 link so I don't need the upper link mounts anymore.
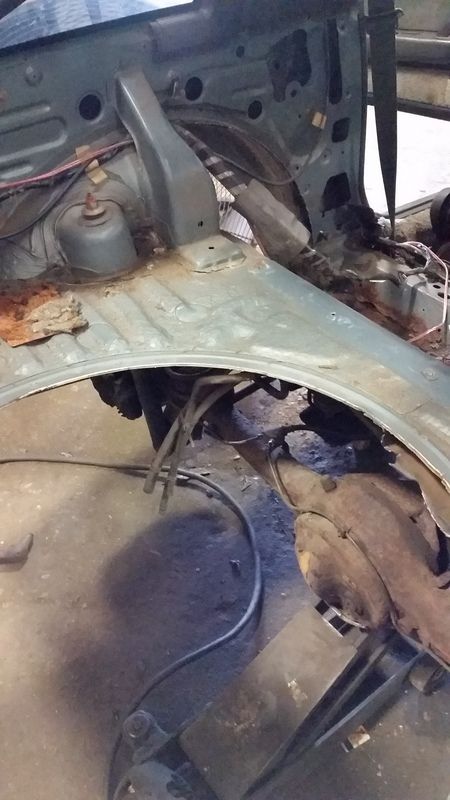
Cut out the spare tire well so I can get a fuel tank in there.
Following with much interest. My girlfriend's FB is quite rusty in the same areas.
I used 14 ga steel to fix.
Fully welded inside and out.
Going for strong and not looks or symmetry. The other side looks more like a mini-tub since I had to replace most of the front of the wheelwell. Should have it welded in tomorrow.

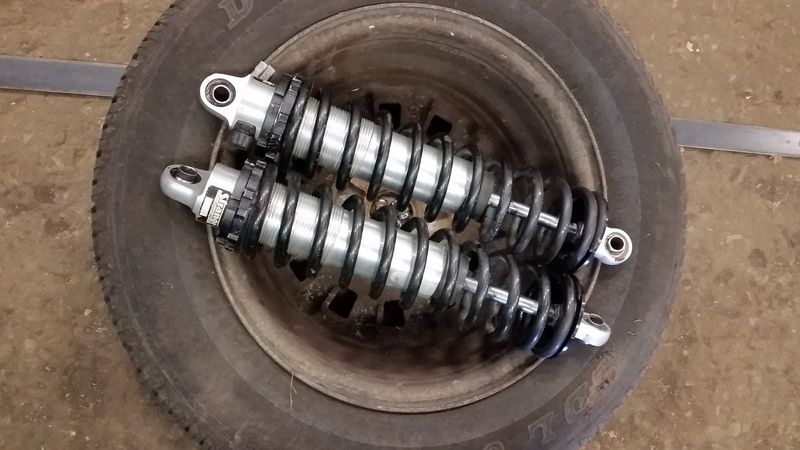
Bought these on ebay used. They're supposed to fit but glancing at the shock mounts today it doesn't look like it.
Found info on these on this thread:
https://www.rx7club.com/1st-generation-specific-1979-1985-18/front-rear-coilovers-possible-975939/
I'll make them fit regardless.
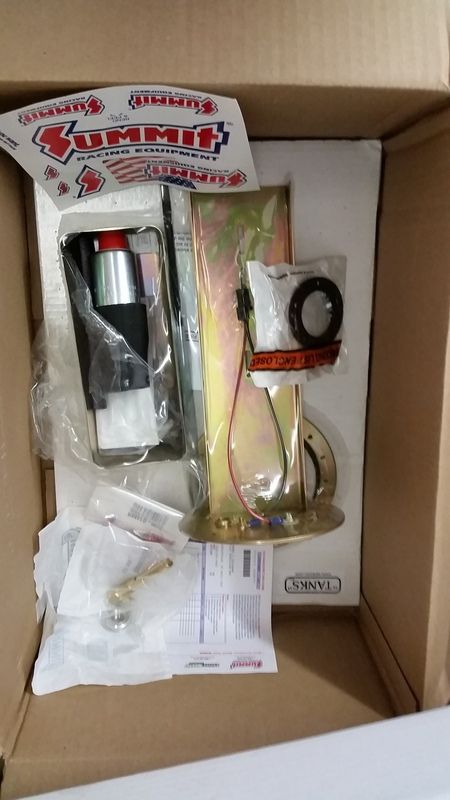
Goody box from Summit. 'build your own tank kit' basically. Walbro 255 pump included. Also bought rollover valve, bungs for it and a drain, and a plug. (plus sending unit)
Will be fabbing an aluminum tank after the rear suspension is in.
Ah, the tanks inc kit.
Makr sure to use thread sealant on the fittings.
Also, welding the ring to your used gas tank may seem like a good idea. And filling the tank with water may seem like enough of a safety precaution.
Its not. I blew E36 M3 up doing that. With this same kit.
Don't be me.
Dusterbd13 wrote:
Ah, the tanks inc kit.
Makr sure to use thread sealant on the fittings.
Also, welding the ring to your used gas tank may seem like a good idea. And filling the tank with water may seem like enough of a safety precaution.
Its not. I blew E36 M3 up doing that. With this same kit.
Don't be me.
Ouch. Yes, this is for a new tank, not the used one.
I occasionally make customers mad by not welding/cutting on their fuel tanks or otherwise grease or oil soaked parks.
NOHOME
PowerDork
5/11/17 6:07 a.m.
Dusterbd13 wrote:
Ah, the tanks inc kit.
Makr sure to use thread sealant on the fittings.
Also, welding the ring to your used gas tank may seem like a good idea. And filling the tank with water may seem like enough of a safety precaution.
Its not. I blew E36 M3 up doing that. With this same kit.
Don't be me.
While a part of me wants to know how the heck you make water explode, the other part of me is saying "see, I TOLD you that there is no way to make a fuel tank safe to weld on".
In reply to NOHOME:
Air pocket. Welding spatter. Boom....
No injury but i E36 M3 myself.
The bad side/mini tub. I had about an inch of good metal that acted as a flange to overlap my tub.
Inside:
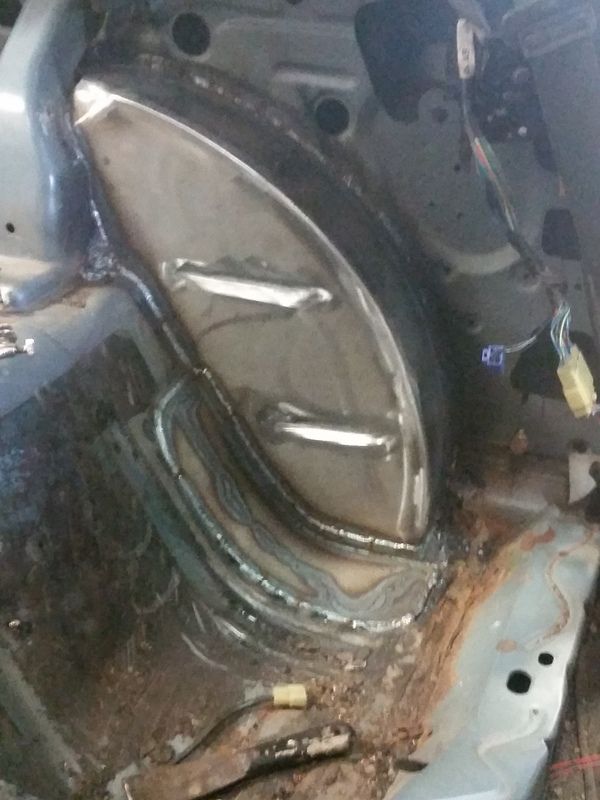
Outside:
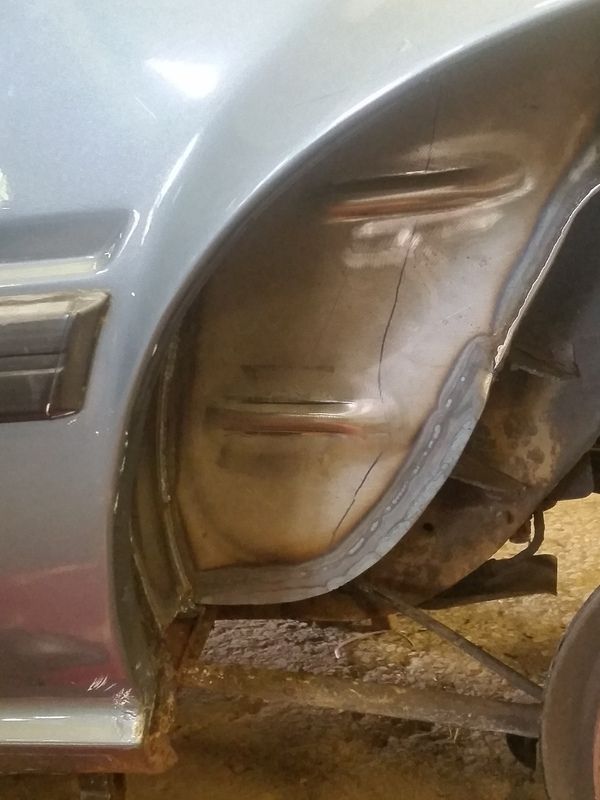
The structural problems are taken care of and I'm not so worried about the cosmetic. There is still average 30 yr old car rust problems but nothing impacting safety like that ^^^was.
So, onto the mods.
NOHOME
PowerDork
5/11/17 6:10 p.m.
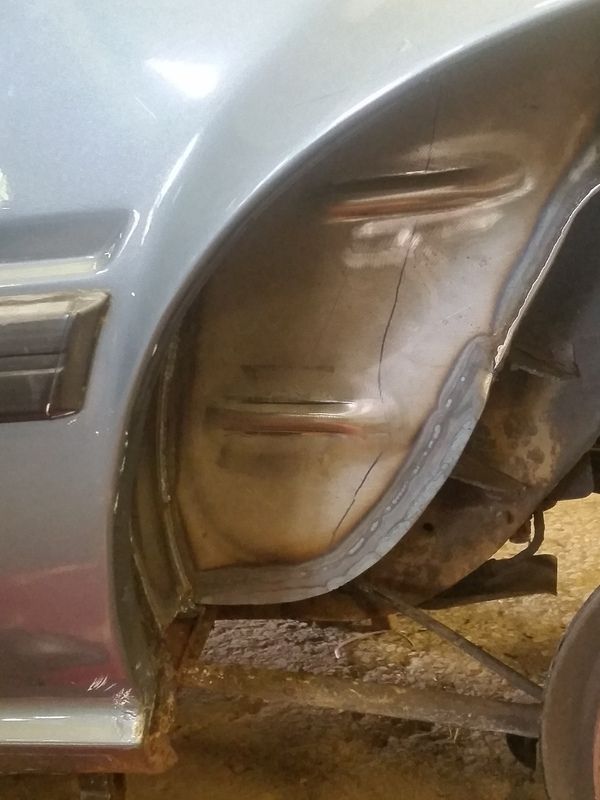
You say that you are using 14 (0.075") gauge tin?
Worried about IEDs? That is like one step away from steel plate. How are you getting the beads in the panels and shaping the curves? I use 18 gauge ( 0.048")) and that is plenty solid.
Nice work by the way!
Ooooh! You have all sorts of cool toys in that shop, don't you?
Crackers wrote:
Ooooh! You have all sorts of cool toys in that shop, don't you?
I do. 
Finally got a week or two that was slow enough to get started on this but it looks like that's going away.
I have a weld/fab shop with 2-3 employees. I have most everything I want as far as metalwork/welding/fab goes.
NOHOME:
14 ga is a little on the thick side but in the area this is I wanted a little more beef, as some factory panels in this area were doubled up anyway....plus it's the area where the future roll bar will go.
I used an english wheel for those beads (special wheels) and it was sort of an afterthought but worked ok.
I have most of the metal shaping tools too but am an amateur on them.
I also used brake, roller and shrinker on this project.
Also an amateur on rust repair of vehicles.
Instagram is @rlcweldfab
I'm lucky enough to do cool projects in general and more than cars I'm ate up with metalwork. Always lots to learn and I'm fine with that.
This piece I made from 18 ga.
Probably won't weld it in until the suspension is in.
Used the bead roller to roll a flange around the perimeter. Cut a 12" square to access the top of the fuel tank in the future and it will have some sort of door or cover plate.
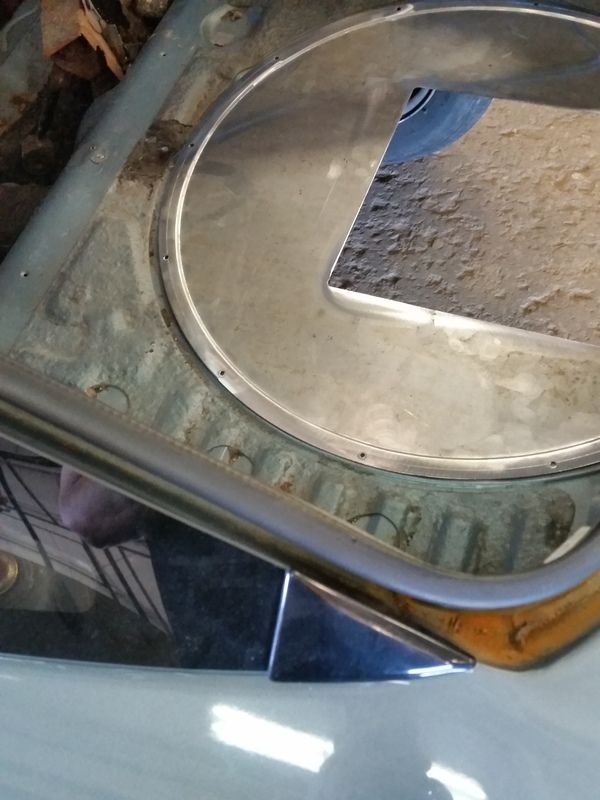
I'm paranoid about working under cars.
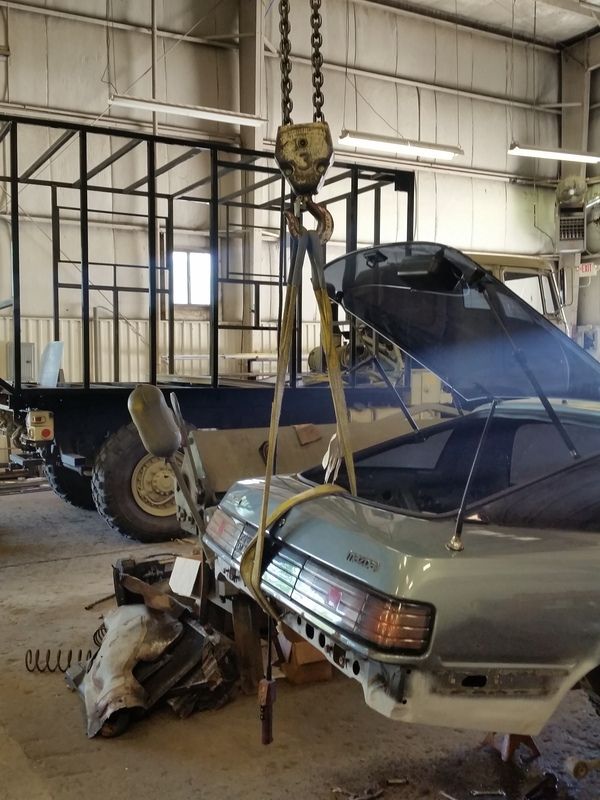
jamscal wrote:
I'm paranoid about working under cars.
is that a factory lift point? 