After test-fitting a bellhousing, the next problem that needs to be solved became obvious: the thermostat housing.

I figured there would be some interference here, and my original idea was to make some spacers like the EcotecMiata kit uses, or just see if I could get them to sell me a set:

But if I want to use this turbo manifold, spacing out the thermostat housing is going to cause clearance problems with the coolant pipe. You can see here that it's already touching the #3 primary tube:

And even with a gap between the housing and the block, it's also touching the adapter plate:

The adapter plate is notched for thermostat housing clearance, but it was designed to work with the older-style thermostat housing that came on 02-05 L61 engines:

I don't really want to use that one. It looks like it would cause even more interference with the turbo manifold, and I don't want to loop the lower radiator hose behind the head to the driver's side of the engine bay. The Conquest lower radiator hose is on the passenger's side, and I'd like to use a stock-style aftermarket radiator, so I want to keep everything on that side of the engine bay.
Most people who use adapter plates on Ecotecs just slap on a CBM water neck. The problem with it is that it deletes both the thermostat and the heater hose ports, which are two things I'd like to keep:

I found a guy who cleverly modified his to incorporate a thermostat, but even if I did that, I still don't see a good way to plumb a heater core.
So, back to the drawing board. Here's a diagram of the stock Ecotec cooling system. Looking at this, it dawned on me: why does the thermostat need to be mounted back there at all? The port on the back of the head that feeds the heater core doesn't flow into the rest of the housing; they are only connected by a small bleed hole. I could get rid of the thermostat housing and water pipe entirely, and mount the thermostat up by the water pump instead.
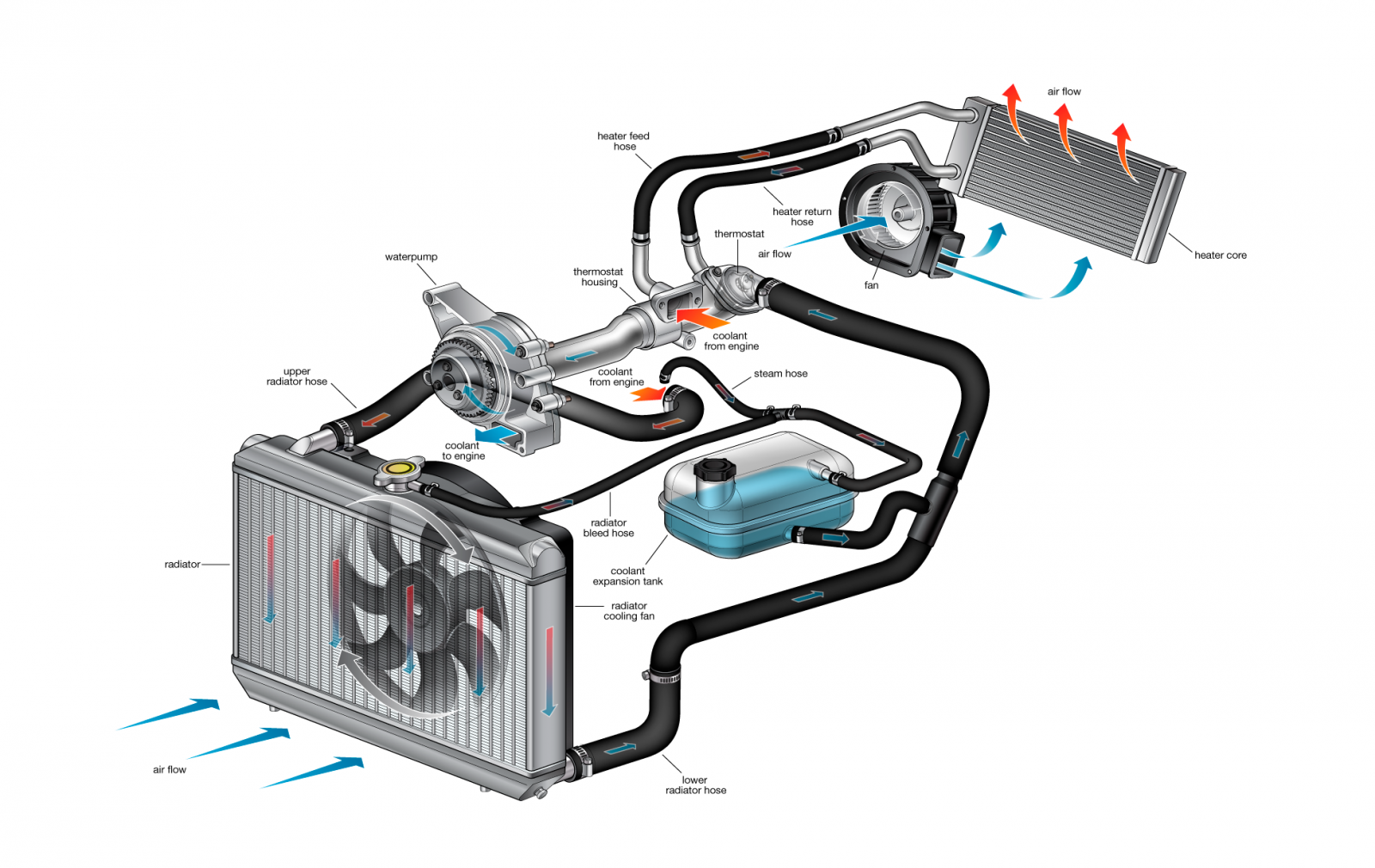
Then I remembered this awesome NASA ST4 build where a guy did just that:
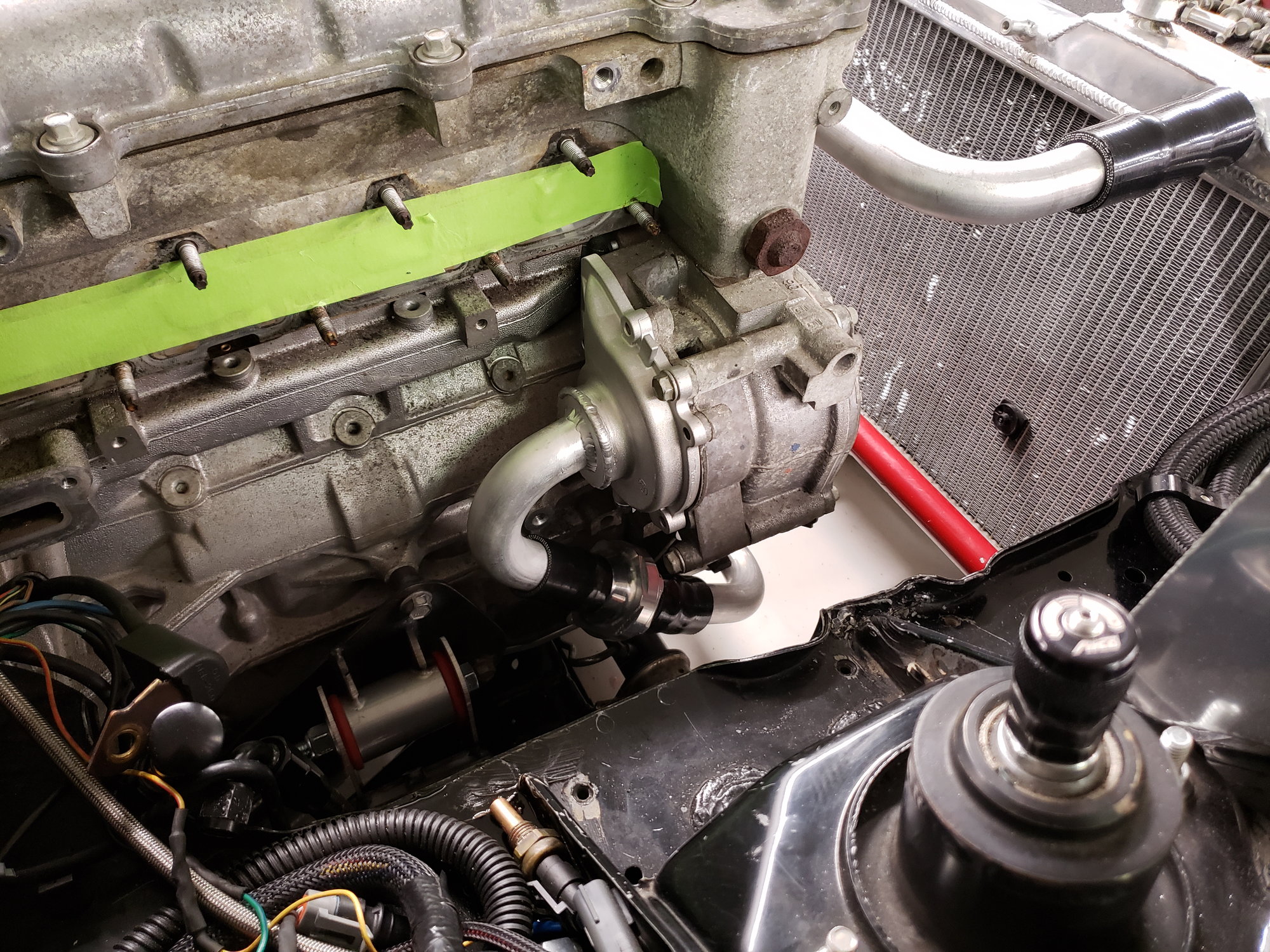
I don't have his TIG skills, but I have a local fabricator who will do small jobs like that for pretty reasonable prices, so I think that'll be my plan. I also discovered something convenient. -16 AN ORB bungs, like this one, have an OD of around 48mm. And the ID of the water pipe port on the rear cover of the water pump is...

I also found this nice inline thermostat housing that has 1.5" hose ports with -16 AN ORB threads on the inside. Plus, it has a 1/2" NPT threaded port that I can plumb the return from the heater core into, just like factory. Perfect!

So, now I just need something for this port at the back of the head to feed the heater core and mount the coolant temp sensor.

Turns out that such a product already exists, but I think I can make a better one myself for a lot less than $90.

So, that's the plan. Works great in my head, we'll see how well it actually works in real life eventually...