So it's been about three months since I've made an update here, but there's plenty to report.
The axles have been fine and the suspension and tires have been amazing. By turning the fans the correct way, ensuring that the radiator is filled using water and Hyper Cool, and having the shrouding installed, the temps are staying in range and that problem seems to be squared away.
The real problem, though, is keeping the motor installed in the car:

That is the 1st gen Stratus 2.4 motor mount. The astute among you will notice that despite being created as a single piece of aluminum, this mount is in three sections. It turns out that a three-piece motor mount bracket lacks the efficacy of the original single piece implementation.
I discovered this failure while on-course. The temps started rising rapidly, I was getting coolant on the windshield, and the brake pedal went right to the floor and did absolutely nothing to stop the car. Pulling off course, I found that the motor had shifted which cracked the plastic thermostat housing. Looking further, the lack of brakes was caused by the alternator pulley tearing through the front-right brake line. Going even further, though, I found this:

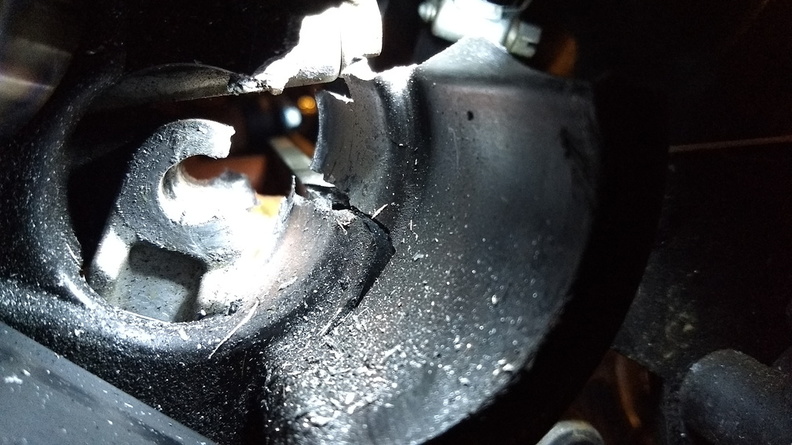
That is -- or more appropriately was -- a dogear in the block that one of the mount plate bolts was threaded through. When the plate sheared, the bolt tore that dogear out completely, but that appears to be the only permanent damage done.
I didn't have much time to work on it before the next event -- between having to make Edward Scissorhands props for my wife and then frying up 10,000 doughnuts for my church festival, I didn't have a whole lot of time to get things patched back together. After running to all three U-Pull yards in town, I scored a thermostat housing, another aluminum bracket from a former Cincinnati Bell Stratus, a new right-side mount and Prothane inserts from Amazon, and some brake line and a compression fitting from Advance. After a day's worth of actual work, everything was back together, the brakes were bled, and the car was running great again.
One hurdle that I really didn't have time or equipment to fix "right" was the torn dogear. I didn't want to go with just two bolts, so I cut up a bit of 1/8" steel and put some holes in it. I welded a nut to it and trimmed down the "foot" on the mount bracket to accommodate it and then bolted it through the power steering adapter plate (which is attached to the block with two or three larger bolts).
The very next morning, I took the RV with the car trailing behind up to the OVR 2-day rallycross event. The car started out really strong, but wound up overheating after the second run. Turns out, I didn't have enough water in the system and I forgot to turn on the fan, so I cooled it down and filled it up to make my third run. It ran great yet again, and I was feeling pretty good about things. I pulled off the start line for the fourth time, and didn't make it past the first turn when it died and wouldn't restart. At the lunch break, I did a little troubleshooting and found that the fuel pump fuse had blown and replacing it with one out of eastsidemav's car got the engine running perfectly again. The motor was rocking a bit, though, because the bolt for the lower-right engine mount strut had sheared. Our gracious host opened up Bolt Bazaar so I could go shopping for a new bolt and I was able to get that installed with no problems.
At that point, I was all ready to go back to racing but since I had a little time, I asked eastsidemav to come over and give me an opinion. As I was standing on the course after the car broke, I had some time to think about what was going on and I remembered that when I was putting things back together the day before, I had to put a ratchet strap on the engine to twist it forward so that the motor mount bolt would be able to thread. As I continued to think about it, I'm thinking that maybe I've got the motor rocked backwards too far, which is putting the bolt hole too far back and then the whole thing is under constant stress. My thought, and I what I wanted an opinion on was if it would make sense to go ahead and try to move the motor around there in the field. Before he could get over there, though, I noticed that the aluminum bracket was sheared again. It doesn't appear to be as bad as before, but it was enough to retire the car for the day.
I'm enjoying taking a couple days off not thrashing to get any projects moved forward, and I need to spend some time helping out with the Challenge trucklet, but in the meantime I'm kind of formulating a plan, assuming that the damage is as light as I think it is:
First, I want to support the motor so I can pull the side mount and the remains of the bracket out to let the engine find it's natural place. Then I'm going to unbolt the lower-right mount strut and the bobble strut so I can reposition the engine where I want it. I'll go get another mount bracket and get the motor bolted in - this time it shouldn't be under any torsional stress. Then I can go ahead and connect the bobble and the strut to eliminate the rocking of the engine. Finally, I'm going to put another strut on the front of the motor where the original engine would have had the front motor mount. The idea with all that is to have the motor mounted so that it doesn't move, but not have it preloaded.
One change I could make to that plan would be to use the steel front plate from the PT Cruiser 2.4 after I ground off the PS mounting bolts and drilled and tapped a new hole for the frame mount. I like having that aluminum bracket there, though, because I feel like it acts as more of a circuit breaker against doing any further damage to the block.