Prepare yourself for a scatter brained post.
This week I've been focusing on the engine bay and transmission tunnel. I've managed to get the false firewall removed and have started cleaning up the now much larger bay.
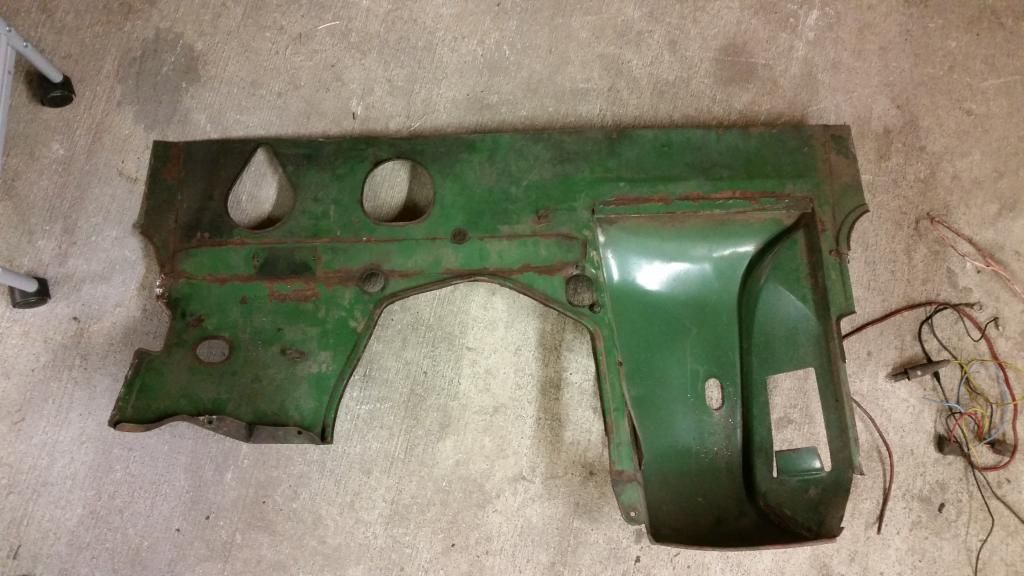
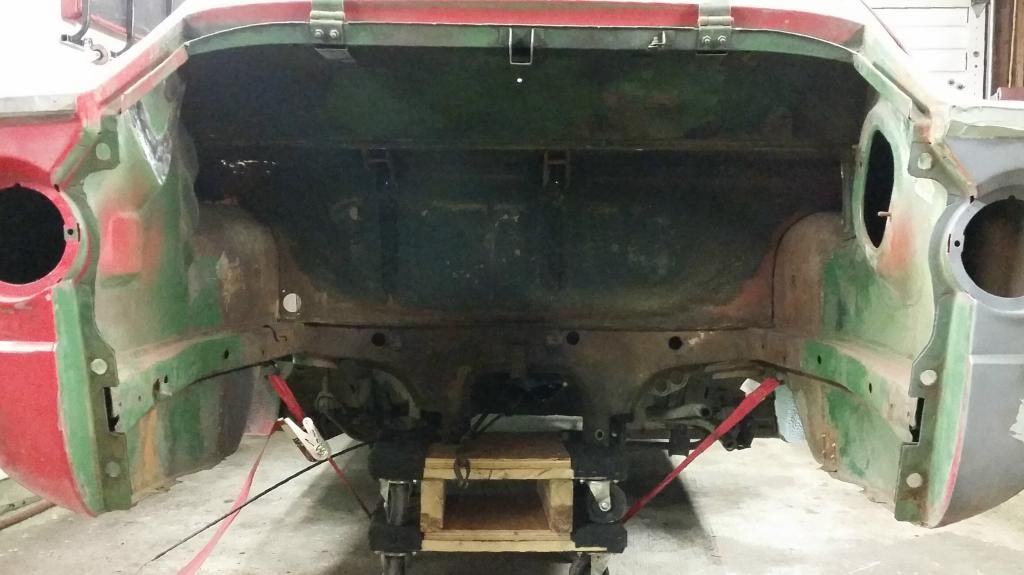
Lots of undercoat and surface rust to be dealt with.
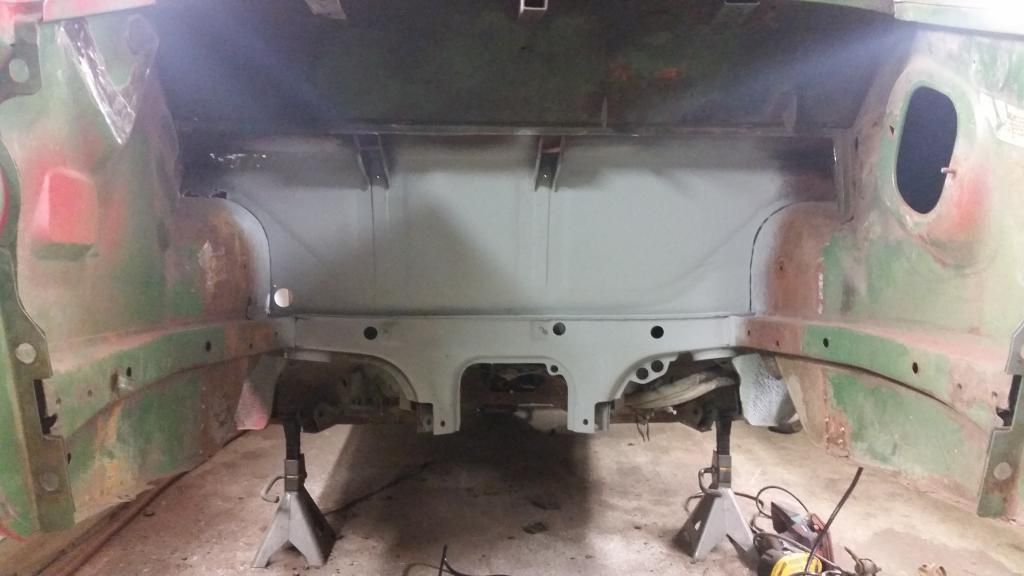
Everything in primer here has been taken back to bare metal.
At some point during the week I leveled the car out and offered up the transmission for the first time. The results weren't fantastic.
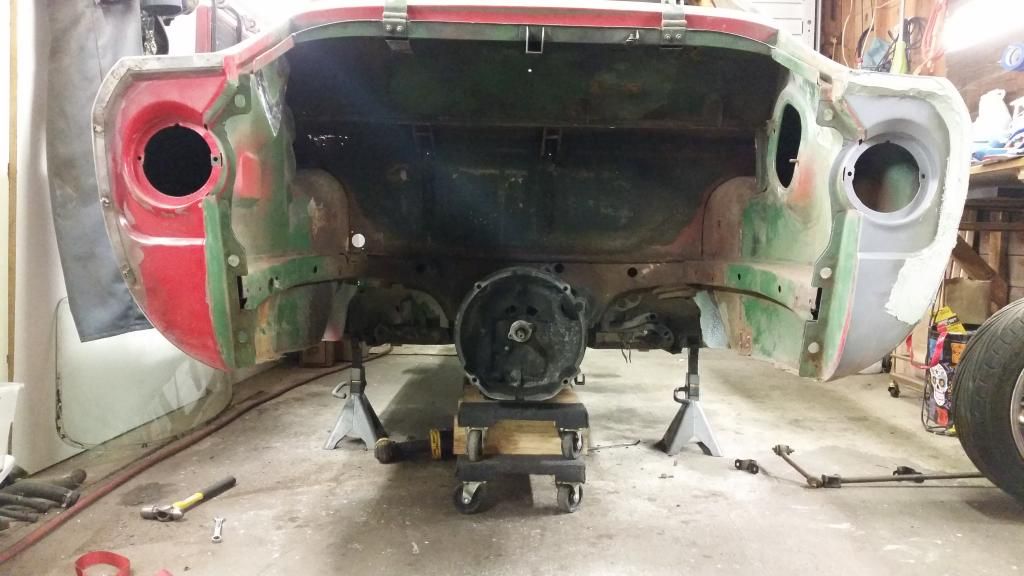
That's as high as it goes. That's with both the body and the transmission level. At this point the oilpan would be about an inch above the ground at my preferred ride height. I would really like to have 5 or so inches of air separating the two from any sort of intimate contact.
So, that means I need to buy myself a good 4 inches of vertical space for the transaxle to dwell in. There's no good way that I can see to do this, and I have been drinking beer and staring at the problem for 2 afternoons now.
I can cut the pinch weld off of the trans pocket here and weld the seam up flush:
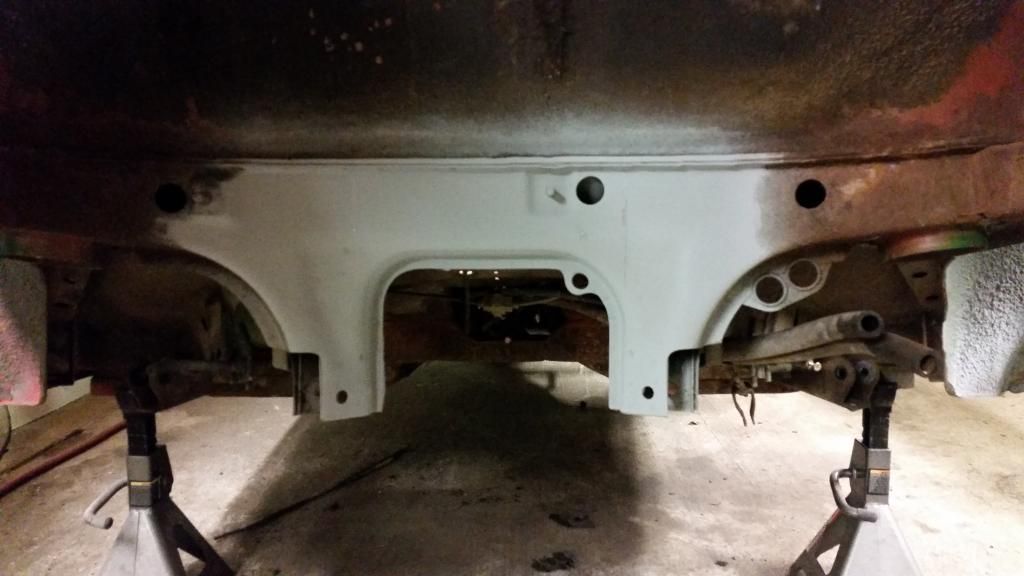
That would buy me .5".
I can cut over 1.5" of webbing off of the top of the transaxle before running into the internals, but I really don't want to do this. This could work in conjunction with the previous idea, buying me 2".
I can cut the center of the transaxle pocket out, move it up 4 inches, fabricate a new section of "frame" to mount above what I cut out (this will be in the cabin), and a fabricate a stress bar to pass between the two suspension mounting points (this will go under the trans). This is what I'm planning on doing, because I am both an idiot and a man who doesn't value his free time or understand arbitrarily set deadlines.
If this still isn't enough, I will say berkeley it and run the engine and transmission at an angle.
I was having trouble telling where and how the rear frame section met up with the floor, so I cut a big porthole today...
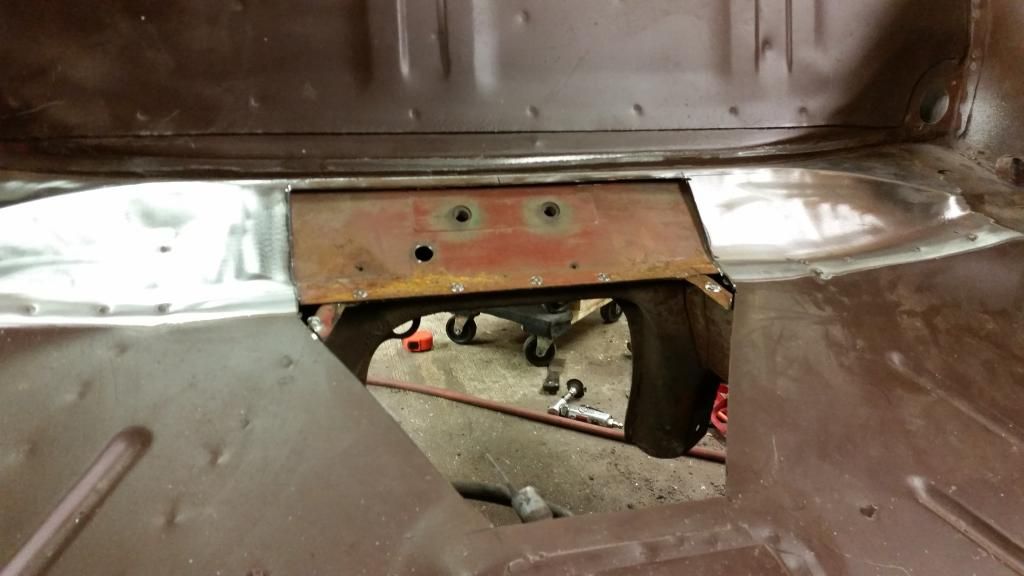
I will see about drawing up some quick diagrams to better convey my thoughts.
Thoughts, concerns, criticisms?