The results are great. 88 PSI oil pressure at idle cold. 68 PSI at idle with oil at 160 F. You can hear the oil circulating. Rev produces 100 PSI max. This a mechanical gauge connected to the oil port on the top rear of the block. The belt tracks straight and true. Looks like the oil system is as good as it can get. Now for a rework of the skid plate and off to the dyno for some tuning.
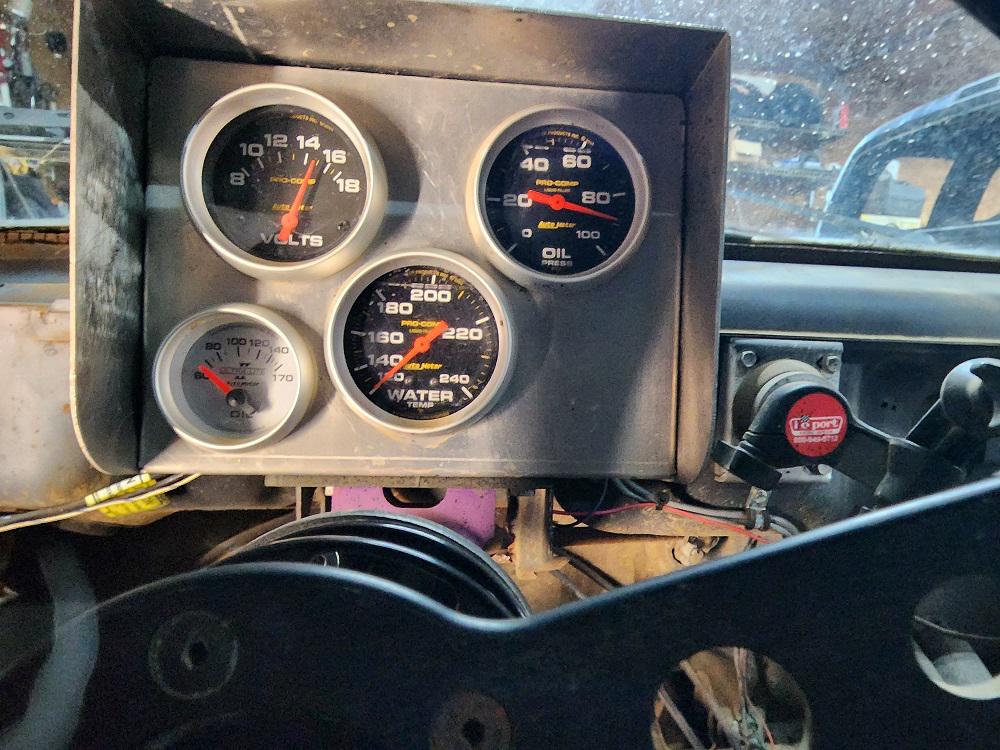
I'm co-driving the Porscharu this weekend--anyone have questions? 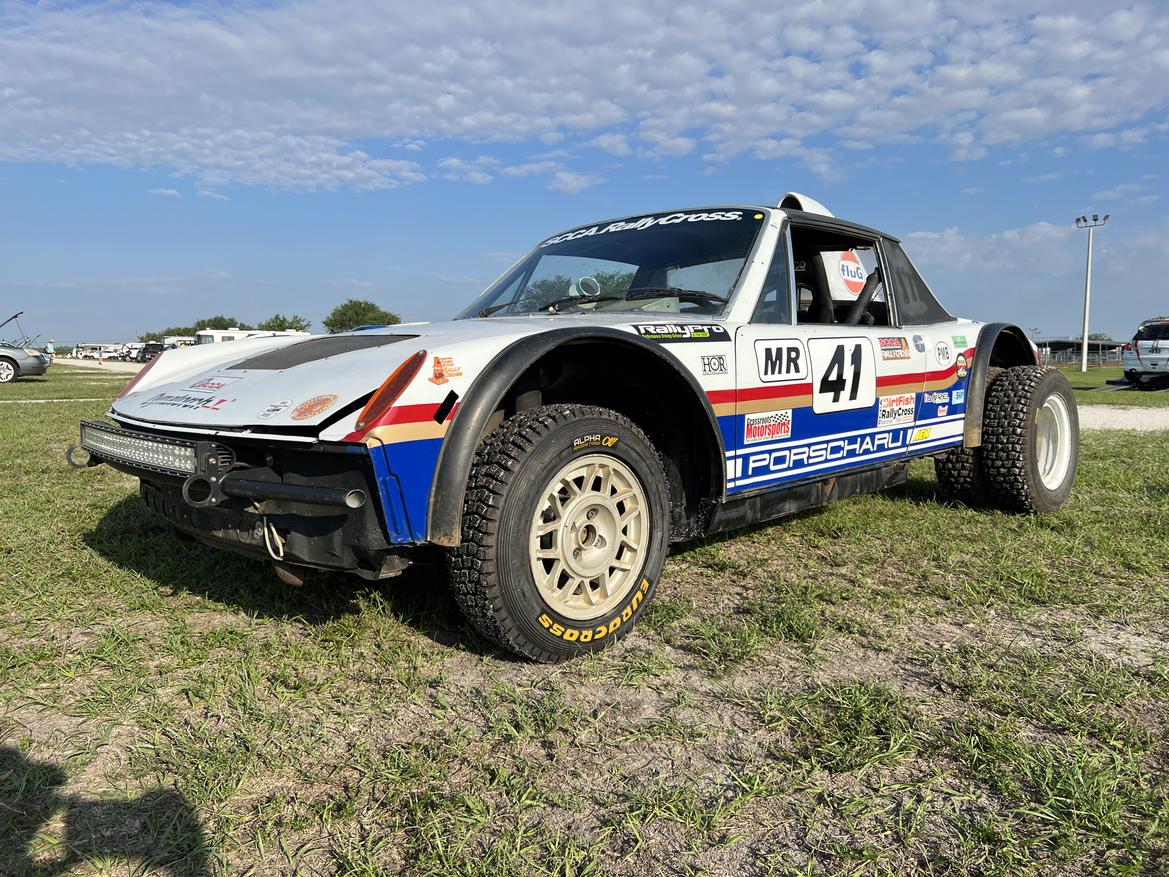
In reply to Tom Suddard :
Going to have in car video? What venue?
Yep. IT'S BACK. Well, never left. Porscharu has been living the race car life. Won the SCCA SouthEast divisionals in 2022 and 2023. It won the national championship in 2022 and then did a repeat in 2023 winning 1st AND 2nd at nationals (2 drivers). It's the one to beat now. And they are coming so it's time to upgrade and get some MORE power!!
TURBO time. Yep the EJ20 in it now (after loosing a few EJ25'sback in 2019) is getting some love. The dry sump is awesome goodness and maybe why it's still working. So lets jump in.
My other new project Frankaru (Frankenstien #2 on you tube) had a spare 2006 WRX engine that turned up bad. Water got in it. So it had a turbo and all the parts and with a good long block in Porscharu, it was worth the shot.
1st step. Remove the old dual exhaust.Then install the header pipe from the donor and see if it fits and clears all the dry sump lines.
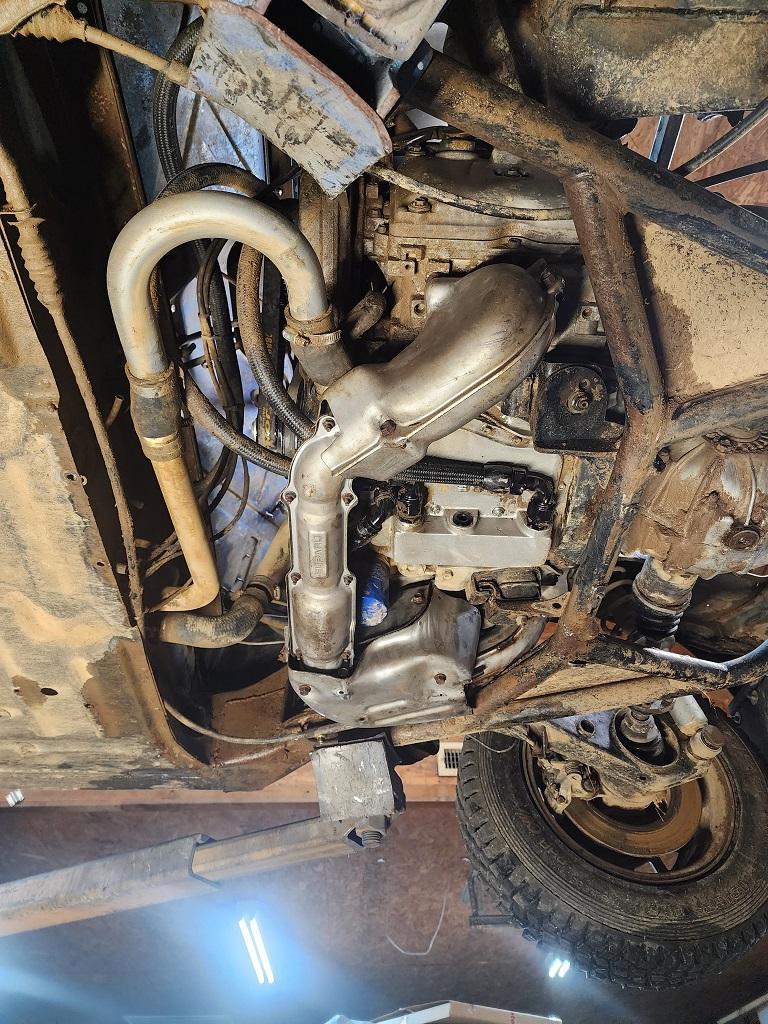
Yep. Mostly. Sort of. The lines will need to be moved slightly to avoid the heat. Maybe some DEI wrap. The up pipe however hits the head on the right side. I plasma cut a 1/2" spacer where the 2 bolt flange is and it clears.
Then drop the turbo on and see what hits and what all will have to be changed. Answer, lots of small things. Oil lines, water lines, drain line and well it points the wrong way so the hosing has to get rotated. Turbo support brace needed to be remade also. More on the way. Stay tuned.
On to bigger and better details. Next step, install the intercooler. The donor had a front mount intercooler and an original engine top mount. The heat sink on the originals is a negative to me. Plus this is going to be in the back so no good air supply for the little one. Plus the big one fits right where I like it. In place of the rear window. Yup, you read that right. Air scooops on the roof will supply relatively air to the cabin and pressurize the interior so dust wont pour in the back window. I've done this already on the Rally VW Caddy pickup and it works.
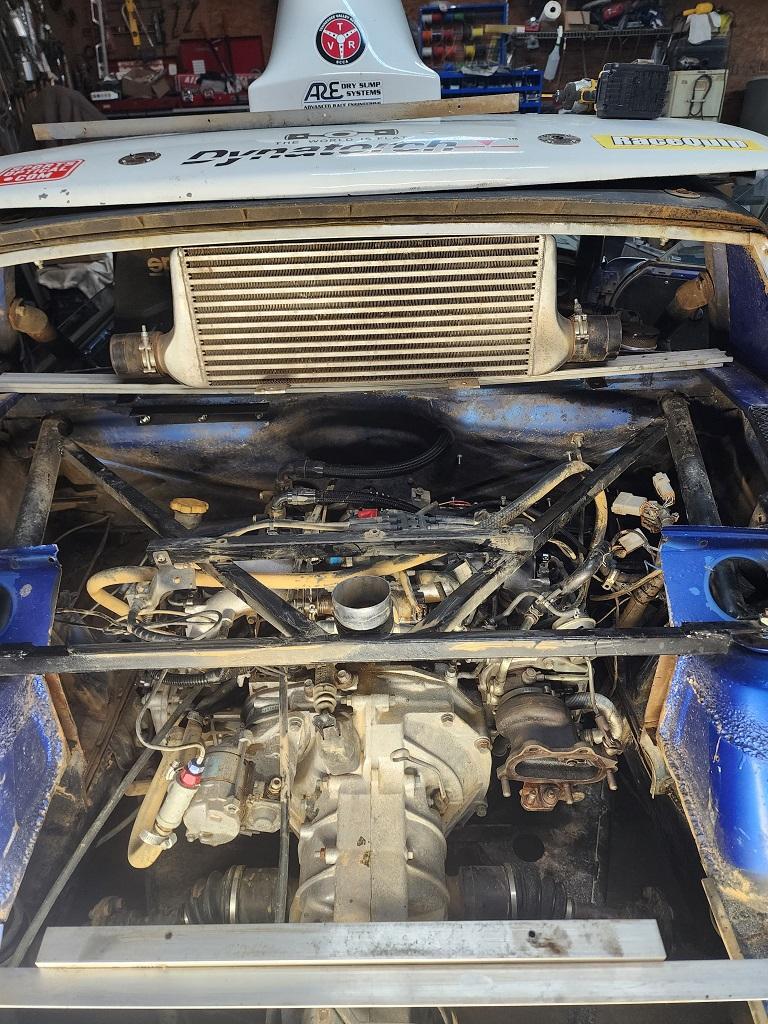
From the cab its like this:
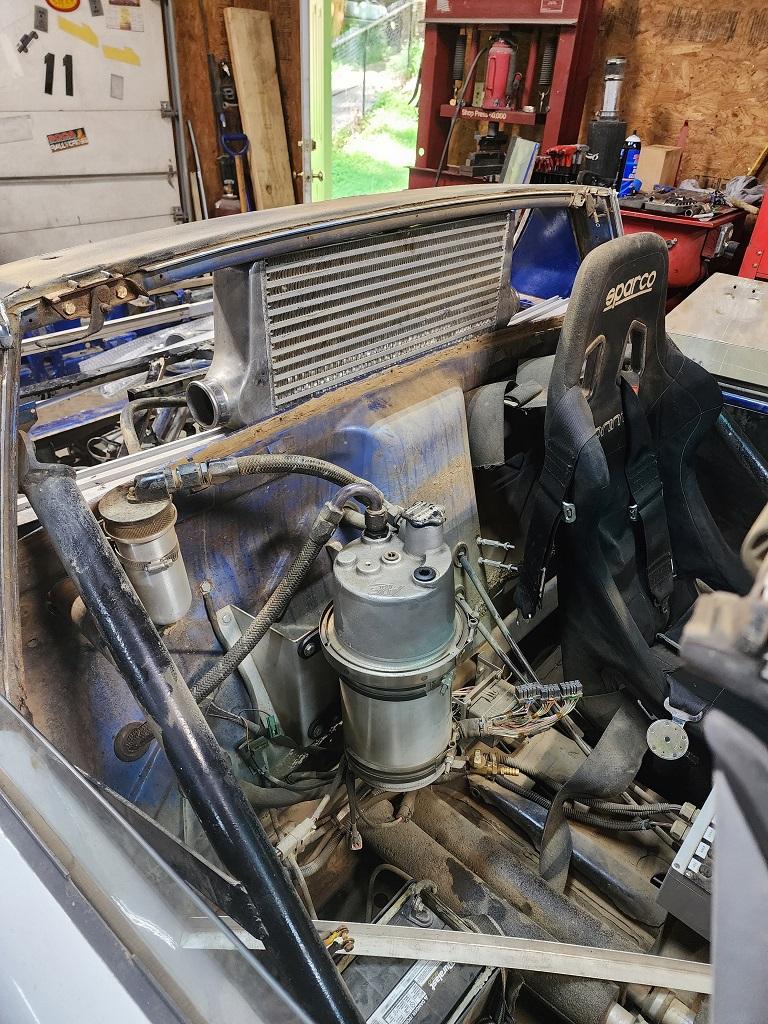
That's the test fit. The brackets were OK with a trim on the bottom edge of the window opening and the top bolt boss actually fit with a grommet into the channel in the targa bar. Tight and solid.
The donor came with a pile of welded intercooler tubing, clamps and boots so with a bunch of fit up, I came up with a layout. I had to rotate (clock) the turbo compressor side about 180 degrees. A lot more on that later. It's not easy.
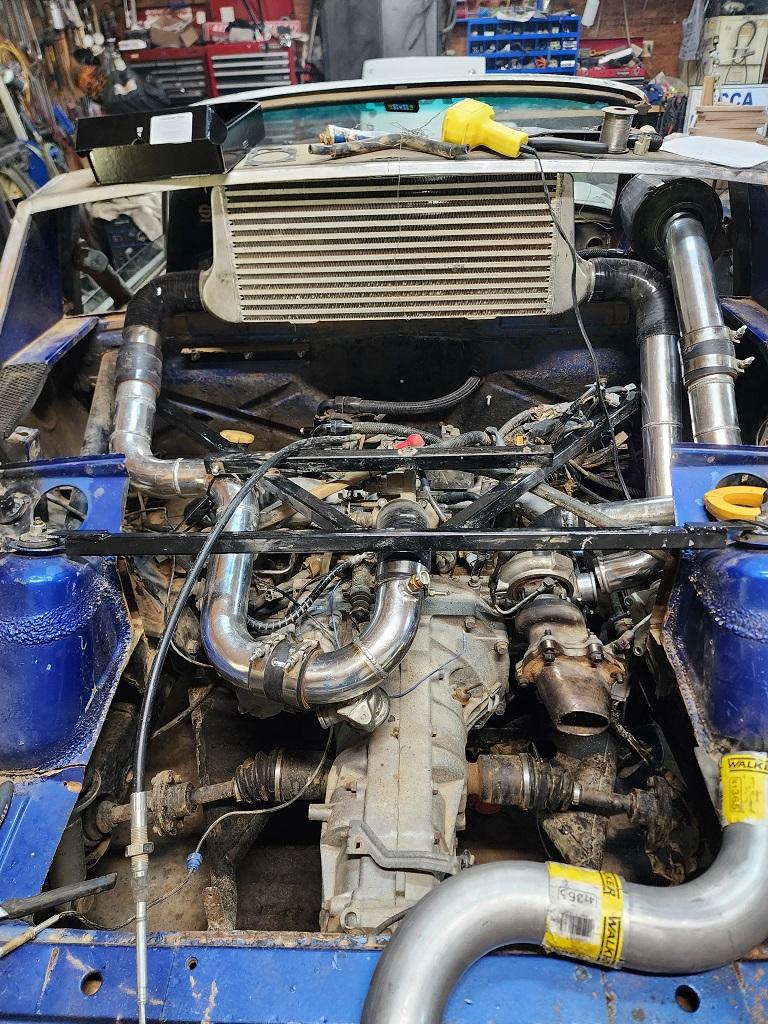
Still a LONG way to go.
Next: The Injector ordeal.
The factory injectors are 300cc and just shy of what I need for more HP. I'd like 400. I searched web sources, left messages with Bosch and injector houses to see what they might supply but no answers. I pulled the ones from the turbo motor. Denzo brand and 550cc. A bit much but OK to use. the problem is different fuel rails and length.

So they fit into the intake manifold tight. Are shorter on the bottom end but do look like it will work and that end. The top end has smaller o-ring and a completely different fuel rail spacing due to added hardware between the intake and cylinder head. After a lot of back and forth, I decided I could modify the rails a bit from one of the many sets Persad had at his Subaru recycle yard. It required machining adaptor spacers for the bolt locations. So order material, wait, cut and machine. days later I got them done and they fit up. At least connector plugs are the same.
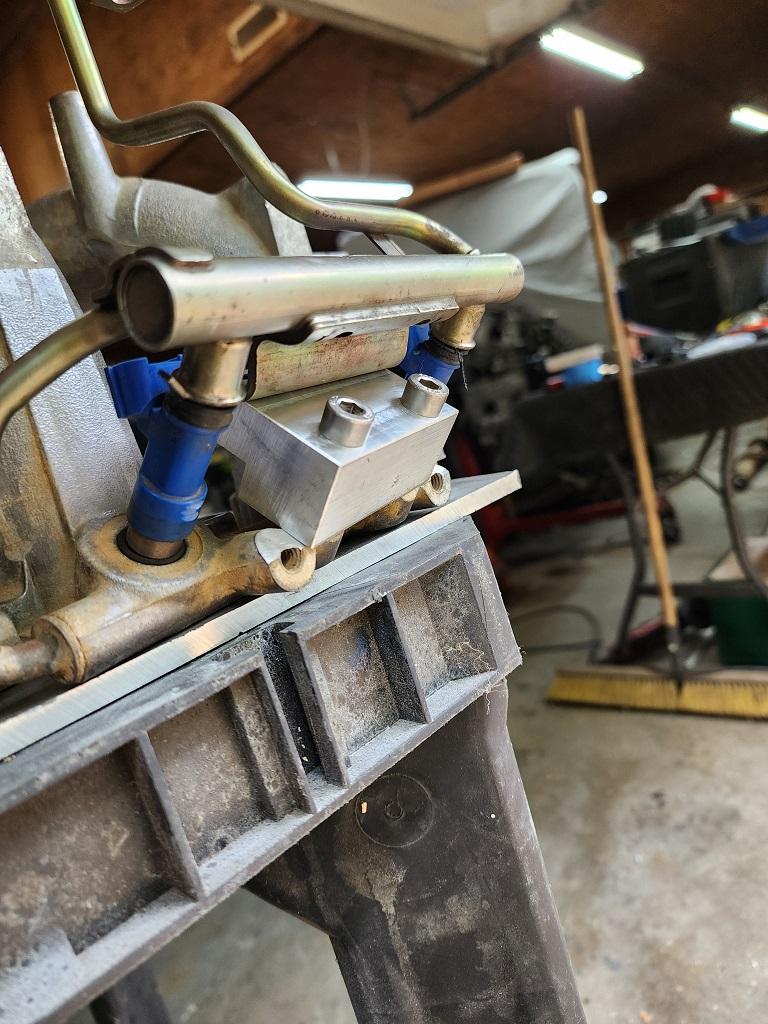
Next, Turbo oil supply and drain.
For Colin, I decapped the WRX blue injectors. Should be 800cc if the internet has anything to say about it.
Not particularly interested in light throttle cruise for this application, and idle is probably going to stutter a lot anyway with a rolling fuel cut.
It's a pretty fantastic build. Almost makes me think about reviving my Subaru-powered 850 Spyder as a rally machine, although it mightn't have enough weight on the front to make it turn in.
I see that you're going the turbo route. Is there any reason that you never tried one of the H6s? It looks like there's enough room in there.
In reply to Kreb (Forum Supporter) :
Weight mostly. It would likely fit as there is a lot of room ahead of the motor. Also not a great deal of support for the 6 cylinders. Lots of EJ parts everywhere. Plus the turbo kind of fell out of the sky for me when Frankaru's replacement engine turned up bad.
Oil to the turbo. I had added a port for the mechanical oil pressure gauge using an adaptor in the top rear oil gallery. Kind of a standard thing. So I learned the hard way on my Toyota turbo that you want to keep hard line for at least 4 inches from the turbo. Running an AN line on a banjo fitting right on the turbo melted the inside and started a fire. Lots of heat there. So the old line went down to a pressure port on the WRX motor that I do not have. I inverted the line so it goes up. Added a Tee fitting and an NPT to AN adaptor on the gauge port I already had and ran the AN line to an adaptor I machined from a 1x1 piece of aluminum. The hard line has banjo fittings on both ends thus the adaptor. Pretty easy fab job.
The hard line has a rubber lined clamp for the oil line that I used to support the line so that it doesn't vibrate, crack, break and spray oil all over a hot engine. The problem is that the brace I'm using is on the body and the oil line moves with the engine. There must be some give allowed. So I welded on a tab to the brace and added a bolt with a rubber grommet and a nylock nut so I did't have to fully tighten it. Anyway, it's not going to shake about and it all should stay together.
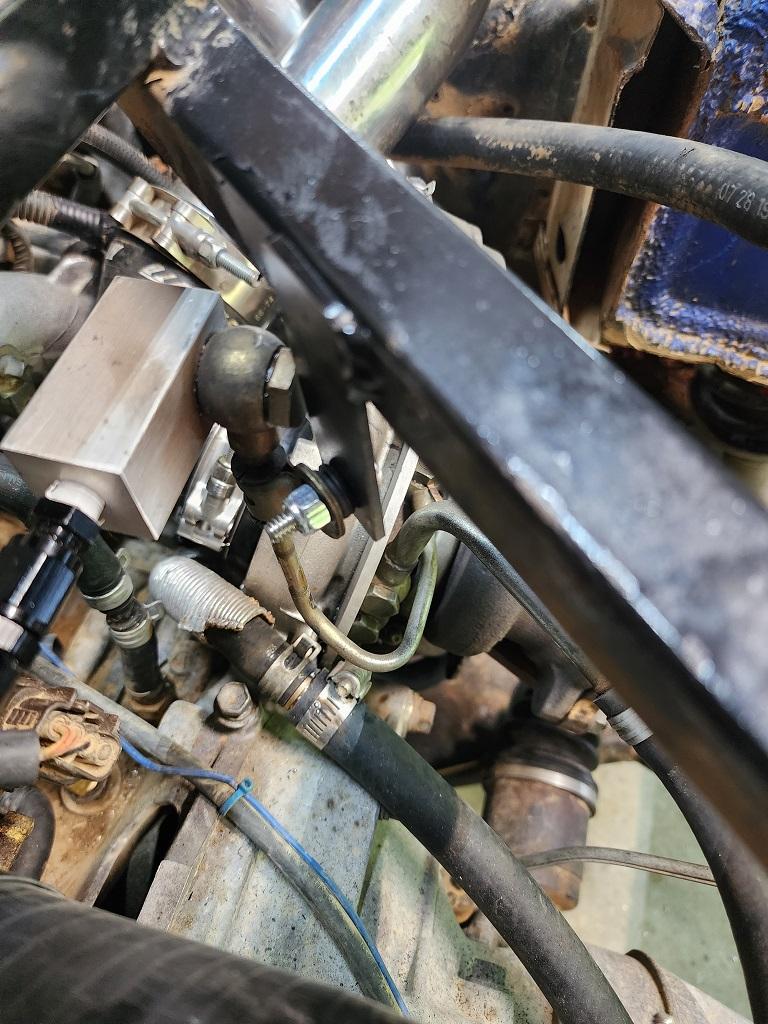
That's better. The old death by 1000 brackets.
Oil drain back. Unlike a normal upright motor, boxers sit low and using a dry sump does away with a drain back to the pan. Just dump it in the valve cover. It's below the turbo and will get back to the dry sump. I added a bung to the valve cover for an NPT fitting. The hose is 5/8" I.D.
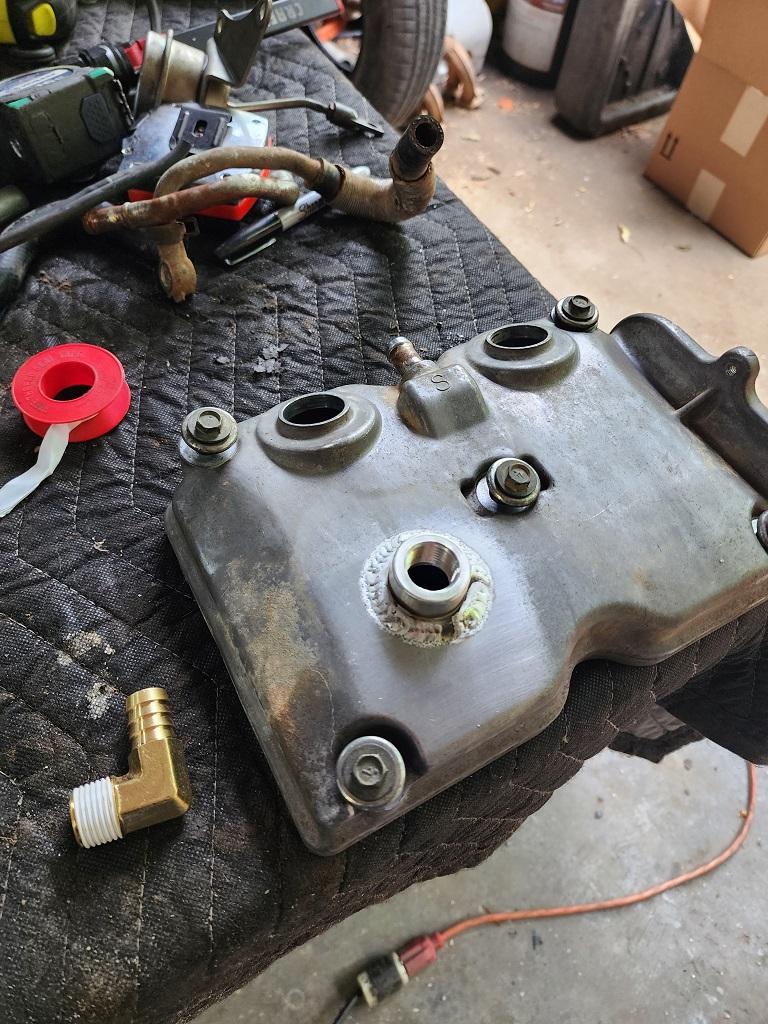
With a fair amount of room between the valve cover and frame rail I wasn't picky about location. Should have been. Oops. It ended up right next to the lower control arm mount that intrudes. So I milled off 3/16 of material on the bung, re-threaded the NPT deeper and installed the cover BEFORE adding the fitting so as to clear the valve train. 2nd time around works better. Then installed the hose (heat covering on the way) and used a rubber lined clamp to a convenient support location on the exhaust heat shield. It does get to running flat for a bit so I wish I had put it lower but at least it does NOT run uphill. That's a no-no.
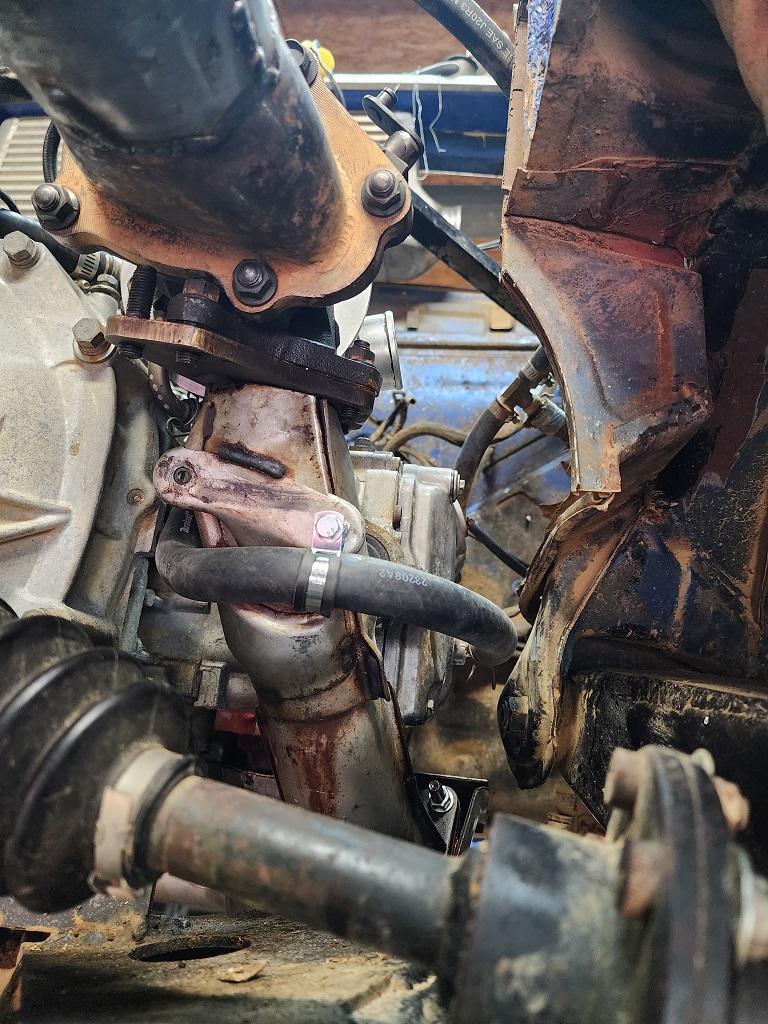
Cool bit - exhaust.
Mufflers? On a turbo? You must be old school. Not me. No mufflers on this one. Just a simple 3" S curve and a home made oval tip exit between the tail lights like a true super-car.
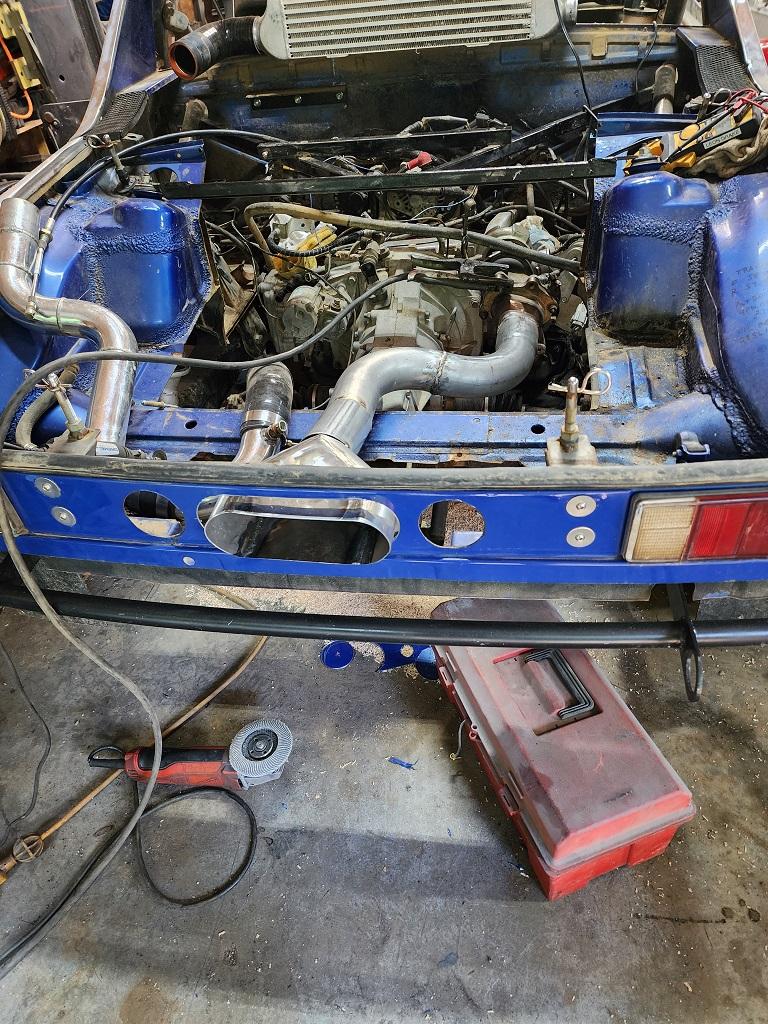
OK,a bit more welding and fit work. The whole system should not hand on the turbo so a support is required. It's hot so not nylon but aluminum is used for a block to support. But then, it will rattle and make nasty noise so I added some hold down springs like a race car.
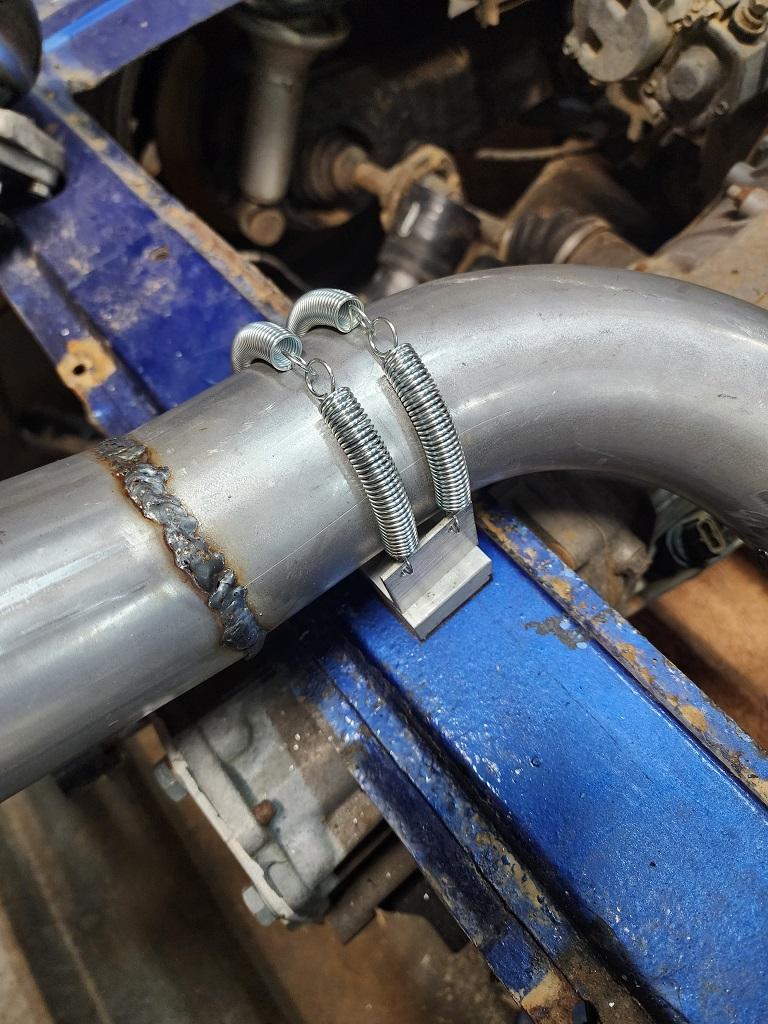
Finish weld and some paint. It will show up in more pictures later. The old outlets on each side will get some screen and dress up so it looks like I wanted it that way.
Dumb question, is there a reason you are sticking with air to air intercooling, aside from "already have the parts"?
After seeing lots of people get out the water misters to cool off their intercoolers between runs, or suffer heatsoak in grid despite that, I really really want to go with water to air intercooling. You can run the pump and fans to cool everything off between runs and they heat soak less because of the thermal mass of the water.
Well I agree with factory intercoolers located on top of the engine, water is better. But it adds complexity and plumbing. With low boost and an easy less heated location (like this) its kind of a simple go to. It may not be much heat generated on 7 psi. Now if pushing 14 or more PSI or long boost cycles like I do on another car say at Road Atlanta, so much boost for so long a lot of heat soak happens. On a 60 second run in rallycross, it's not such a thing. Street driving also where you have the engine on for 30 minutes to an hour or more the water has advantages. Each has it's place, but you can always go for the absolute best maximum cost choice and sure enough it's going to work but some of us have a budget (sometimes).
I will allow that I saw IAT go up to 140F in a single pull of a few seconds in a 9psi car. (A 421ci LS1 based car... yes it was stupid fast, quarter mile MPH estimates were 1000hp) My daily driver has a neat gizmo by Autometer that lets me see engine control data on the dashboard, it is amazing how fast IAT goes up under boost for any length of time. It's also pushing 16psi, so there's also that.
I also recognize that a rear drive car is probably going to be more traction limited so you aren't going to go crazy with boost.
I'm also from the perspective of, well, let's see how much boost we can cram into an EJ20 with an STI turbo, with the all wheel drive to be able to utilize that. If 10psi is good then 20psi is better as long as the transmission can hold up and there's still a good supply of 100 octane unleaded 
And so, with a turbo comes another gauge. This time the fun meter gauge.
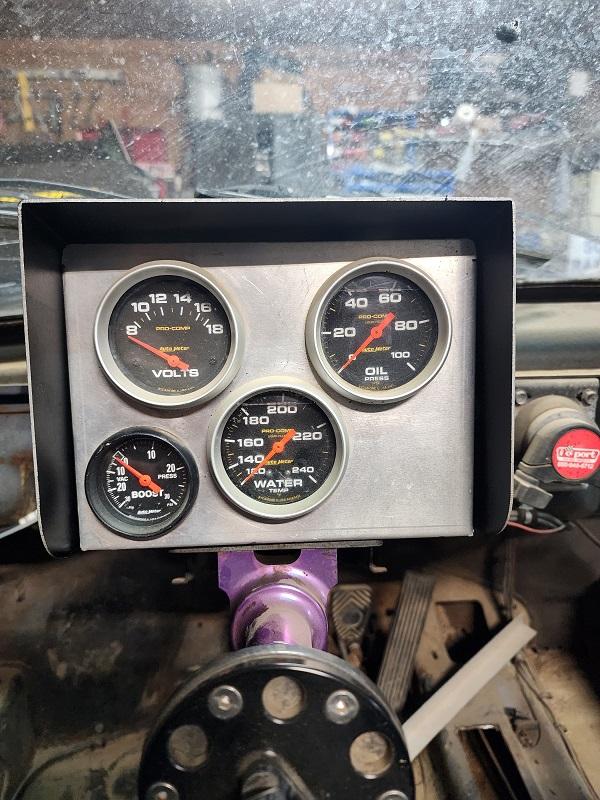
In addition, the DEI heat protection sleve for the oil drain came in so....
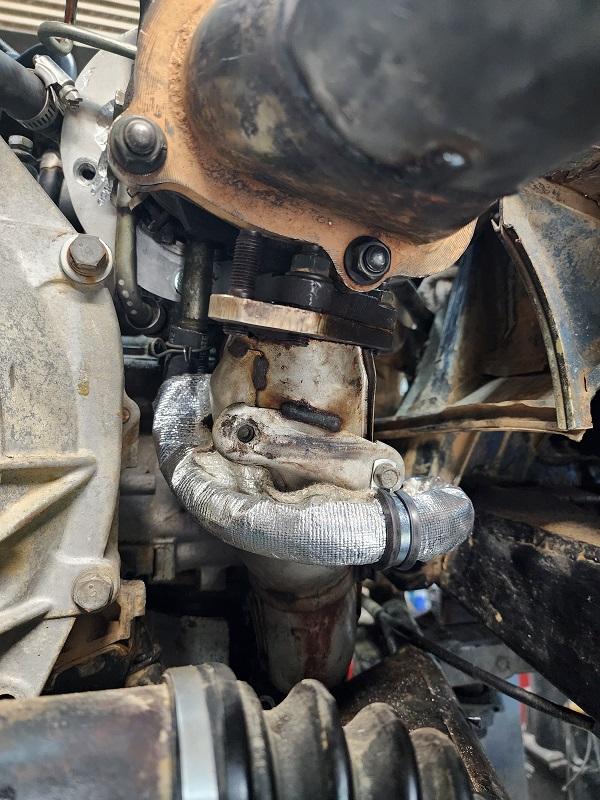
Then, there are always the brackets for everything. Little, big and all sizes. The Intake tube on the left was all floppy on the rubber couplings so to prevent it hitting the braces or rubbing a hole (disaster) it needed to be clamped in place with a silicone sleeve wrapped around it. 1st, make the little tab to bolt to the clutch hose bracket.
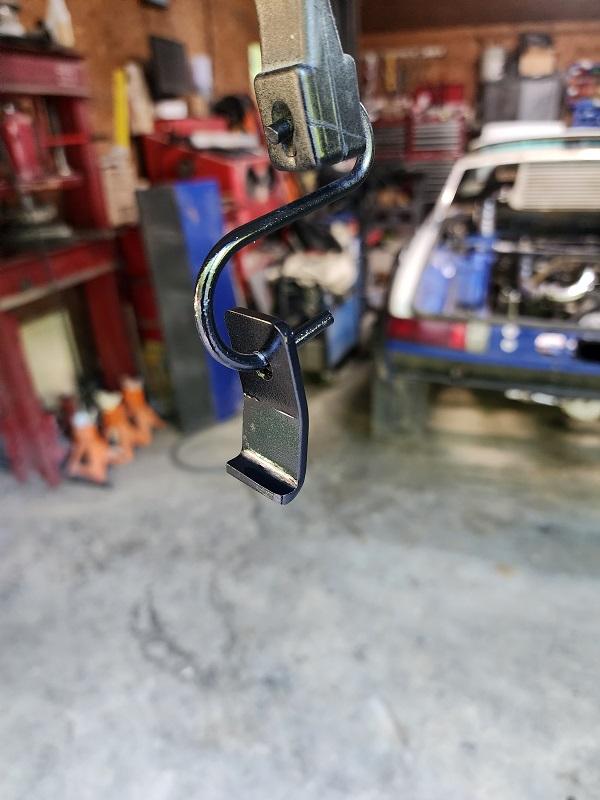
Then after paint, install it with clamps around the protective sleeve. Kind of a pain since it's right on a curved section but it's tight and will prevent damage.
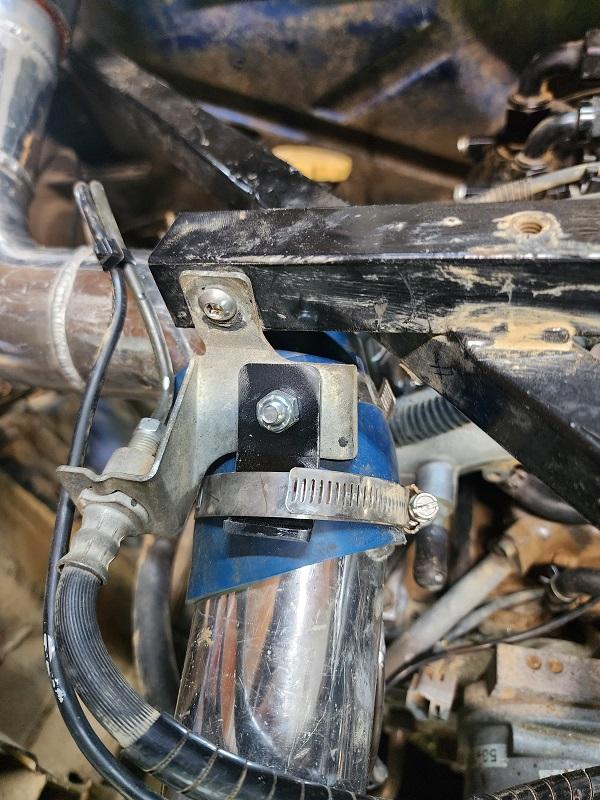
So with all that done, the hoses installed and things tied up it'stime to move onto the new Haltech re-wirejob. Unpin and label every wire I will need from the factory ECU. I use small wire zip ties that have a tag where you can write on them with a fine sharpe pen.
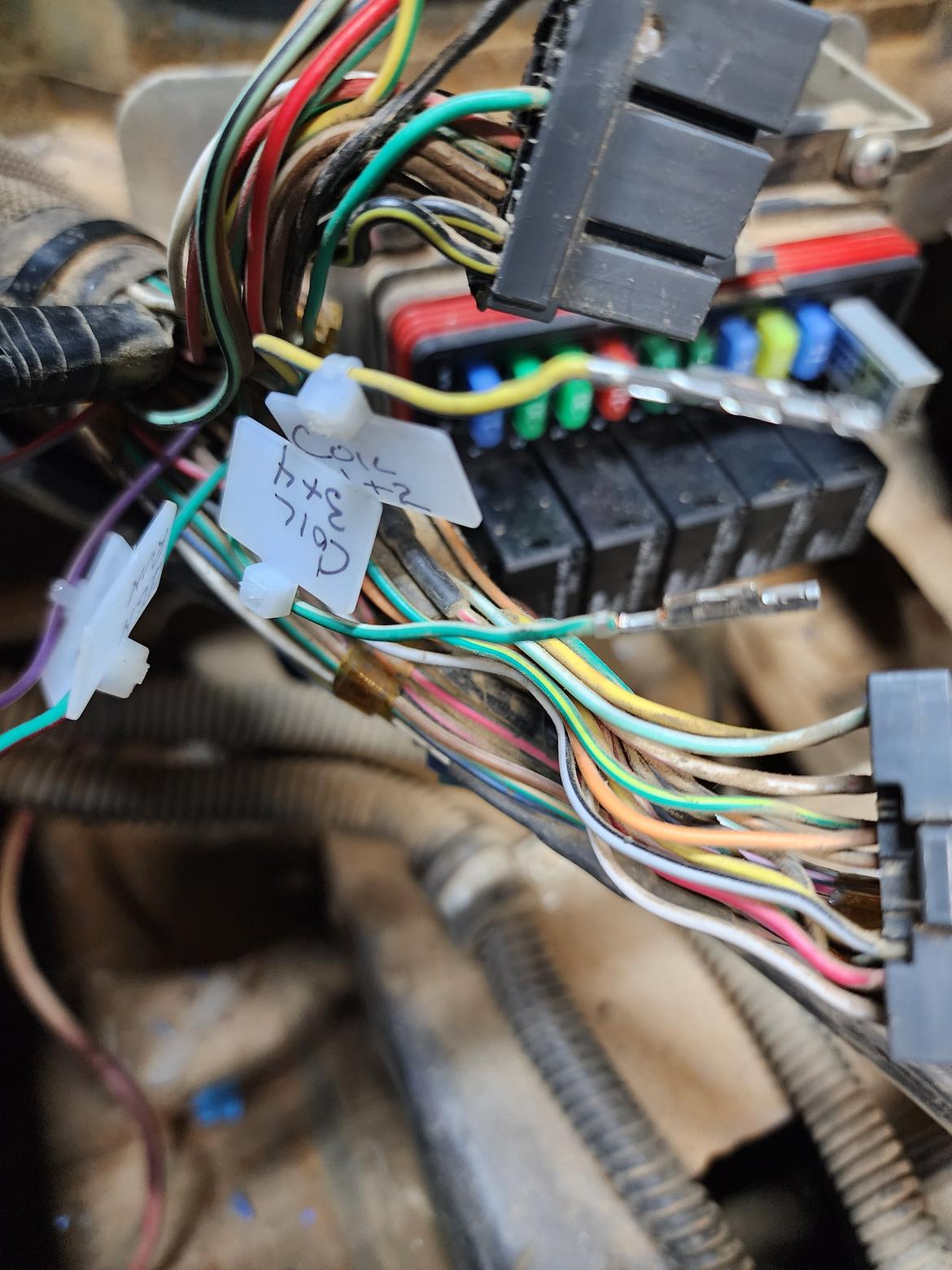
That's where it's at right now. I'm waiting for the new Turbosmart waste gate so it won't start out with too much boost. Due in a few days. Hopefully then in a week, I'll have the Haltech wired and ready to download a base tune just to start it up for the dyno shop. Hang on. It's getting close.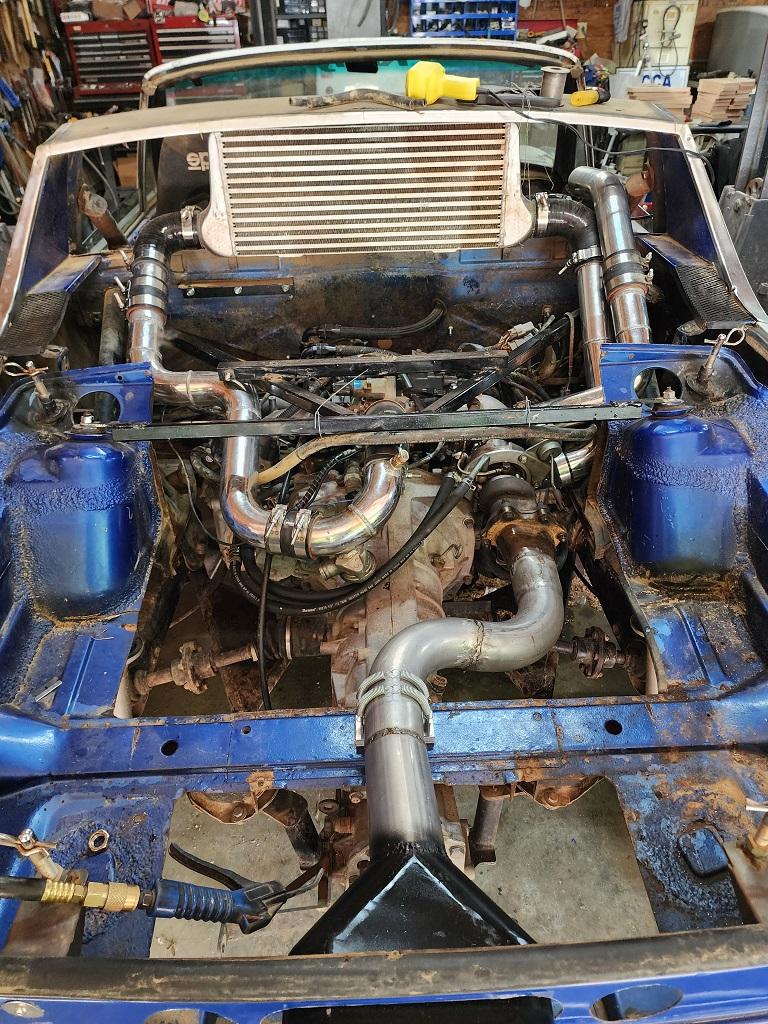
NOW were getting there. IT RUNS. On a base map that will need a lot of rework due to the injector resize but hey, it's loud and proud. Make turbo spinning noises. Yes!
I had to rework the intake air plumbing because the Turbosmart waste gate was bigger on the back side but it's solid and will be fine. No compromising.
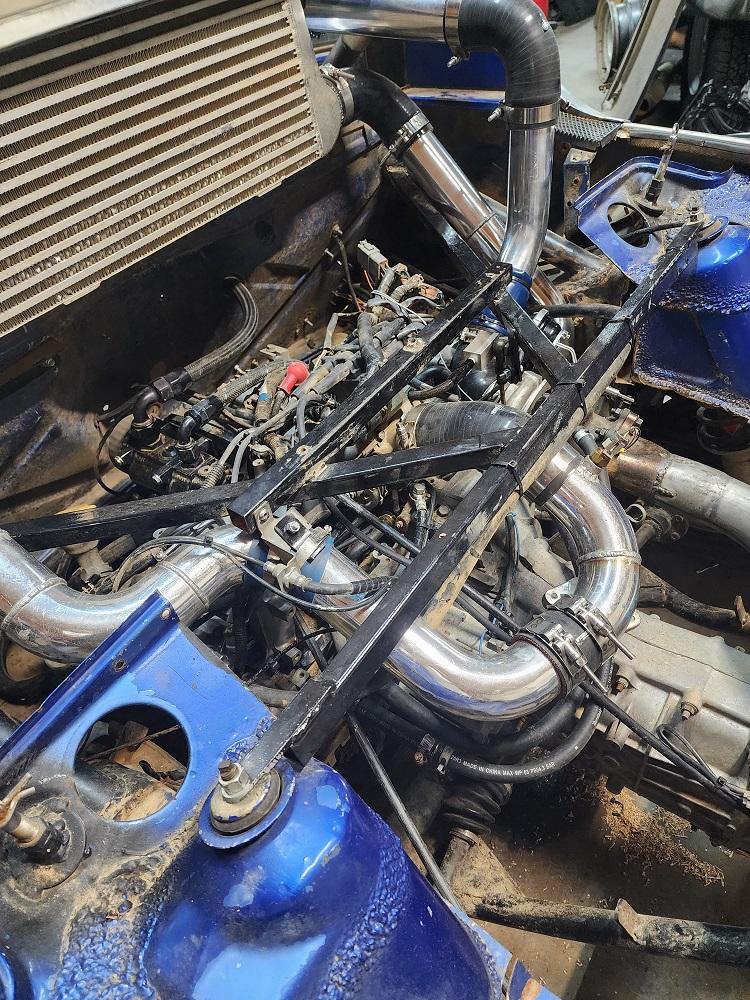
The Haltech is installed with a CAN bus wide band O2 sensor option. Some clean up of the wiring now that it's running. It's located on the firewall in the middle.
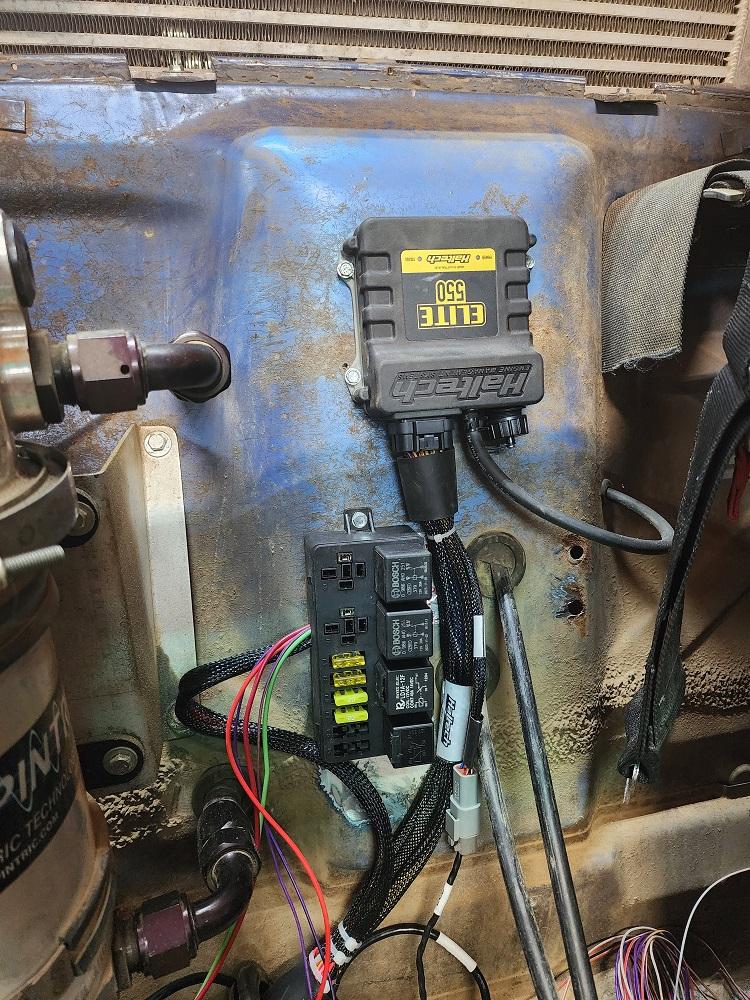
So I still have tuning to go on July the 8th. I'll post what we get. Not expecting a big number, just more than before and no damages. Next post will be the roof panel going back on with the roof vents to feed fresh air into the cabin area, air intake and intercooler.
Not a whole lot of how to do it but since it's straight forward here's the roof vents. These create positive pressure in the cabin to keep dirt out and to feed the intercooler (and me). Just a tune away from greatness.
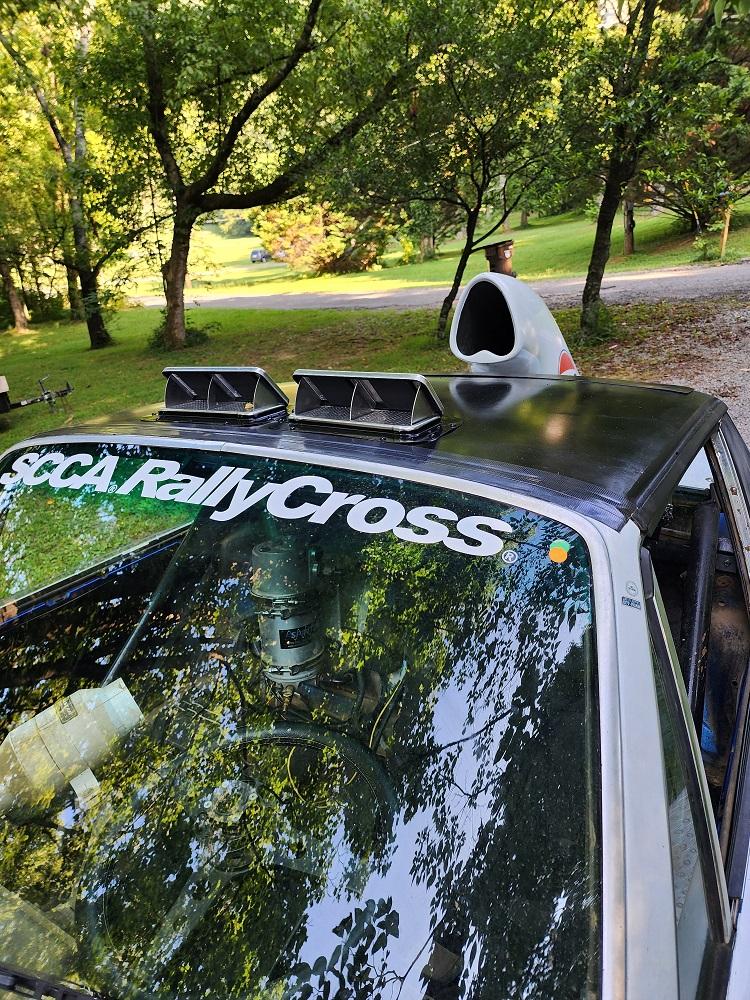
Dyno day turned out great. I was hoping for maybe 170HP at the crank. So around 140 something at the wheels. We beat that with a mild tune and 7 PSI boost it made 188.6 HP and 209.4 Lb Ft at the wheels. It's going be a significant boost this weekend at the track. STOKED.
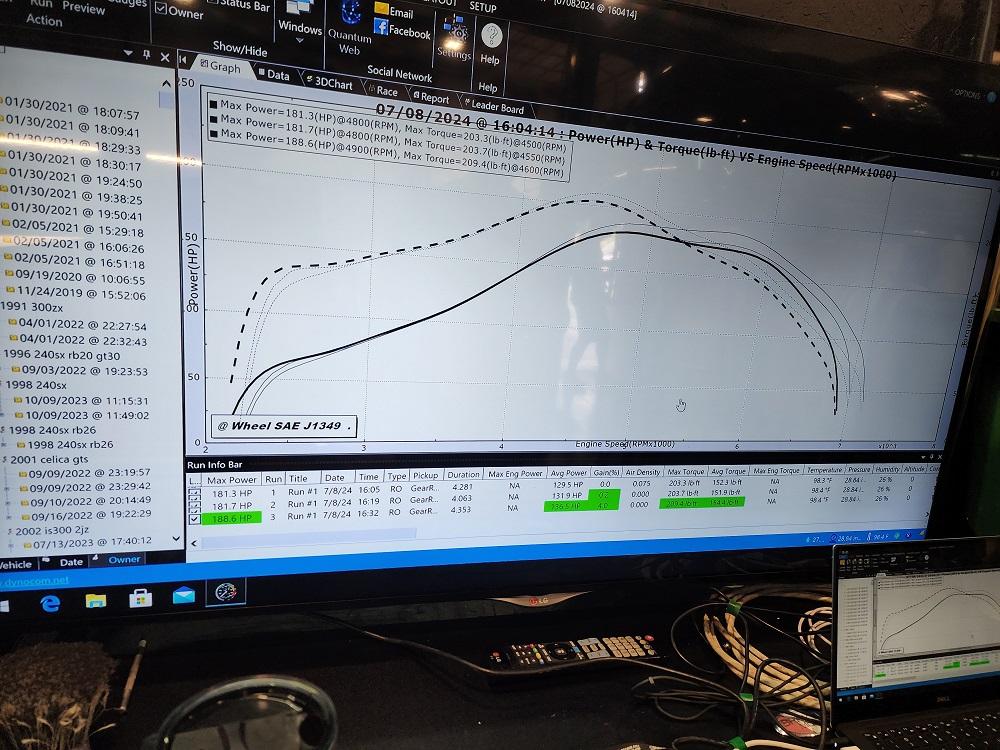
It drops off hard over 6000 RPM. I'll be looking into that but that upper range is more about not needing to shift than getting there. It lives in the 4-6000 RPM range and that's where I spend most of the time on track. Being able to now go all the way to 7K (and a bit more) is going to help a lot in those faster courses.
1st actual race day and it was amazing! Almost no lag and MORE POWER. Really pegs the fun meter. I can't even think of how to make it better right now.
In for results and a recap
Awesome! This is one of favorite cars on here, glad the engine swap paid off.