Working with hot metal has always been something I enjoyed. Mostly cut to fit and weld, but I've always wanted to try my hand a blacksmithing.
In my craigslist wandering, I finally came across an anvil that was in good shape, close by, and reasonably priced. That's the hard part done, but now I need some way to get things hot.
The easy button would be a propane fired forge. They can be bought fairly cheaply, or built, but I really didn't want to listen to a propane burner running WFO for hours on end. With that in mind, I decided to go with a coal fired forge.
I'm building what is called a brake rotor forge. It gets that name because the fire pot is a cast iron brake rotor. I happened to have a brand new one in my pile of scrap, left over from the 635. With the fire pot figured out, next up was a base and table. I wanted something decent sized. Tuesday I picked up a couple of empty 55 gal drums for cheap.
This morning I cut a hole in the bottom so the brake rotor would fit flush and built a table for the coal pile.

Still to build is the blower system and ash pot.
More to come.
Cool! I have never heard of a brake rotor forge.
I was just thinking about a project for the Rangers old rotors. I'll be following along closely.
Neat. I'm going start on building a propane one. I'm using railroad track chucks for my anvil. I haven't been able to find a decent deal on an anvil yet.
Do you follow Alec Steele on YouTube? That kid has talent
I've only made a few knifes. Used scrap rebar to start with.
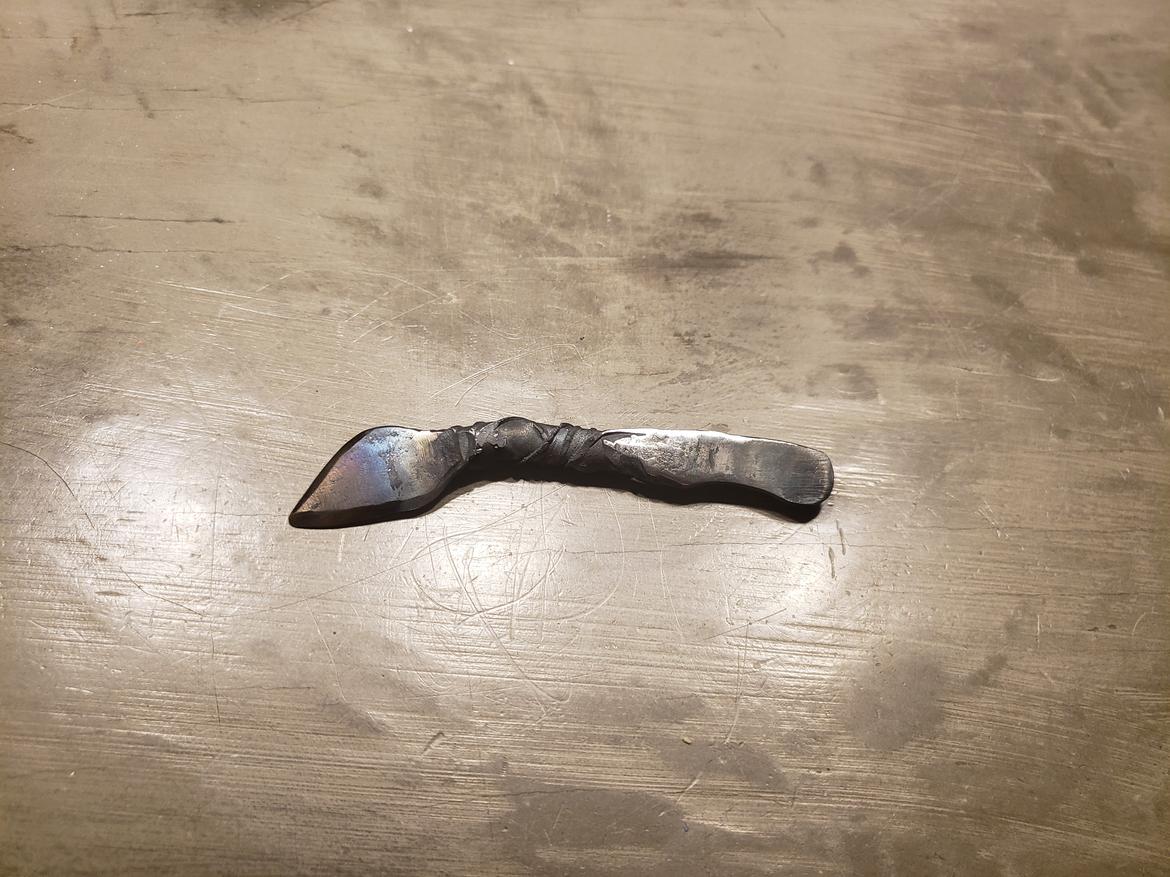
Nice!
Almost got into metal forge but going foundry first. Had a Champion 400 hand cranker but sold it to a experienced smith. Blacksmith classes here, just 20 some miles away, kinda pricey tho.
Following along.
Good luck!
I gathered most og the parts to build one of these a few years ago, realized I didn't have time or space and scrapped it all. Someday.
Also anvils always seem to cost more than I usually spend on whole cars.
There wasn't any 2" iron pipe to be found today. I considered using exhaust pipe but decided to stick with iron pipe. Amazon is shipping me what I need to build the blower system.
All the pipe fitting showed up Friday so after spending the day cleaning yesterday, it was time to get the forge working.
The pipe is used for the air inlet from the blower. With that in mind, I bolted a floor flange on to my brake rotor and screwed all the parts together.

Air comes in from the blower on the right. Ash can fall out the bottom.
The bottom also has a door that keeps the air from blowing out the bottom.

And open.

The blower is a cheap yard blower for now. It turns out that is way too much air so it will be getting changed out for something less powerful. Even with the speed control turned all the way down it was blowing coal out of the pot.


Naturally, I had to fire it up and see if it worked.

I even pounded some steel into new shapes. Unfortunately, I also cracked it several times while trying to make a coal rake. My right arm now feels like a noodle. I need to do some research and figure out if it's the cheap steel or the process that is making it crack. I initially thought it was due to overheating the steel, but the last crack happened even though I was being very careful.


RossD
MegaDork
9/23/18 3:09 p.m.
Use a butterfly valve at the blower outlet
In reply to RossD :
A ball valve would do the trick but I have a old heat gun that I think will work. It also has the advantage of being quieter.
Finally got around to playing with this thing today. Even after switching to a 2# hammer my arm feels like a soggy spaghetti noodle.
Good news though. I figured out why the steel was getting brittle. Apparently if you get it too hot, it burns all the carbon out of it leaving you with plain old iron. Which it brittle.
With that in mind I made me a forge tool. I started with a 1/2" rod because that is what I had on hand. I drew it out and squared it. It has a blade on one end for dragging coal into the pot, and a spike on the other for cleaning the air grate in the bottom of the pot.
It gave me a lot of practice managing the heat and the fire. Metal doesn't have to be super hot to form it.

Pretty sure I still have a lot to learn.
bigfranks84 said:
Do you follow Alec Steele on YouTube? That kid has talent
He's talented but he's really annoying.
I've been watching a couple other blacksmiths who are also very good,but aren't nearly as manic as Alec:
Torbjorn Ahman and Paul Pinto
Torbjorn is outstanding. Thanks for the other name.
And i know what we’re building this winter. My son is 7 and wants to learn blacksmithing