Ok, got a bit behind on my posting here. Few hours on Sunday got the new seat trimmed and fully mounted. It is a big upgrade, for free!
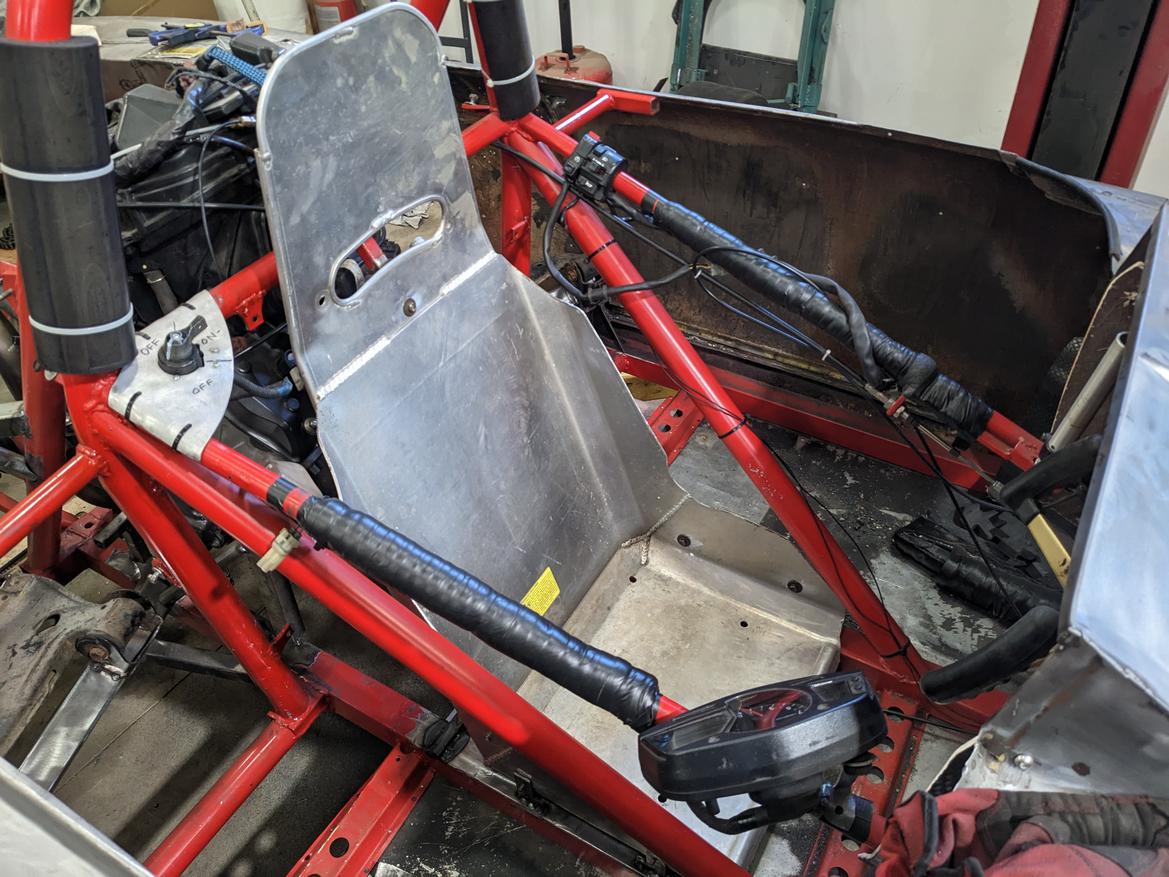
I was able to re-use the bolts from before, and I used the Datsun door hinge backing plates to make the tabs to weld to the frame. The backing plates were already the right thread. In fact, the bolts for the seat may have been door hinge bolts originally. Who knew?
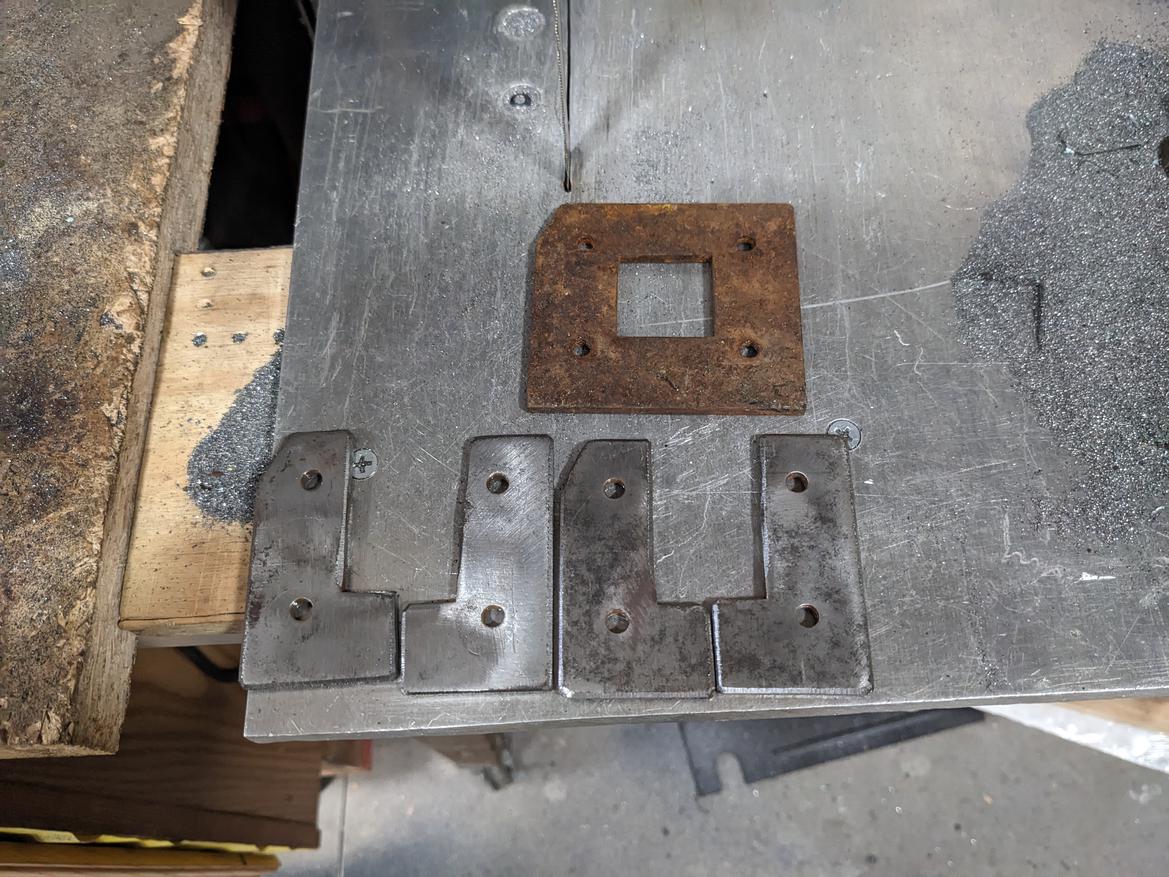
The seat cover will require just a few cuts but will wrap around the bars to provide extra elbow and knee protection.
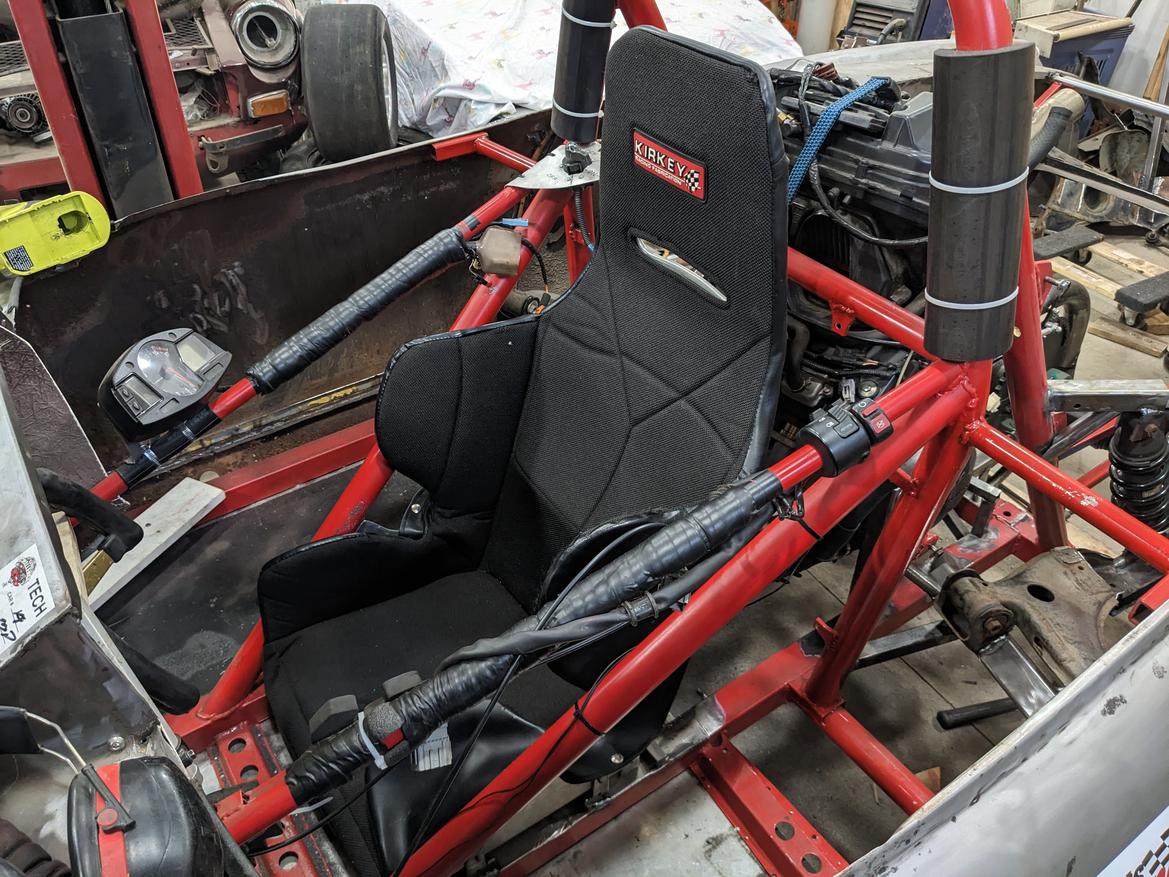
I also got out a harness and made sure I had good locations for all the straps. Done!
Next I looked at shortening the exhaust and mounting the muffler. Over the years I've mounted this to many different things, but it has always been way up high. The tubing is titanium, and I cannot weld it, so I've been hesitant to modify. But now that the engine is turned, the muffler ended up not only way up in the air, but also pointed at an angle and off to the side. Aaaand much too close to the gas tank for comfort.
So I grabbed the band clamp I traded to stampie like 2 years ago (for a Datsun wiring harness), and got to work.
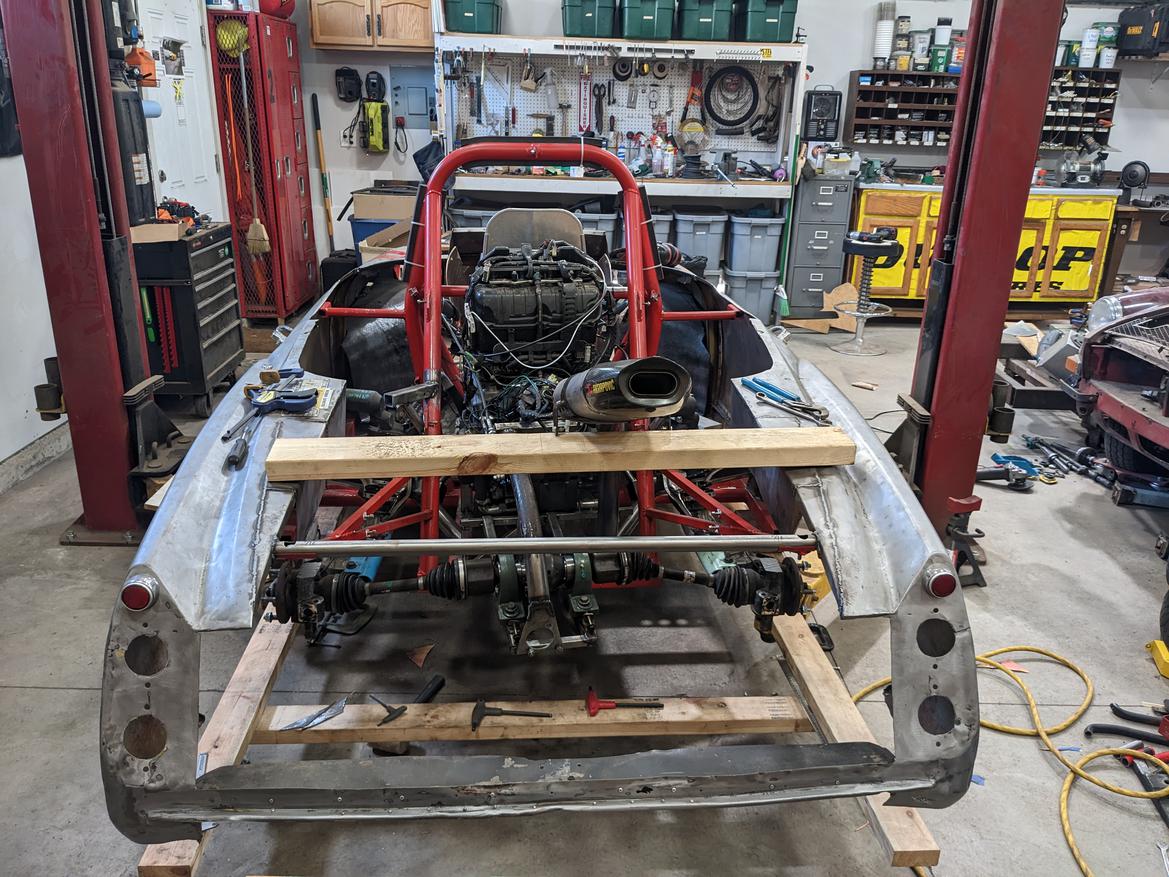
With only a band clamp, basically my option is to shorten a straight section.
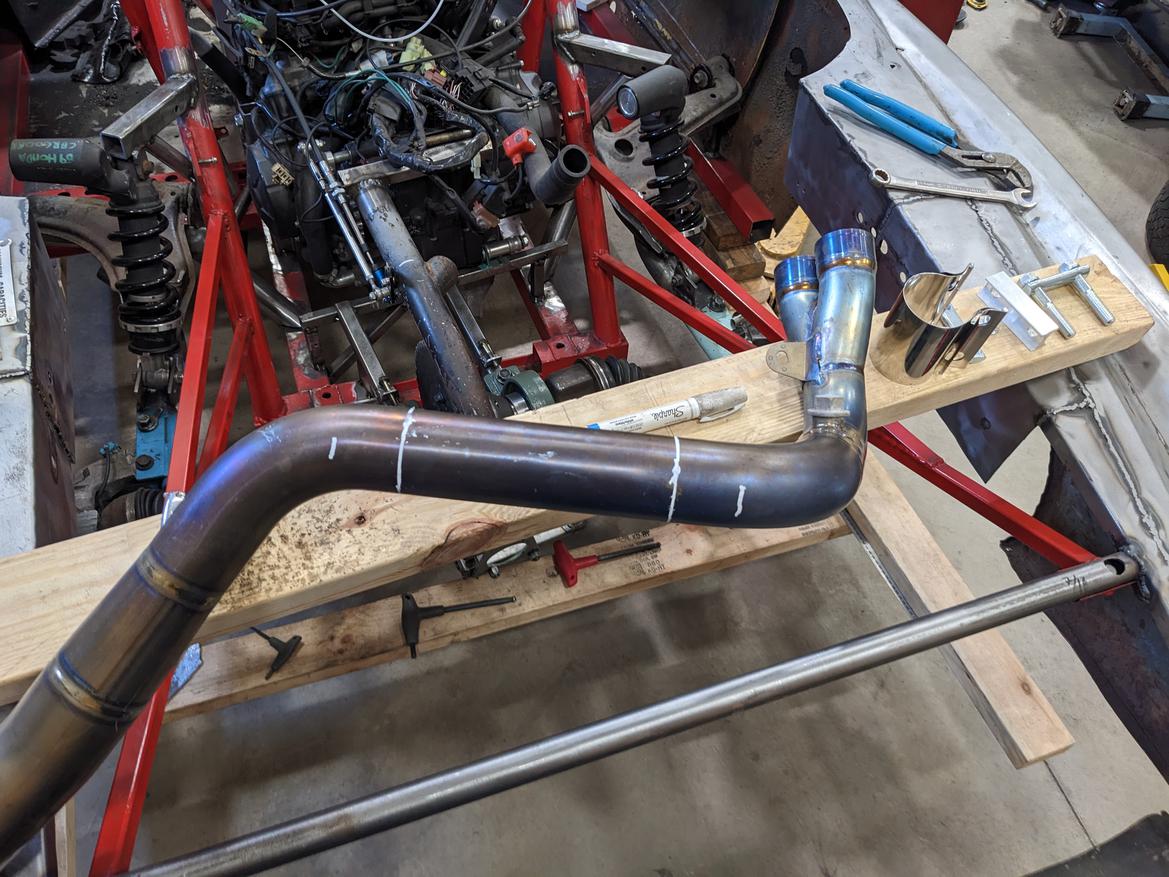
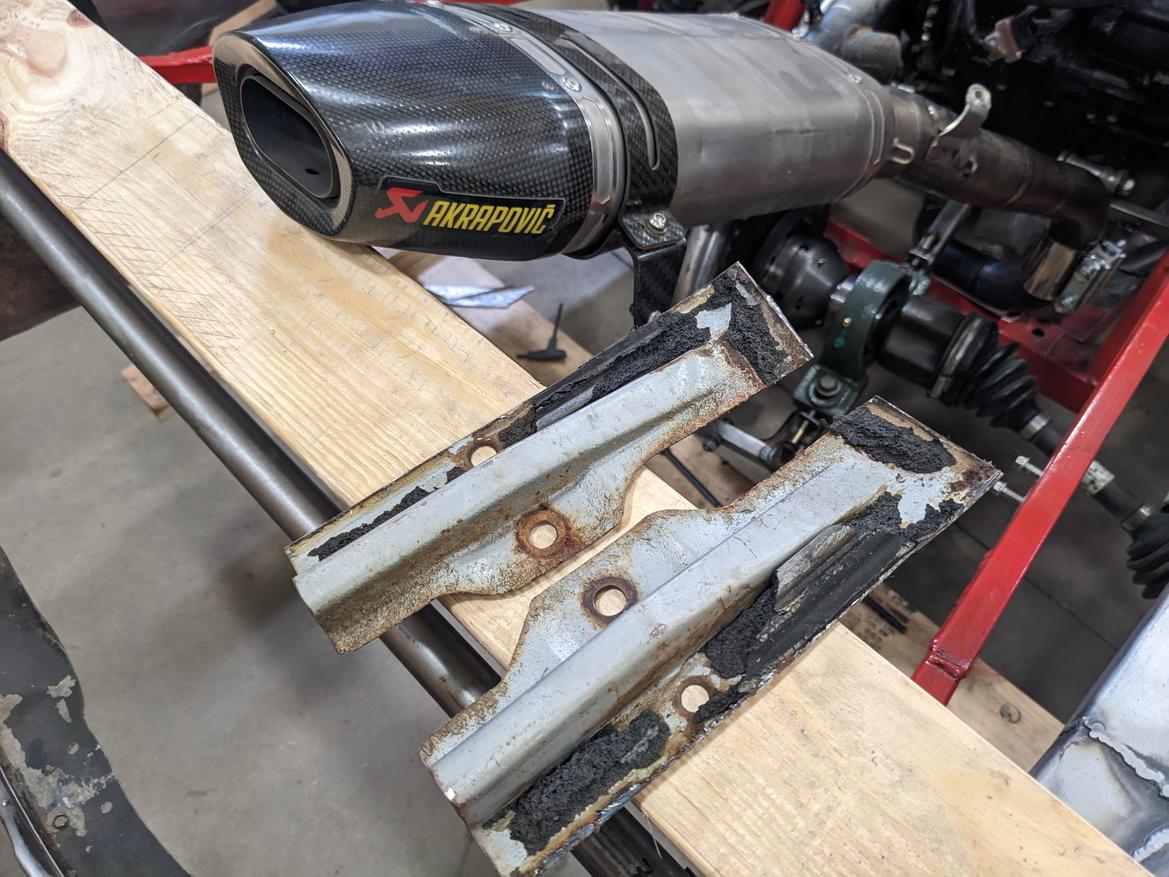
I found these stampings in my scrap pile, they are originally trunk lid support structure around the hinge mounts.
And now they are muffler supports!
Muffler is lower, straighter, still not centered, and much further from the fuel tank.
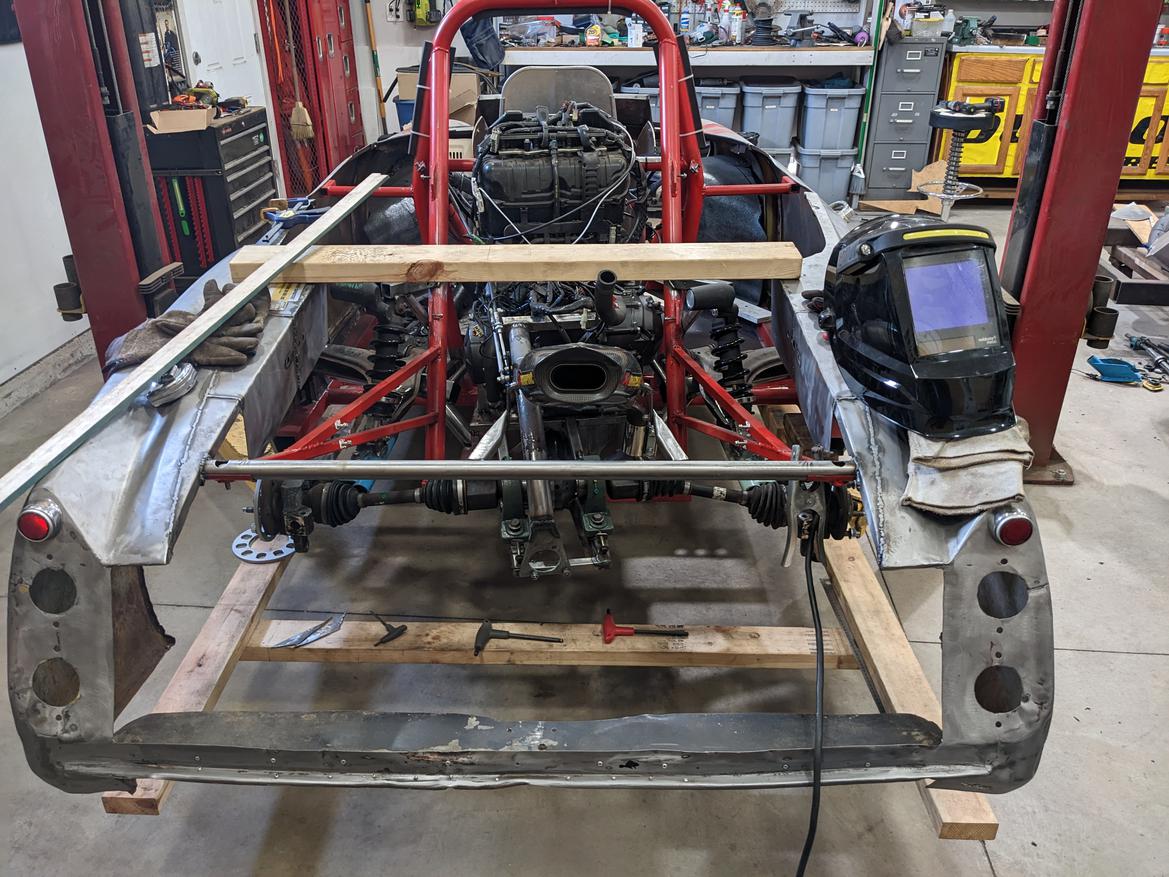
And here's the band clamp where it ended up.
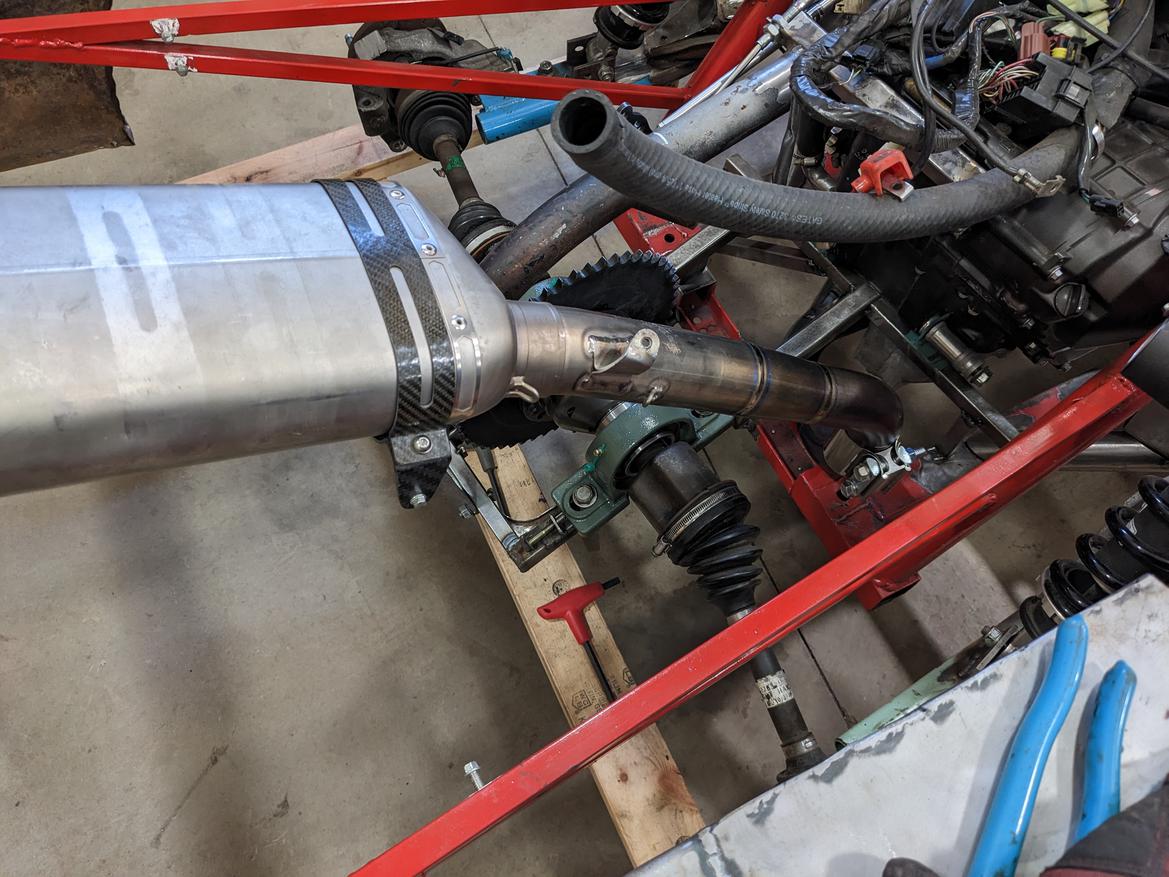
772 hours.