So here's the story. It's really two stories.
The details on the engine are the shorter story. It's a Model A 'banger with some pretty rare speed parts on it. First, the head is a Miller/Schofield. Harry Miller of Indy fame (Miller eventually became Offenhauser which became Meyer/Drake--all won a lot of Indy 500s) sold his company to an investment group left by a Schofield and around 1929 put out a Leo Goosen/Harry Miller designed OHV conversion for Model A Fords. Schofield went out of business pretty soon after and the patterns etc. for the head were purchased by Bell Auto Parts. They made some adjustments and sold the heads under the Cragar name for many years (same brand as the wheels but before the wheels). The history is murky but the Schofield heads were only made for a year or two so they're rare. Next, it has Winfield carbs. Ed Winfield made carbs but later became much better known for his cams. Winfield carbs were nonetheless sought after by racers as he was a sharp guy. The air filters are really cool, and they're fairly new. There's a guy called Crafty B who makes cast aluminum parts. His flipper gas caps are on many famous hot rods. He made those air filters for Nick, and didn't make any more. 2 of 2. There's also a magneto on it that I don't know much about yet, plus a few other neat bits.
The longer story starts with this Jalopy '34 Ford race car called Tootles. Nick always has interesting stuff come his way and this car was one of his for a short while. It looks way better in this photo than it was in person It had no floors, just a race seat, pedals, and steering wheel. It was junk, but it was a real deal jalopy. The most interesting feature was drilled lightening holes. I've never seen more drilled holes in a car--hundreds of 5/16"ish holes in the brake backing plates, holes everywhere in the frame, firewall, radius rods, and more. Thousands of lightening holes, likely to the point of destroying the structural integrity. And yet the car survived, and Nick ended up with it.
He used to letter a lot of race cars and hot rods and he did a couple for a serious Model T and Model A speed freak. 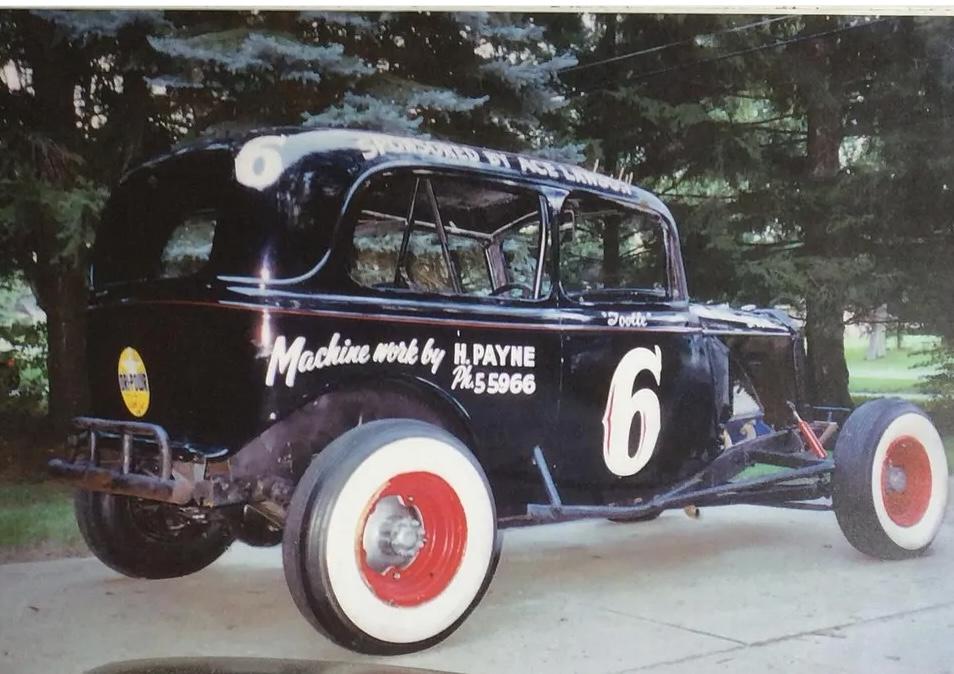
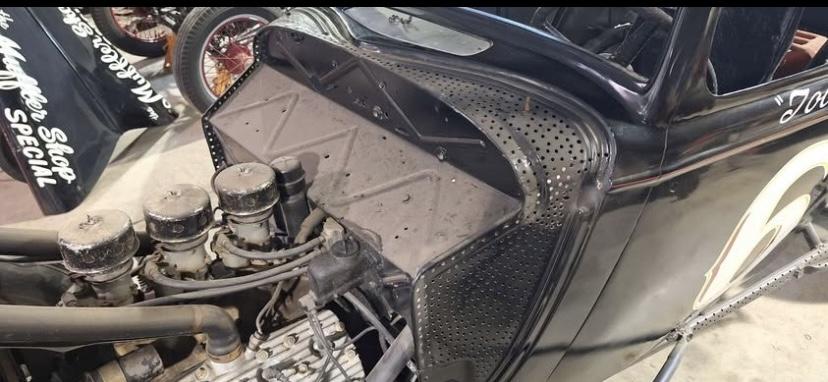
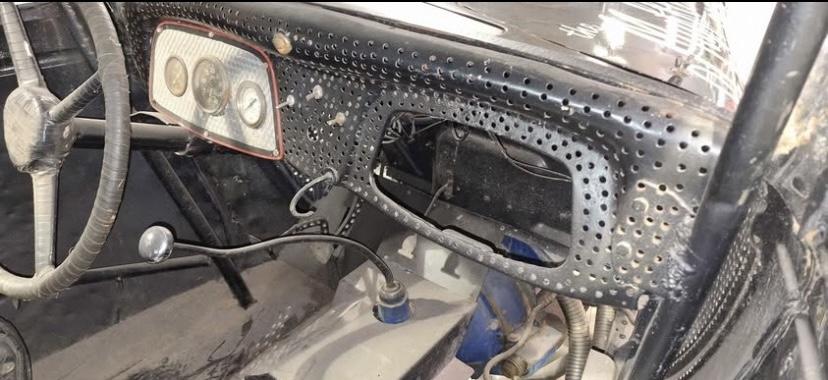
(edited to add speed hole photos)
Long story short, he traded Tootles for the 'banger engine that this guy had in his inventory. He then set out to build a car around it.
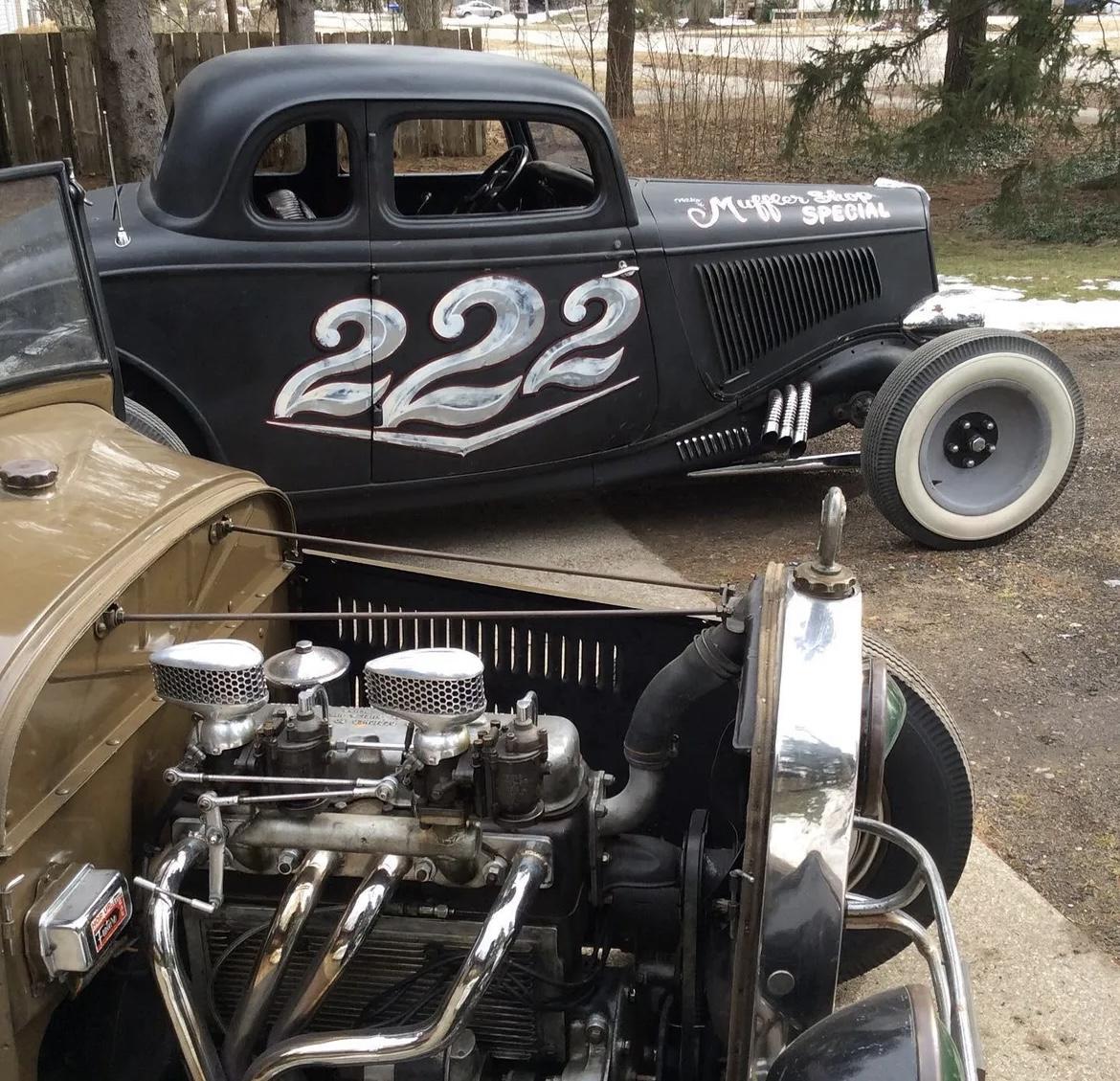
The car was a 1929 Model A Roadster Pickup on a 1932 chassis with all kinds of vintage speed parts on it. Nick has been at this for a long time and has painted/lettered cars for everyone, so he never has trouble finding rare parts from his friends.
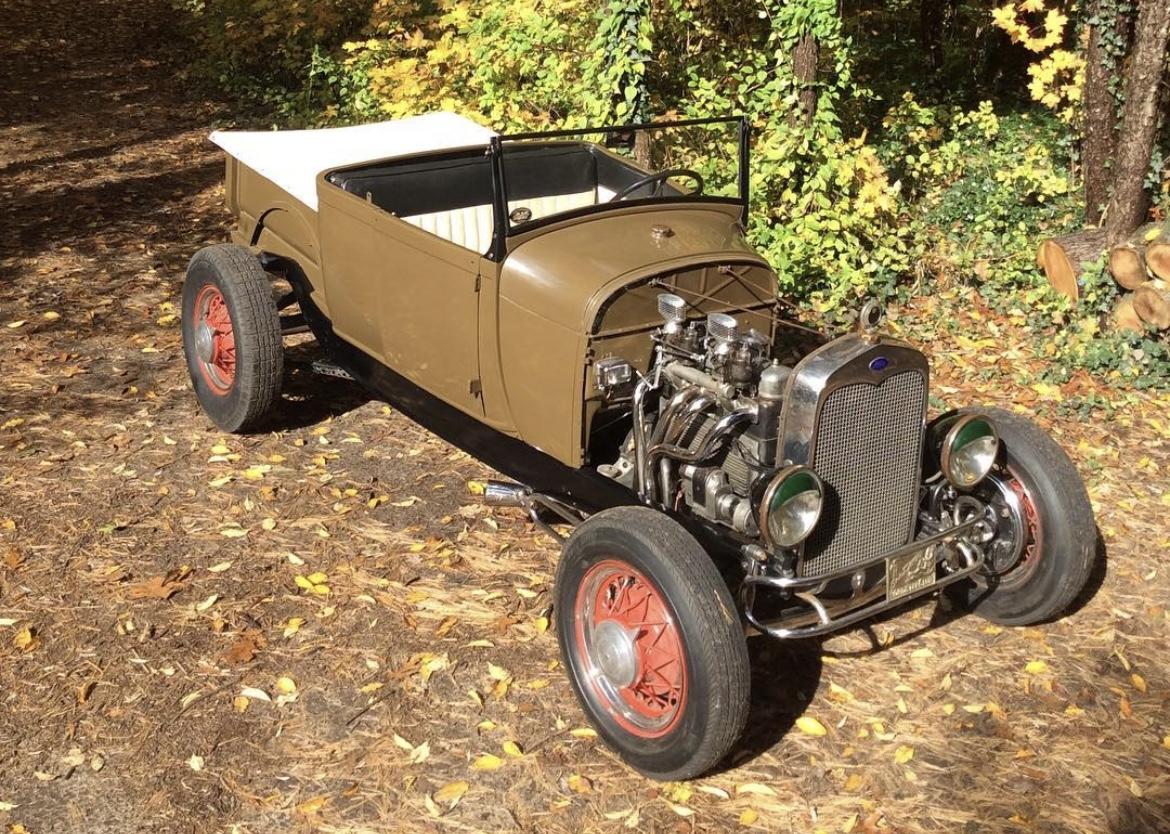
Nick's cars often evolve as he gets bored and changes things up. The pickup was no exception.
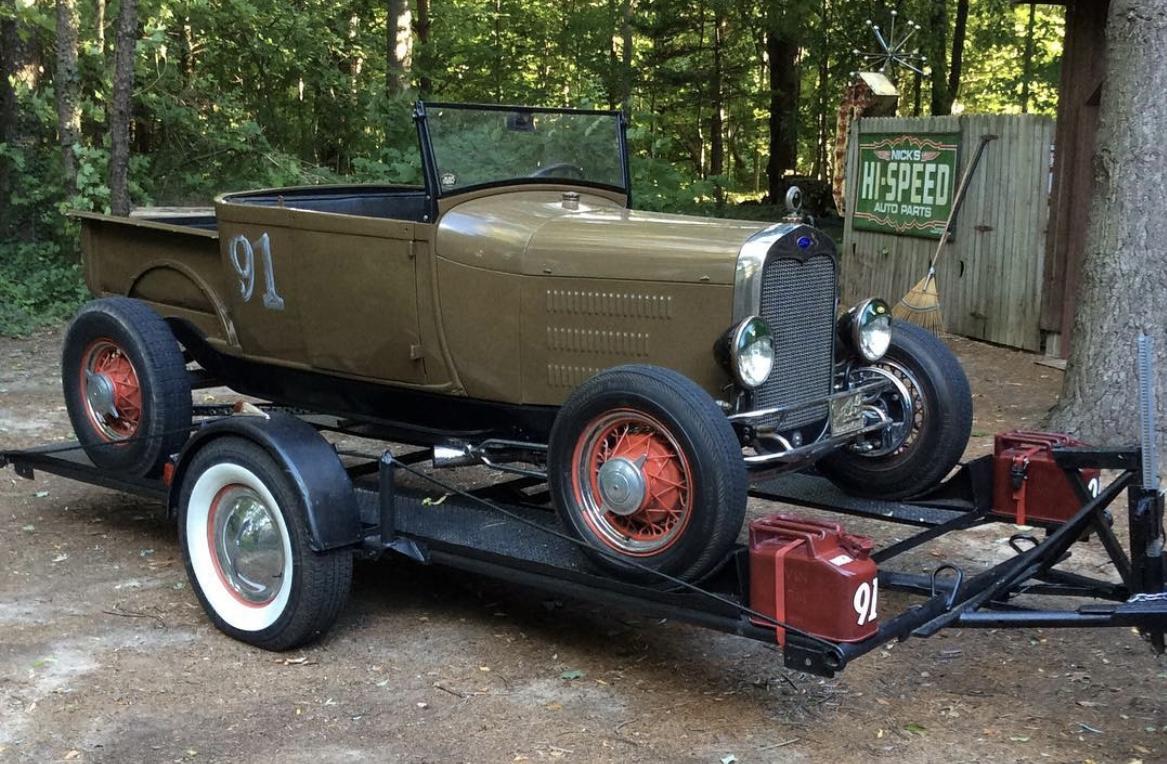
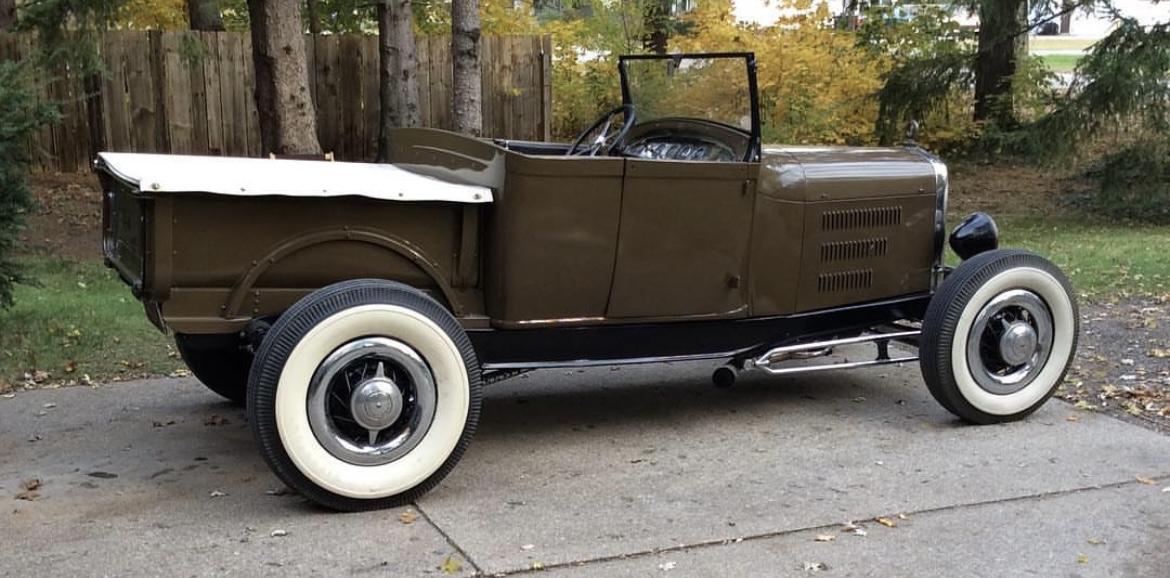
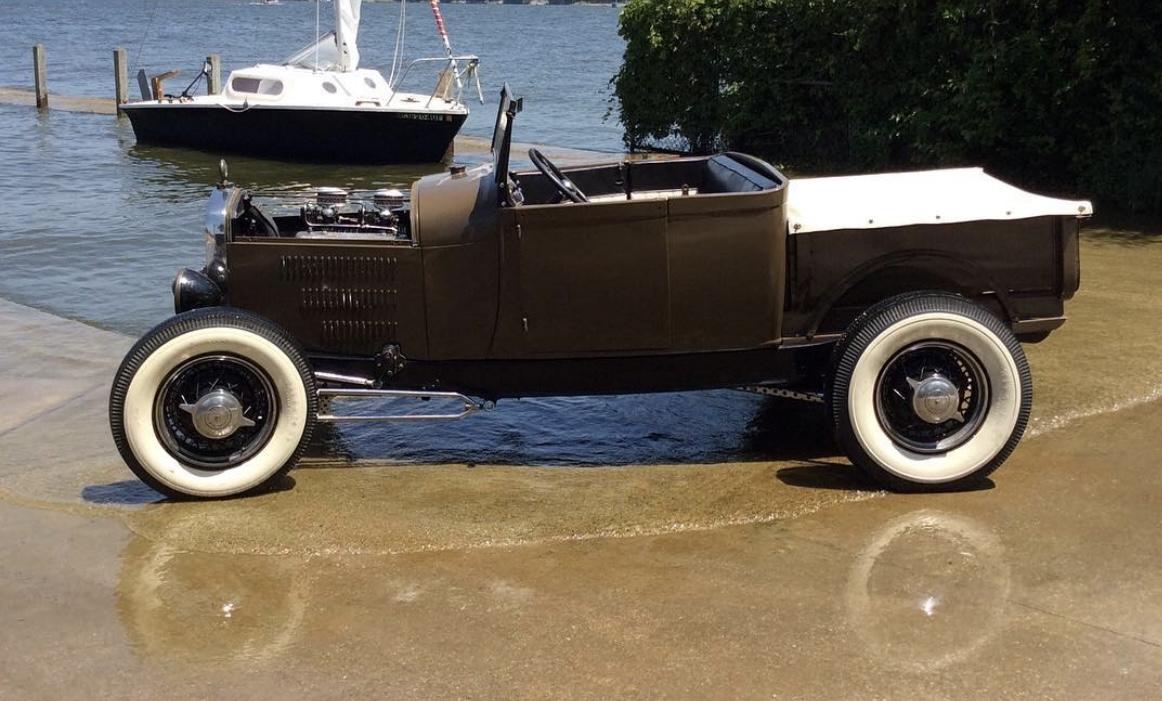
He especially played with the wheels and tires and various versions of hood setups. Not shown, but it eventually had early Halibrands on it.
Nick's built a lot of cars that have ended up in magazines and books, with several covers. One of his cars was featured in many full page Coker Tire ads for a few years. He's known as a hot rod artist, and when he finishes a car, he usually gets offers, sometimes from serious collectors.
He sold the roadster pickup fairly locally and the new owner is taking it in another direction. When the engine became available, I bought it. Nick was pretty happy about that.
Nick's almost 80 and slowing down. He's really enjoying working with us to put the engine back into something cool. But we're the ones having the most fun.
TL;DR, cool engine with a lot of rare parts, came from a cool car built by a very cool guy.