More work on the TB sub-project. Basically, I made a jig to fit around the TPS actuator tab of the butterfly shaft on the PT TB when it was installed at the idle resistance setting to match the Neon one. Kind of a lot of fussing around but it ended up like this: 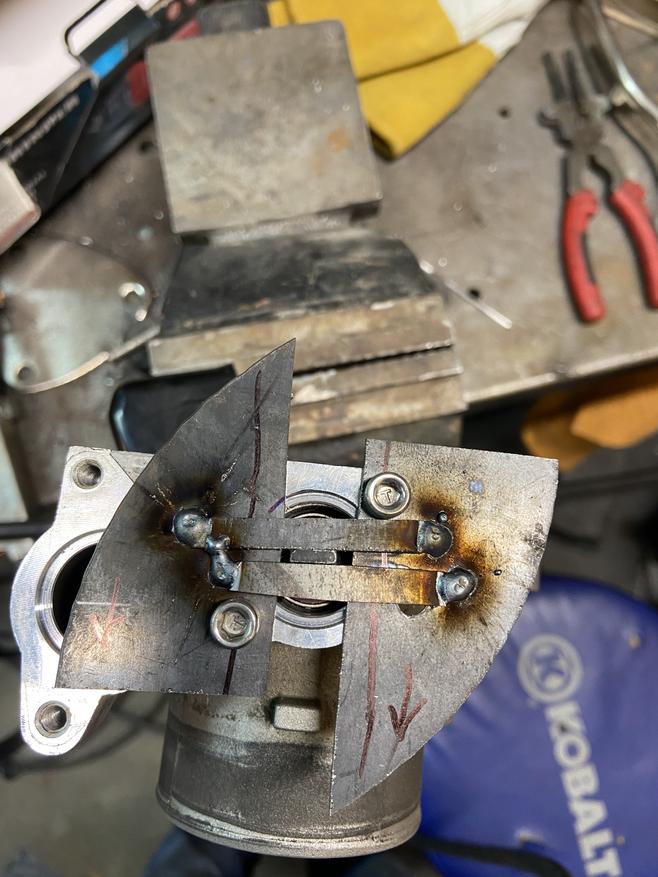
The jig on the Jeep TB shows where the tab needs to be moved to show the same resistance. 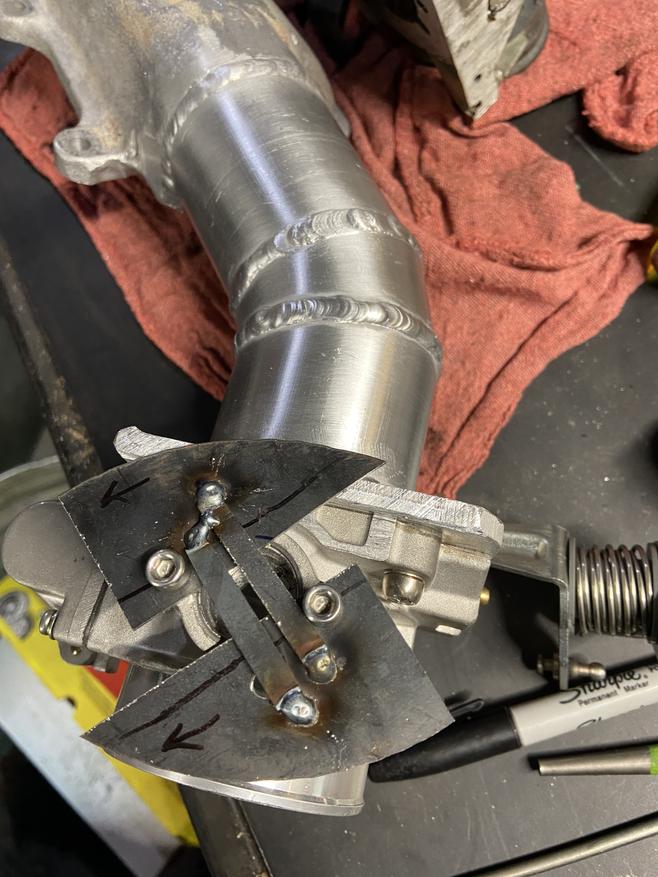
I made two cuts to almost the middle of the tab so that I could twist the tab to match the jig. 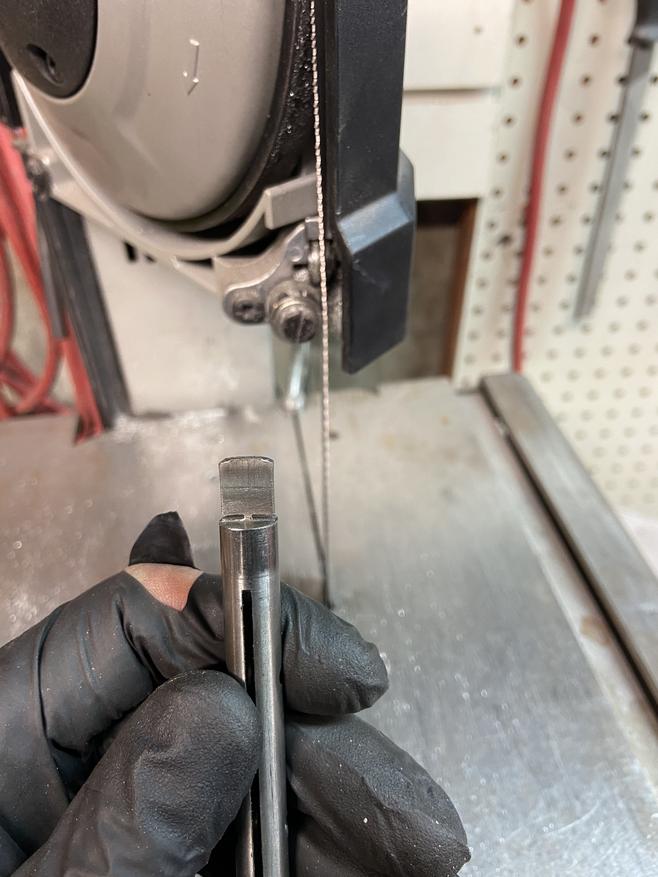
This almost worked. I got it to go into the jig but it ended up breaking off. I did think that this might happen, so on to contingency plans. I welded the PT and the Jeep shafts together to align with scribe marks, made in the jig,on the end of the Jeep one. 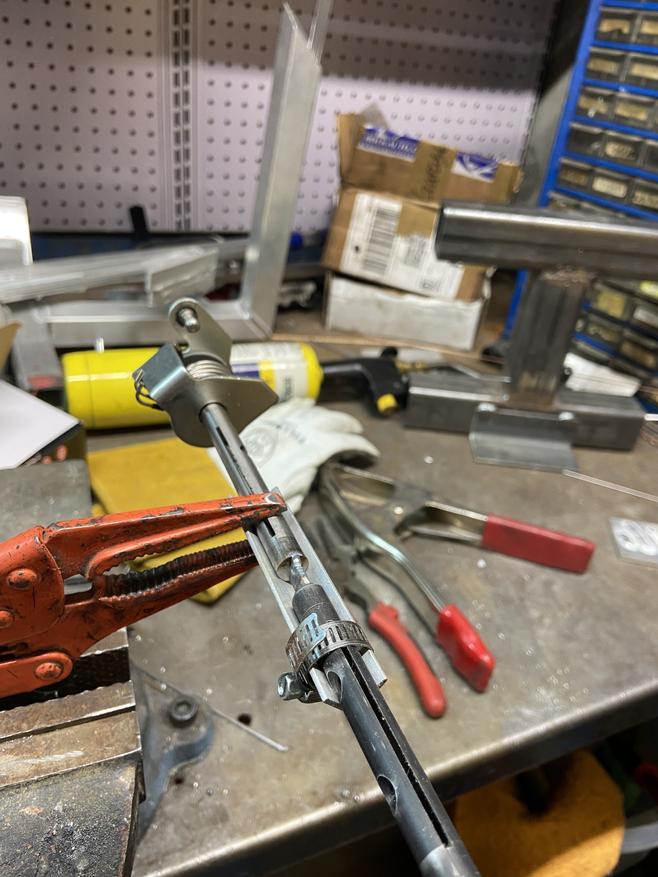
After joining, I cut off the PT shaft. It works now. 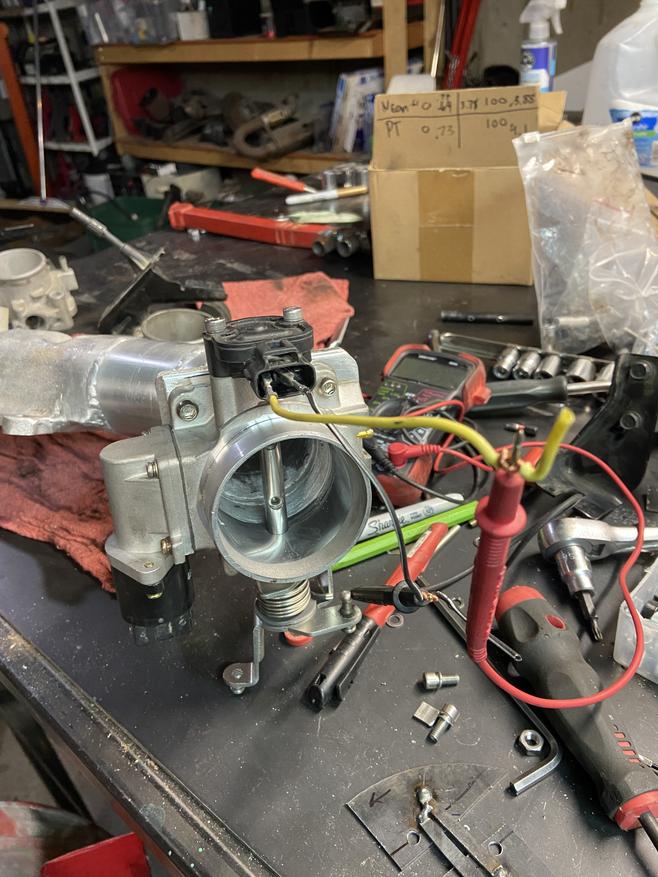
I feel good about how it turned out. I did not like the cheapness of the bearings in the TB however. The sensor side has a notchy metal seal bearing that is thinner than any of the OEM ones (All wiper seals also) and the lever side has this roller bearing that just seems a bit cheesy. 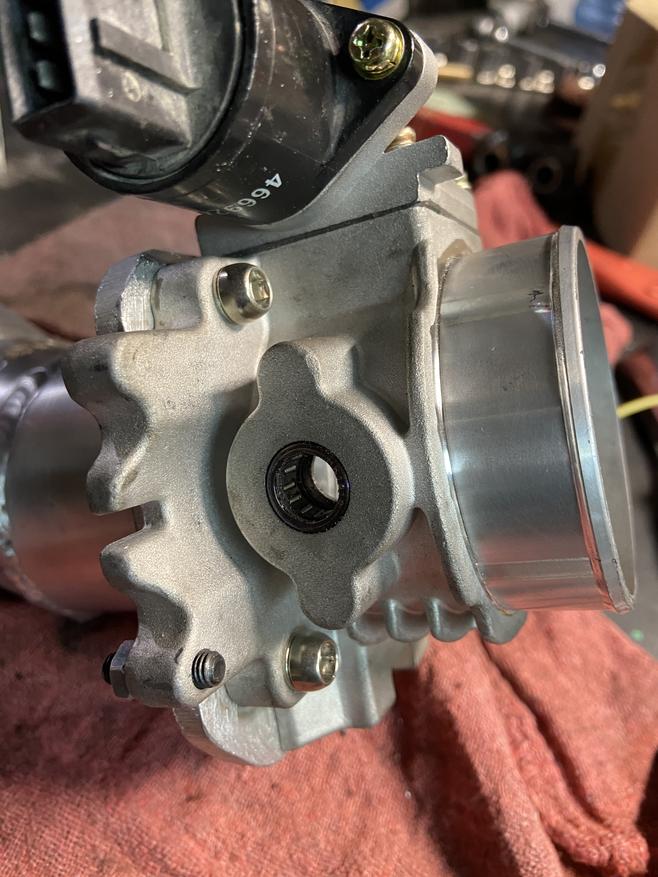
I decided to overcomplicate my life by modifying the casting to take the PT bearings which feel great and seem better. The idea is to build a fixture that the PT butterfly shaft can slide through to keep a cutting tool centered to enlarge the bearing hole to fit the better bearing. First I chopped the sensor side out of the Neon ATX TB. The idea is to use the TPS sensor mounting holes to attach the bearing inside the TB on the jig. 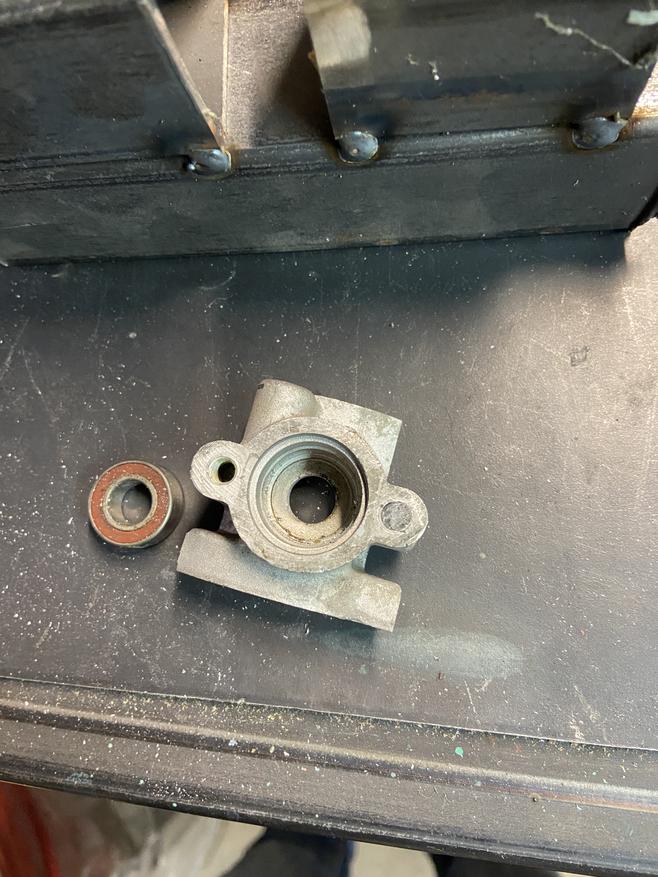
Fun fact: The PT and Jeep TBs use a larger diameter shaft than the Neons. For my purposes this is okay since the OD of the bearings is the same. I cut a piece of scrap angle iron and mounted it to the TB mounting bolts after drilling an oversized hole to fit the throttle shaft. The shaft served as a guide to allow the three bearings to all line up. With the mounting holes done I had this: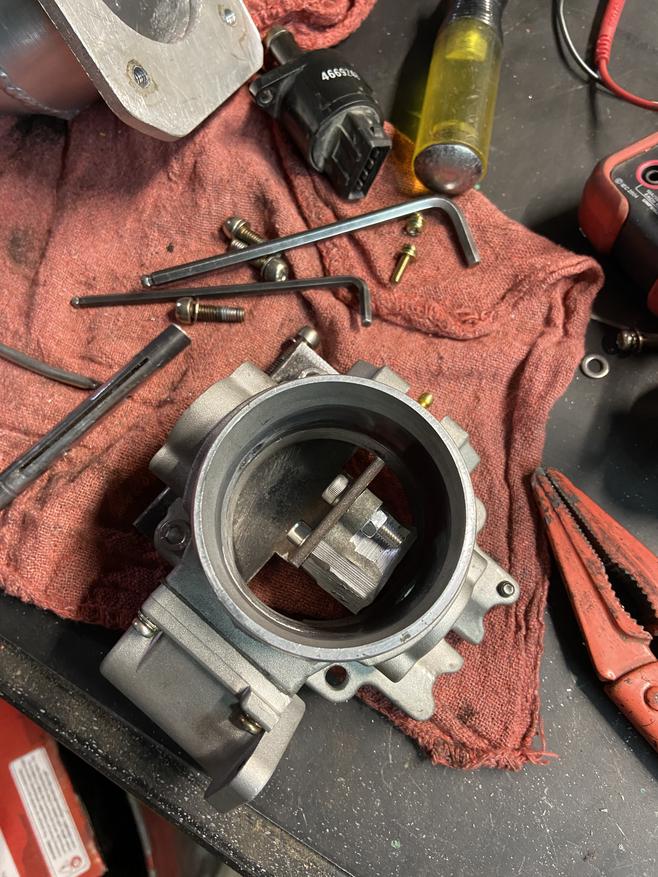
I made a quickie jig to build my cutter. 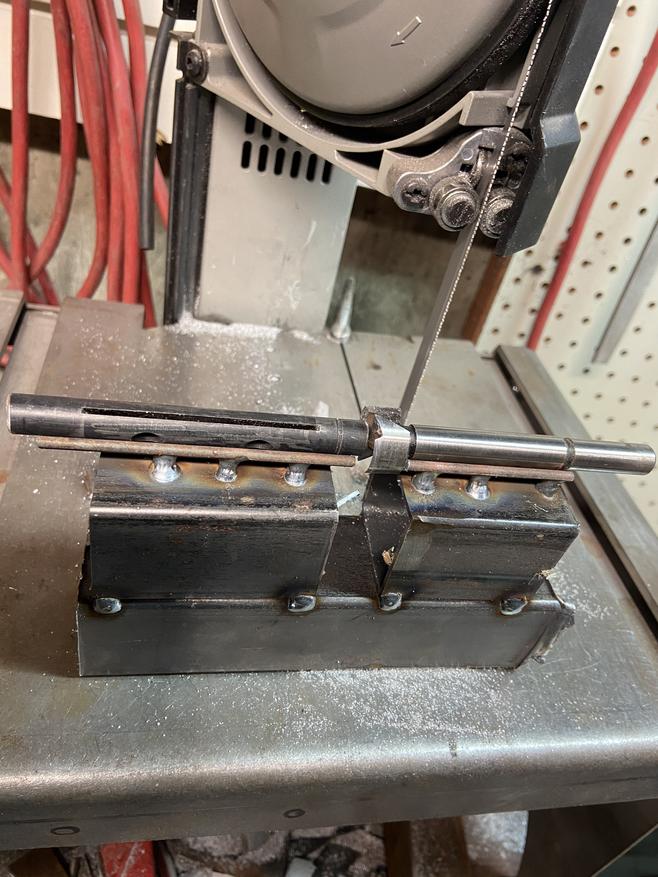
The Forstner bit is for wood and I be that I have previously used on aluminum also. It is 3/4" and I wanted to start with that and then slightly reduce it down for a press fit for the bearing. It did not work well. Lots of effort for barely any results. I chopped the shaft back off and reworked the jig to use a 3/4" spade bit. This was a way better tool. Much easier to reduce diameter and resharpen etc. 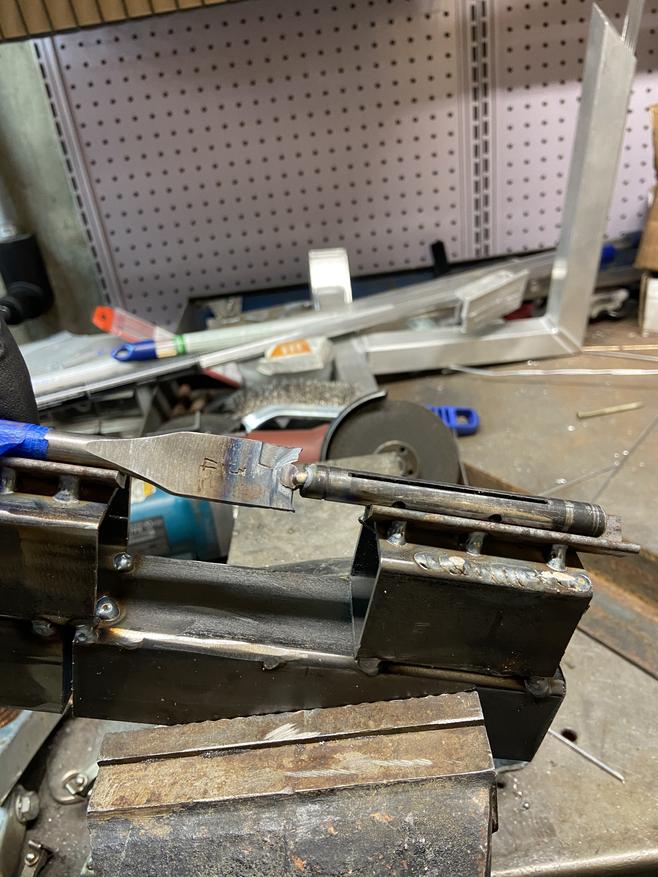
The spade bit got it done. I did a little section at the full size and then ground it down undersized for the rest of the bore. 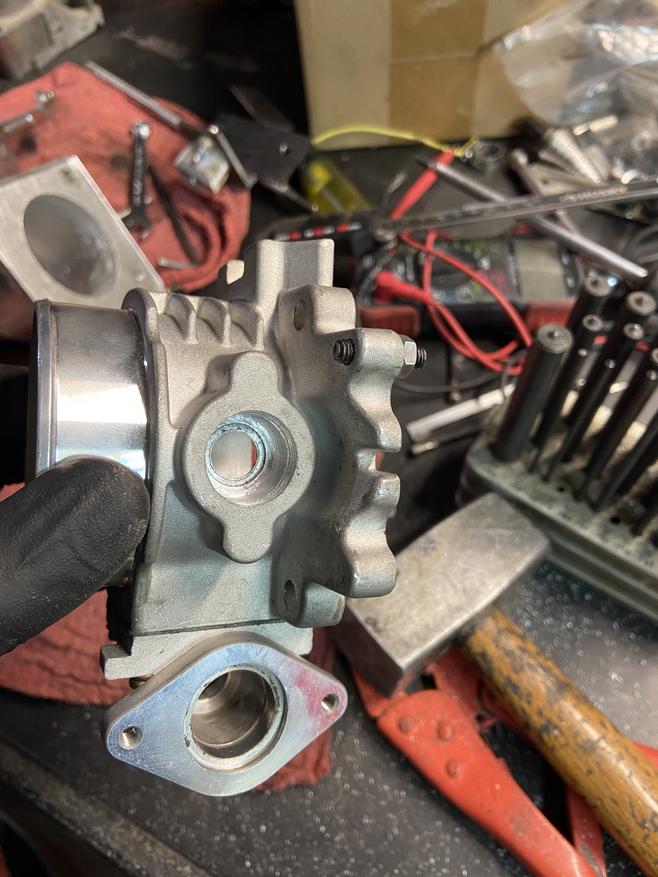
To get to final diameter I ran small beads of TIG on the cutting surfaces and filed them sharp to enlarge the bore. It ended up with a nice press fit. 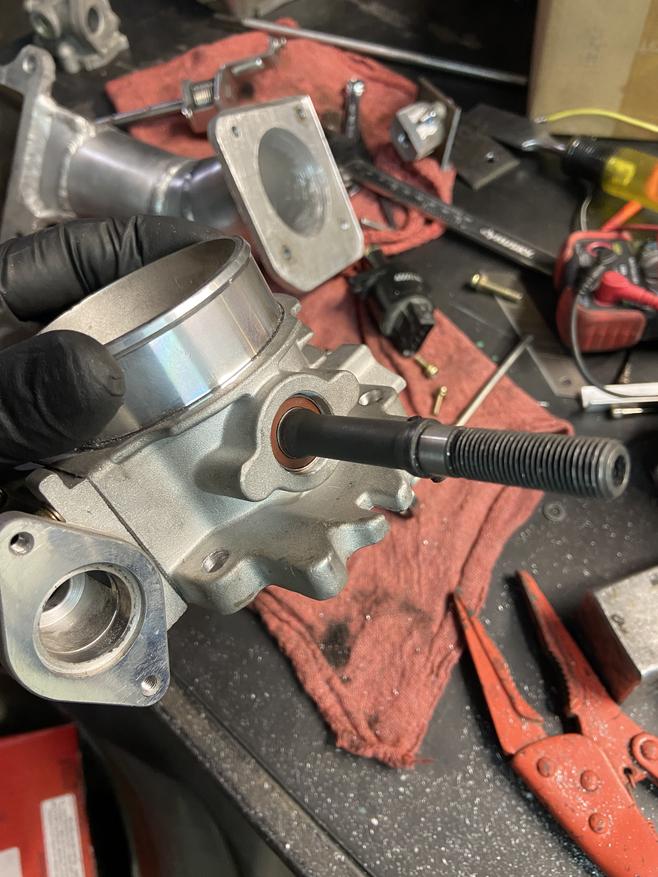
Here is a picture of the jig and cutter outside the TB.
Bearings installed, shaft and butterfly in. I measured for a new spacer and cut it down form the PT donor. 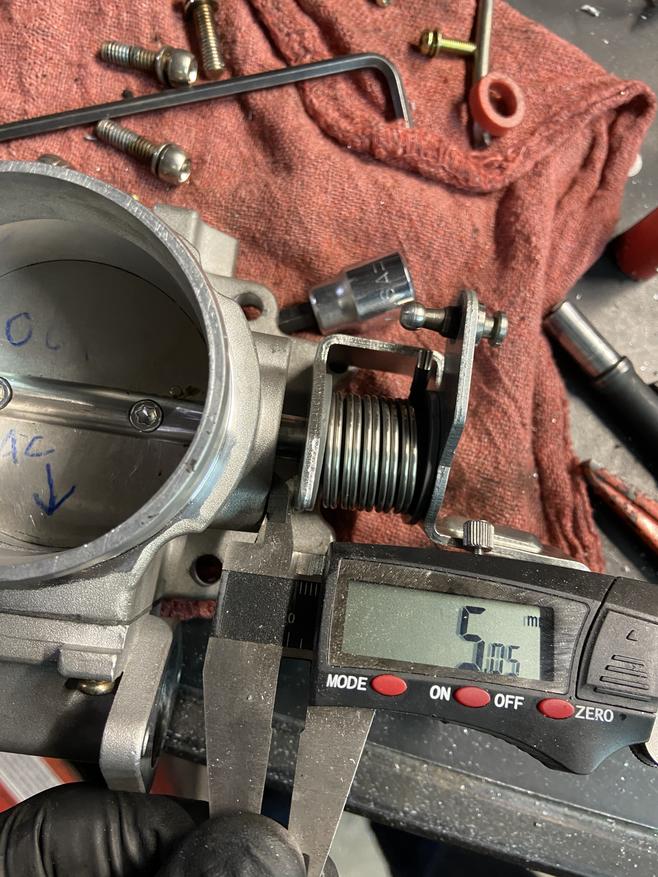
Stopped here and need to clean up; next will be making the TB open an close with the pedal in the car. 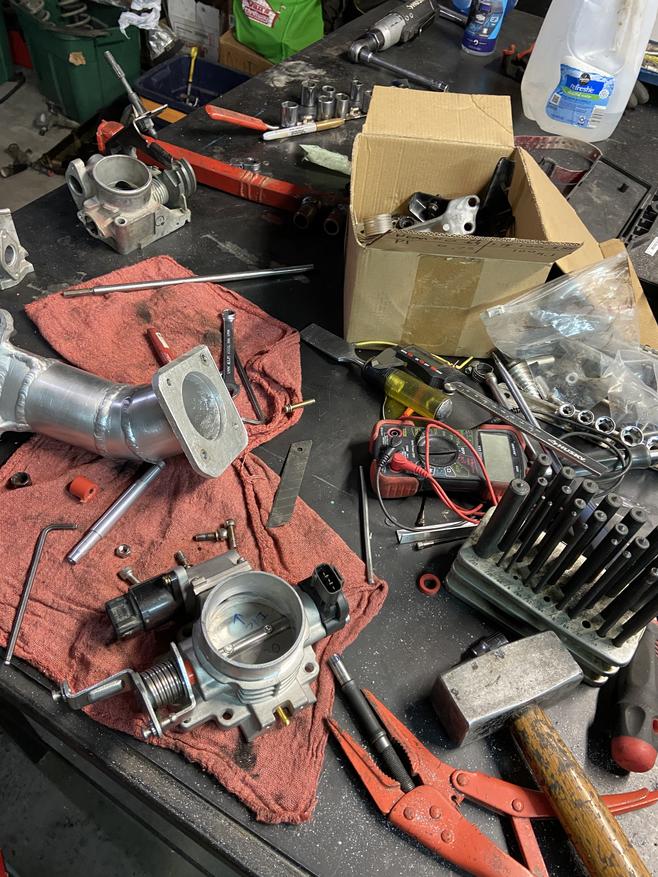
I am not sure how interesting my TB experience is but I am having a good time putting way to much time and effort into it.