It was time to start machining, so I put a 4mm end mill in the machine and secured the stock to the spoil board. How'd I secure it? I don't have a low-profile vise and I wanted to make the entire fixture with one machining step, so I used what the internet claimed was magic double-sided tape that would hold anything down.
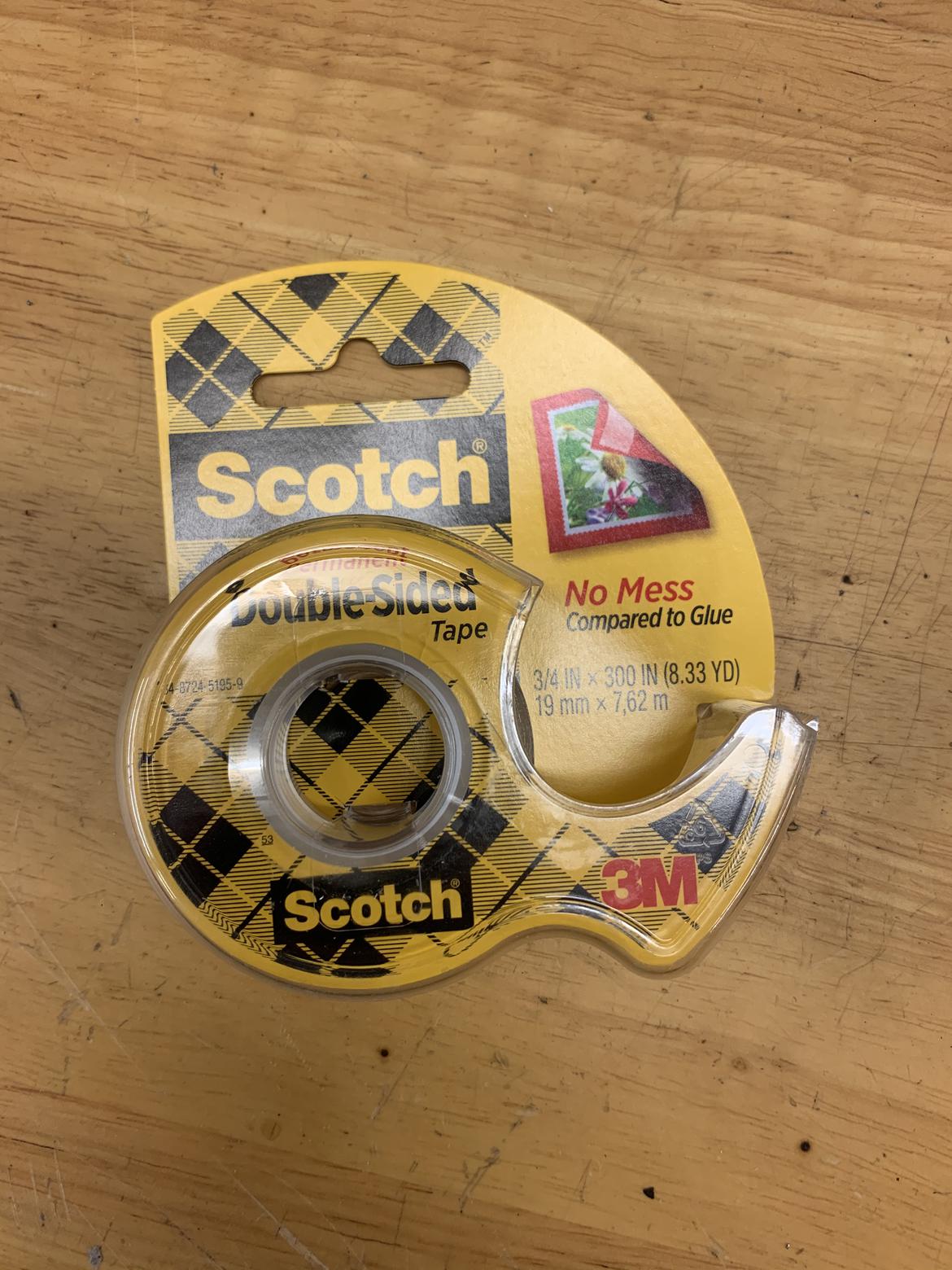
Bit installed, tape taped, file loaded... it was time to machine! I clicked send on the laptop, aiming to take a .5mm deep, 1mm wide cut at 100mm/min. BZZZZZZZ BANG!
At this point I figured my tape was the problem, not the machine, so I drilled a giant hole straight through the middle of the aluminum and bolted it down. Elegant? No. But still cleaner than some of the shortcuts Tesla has taken over the years. I'm basically Elon Musk!
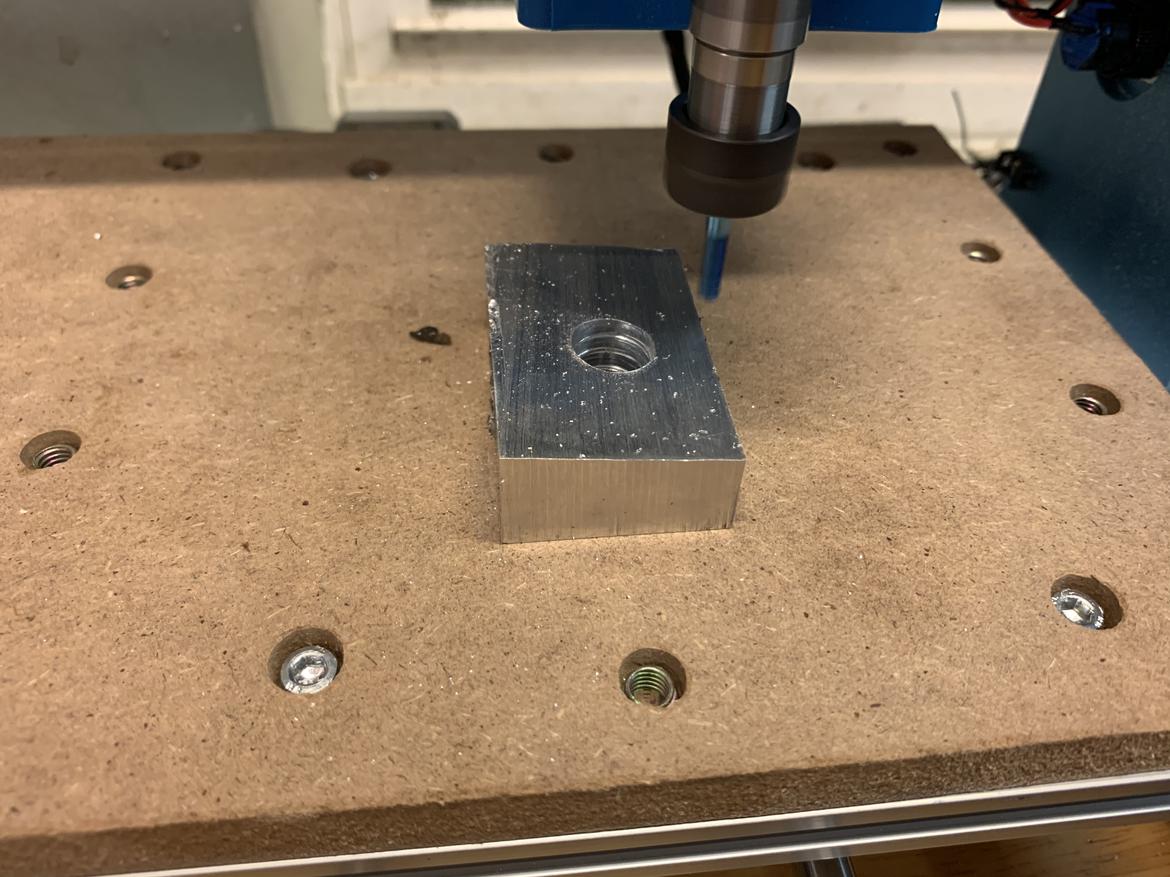
I reset everything and made a new file with the feed speed cut in half.
BZZZZZZZZZ ZZZZ ZZZZ ZZZZ
Oh my gosh, this might actually be working!!
BANG!
Whelp... This time the machine made it a few cm or so into the project before catching the stock weirdly and jumping around. Oops.
Hey, that's why I bought cheap end mills though! Trial and error is the best teacher as long as you don't die, so I kept at it. I lowered the feed speed again, this time to 20mm/minute, and reset for a third attempt.
BANG
Did you know it's possible to bend the spindle shaft on your 3018 in just three easy steps? Neither did I, but I was suddenly looking at a pretzel spindle after the bit chattered, then caught the stock wrong and took itself for a walk around the workpiece. Oops.
At that point I called it a night. Maybe aluminum just wasn't in the cards. Or maybe 6061 isn't the most machinable type. Either way it was time for a break. I ordered a new spindle and went to bed.