Ground out the inside of the lower intake manifold. Light port only, smoothed out the parting marks from casting and sharp machined edges just downstream from the injectors.
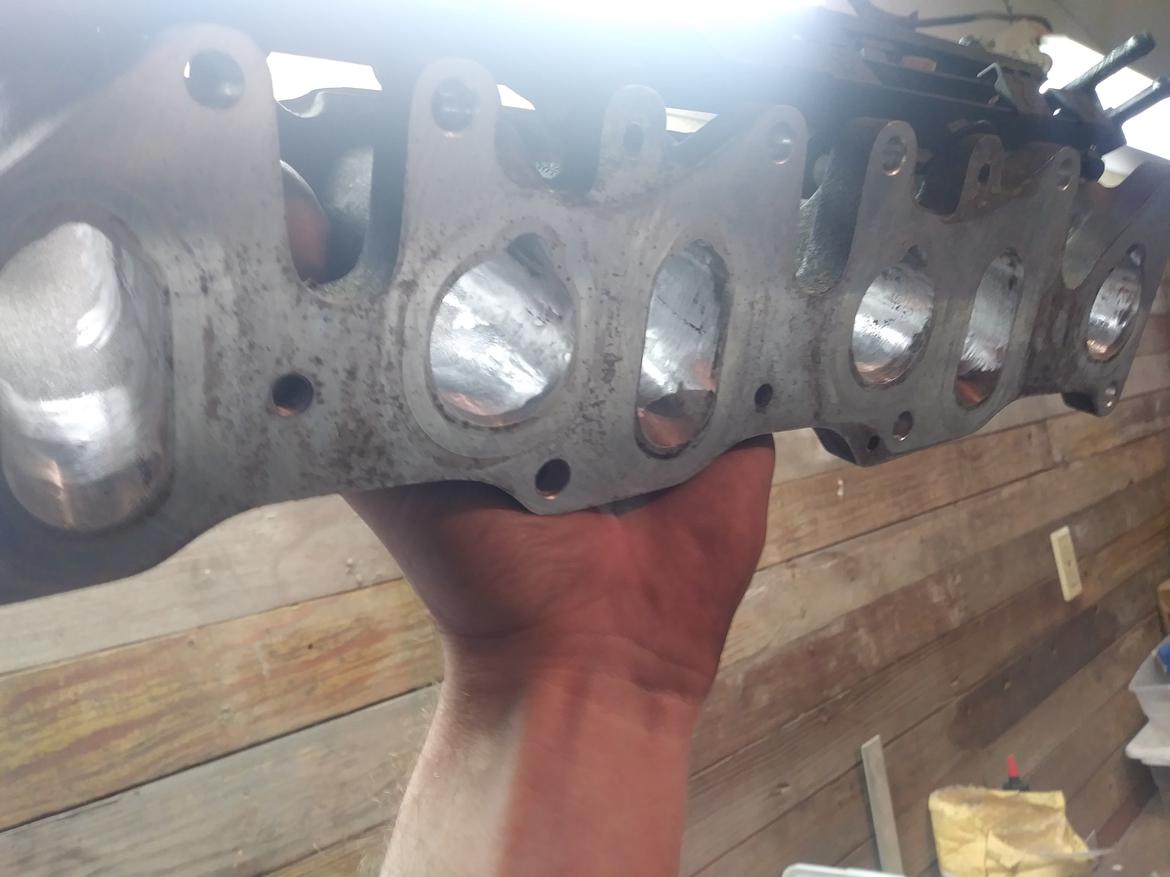
And the same for the exhaust. VR6 has a pair of short cast iron manifolds that empty into a welded steel two-into-one downpipe. The downstream end of the manifolds and upstream end of the downpipe got gasket matched, which wound up being an increase of about 1/4" diameter. The flanges on the upstream end of the downpipe are welded on the inside from the factory, and the boogery welds really disrupt flow, so I welded the flanges on the outside so I could remove most or all of the inside welds.

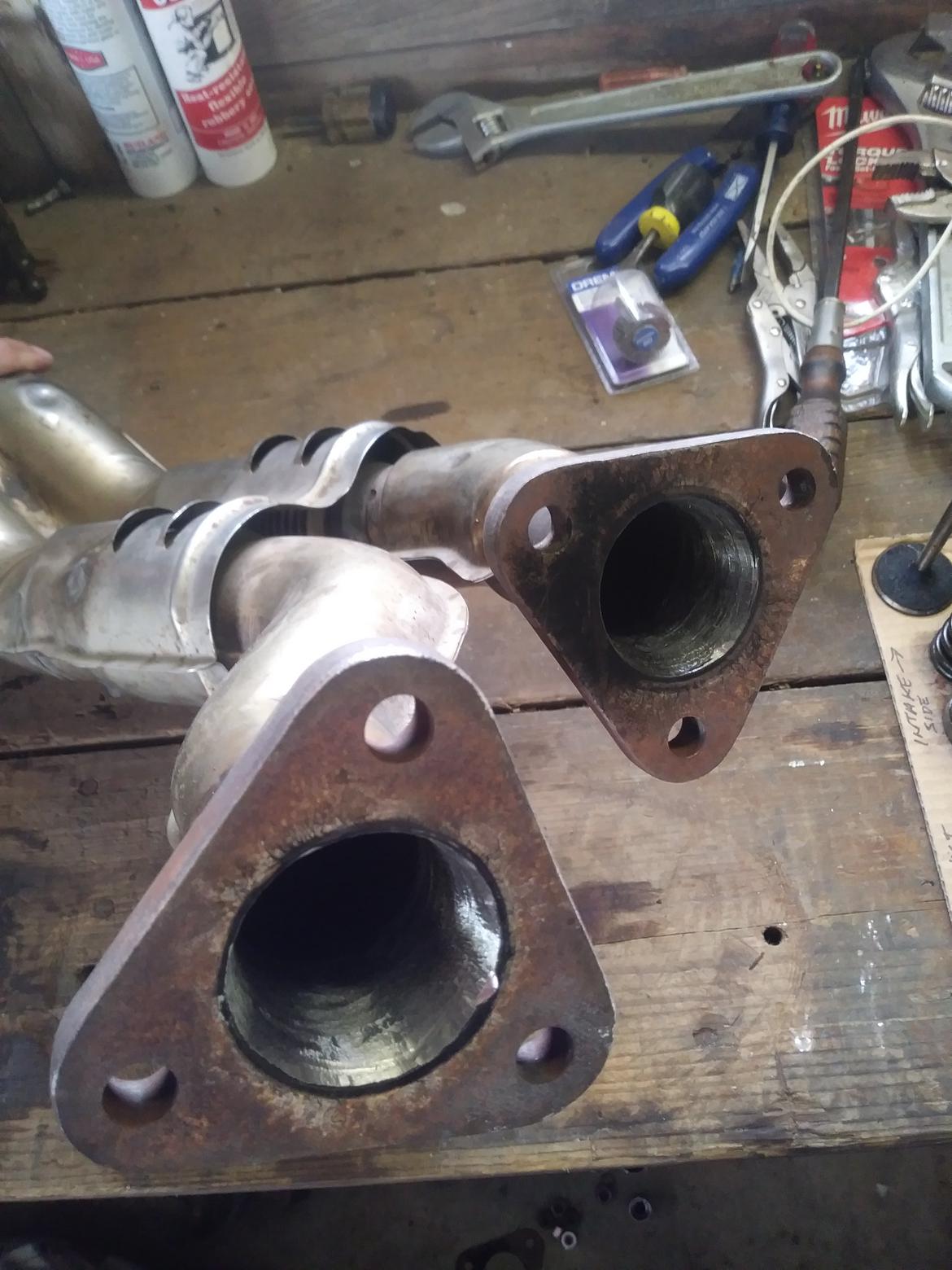
Note: the lug bolt in the driver's side manifold is evidently the preferred method for blocking off your unused EGR port. I'd like to come up with a more elegant solution than that, eventually.
One of the manifolds was missing one stud and had a bolt in place of another (and upon reinstall, we broke another one off entirely), so we have a set on order.
Practiced my lap dancing.
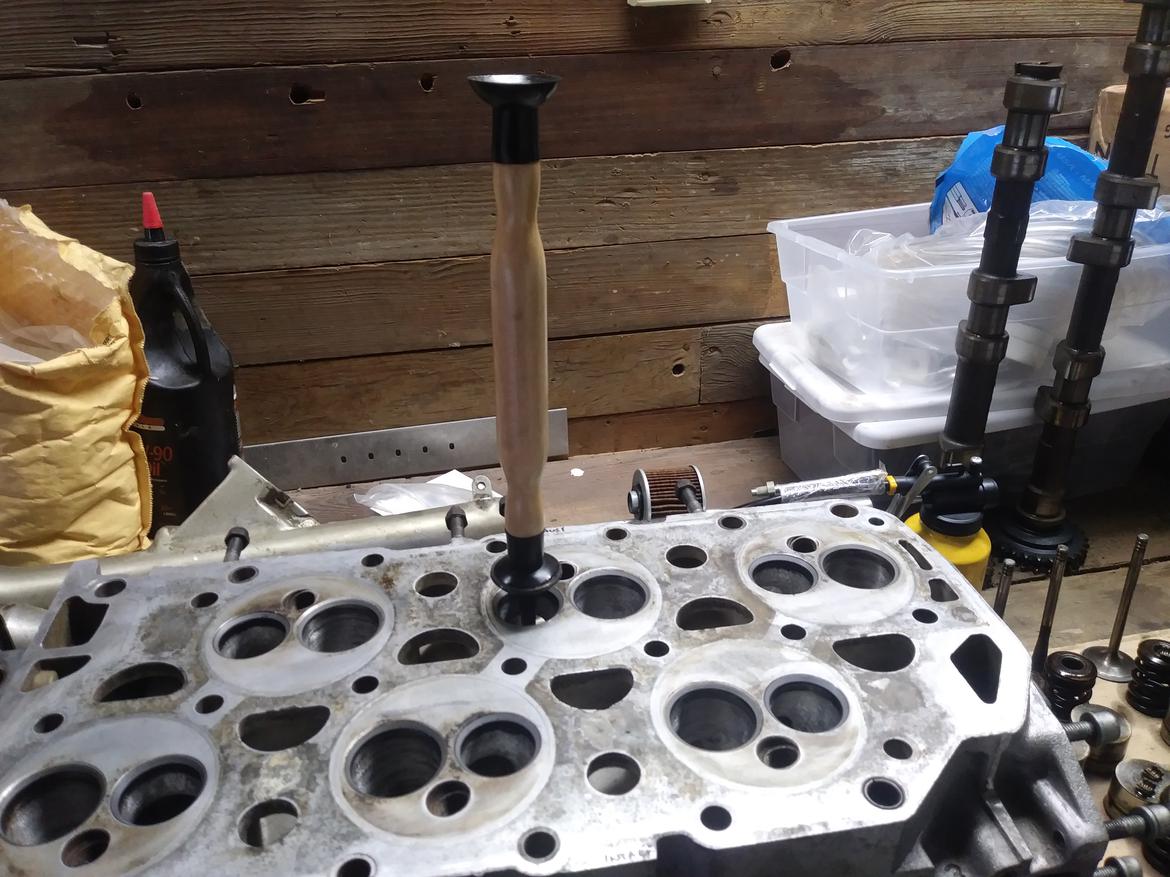
Verified for peace of mind that the head is, indeed, pretty damn near flat and true. Enough.
Finally got some mail.
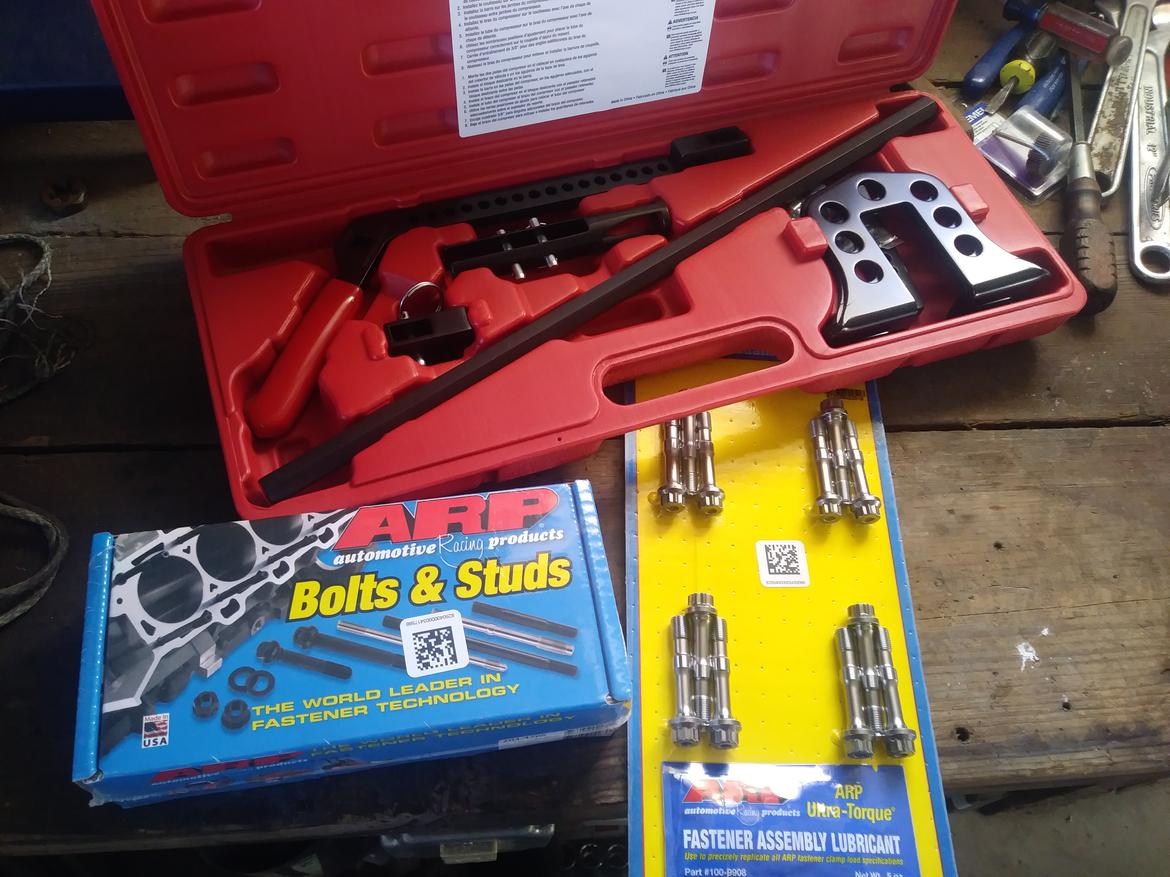
ARP head studs and rod bolts and the spring compressor recommended for VR6 heads. The ARP stuff isn't the cheap answer, but since we don't know how many more times we're gonna need to take the head off (or if/when we'll apply boost), made sense to get hardware that wasn't single use.
Head studs installed. Head gasket is a metal MK4 unit that came as part of a top-end rebuild gasket set; we only used the head gasket, so it will go on the budget at partial price. The MK4 gasket is slightly thinner than the MK3 gasket, supposedly raises compression by .5-1; would love to try it on the butt dyno, but we have no baseline, so we'll never know.
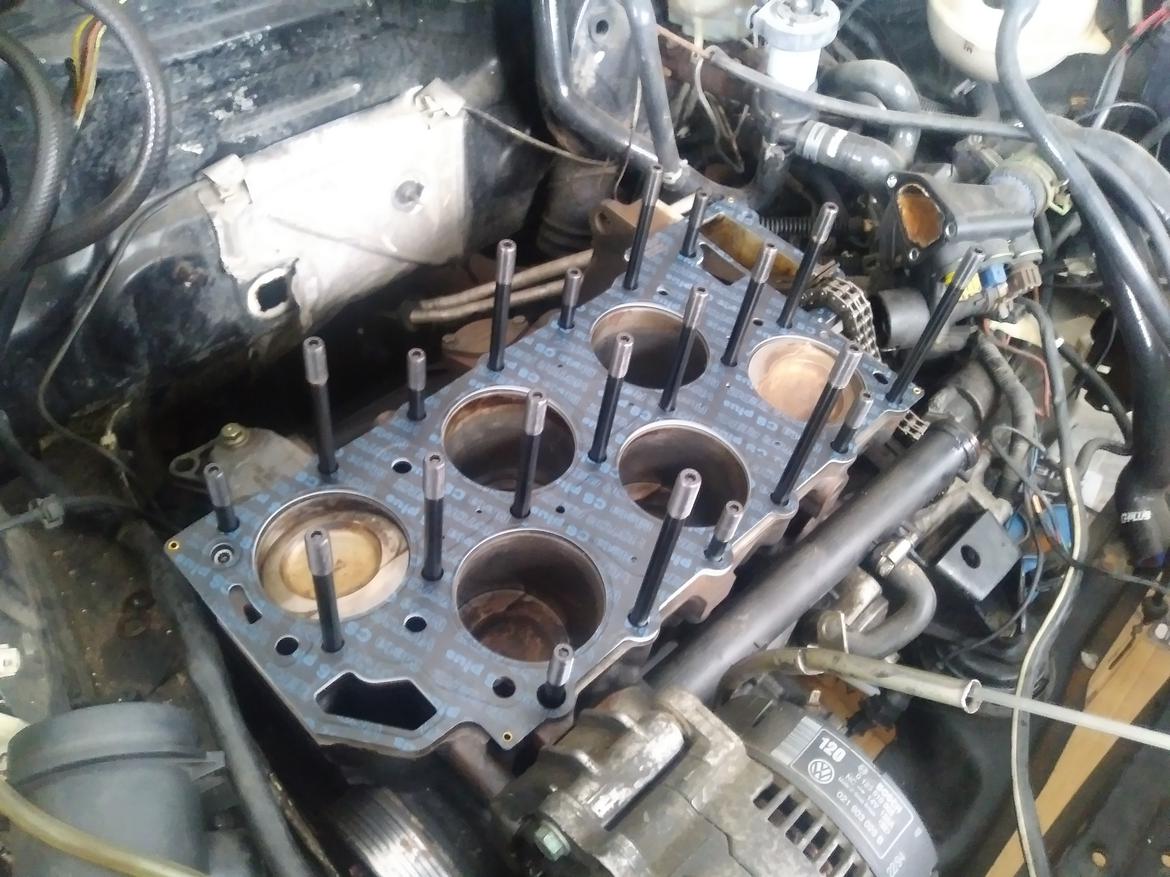
Head on and timing chain set.
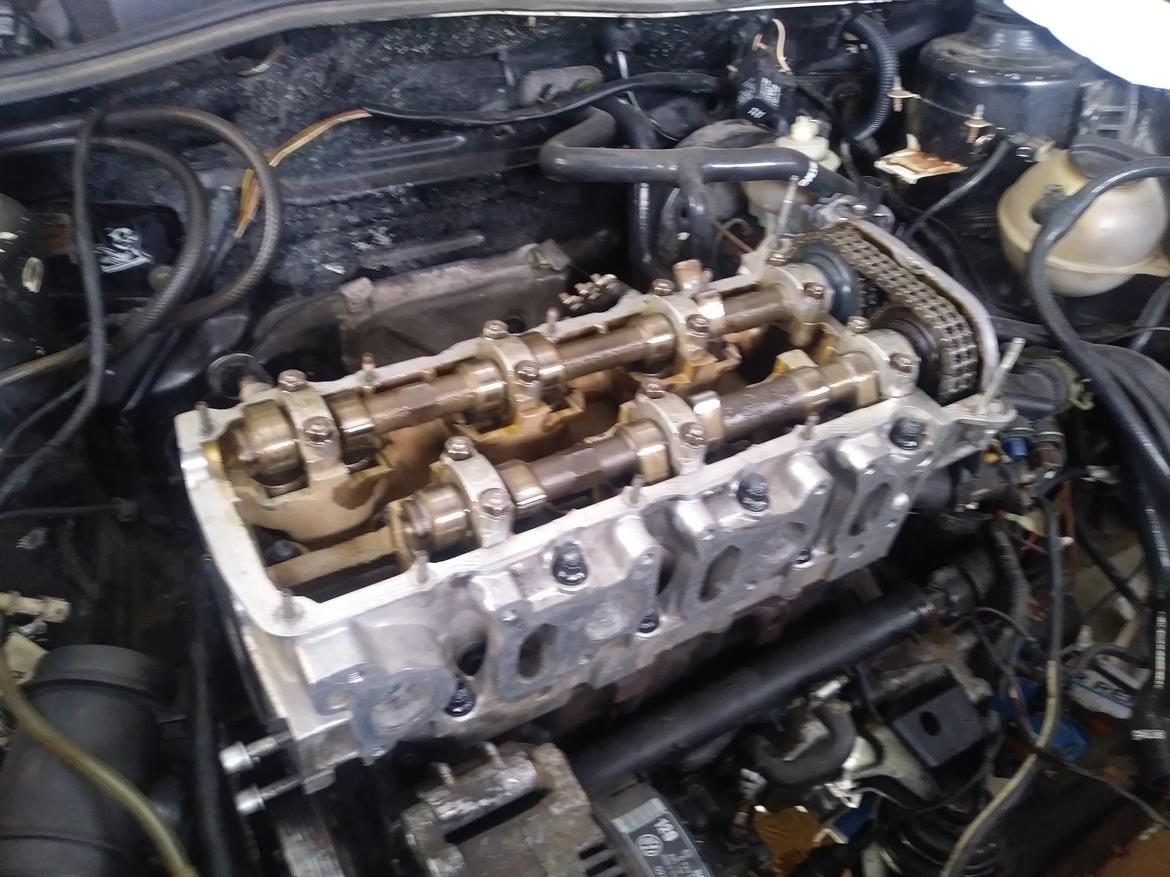
Squirted maybe half an ounce of oil over each of the cam journals and into each of the spark plug holes and turned the engine by hand for maybe 15 minutes to make sure everything was lubed and the timing wasn't horribly wrong. Or that I'd left a bolt in one of the cylinders or something, you know.
Figured this was a decent juncture to see if we had any compression. Little nerve racking to crank with power for the first time knowing the last two heads on this car got valves crashed into pistons. But nothing untoward happened, and all cylinders showed between 100 and 120 psi.
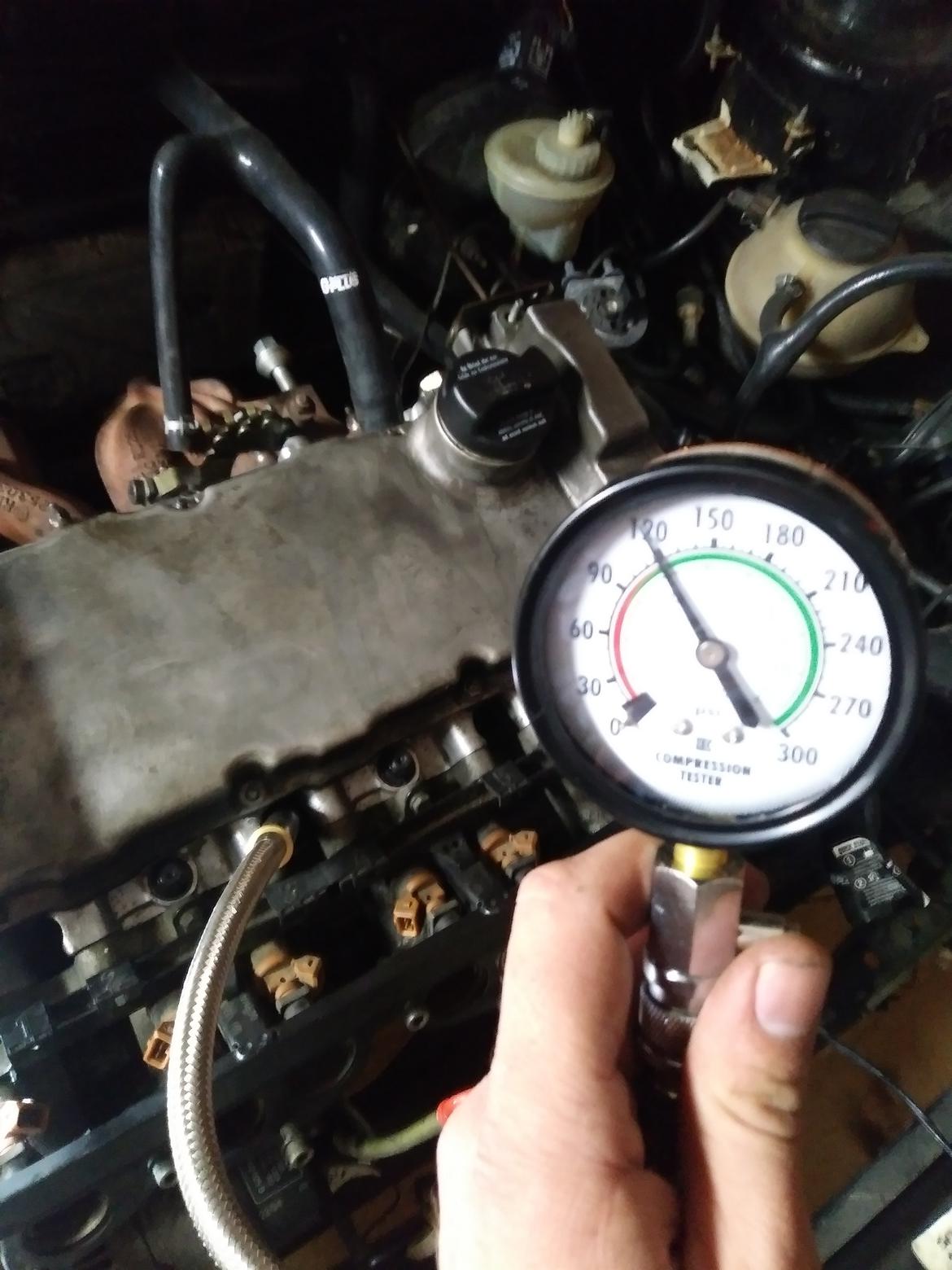
After this, everything went back together pretty fast. Valve cover, spark plugs, intake, exhaust, wiring, fuel lines, refill with oil.
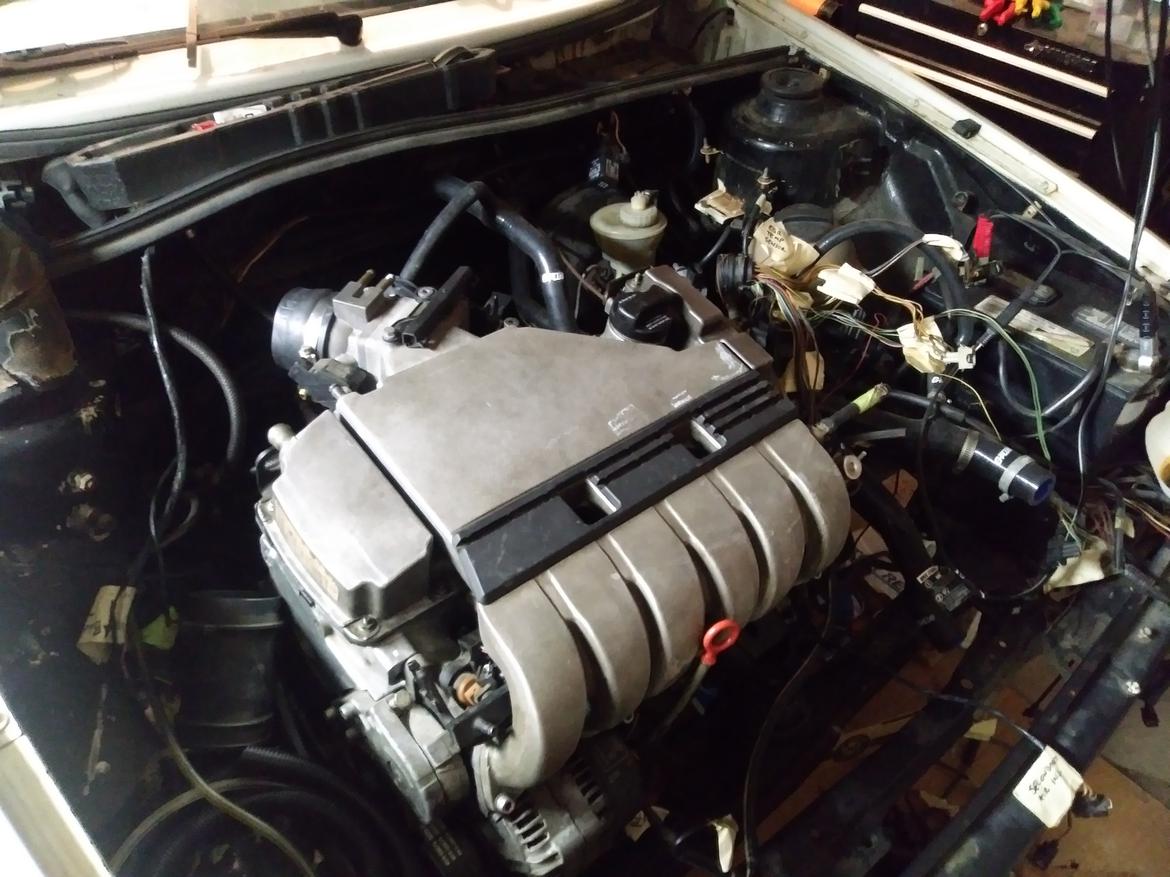
Had to relearn the fuel pump relay (for my own future reference, the reason the pump won't run is there's no power from the ignition switch making it to the relay to activate it during "start" and "on"; hotwire from the black and yellow wire on the ignition switch to the small pin on the relay).
And it ran. And the brothers saw that it was good. So they rested.
I'm back to school in Alabama, brother is back to full-speed-ahead on his MK4 R32 build, so we'll revisit this again this summer with the goal being to drive it 2400 miles roundtrip to the 2021 Challenge.