Hey All;
First Post!
It was suggested by someone on another forum that I come over here and ask for opinions, because a lot of you guys have been here before, trying crazy hybrid stuff, and have the broken pile of parts and subsequent successes to prove your theories. I need to join two shafts together to create an intermediate shaft for a solid transaxle driveline for my 944 engine swap project. Anyone familiar with the driveline layout of the Porsche 968 will know what I am doing.
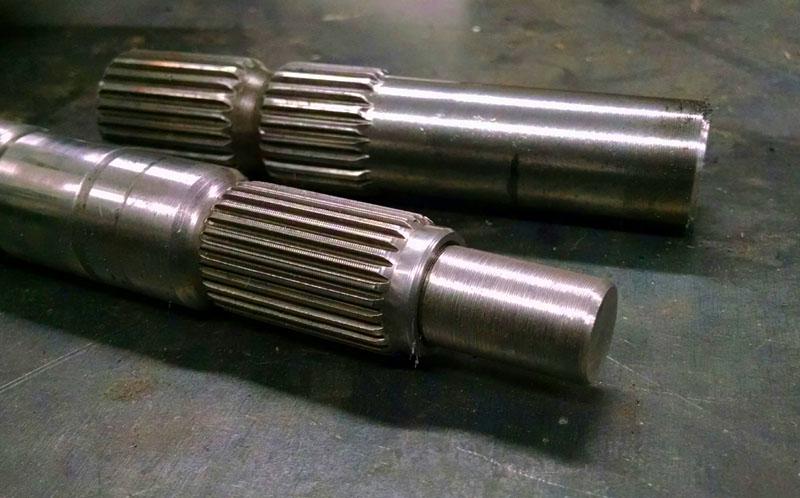
The shaft in the background is the Porsche end, and in front is the clutch side. I had already settled on the notion of turning a sleeve from 4130 to insert the two shafts into, but was quite uncertain as to the method of joining them all. My first thought was to create another snug press fit like the pilot pin you see added to the front shaft (the original application did not use a pilot bearing at all). This would offer me the advantage of a good true linear registration of the two shafts. However, my guts tells me that simply welding the ends of the sleeve to the shafts would be a quick fail. Much too localized stress on far too small a portion of material, HAZ issues with unknown alloys, etc. The only way I could see this possibly working was to only partially spot weld the ends of the sleeve, and then include a number of plug welded holes along the sides of the sleeve to spread the load more evenly throughout the included area. Still, the idea sort of left me uneasy.
One consensus of opinion on the other forum was that a silver soldered joint might be the way to go. About a half-to-a-thou tolerance for the silver to flow would give a very nice and continuous joining of the entire length of material, and also be far less likely to cause any HAZ embrittlement issues. I must admit that this idea appeals to me, but I am still unsure.
So, I leave it to the geniuses, crazies, and whomever else on this forum who have such experience to guide me into the correct one-and-done method of accomplishing this. It's either that, or find me someone that can make such a shaft, and you can only imagine how expensive THAT would be! If your Frankenracer is running such kit, I really want to hear from you!!!
In reply to Redlineman :
Welcome! You're gonna fit in just fine here. 
I was going to say plug welded holes or a V cutout on both ends of the sleeve so you'd have a longer total weld being loaded in shear as the shaft is loaded in torsion.
i hope wheels777 chimes in.
Slash cut sleeve ends /------/ and plug welds
Another vote for the v-shaped cutouts on the ends of your sleeve. You could still get a short length with a press fit for better alignment. Read up on home heat treatment to makes sure you know where you are with regard to the temper of the final part and keep in mind those splines nearby probably dont want to be dead soft.
use a Mid shaft bearing to hold the sleeve, if both ends are Stationary the connecting shaft could float and no weld is needed.
V8 Archie has a deal so both axles are the same length. common bearing support bolted to the block.
hope this is the idea you have I try to over simplify sometimes
zordak
Reader
6/29/18 9:15 a.m.
If this has to transmit power through it I would use a key. Basically have a keyway cut in both shafts and one broached in the sleeve. the sleeve needs to be sized as large a diameter as possible and as long as possible. Press the whole thing together and a couple of small tack welds to keep everything in place.
Driveshafts are just some thinwall tube welded to ends.
You'd probably be just fine with plug welding a sleeve. The tricky part will be ensuring that it is straight and concentric. It isn't transmitting very much torque but it will be spinning rather fast.
I would NOT use 4130, though. That's an awful metal to use, it is tricky to weld and it tends to break around the same time it deforms. It's technically stronger but it doesn't fail nicely.
Oh good you did make it here! I wondered if you would. As this shaft will be spinning at engine speed you will definitely want to have it dynamically balanced at a driveshaft shop or specialty balance shop like Lindskog Balancing in Boxbough Ma. You may find that it needs to be "Whip Balanced" so the middle doesn't deflect and self destruct.
44
Hey;
First, thanks for the responses. Less than I had hoped, but something to build on, as it were. Now, how many of you have actually done this sort of thing? Who has pics of how they did it? Where's the guy running 800hp through spliced axles that knows exactly what works?
For the record, I have thought of everything mentioned so far, for the most part. I had not gone so far as to consider altering the ends of the sleeve so that end welds of whatever sort were not concentric to the shaft, but other than that these things have mostly all occurred to me. I really like the keying idea, but was not sure how to pull it off? I had assumed that if I did do a tight press fit before any sort of end/plug welding, or keying, that pressing the shafts in snugly would more or less obviate registration issues. The only problem with the silver soldering idea was that this press fit registration would necessarily have to be looser. I had thought to use W1 tool steel, but someone said 4130 would be better. Everybody has an idea. That is why I was hoping to find the wacko PREVIOUS to myself that had already done it successfully!
Thanks 44. It took some doing to get here. All these weeks to be exact! I never got an activation email, and so had to rattle some chains to get included.
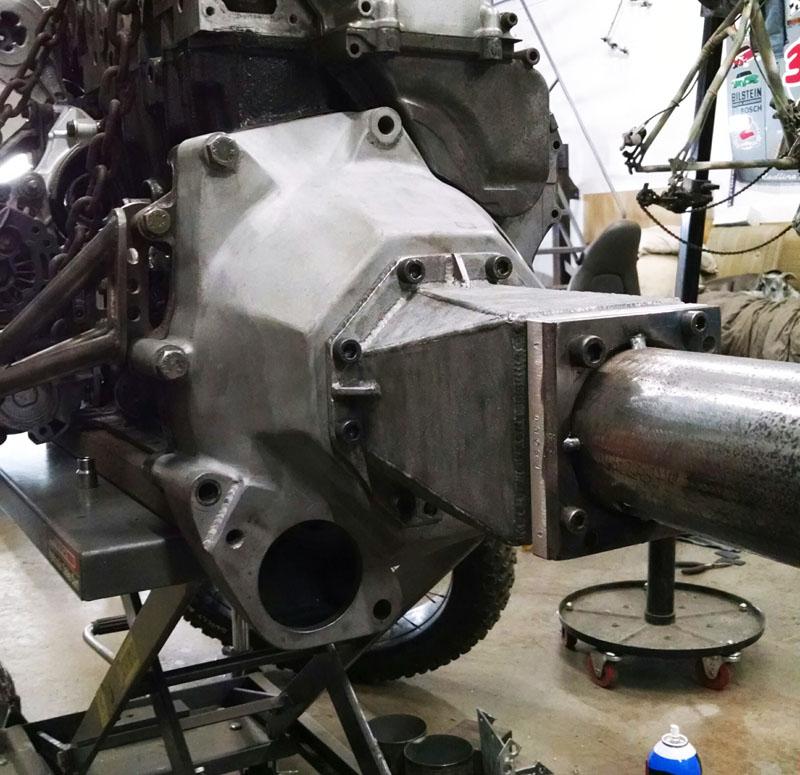
What about making a new shaft via one of the companies that make axle shafts?
If all else, or everything else, fails.....
4130 is a wonderful alloy if both pieces you are welding are 4130, you use the correct filler and have it normalized after welding to homogenize the grain structure. However, if you aren't that surgical it is a royal pain in the ass due to the relatively high carbon content for a "low alloy" steel. 4100 series steels or Chrome-Moly steels are not very forgiving. Knurled is correct in pointing out that the yield strength of these alloys is often very close to their ultimate strength, especially when welded.
As for joining the two shafts sleeving one into the other with a nicely beveled butt weld and a couple plug welds should hold. Check this out for a general idea of joining two shafts in that manner. Spacing out the welds in relation to both time and polar orientation on the shaft will help a lot with thermal warpage. Preheating and post heating can help a lot with warpage, penetration and embrittlement as well and is strongly encouraged whenever you are welding thick cross sections of metal. Rule of thumb for TIG welding steel is 1 ampere per 1 thousandth of wall thickness. I typically preheat if I am welding more than with more than 160 amps.
X2 on making a new shaft....THEN having it heat treated, 1150 PH etc....
Moser can probably make that new
fasted58 said:
Moser can probably make that new
Well, that I might be interested in if it wasn't $10x.
Nice link, Ram50Ron. Kind of funny that those axles depicted there look EXACTLY the same as standard 944 axles.
So... I guess I just have to decide. I'm not the kind that wants to wing it and court a failure. I want one-and-done. Perhaps too much to ask given what I am trying to do. I'd like to hear from Moser, and Wheels777.
fasted58 said:
Moser can probably make that new
After seeing some of the things Moser makes, I wouldn't trust them to make an oil pump drive shaft.
Just random thought, but what about tapping and threading the two male and female shafts together?
May need to be left hand thread depending on rotation?
How long is that shaft going to be?
In reply to Redlineman :
Don’t. Chances of failure are too high and when it goes what else will go with it?
Bring both pieces into a good machine shop and have them make you a new one. Find a shop that normally does transmission parts and they can do it straight off without special ordering tooling or material.
If the quote is a couple of hundred it sounds like you could be in the right place if the quote is $1000 or more and a month you are buying tooling and in the wrong place
In reply to JGRAHAM :
Interesting. Impractical, but interesting.
In reply to APEowner:
Off the top of my head, about 12".
In reply to frenchyd:
My sense is that since it has little mass and therefore inertia of its own, it would simply snap, sit in place, and the car would cease to move. Your thinking is nonetheless very sound and logical, and falls in line with my own inclination. If I could find such a shop, and get the part for under $500 (preferably less), I would very strongly lean that way. Notwithstanding the fact that it would be an interesting exercise to see if a splice would work.
12 inches... Some how i was thinking we were dealing with 3 to 4 feet or more. That certainly does change things. I know from experience with welded axles in Dwarf Cars that they generally will fail when under 10 inches no matter how they are done there's just not enough flex in them for shaft loads. After tumbling end over end 3 times then barrel rolling 4 more times, ending up on my roof looking at a 15 car field coming right at me when a long side axle snapped on a restart i stopped using welded axles (as a note it didn't break at the weld). They were pressed fit with 4 plug welds per side ~ 1 dia shaft with sleave being 1.75 and around 4in long.
The same guy that would do this ended up making stub ends so it no longer took two factory axles to make the long side axle. he would grind splines. He's no longer in that type of work or i'd send you his info but you should be able to find a shop that can grind a spline for you.
How much torque does that engine put out?
What is the nominal diameter of the shafts that you're joining?
Not related to the shaft question directly but because I'm curious about the setup; what supports the throw out bearing?
APEowner said:
How much torque does that engine put out?
What is the nominal diameter of the shafts that you're joining?
Not related to the shaft question directly but because I'm curious about the setup; what supports the throw out bearing?
Torque from this engine will be < 200ft/lbs.
Shaft diameter is 25mm (0.982").
The clutch release bearing will be hydraulic.
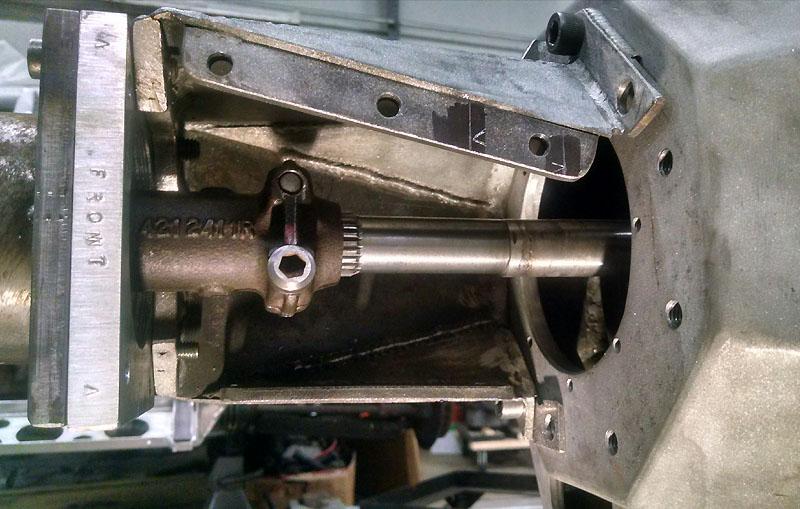
Redlineman said:
In reply to JGRAHAM :
Interesting. Impractical, but interesting.
In reply to APEowner:
Off the top of my head, about 12".
In reply to frenchyd:
My sense is that since it has little mass and therefore inertia of its own, it would simply snap, sit in place, and the car would cease to move. Your thinking is nonetheless very sound and logical, and falls in line with my own inclination. If I could find such a shop, and get the part for under $500 (preferably less), I would very strongly lean that way. Notwithstanding the fact that it would be an interesting exercise to see if a splice would work.
Find an axle with those splines on one end and send it to someone like Moser to do the rest of the required machining