frenchyd said:
Find an axle with those splines on one end and send it to someone like Moser to do the rest of the required machining
That's an interesting idea, except I have never seen an axle where the spline OD was equal to the shaft OD. The spline is always larger, and the shaft portion smaller. However, if the clutch end were small enough, relative to the Porsche shaft OD, your idea might be feasible. In fact, the clutch spline here is .847"OD, so it may be feasible to create a pilot pin and clutch spline from a .982" OD Porsche shaft. Hmmmmmm.........
NOHOME
UltimaDork
7/9/18 9:50 p.m.
Here is an option that I had never heard of for this applicatoin. Link to video of an axle being friction welded.
http://www.cpsdrivelink.co.uk/friction-welding/
Pete
NOHOME said:
Here is an option that I had never heard of for this applicatoin. Link to video of an axle being friction welded.
That's very interesting, and they have a motorsports division. Perhaps I will see if they will offer me any information. Thanks!
In reply to NOHOME :
I feel really dumb for not thinking of this before. We used to do this at my last job when my oil field customers wanted us to cast custom hardware for them. It's a lot easier to cast the head of a 2" bolt and spin weld it onto 18" of stock than it is to cast a 18" long bolt.
Obviously the "right" way to do this is to have a shaft machined from scratch but that's likely to be pricey. Not only do splines require slightly specialized tooling but the clutch end at least will need to be hardened after machining.
I like the idea of just machining the clutch end of the input shaft but not knowing the alloy may make it a challenge to heat treat after machining.
Joining the two shafts by welding is also problematic due to the unknown alloys. They're obviously steel of some sort so a MIG weld with a mild steel wire of some sort will stick them together but I don't know that I'd want to rely on just the weld. I think that bring us to a mechanical connection with possibly a weld backup.
I'd want to do some FEA or maybe just some basic math to see of this is strong enough but I'm thinking that joining the two shafts with this -> Steel Hexagon Hole Sleeve is the way to go. Machine the ends of the shafts to hexes 0.0001" or so (again, do the math) larger than the internal hex on the sleeve. Heat the sleave so it slides over the end of one shaft. Heat it again to slide the other shaft in and then weld a bead around the outside of both ends of the sleeve to lock everything together.
tuna55
MegaDork
7/10/18 10:56 a.m.
I don't have any direct experience with this in a garage, but as an engineer I think you need to drop the solder idea. That's not going to be strong enough.
I am a fan of welding, but in this instance you have a few problems. One is that you likely cannot measure penetration when you are through, and you cannot control eccentricity when you are done, and you are welding a hardened steel, which is not only more difficult but also you're losing the hardness and therefore the strength when you do it. Without the heat treatment and resulting hardness it's nearly as weak as a typical low carbon steel. I would prefer to have a spline broached onto either end, and a sleeve made to connect them, and then perhaps a spot weld or two to hold it together.
If you want to weld them, you would be best served by someone checking for straightness, balance and heat treatment.
Wait we're talking a foot or so what about a CV shaft? Any chance there's one with the same splines?
NOHOME
UltimaDork
7/10/18 10:21 p.m.
If anyone is familiar with the finer points of that friction weld Ju-Ju, I would welcome the education.
Pete
44Dwarf said:
Wait we're talking a foot or so what about a CV shaft? Any chance there's one with the same splines?
No;
NONE. They are different on either end.
UPDATE: I have been in contact with a custom machining company that says this is right in their wheelhouse. No problem creating a part like this. Approximately $400 for the part. More than I was hoping for, but less than I feared. I know that a talented home shop guy with an indexer and a good mill could do one, but I don't know any of those guys.
Redlineman said:
UPDATE: I have been in contact with a custom machining company that says this is right in their wheelhouse. No problem creating a part like this. Approximately $400 for the part. More than I was hoping for, but less than I feared. I know that a talented home shop guy with an indexer and a good mill could do one, but I don't know any of those guys.
Excellent! That's the best way to handle it. What are they proposing for material and what are they going to harden the clutch end to?
In reply to NOHOME :
Yes!! Friction welding is the very first thing that came to mind.
Success requires some process experience to get right; the initial RPM, the applied pressure, how long to apply pressure to create the melt, and subsequent heat treat (if any).
But it's been around long enough that there are design calculators available to get the process specs pretty close the first time.
rothwem
New Reader
7/13/18 10:45 a.m.
I used to work in a half-shaft plant as a metallurgist, so this is relevant to my interests.
The best option is to machine from barstock, but this is grassroots motorsports, not OEM motorsports. The friction welding is also an OEM-type solution, since the machines cost a lot and it takes a LOT of work to get them dialed in right. You also need to anneal back the weld, machine off the flash, surface harden, and then temper back. Lots of heat treatment=lots of cost. Its not such a bad thing for an industrial application that produces 1500 shafts per machine per day since its all induction heat treating. Most FWD cars with "equal length" halfshafts use a friction weld on the "long stem tulip" plunge joint, since its the best way to join a forging to a piece of barstock.
As for welding, its probably not the best choice. OEM halfshafts are usually mid-carbon steel, around a 1045. 1045 welds poorly, and gets really hard and brittle in the HAZ. The filler you would probably use would be a low-carbon filler, so your weld would be weaker than the surrounding metal, and not as hardenable. You may be able to use something like an ER80S, but I'm not sure if you would be able to match the hardness to the surrounding area. Either way, you'd probably want to use a boatload of preheat and then attempt to re-harden later.
And then it'll probably fail, and you'll get a newly machined shaft anyways, but it'll be a fun experiment! Please post results.
Yowza...
Lots of great stuff there guys. Particular thanks to rothwem for his direct and salient expertise in such shafty things. For the record, I too have always been leery of the welding venture. I've never liked it, but was in some sense forced to embrace it, failing the discovery of someone that could make me an engineered part. I don't know metals or hardness or heat treating from an engineering standpoint, but I know enough to know that welding such a thing is marginal without some pre weld tech and post weld processing. The advantage of this manufactured part, among many others, is that I will know for certain what kind of alloy I am dealing with.
Many of the details have yet to be worked out, but I will be moving forward with providing them with more design specifics. if we get to that point, they are also going to perform hardness testing on the actual parts that I have in order to inform their own choice of materials and processes. All I know right now is that the splines will be hobbed, which I figured anyway.
Updates to follow.
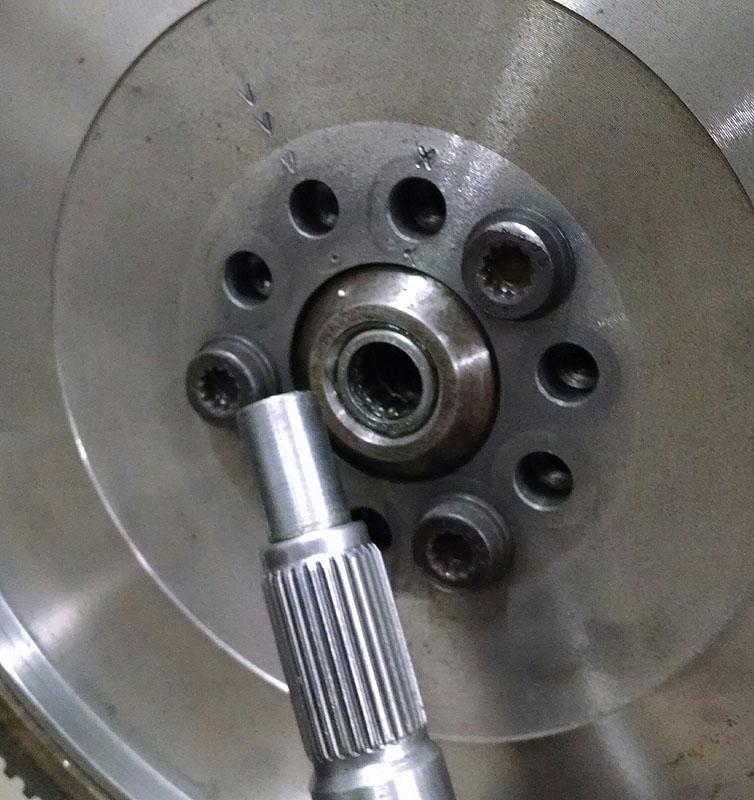
A crank that previously never had a pilot bearing, and a shaft that never had a pilot bearing pin!
Xenith
New Reader
3/14/25 8:50 a.m.
Ji I know this is an old thread but just thought I'd comment for anyone trying to do this in the future . I have come across this actual part in an OME gearbox and what they had done there was drilled and taped both ends of the shaft screwed them together with a 1" long threaded piece and also splined the outside of both shafts one having a longer spline than needed to allow a sleeve (which was Also reverse gear) to slide completely over it allowing you to screw the two shafts together (there were shims in between the shafts to get the splines to aline when tightened to a spec) and then the sleeve was slid over the joint and a snap ring stopped the sleeve from moving back off the joint .job done no welding needed one and done . this was on a porsche gearbox input shaft. This bugy had a worked 5.3 Lt V8 fitted to it