Welcome back to the Frugal Mechanic. Let’s put this car back together again.
Porsche uses a Dual Mass Flywheel in the Boxster. The internals are pretty complicated, but the most important subcomponents are springs that can weaken over time. There’s a Porsche TSB floating around providing a go-no go test for this component. Basically, you put matching marks on the outer edges of the clutch face and the toothed tone ring and then measure how much you can “twist” the flywheel.
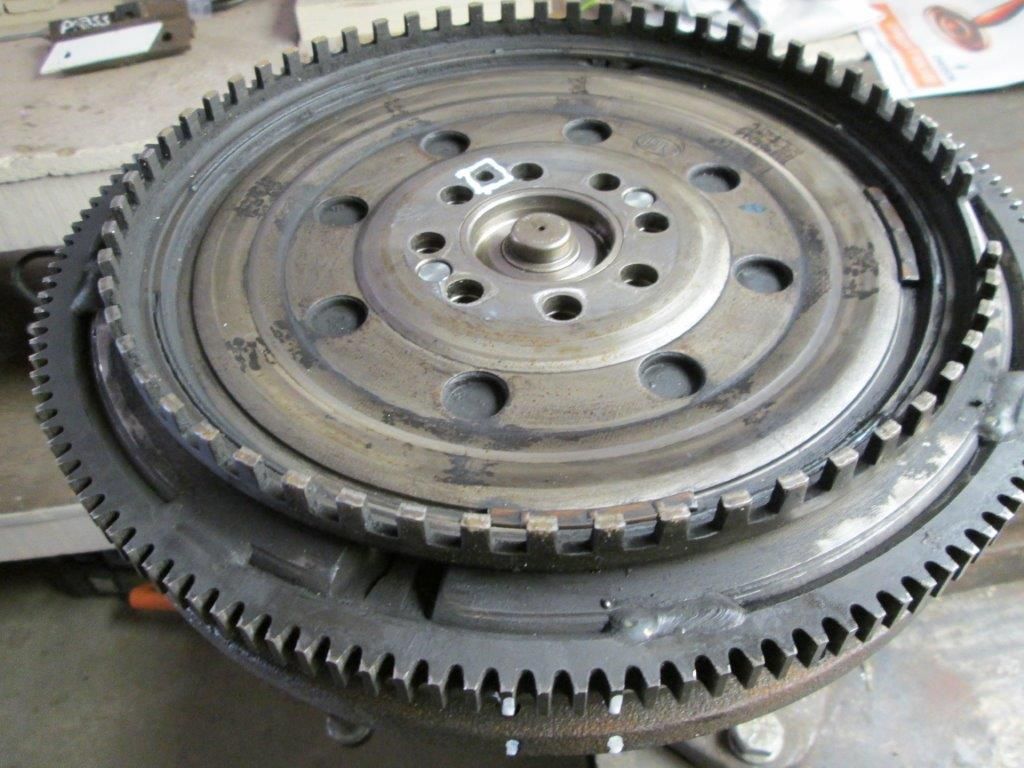
Picture isn’t mine. The process takes two hands and I’ve had mixed luck snapping my camera shutter with my tongue. I got around 5 mm of twist on my flywheel in both directions – well under the 15 mm limit in the TSB. Porsche also requires the flywheel to snap back to center after twisting, but mine didn’t do that. There are Youtube videos with the test performed on brand new flywheels, and I noted they didn’t snap back to center either. Displaying the deep respect that one must show for fine German machinery, I tipped the flywheel on its side and pounded it several times on the concrete floor. About two tablespoons of clutch dust sifted out and the internal springs started “springing” again. Called it good.
New flywheel bolts. Torque spec calls for tightening to 19 ft-lbs and then though another 120 degrees. Some folks go to the trouble of actually affixing a degree wheel to the bolts to ensure the heads are tightened the full 120 degrees. Since the cavity for the Torx drive already divides the bolt head into six equal segments, I made a mark on the bolt, counted down two segments and marked the flywheel. I threaded in a transmission bolt, a pressure plate bolt and used a heavy-duty tie wrap to restrain the pressure plate. Used my biggest breaker bar and went to town.
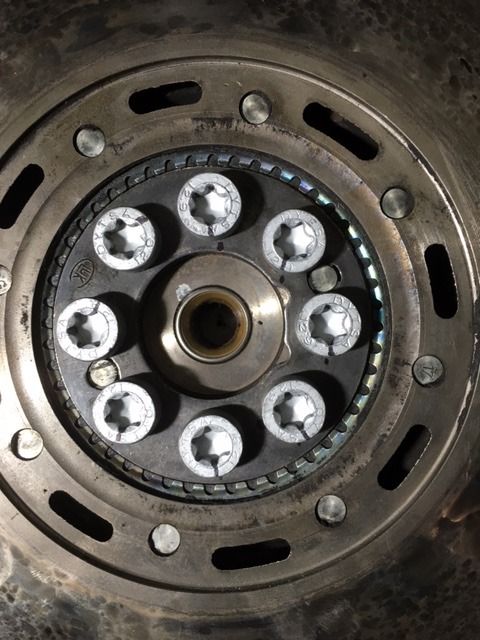
Thread in the clutch alignment tool (my clutch kit came with one) and the clutch disk, then bolt down the pressure plate. Should be good for another 30,000 to 60,000 miles.
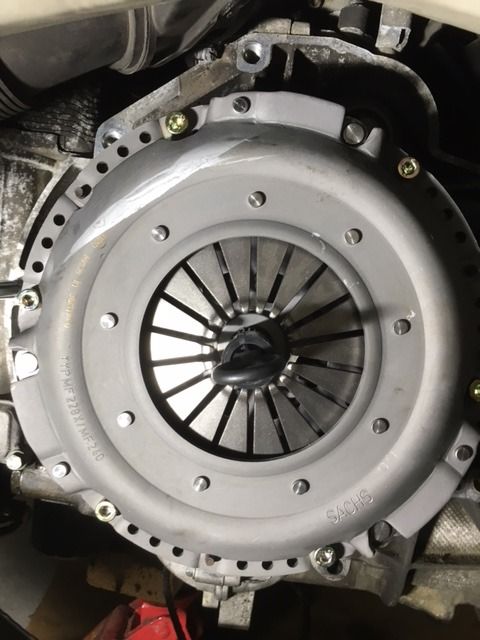
The original throw-out bearing showed great reluctance to slide along the shaft and the bearing sounded like the wheel on a matchbox car when spun. Replaced, with a few dabs of Lucas pressure grease in the right places, and it’s time to move on to reinstalling the transmission.
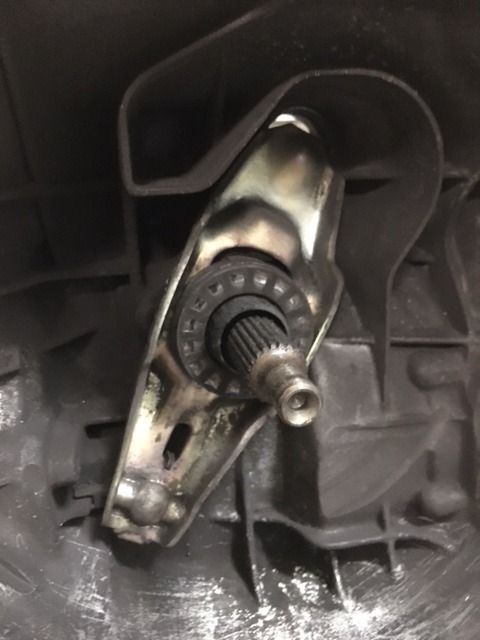
And here’s where I hit a wall. Up until now, I’d moved pretty quickly through this job. But stabbing that transmission shaft? Oof. I spent about four hours trying to get the pilot shaft to mesh with the splines on the clutch plate. Just….wouldn’t…go. I’d work for a half hour, fire up the computer and consult Youtube videos, and then try some more. Finally, I rolled the transmission back and disassembled down to the clutch plate to see what was hanging up. Turns out my ham-fisted attempts had buggered up the spines on the clutch plate. Pondering the situation, I realized the car wasn’t level – my jack stands at the front of the car were a few inches lower than the rears. As a result, the engine and transmission weren’t on the same plane and would be nearly impossible to mate.
I was able to salvage the damaged clutch plate by chucking a grind stone in my Dremel and lightly dressing the damaged splines. Then I flipped the clutch plate over, and using the transmission shaft as a makeshift die, worked the plate over the shaft from the undamaged side. I’m ashamed to admit that a hammer was involved, but in the end, the splines were restored to a relatively undamaged state.
With the car and engine perfectly leveled, I also shimmed the transmission into alignment. That’s my biggest issue with the Harbor Freight Transmission jack, which is only adjustable for fore and aft alignment. However, similar to my experience with finding a spouse and rearing children, dumb luck trumped my meager skill set, and things went back together. My experience was similar to others on the interwebs – the Boxster transmission and engine casing don’t go back together with a satisfying “clunk”. Rather, with an inch of separation, they have to be “drawn” together by installing a bolt on either side and alternating one turn at a time. As I said during disassembly, I really appreciate the access to the transmission bolts on this car. The bolts are an assortment of M10 and M12 fasteners, readily available at the local home improvement store. Next time I’m in here, I’ll pick up a few in longer sizes, chop the heads off and screw them in as alignment pins to skip all this hassle.
The new bolts on the CV joints installed without incident. The boots and the grease all looked good, and I was happy I didn’t have to replace them. Re-installing the clutch slave cylinder was a struggle. The clutch arm was now in a new position and I couldn’t get the mounting bolt in without opening the bleed valve to retract the pin. That requires the clutch hydraulics to be re-bled. Oh, bother. The Boxster clutch and brakes share the same fluid reservoir, and at least it uses standard European threading on the cap. I hooked up the Volvo adapter on my Motiv pressure bleeder and burped out a few bubbles.
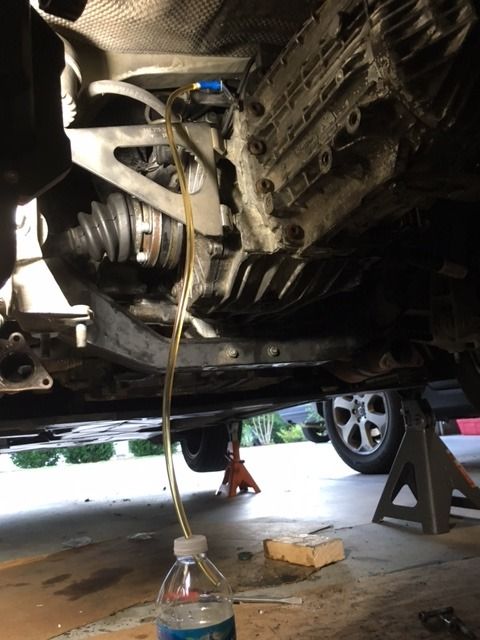
Because I’d just removed a bracket and set screw, the shifter cables went back into place without fracturing the uber-expensive ball joint ends. The muffler and exhaust also bolted back into place with brand-new stainless steel hardware. Finally, I installed the straight aluminum braces and the large aluminum plate and bracket. I was done with everything under the car.
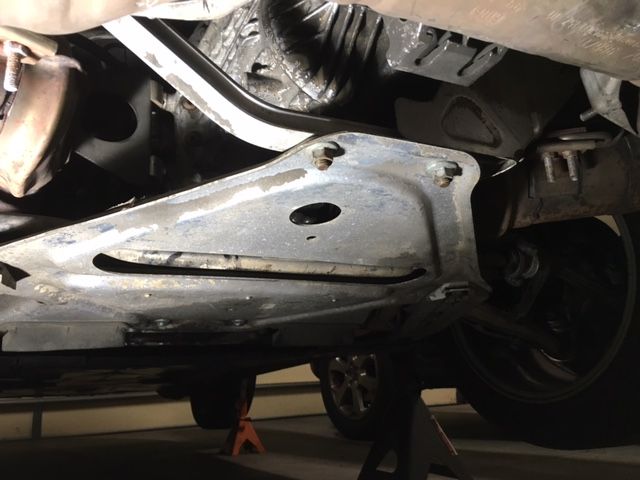
I had a checklist of work steps required for re-assembly, so I sat down and double-checked everything. Made sure the timing lock tools had been removed and the tensioners re-torqued. Forgot about oil. The sump had been drained before the tensioners were removed and hadn’t been re-filled. I’d stored the 10 quarts I’d drained in a clean, covered pan because the oil only had few hundred miles on it, and I’m frugal. As I was dumping the oil into the filler tube, the old crush ring in the bottom of the oil pan uncovered. Certainly, I’d installed a new crush ring when I re-torqued the drain plug? D-OH! A reminder of why I don’t do this for a living. Re-drain oil and install crush ring.
It’s time. Really getting nervous now. Key in the ignition. I anticipated chain clatter as the tensioners refilled with oil. What else would prompt me to immediately shut down the engine? My brain imagines my new bearing making a noise like a chain saw cutting sheet metal, or oil pouring out from the rear main seal. Ok, happy thoughts…happy thoughts.
Turn the key….two seconds of chain clatter….then nothing but the sewing-machine hum of a happy engine. I got a chill up my spine like the dang car was actually smiling at me. I said a quick prayer of thanks.
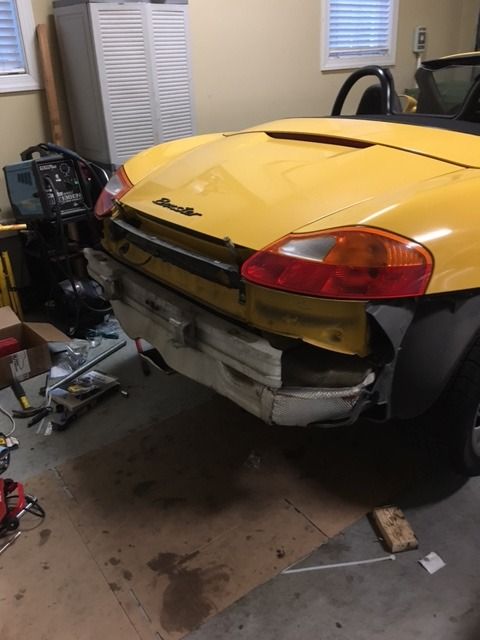
I really wanted to drive it, so I hauled the bumper cover into position and fumbled with the fasteners and screws. I’ve pulled a few bumper covers before, and anticipated a struggle getting the holes aligned with the rear quarter, but it all fell perfectly into place. New, black-oxide bolts on the actuators for the rear wing and snapped the painted cover back on. Dropped the car down off the jack stands and pulled it out of the garage. The clutch action was feather-light, with a nice progressive feel at the actuation point. Some of the message board debates on using the IMS shaft as an oil supply had mentioned the possibility of vibration or weird harmonics from the presence of oil within the shaft, but the engine felt smooth as silk. I put around 20 miles on it, and pulled it back into the garage. Shut it down, and there’s the reassuring sound of tick…tick…tick…as the engine starts to cool down.
So – a few thoughts from my project: R & R’ing a Porsche Boxster clutch is pretty straightforward, and is easily done without a lift. With a little pre-planning, it’s do-able over a weekend, and there are several IMS bearing replacement options that can be installed “while you’re in there” in less than two hours.
I’m a frugal mechanic, and so far, I’m really glad I bought this car.