Today was very productive! And over 100F, which is an odd combination. Usually I wilt in the heat like a fragile flower.
First, I implemented the "shelf under the welding bench" project. Basically, four cross tubes under the bench spaced at about 10" intervals. I used tube instead of square because I figured it would be easier to slide things over it. Also, I had tube.
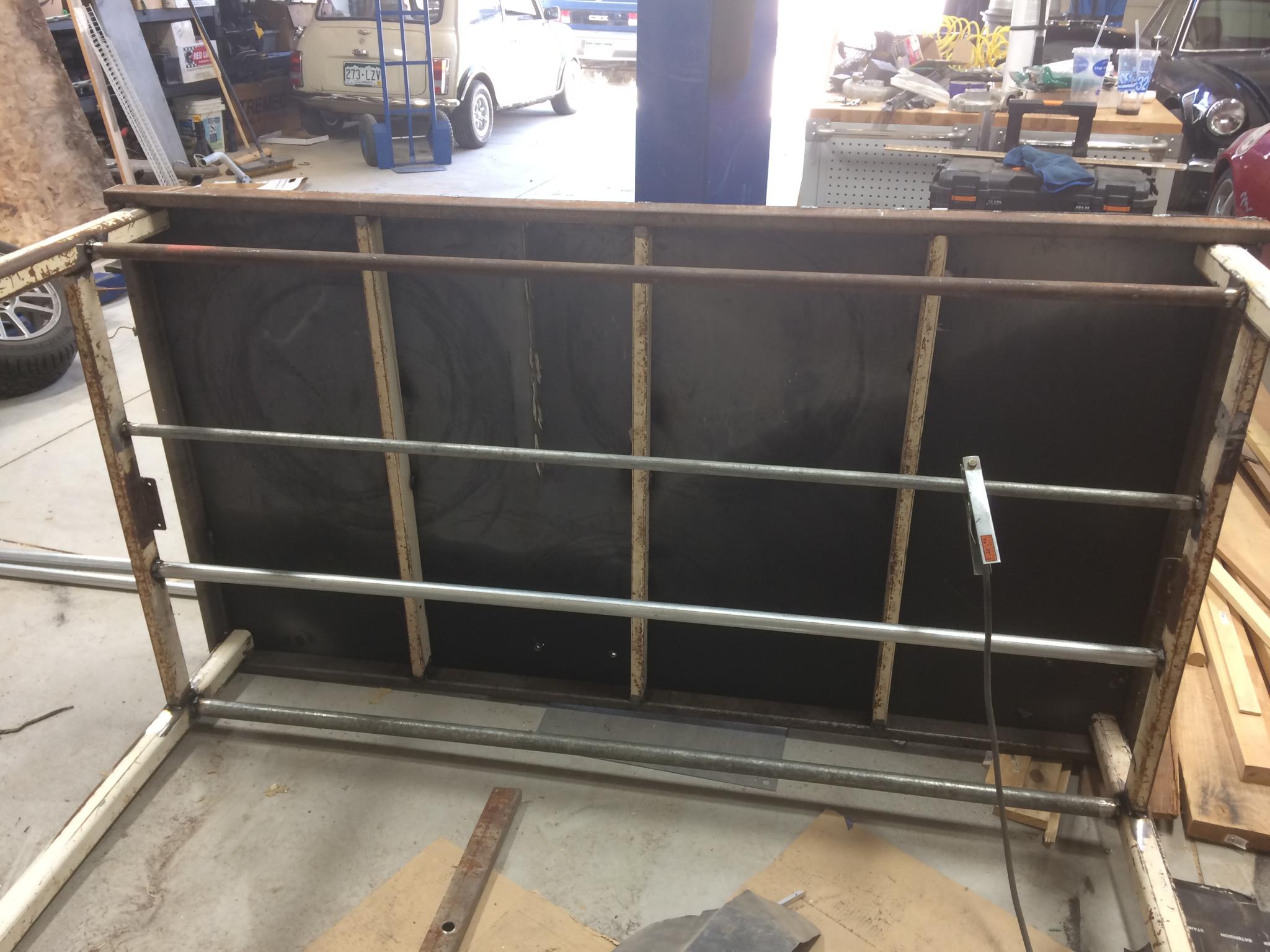
I love my welding bench. It's made of scrap steel. The legs are 2x2x1/4", the bars are 1x2x3/16" or so. It's immensely strong and really heavy. I'm thinking of getting some sort of magnetic clamps to use for holding things in place, but that's for later.
Because I had it away from the wall, I figured I'd mount my steel pegboard behind it. This is partly for convenience so I can hang tools and also to protect the plastic-backed insulation. I headed to Home Depot to pick up supplies.
And when I walked in, I saw an air conditioner sitting just inside the door. "That's funny," I thought, "that's the same model I ordered. Mine's not supposed to be here for a week." I looked closer and my name was on it. It had just arrived. Did I mention it was 100F outside? Woohoo!
A big tip of the hat to RossD for doing the calculations on the amount of cooling I'd need. He figured that a 1.5 ton system would keep the shop at 75F for all but the hottest 5-10 days of the year. Did you know that means the equivalent of 1.5 tons of ice? What an excellent unit of measurement. Anyhow, that means 18,000 BTU or 18 MBH. 21 MBH would be able to handle the worst days. I looked around and saw that most used AC systems were on the sketchy side and either too small or industrial sized, so I popped for a new 22 MBH unit.
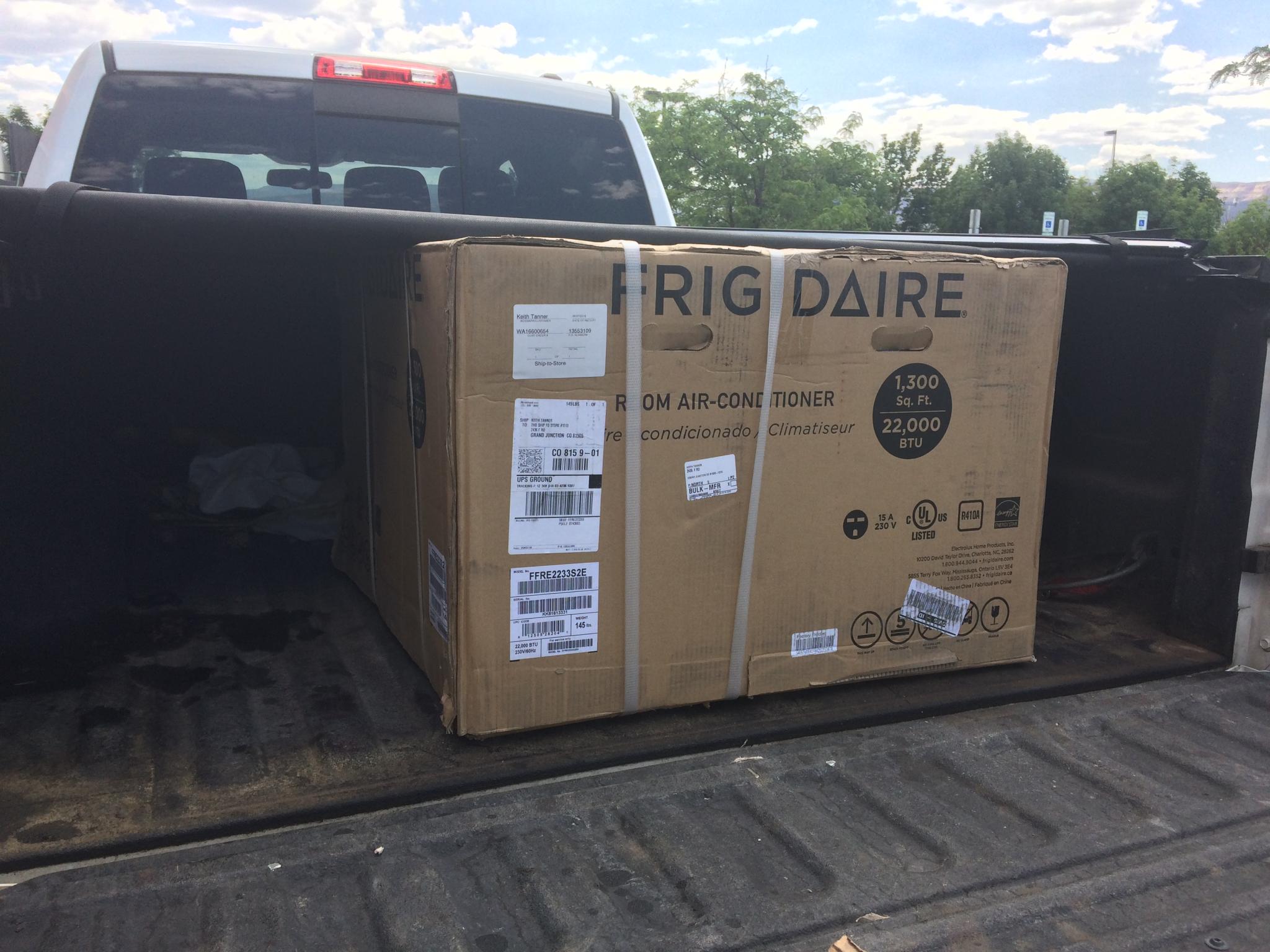
Unfortunately, I was in the middle of a linked series of projects so the sexy new aircon had to wait. Unloading that out of the truck solo required a bit of creativity, by the way. Two 10' 2x4s were used as a ramp and gravity helped out. Anyhow...
To mount the pegboard, I used joist hangers attached to the steel uprights. A couple of 2x4s between them and I was able to start paneling with the steel pegboard. I'd say this was really quick, but it took a surprisingly long time.
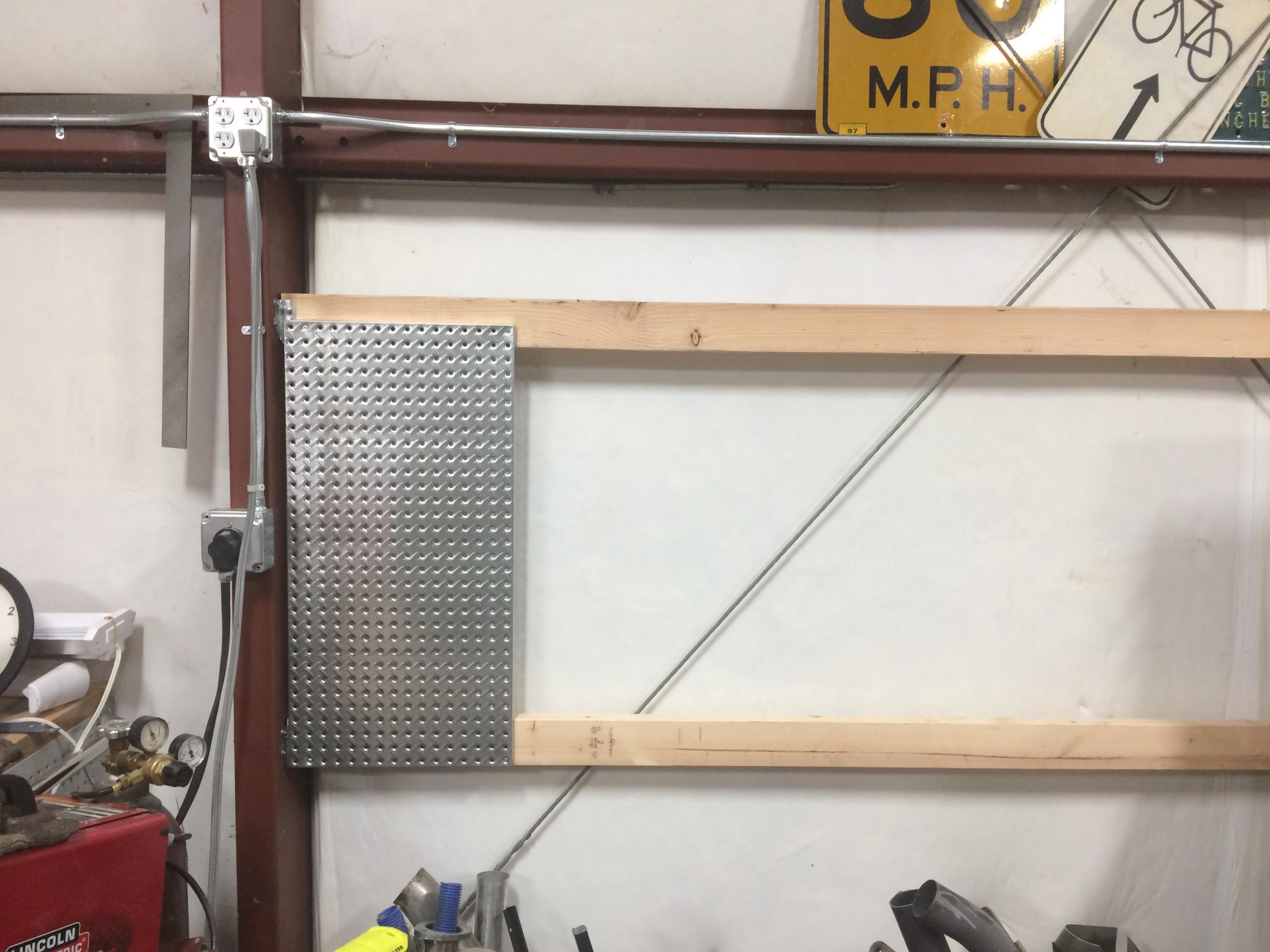
I left some exposed wood at the top in case I decide to screw anything else on there.
Here's the fab station almost fully set up. Look at all that nicely organized metal on the shelf underneath! Thanks for the idea on that one specifically, Paul. I'll be building little trolleys for the other stuff that didn't fit later.
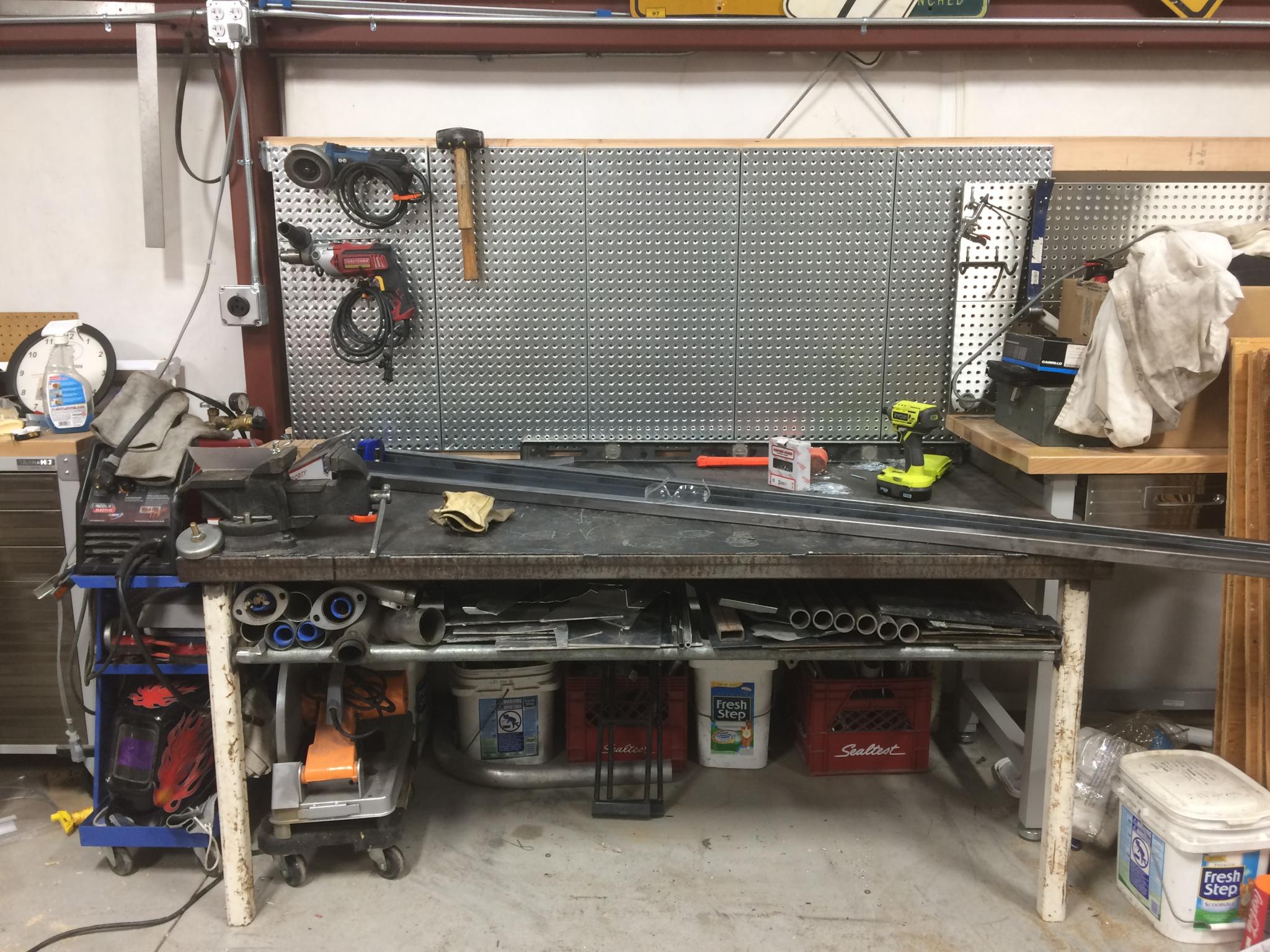
Since I was doing pegboard, I decided to mount the 4x8 sheet that was planned for behind one of my workbenches. For this one, I used one 2x6 as well as two 2x4s because the board is a little less solid. This corner is really coming together, and now I can start to put tools away in their forever homes. In case you're wondering, I have about 50 square feet of pegboard plus pegboard backs on two workbenches.
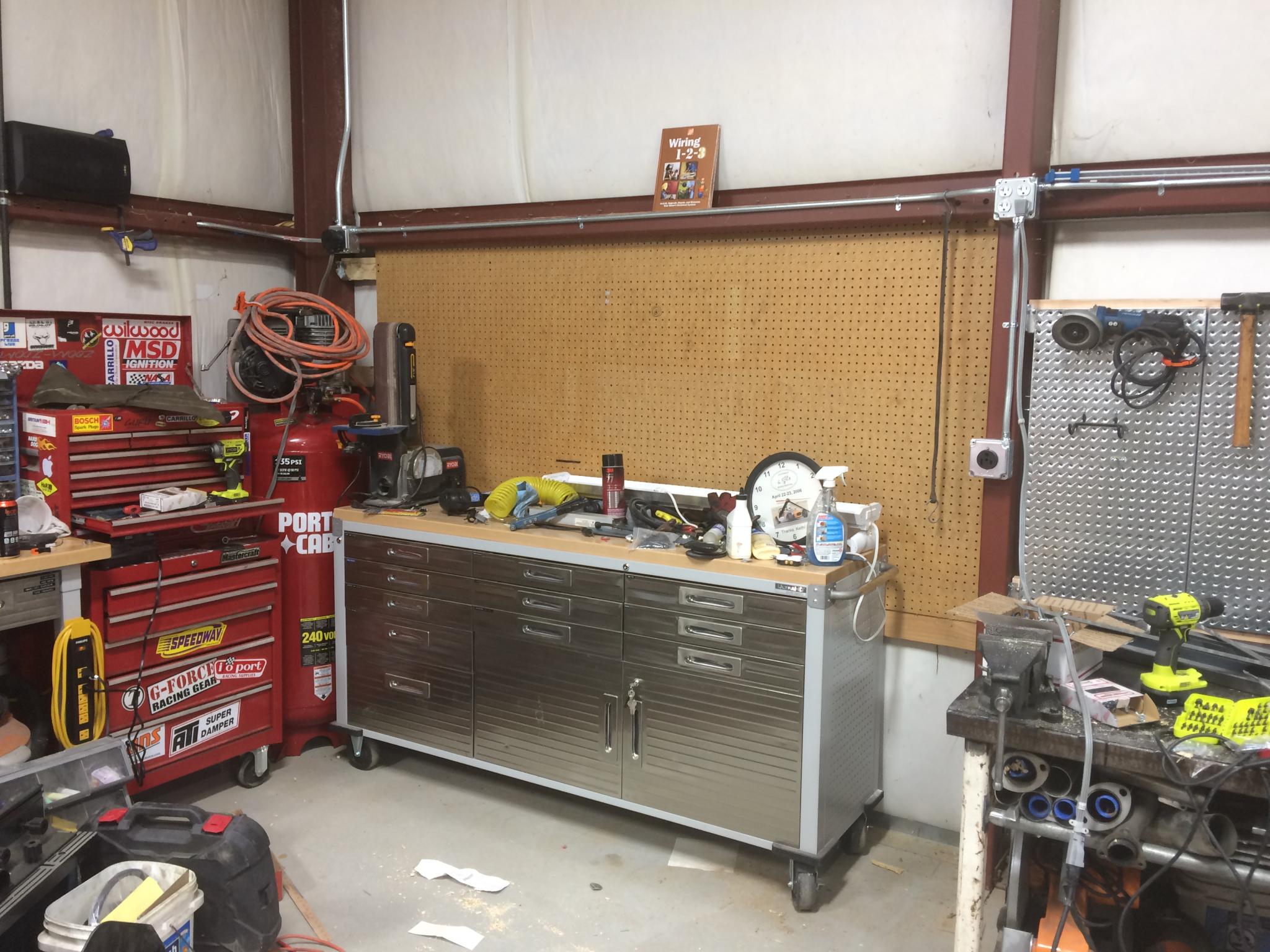
I also built my tire rack to get all the spare wheels and tires out of the way. I'd started this project earlier in the week but all the debris that needed to go in the sheet metal rack was in the way. Everything is connected.
This is super-simple - a couple of 1" pipes stuck through some 2x4s. The 2x4s are in joist hangers and the outer pipe is supported by cables that run up to the eyebolts for the garage cross bracing. This is an experiment. I've learned so far that I need thicker wall pipes as this stuff is bending. I put a strap between the two pipes to keep them from spreading and I could add a third support cable in the middle, but the right answer is really more rigidity. I may build another one of these as this one won't hold all my wheel/tire detritus.
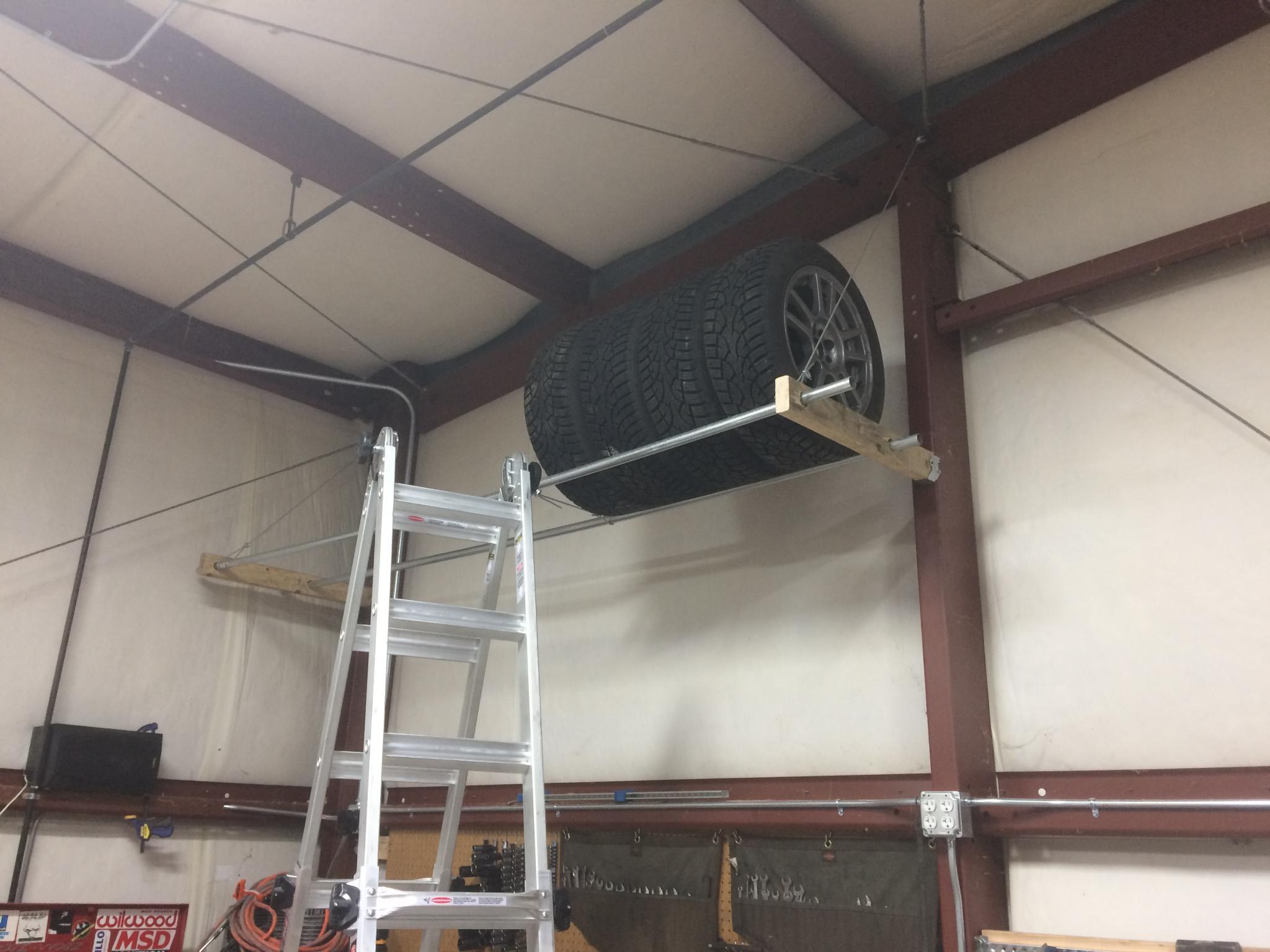
By this point, I was dehydrated and hot and so (ironically) unable to install the AC. Hopefully on Saturday! It was a good day today, I made a couple of major steps that will let me really put things away and clean the place up. Progress!