Looking back through team emails, I see that as of late April of this year, this was about where the project stood. I'm amazed that between April and November the Plymford went from a not-yet-running project to....well..you'll see soon enough. Incidentally, I just got word today that I have to travel down to southern GA (about an hour north of Jacksonville, FL) next week after Thanksgiving. That means a lot fo late nights in the hotel with nothing to do other than pound out some more of this story. :-)
As things stand...now, it was April. And after this melted...
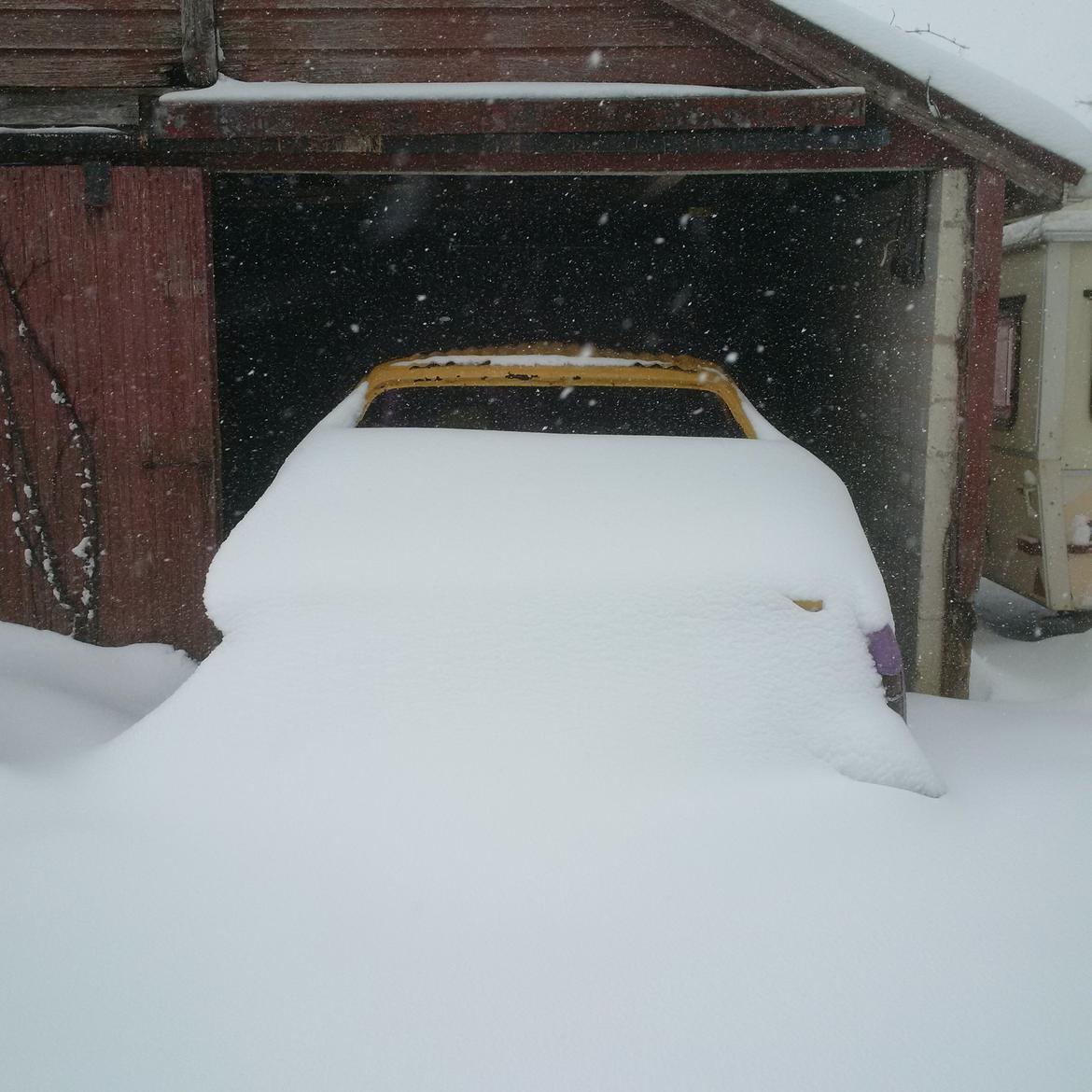
The transmission mount was the next thing on the list.
The stock LTD trans mount was a crossmember that mounted to two rear-facing frame appendages. Those appendages don't stick far enough back for the new trans location. I didn't want to lengthen them, as this would have created an even longer, cantilevered beam. So, the plan was to borrow a page from Chevrolet's playbook, and do it lke they did it on a late 60's Impala:

which is to say, frame rail to frame rail. Above pic is a '68 Impala underframe. Kinda neat how GM had two sets of mounting points for the crossmember- probably one for the manual trans, and the other for the auto. Anyway, that's basically how I planned to do it on the LTD- mounting tabs welded under the frame on each side, and a big ole C channel, facing up, from side to side (straight, though, not bent).
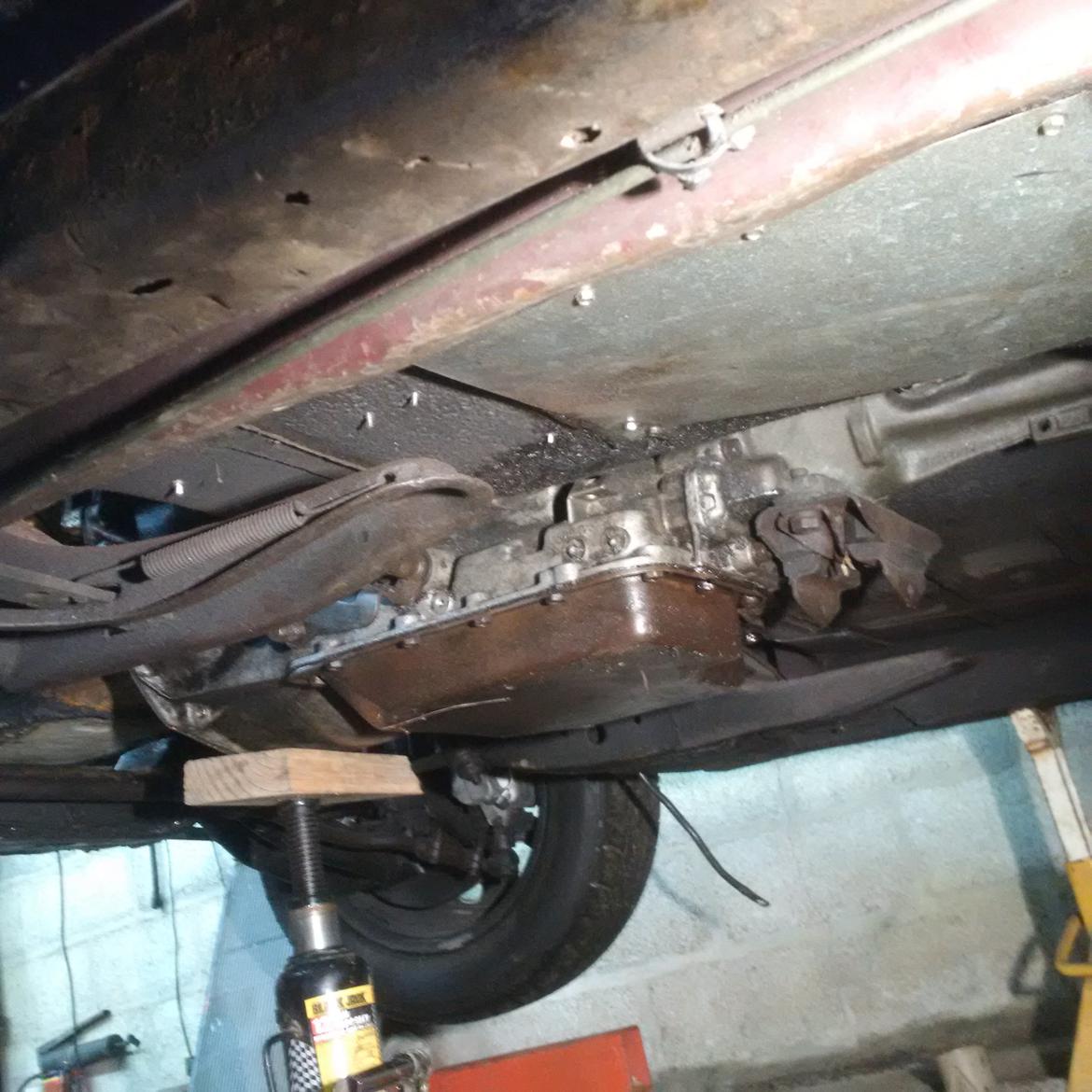
Without a lift, it's kinda hard to show what all I was dealing with under the car, but the above picture shows the two rearward-extending frame horns and the transmission between them. This whole setup was a bit hokey when it was originally conceived ("Hey! I've got an idea! Let's cantilever the rear drivetrain support right off into thin air! That'll totally work and not at all fatigue and fail!"...which, in all fairness, it hadn't...yet) but my redneck garage engineerin' was going to be a real thing of beauty and elegance.
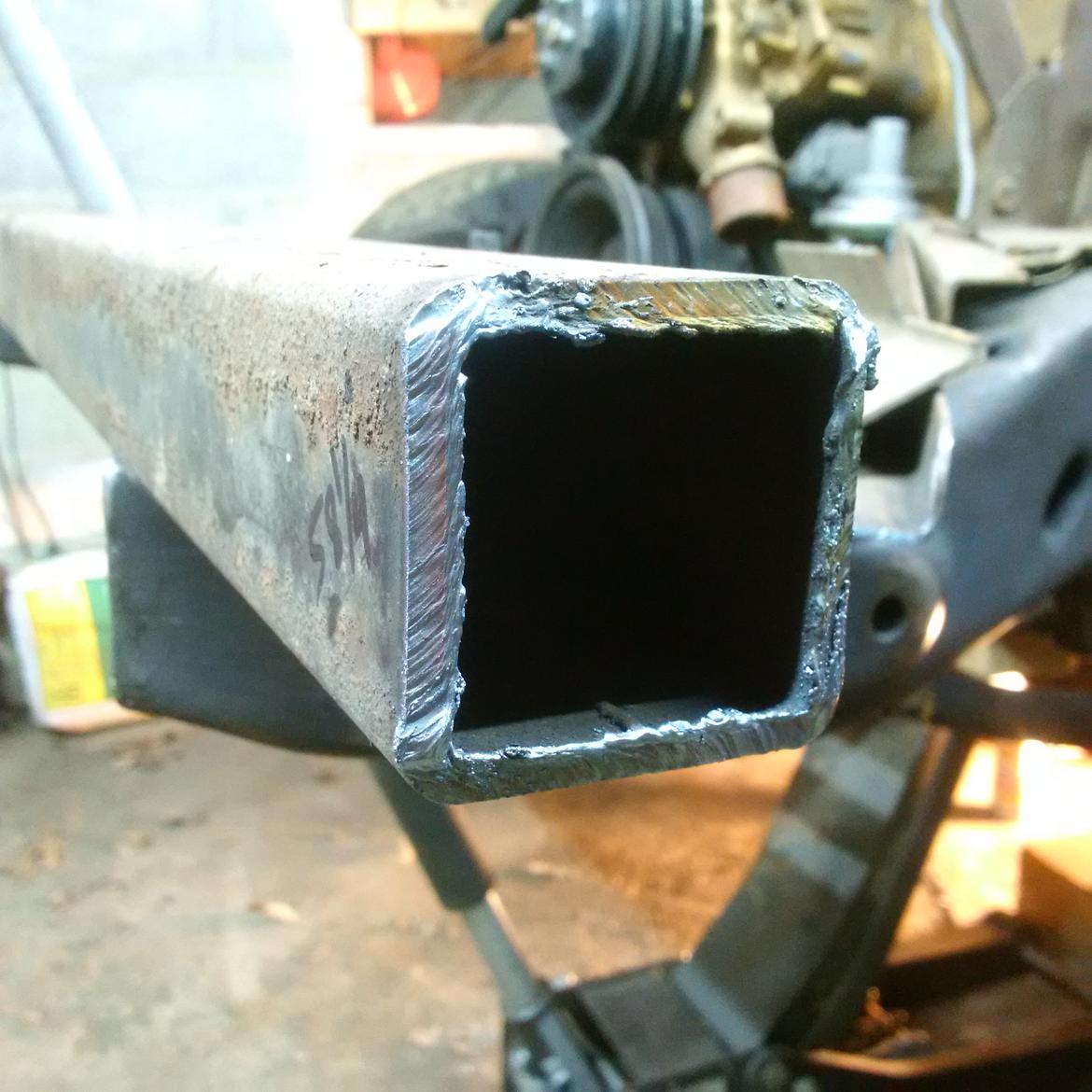
Or....whatever steel box channel I happened to have laying around that was long enough to span the left and right frame rail separation. In case you were wondering, that's from the tongue of a decrepit trailer I cut up for scrap a few years ago.
A straightedge long enough to span the width of the giant ridiculous car is a nice tool to have on hand.
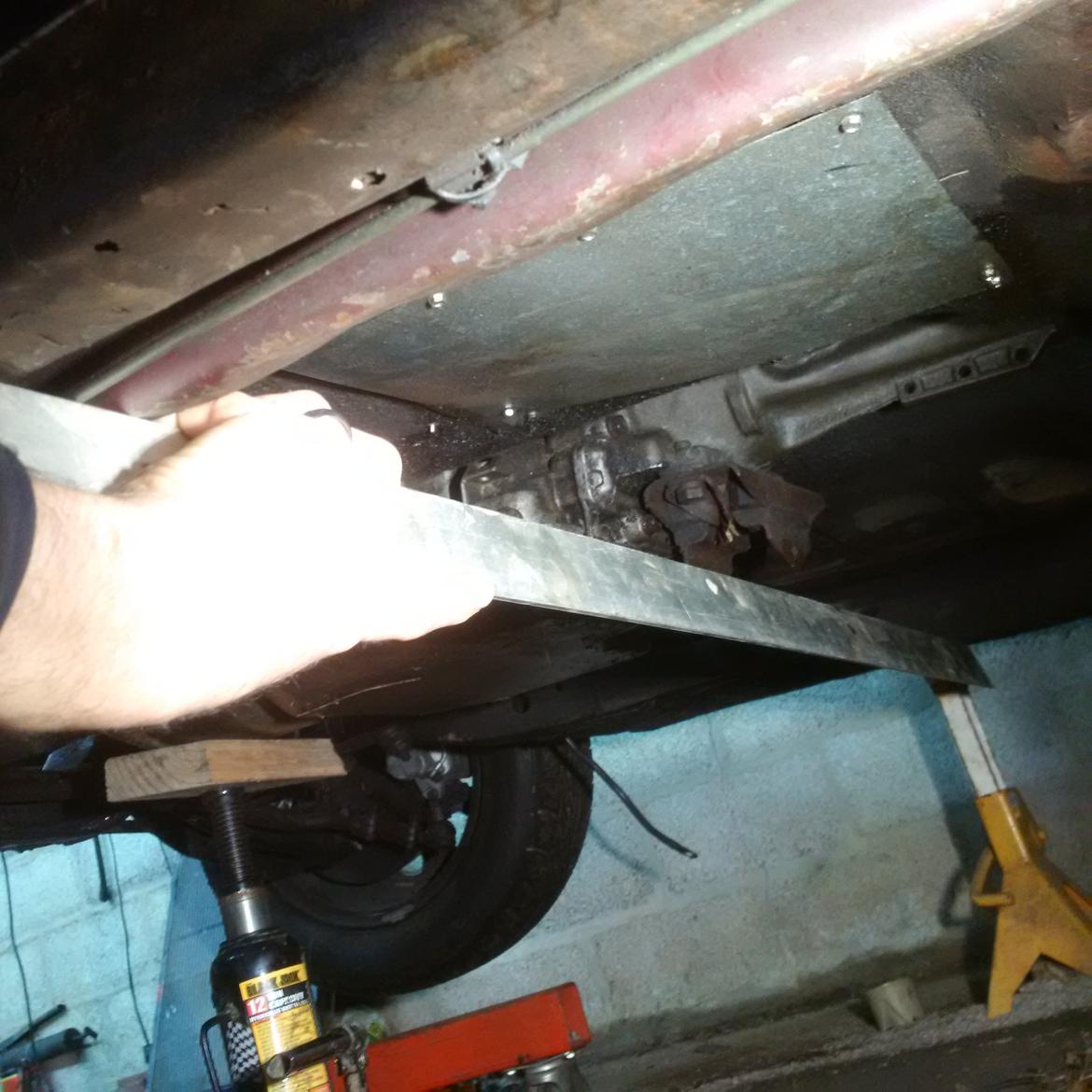
More hieroglyphics.
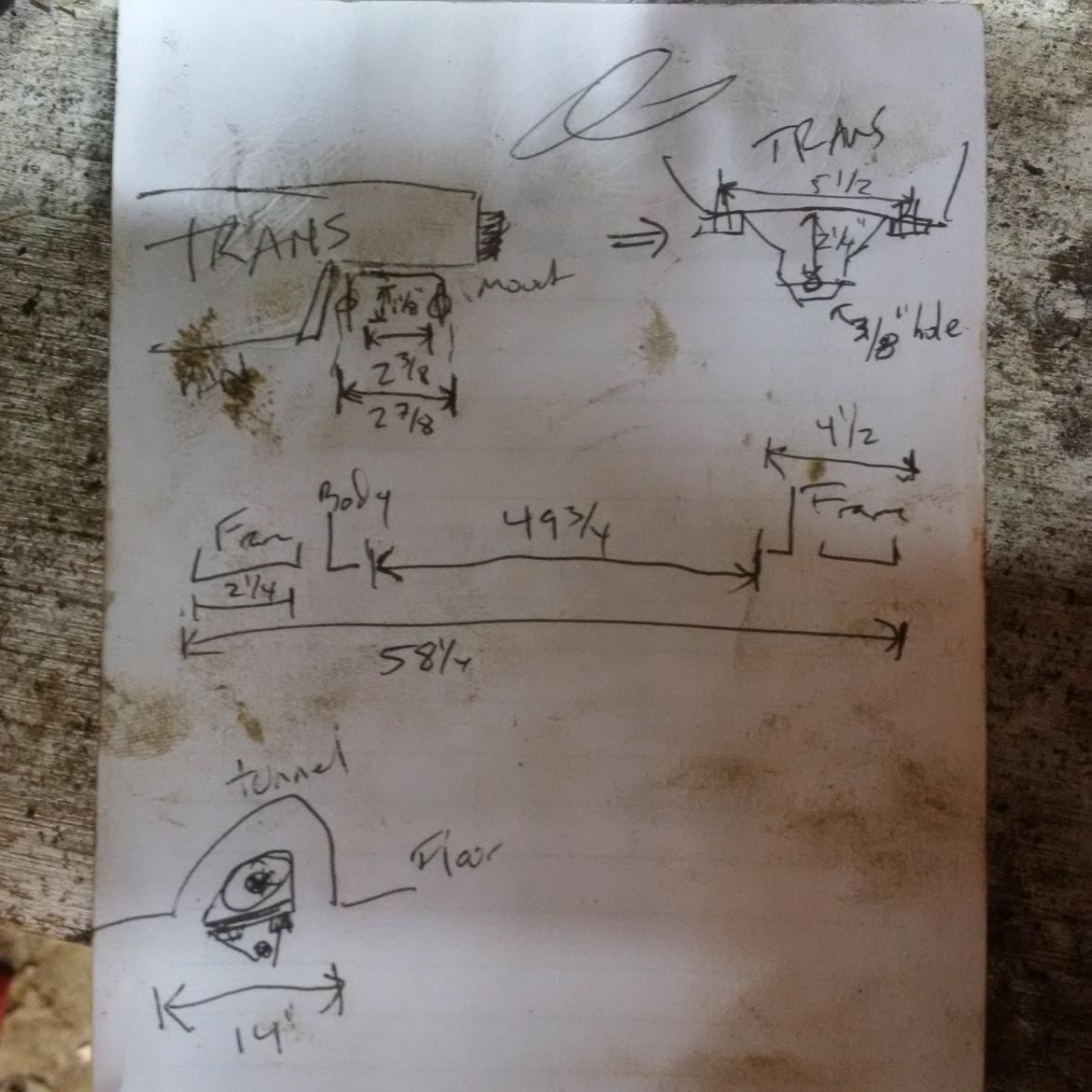
The frame rails of the 1975 LTD are extremely beefy. Actually, the whole car feels very solid. As one team mate said, it's like they took a full perimeter frame, and then designed a unibody car, and then combined the two. It's like a freaking tank. The frame rails run right inside the rocker panels. I'm not entirely unconvinced that this setup provides more side impact protection than the stoutest modern SUV. Regardless, the frame rails made for perfect locations to cut out and weld in some mounting pads.
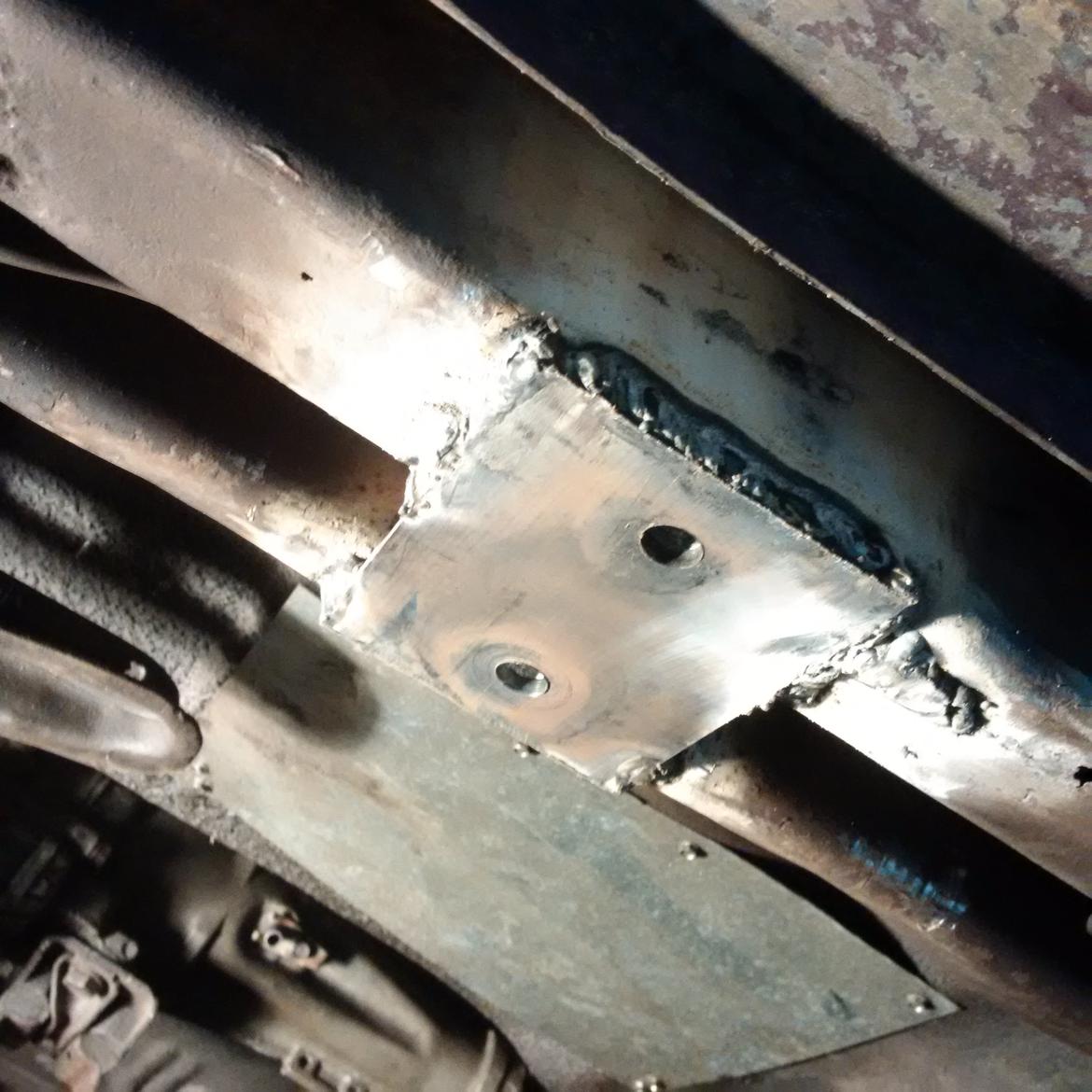
Wish I had some more pictures here to fully show what all is going on. These plates were cut out of 1/4" steel, drilled and mounting nuts welded onto the back. I then plasma'd holes in frame rails for the mounting nuts to go up inside, so the plate mounts just 1/4" down from the frame. Then the whole plate was perimeter welded into place.
Oh, and before welding the plates to the frame, I match-drilled the holes in the plates to that hulking chunk of box channel that's meant to span from one frame rail to the other.
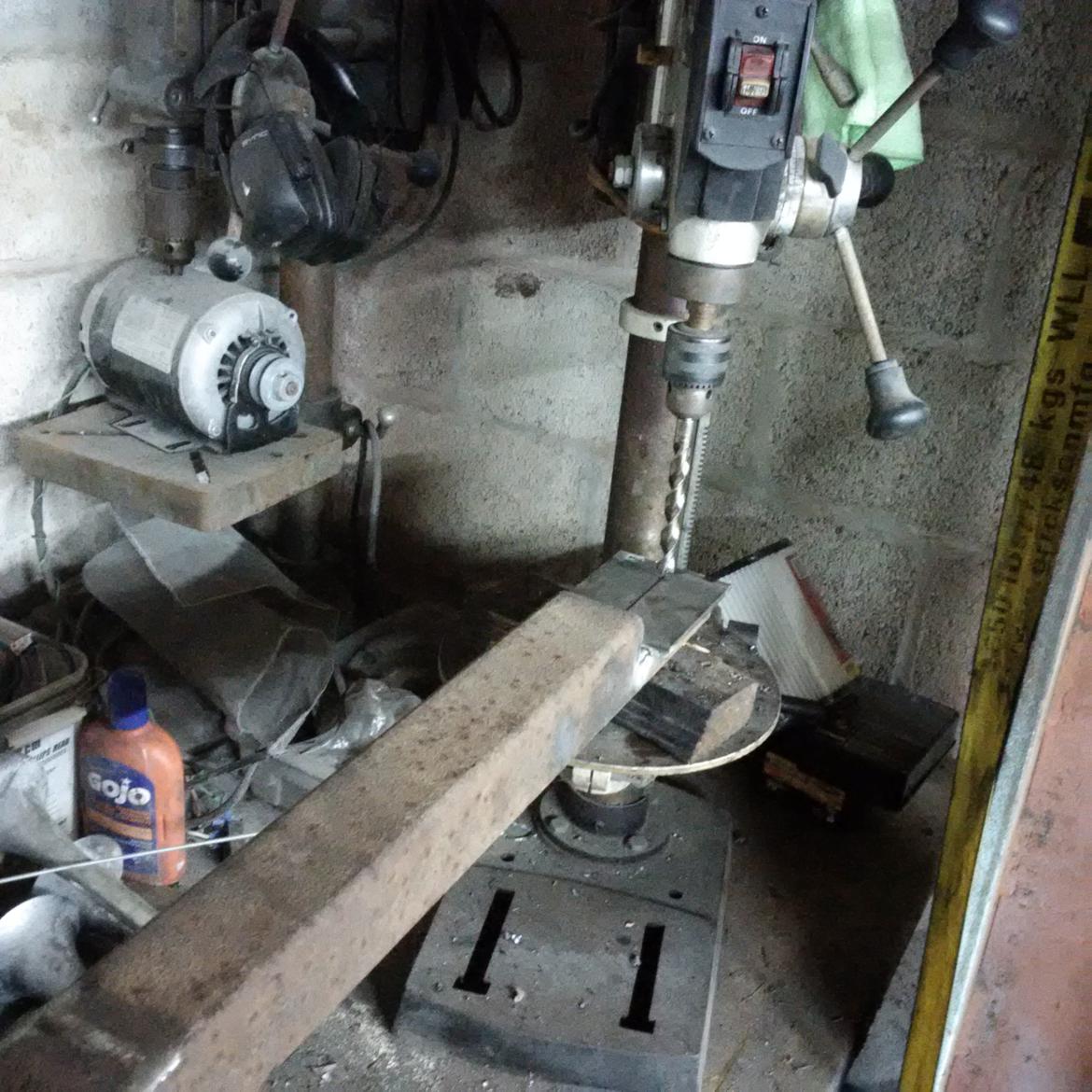
AND- notched the box channel at each end to provide the correct mounting height for the back of the transmission mount.
There was just so much geometry going on here...and calculations...and measurements. It was sort of like putting together a giant erector set, only the pieces are all custom-made, and everything has to be cut apart and put together with fire. And there's no instructions.
Both frame rail pads in place, it was time to test fit the transmission crossmember.
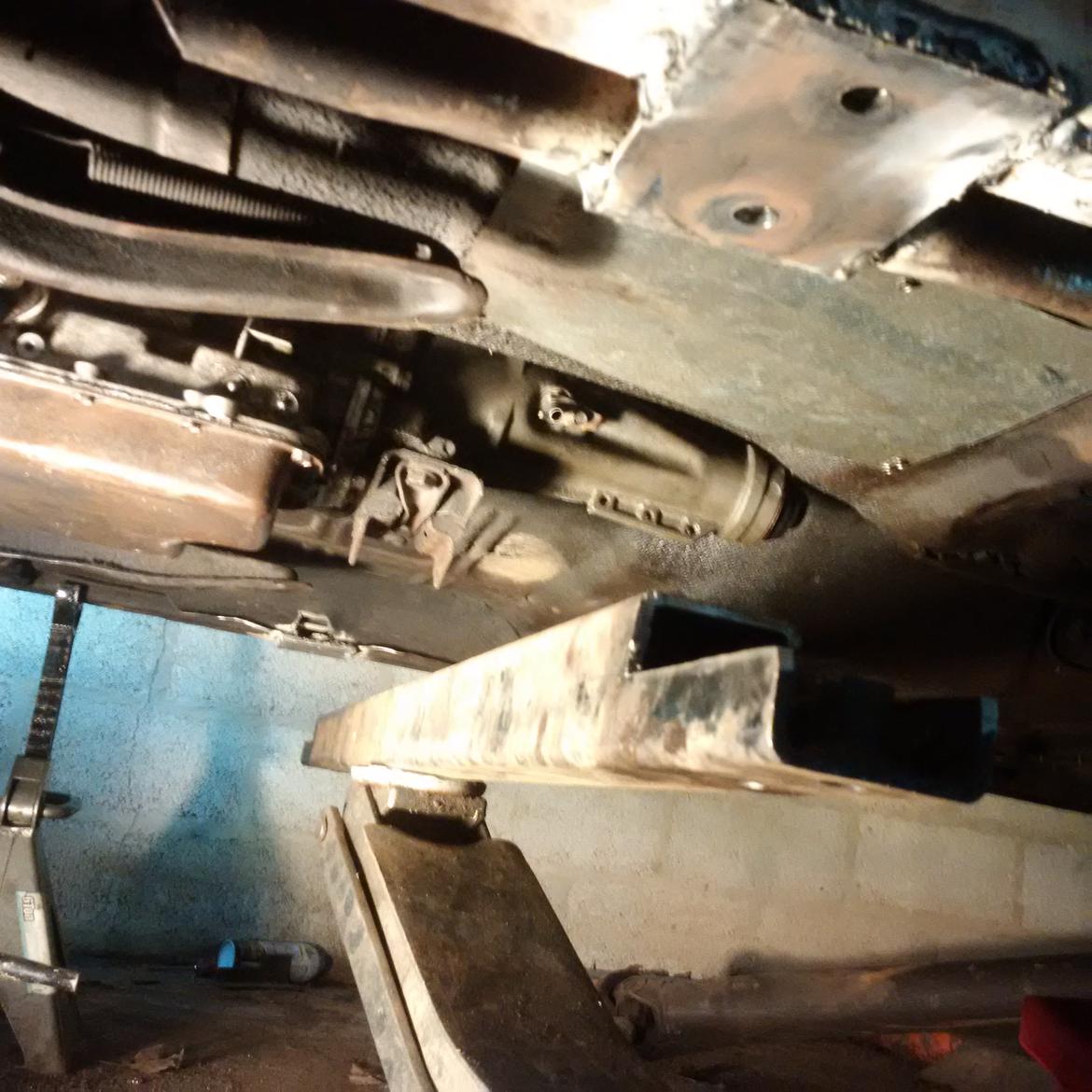
(This is the part where we cut to a commercial. Everyone, hold your breath!)
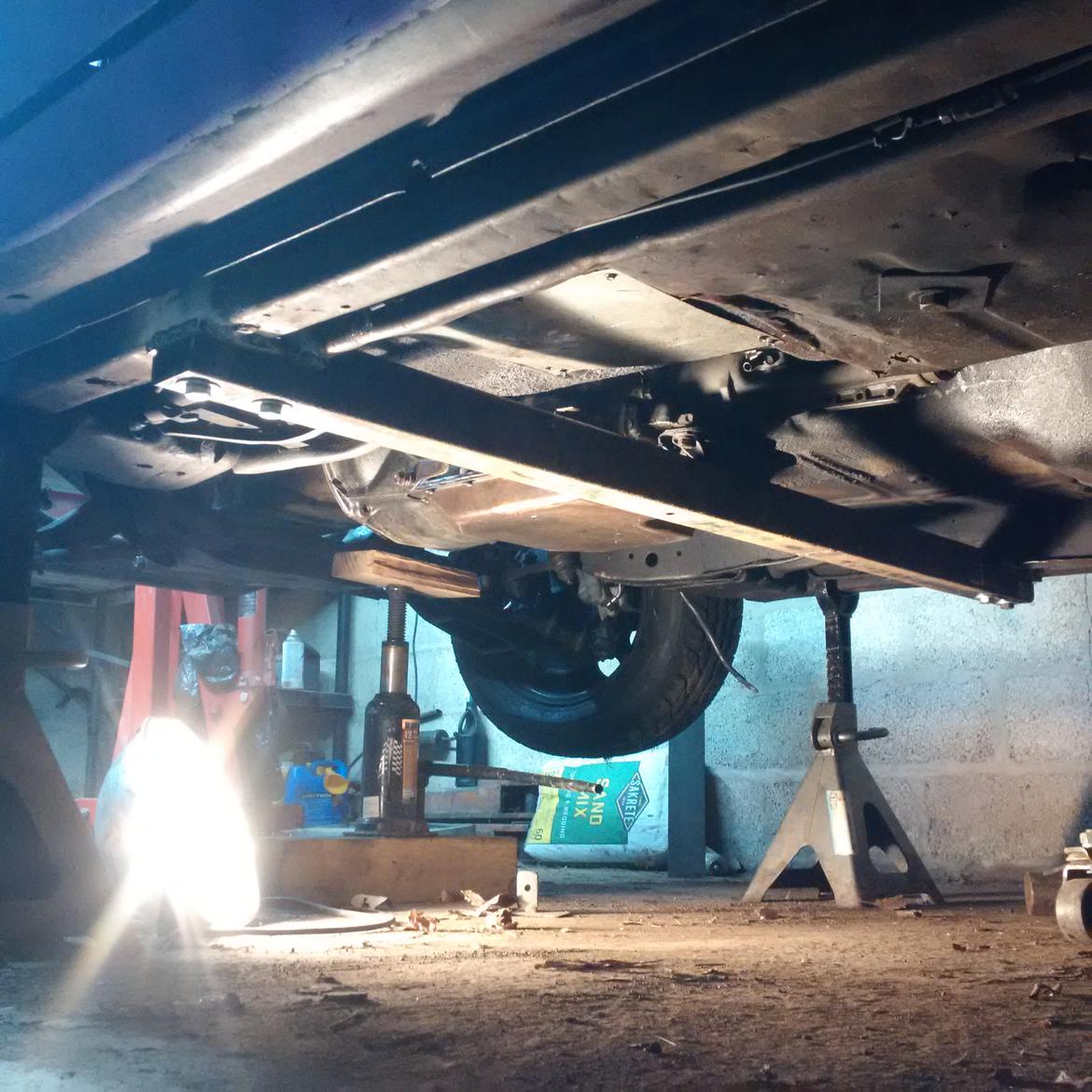
It's in! And hey, look at that- the box channel is exactly the same width as the clearance inside the transmission mount bracket. It's like..someone actually thought of that beforehand!
The bolts all go in, and everything. Wow. This sure felt good.
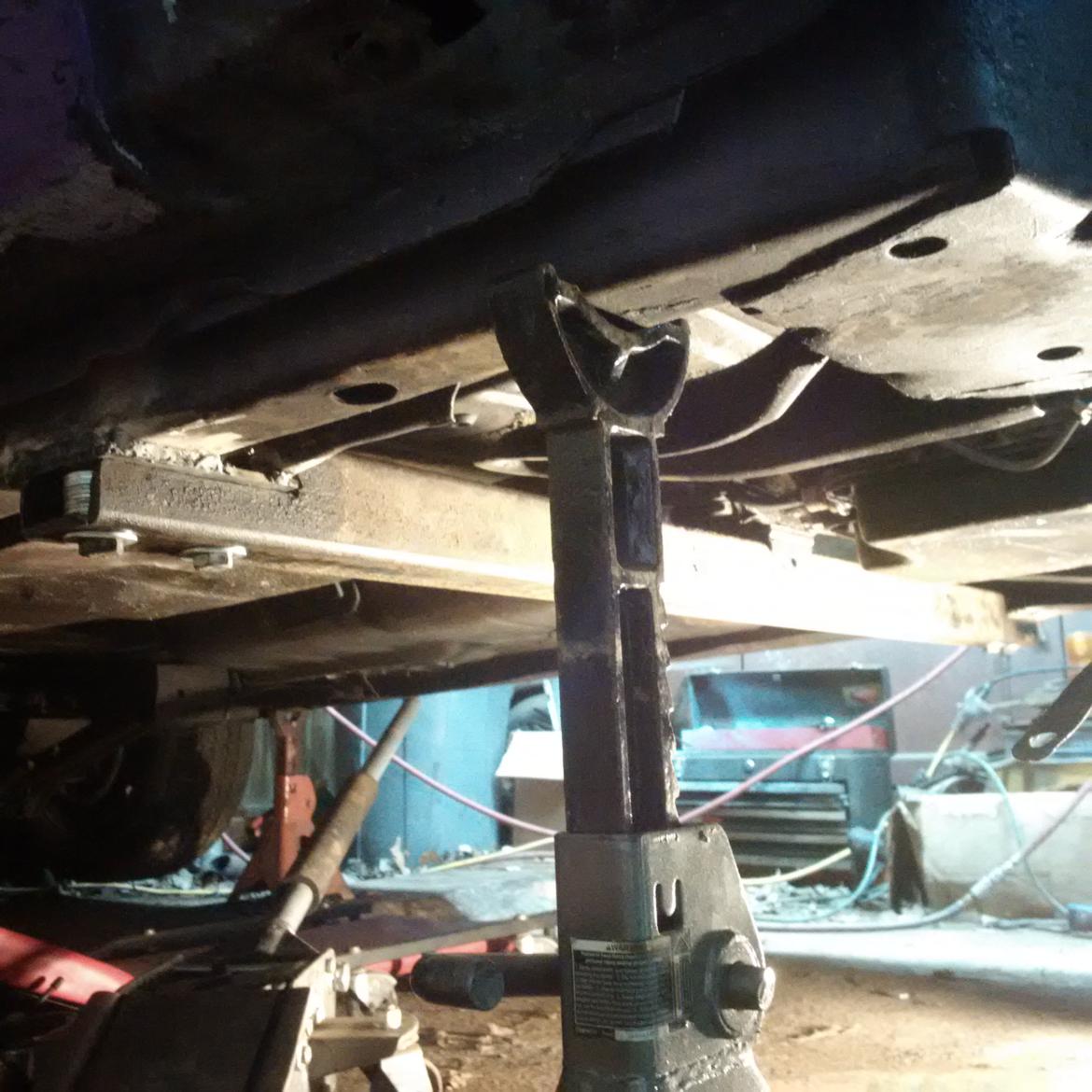
You can sort-of see inside the crossmember there, at the end, there's a stack of washers for each bolt to go through (4 bolts total, 2 per side). That's so the open section of channel there doesn't bend is as the bolts tighten. The stacks of washers were welded together to make spacers. Not particularly elegant, but it works. I wasn't super happy about the whole transmission crossmember jutting down an inch or so from the bottom of the frame....but berk it, it's a race car. It'll be _fiiine_.
And now we can cross "mount transmission mount" off the list.