If you want to print a template, print one that has oversize holes you can press a steel bushing into (because a drill bit will quickly enlarge any plastic bore), with an I.D. only large enough for a pilot hole. Use the template to get all your pilot holes dead nuts on then just come back and open them up.
This is a great use of a 3d printer. I do stuff like that often at work.
In reply to ProDarwin :
I was thinking about making the holes just big enough to drill some pilot holes to get started...
TAB
None
12/10/19 11:22 p.m.
Hopefully I can resurrect this thread or get pointed in the right direction.
I’m wondering about a plastic adapter/spacer between cv bolt on flange and transaxle flange. Specifically, is there 3D printed filament strong enough to hold threads?
Thanks. Google searches keep sending me to GRM. Love the innovation and assistance I see here. Figured it was definitely time I signed up.
Threads in ABS fail at very low torque. I think the short answer is no. However, you could increase the strength by having a metal insert. It is common to put a hexagon shape relief in 3d parts to press fit a standard nut.
bluej
UberDork
12/11/19 4:18 p.m.
Knurled. said:
ProDarwin said:
If you want to print a template, print one that has oversize holes you can press a steel bushing into (because a drill bit will quickly enlarge any plastic bore), with an I.D. only large enough for a pilot hole. Use the template to get all your pilot holes dead nuts on then just come back and open them up.
This is a great use of a 3d printer. I do stuff like that often at work.
BRILLIANT!
I was thinking about doing similar to make engine-bellhousing adapters.
TAB said:
Hopefully I can resurrect this thread or get pointed in the right direction.
I’m wondering about a plastic adapter/spacer between cv bolt on flange and transaxle flange. Specifically, is there 3D printed filament strong enough to hold threads?
Thanks. Google searches keep sending me to GRM. Love the innovation and assistance I see here. Figured it was definitely time I signed up.
I'm not picturing this use case, but to answer the thread question - even basic ABS machines you can heat-stake threaded inserts (made for injection molding) into the material that are crazy strong. They don't make sizes for large bolts though.
https://www.mcmaster.com/threaded-inserts/=d1c811cf5998467cb98a366f8b85dd1dk424z8ie
They sell a small adapter so you can install them with a soldering iron. I've done this before with PC-ABS off a Stratasys machine like 10 years ago, and even a 10-32 you would bend the screw before the material gave out. I'm not sure which would strip out first, but you are well beyond the torque needed if you strip it out.
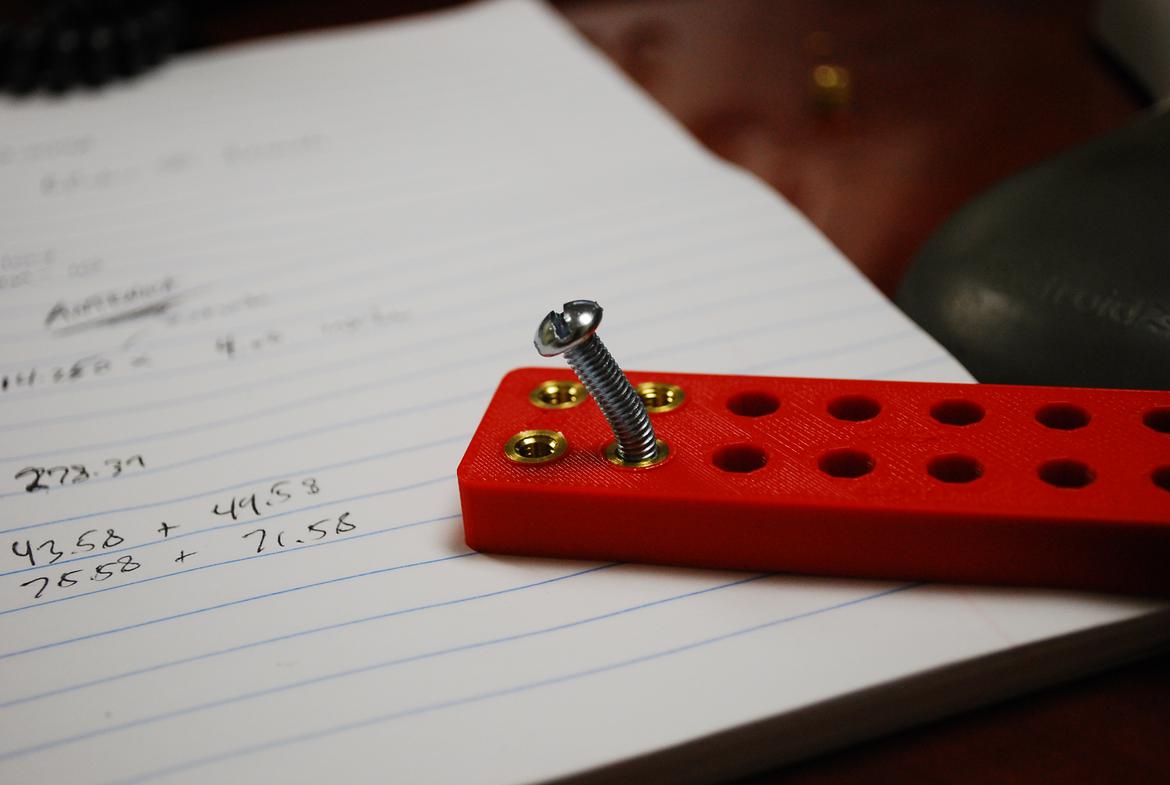
TAB
New Reader
12/14/19 4:20 a.m.
ProDarwin said:
TAB said:
Hopefully I can resurrect this thread or get pointed in the right direction.
I’m wondering about a plastic adapter/spacer between cv bolt on flange and transaxle flange. Specifically, is there 3D printed filament strong enough to hold threads?
Thanks. Google searches keep sending me to GRM. Love the innovation and assistance I see here. Figured it was definitely time I signed up.
I'm not picturing this use case, but to answer the thread question - even basic ABS machines you can heat-stake threaded inserts (made for injection molding) into the material that are crazy strong. They don't make sizes for large bolts though.
https://www.mcmaster.com/threaded-inserts/=d1c811cf5998467cb98a366f8b85dd1dk424z8ie
They sell a small adapter so you can install them with a soldering iron. I've done this before with PC-ABS off a Stratasys machine like 10 years ago, and even a 10-32 you would bend the screw before the material gave out. I'm not sure which would strip out first, but you are well beyond the torque needed if you strip it out.
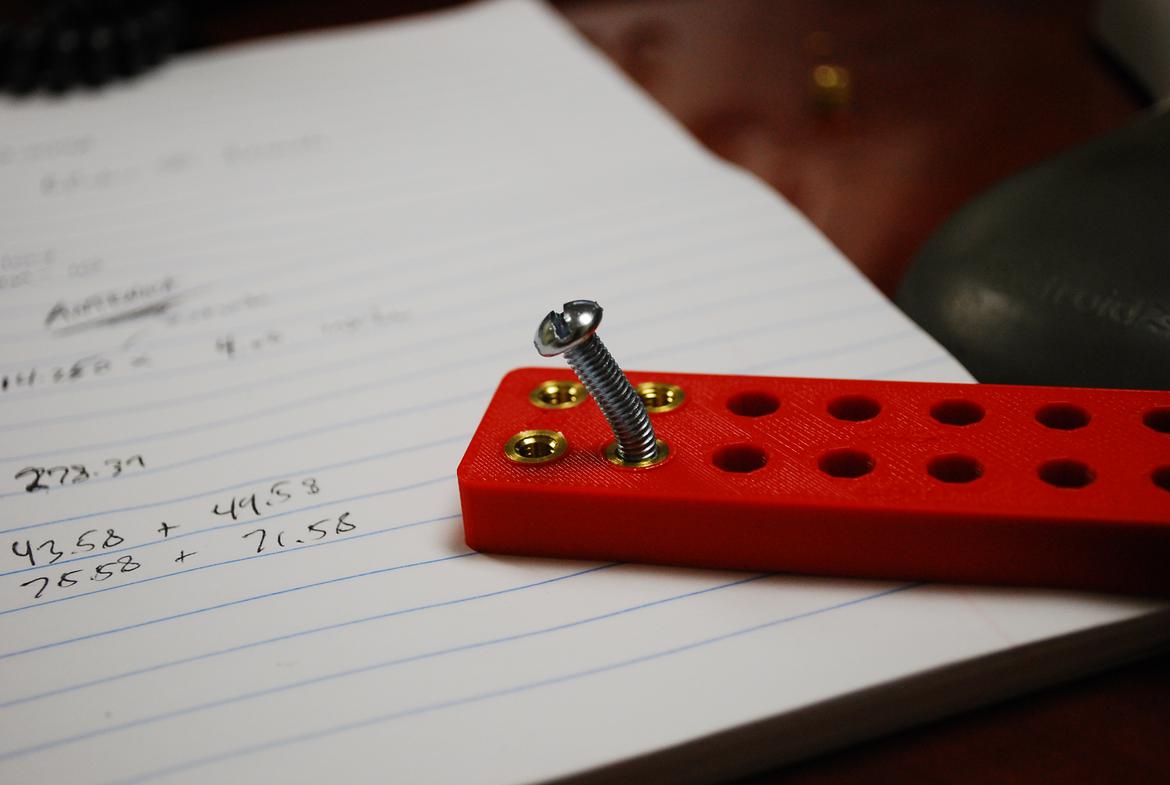
I was envisioning using a tap to get the threads as would be done in metal. Much appreciate you sharing the McMasters info. Looks like that may be a great option.
bluej said:
Knurled. said:
ProDarwin said:
If you want to print a template, print one that has oversize holes you can press a steel bushing into (because a drill bit will quickly enlarge any plastic bore), with an I.D. only large enough for a pilot hole. Use the template to get all your pilot holes dead nuts on then just come back and open them up.
This is a great use of a 3d printer. I do stuff like that often at work.
BRILLIANT!
I was thinking about doing similar to make engine-bellhousing adapters.
You'd need something with a huge table to do that.
Maybe I'm OTB. In my mind when I think of 3D printing things at home, it's stuff under 3-4 inches square. A bellhousing adaptor, even a drill guide, would require a table at least 24x24 inches.
I also can't see doing it in plastic and reinforcing it without a lot of fettling. Hell, bits made out of cast or weldment need fettling, to get within tolerance. That's why offset dowels exist, just to make OEM mass produced (read: fairly precise) product correct.
TAB said:
ProDarwin said:
TAB said:
Hopefully I can resurrect this thread or get pointed in the right direction.
I’m wondering about a plastic adapter/spacer between cv bolt on flange and transaxle flange. Specifically, is there 3D printed filament strong enough to hold threads?
Thanks. Google searches keep sending me to GRM. Love the innovation and assistance I see here. Figured it was definitely time I signed up.
I'm not picturing this use case, but to answer the thread question - even basic ABS machines you can heat-stake threaded inserts (made for injection molding) into the material that are crazy strong. They don't make sizes for large bolts though.
https://www.mcmaster.com/threaded-inserts/=d1c811cf5998467cb98a366f8b85dd1dk424z8ie
They sell a small adapter so you can install them with a soldering iron. I've done this before with PC-ABS off a Stratasys machine like 10 years ago, and even a 10-32 you would bend the screw before the material gave out. I'm not sure which would strip out first, but you are well beyond the torque needed if you strip it out.
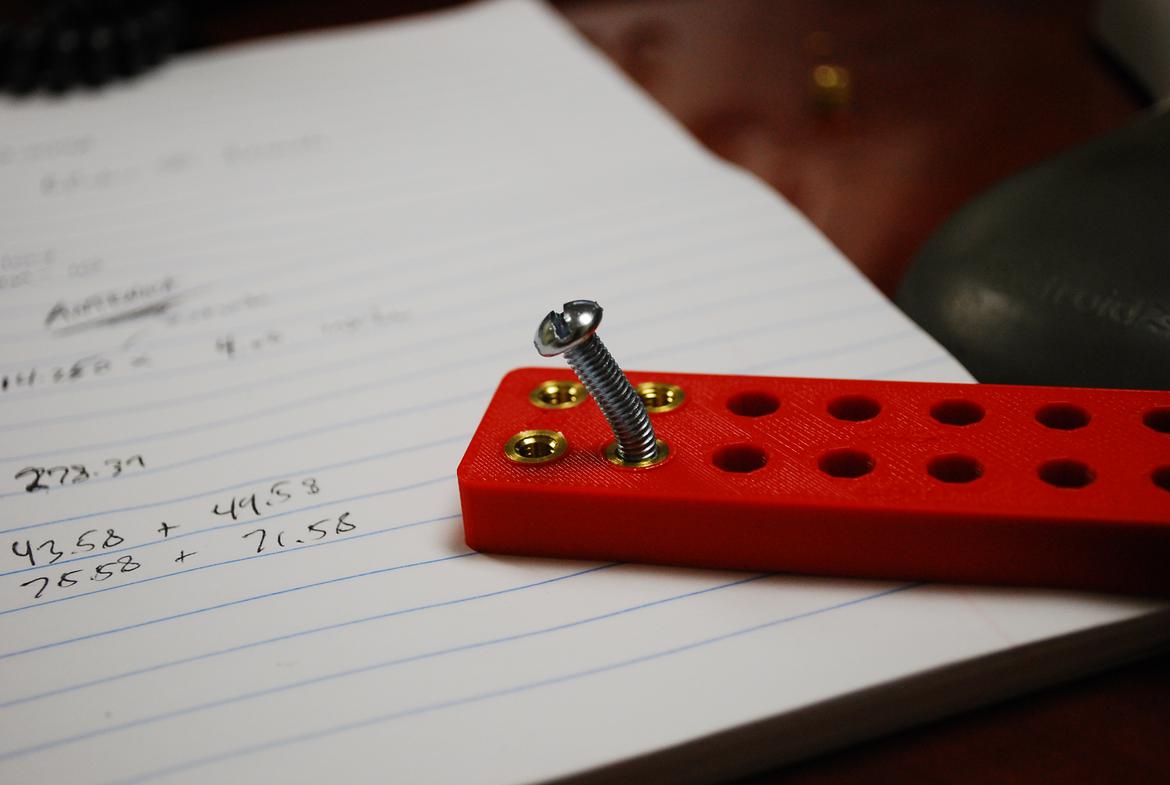
I was envisioning using a tap to get the threads as would be done in metal. Much appreciate you sharing the McMasters info. Looks like that may be a great option.
I've use Helicoils (or Non-Trademark Named Spiral Thread Inserts) to reinforce aluminum a number of times. Would they work just as well in plastic?
Only one way to find out!
bluej
UberDork
12/14/19 10:05 a.m.
Knurled. said:
bluej said:
Knurled. said:
ProDarwin said:
If you want to print a template, print one that has oversize holes you can press a steel bushing into (because a drill bit will quickly enlarge any plastic bore), with an I.D. only large enough for a pilot hole. Use the template to get all your pilot holes dead nuts on then just come back and open them up.
This is a great use of a 3d printer. I do stuff like that often at work.
BRILLIANT!
I was thinking about doing similar to make engine-bellhousing adapters.
You'd need something with a huge table to do that.
Maybe I'm OTB. In my mind when I think of 3D printing things at home, it's stuff under 3-4 inches square. A bellhousing adaptor, even a drill guide, would require a table at least 24x24 inches.
I also can't see doing it in plastic and reinforcing it without a lot of fettling. Hell, bits made out of cast or weldment need fettling, to get within tolerance. That's why offset dowels exist, just to make OEM mass produced (read: fairly precise) product correct.
you're a bit behind the times in terms of 3d printing capabilities. I just bought a machine w/ a 350mm x 350mm x 400mm build volume for a bit over $500.
You also assume you have to print the entire thing in one go. if all you're doing is creating essentially a drill guide for where to place holes, etc, it can be multiple pieces that are intelligently designed to lock together. also, of course you'd need to check for accuracy, but if your machine is consistent, you can adjust the printing process to compensate.
As for size. My printer will do 14.5" in dia. and 18.5 tall.
Spacers would be a hard no for 3D printing in plastic. The extruder temps about only about 400 degrees. The spacer would just extrude itself under braking temps.
I have made a set of centering rings out of PVC before. They worked fine for several years.
kb58
SuperDork
12/14/19 11:39 a.m.
FWIW, back a few years (and maybe still), there were paint kits sold for painting brake calipers blingy colors. I painted mine red and all was good, right up until the first trackday event. Discovered part way through the event that the caliper mounting bolts were loose. I was sure I'd tightened them and couldn't figure out how I screwed up on both sides, then it hit me. The heat of using the brakes had turned the paint to goo, which oozed out from between the calipers and mounting pads, making the bolts loose. Yes, had I masked off the mounting points, that woudn't have happened, but it proves the point about unintended consequences of high brake heat.
Your proposed idea is pretty much the worst possible application for a 3D-generated part. High pressure, under high temperature, a thermoplastic, and dire consequences of failure. As other said, don't do it, stick with aluminum. And to be clear, it's very smart of you to have asked first!
I made wheel centering rings in my printer, which I assumed would melt, but they never did. I probably don't drive hard enough to melt them.
bluej said:
you're a bit behind the times in terms of 3d printing capabilities. I just bought a machine w/ a 350mm x 350mm x 400mm build volume for a bit over $500.
You also assume you have to print the entire thing in one go. if all you're doing is creating essentially a drill guide for where to place holes, etc, it can be multiple pieces that are intelligently designed to lock together. also, of course you'd need to check for accuracy, but if your machine is consistent, you can adjust the printing process to compensate.
That's really good to know! Or bad to know, I guess.
I'd want to get the holes positioned +- .001" for accuracy. The bolt holes can be fudged but the dowel locations are the critical ones. The transmission needs to be concentric to the engine within about .002" and as parallel as you can get. Parallel is fairly simple, at least.
speaking of adapters , does anyone have the print file for these bolt pattern gauges ?
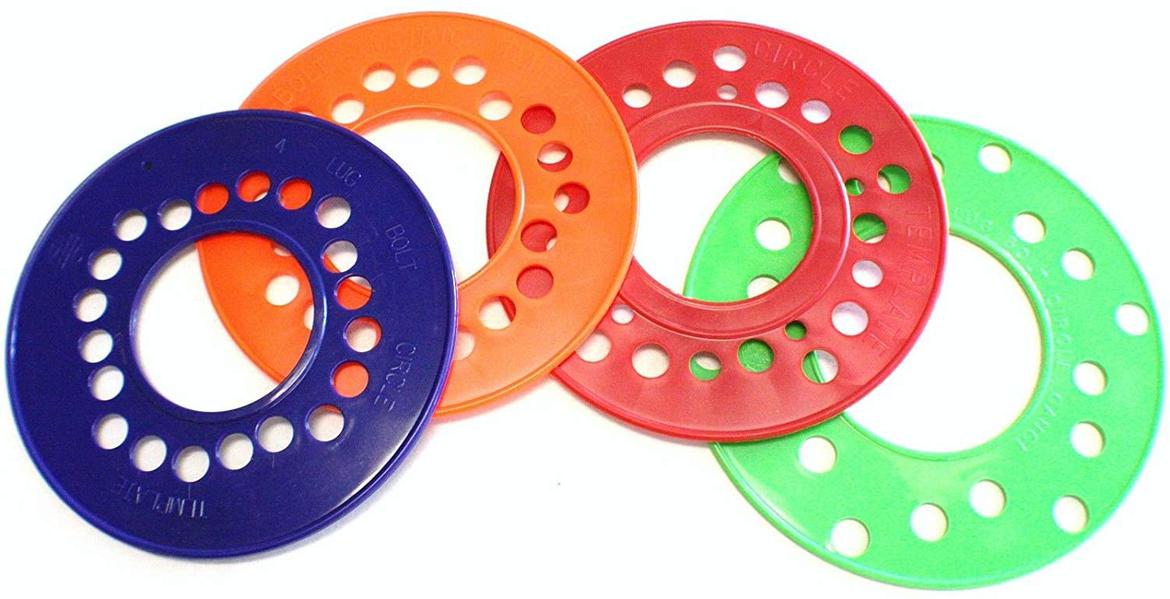
californiamilleghia said:
speaking of adapters , does anyone have the print file for these bolt pattern gauges ?
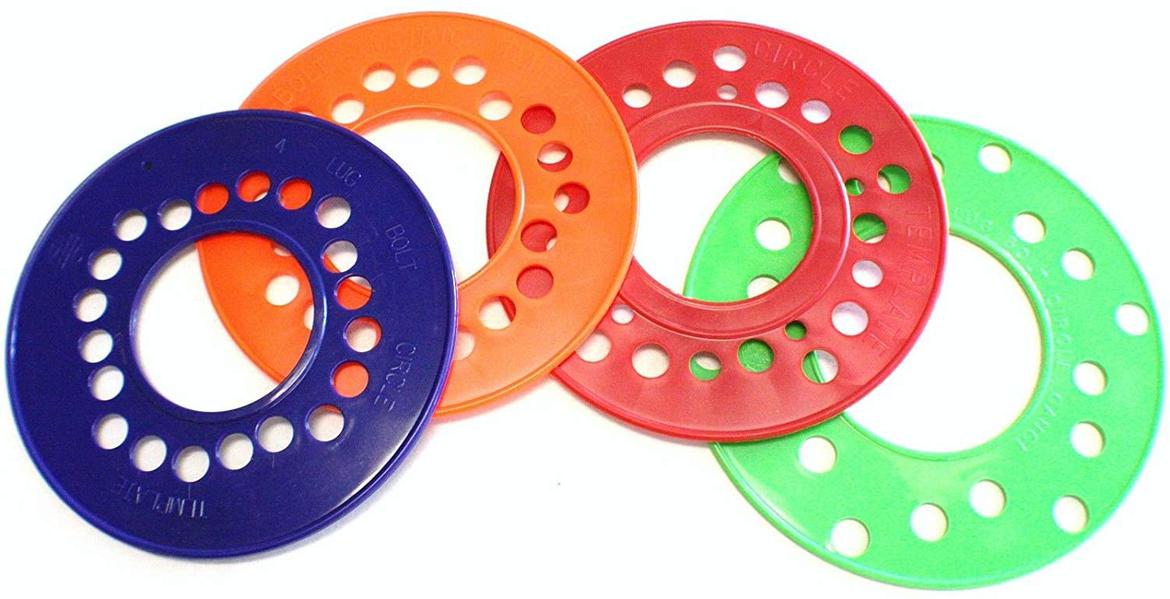
Which patterns do you want, and what size clearance holes? I'll make one for you.
In reply to JamesMcD :
thanks I will send you a PM
DrBoost
MegaDork
12/14/19 3:36 p.m.
bluej said:
Knurled. said:
bluej said:
Knurled. said:
ProDarwin said:
If you want to print a template, print one that has oversize holes you can press a steel bushing into (because a drill bit will quickly enlarge any plastic bore), with an I.D. only large enough for a pilot hole. Use the template to get all your pilot holes dead nuts on then just come back and open them up.
This is a great use of a 3d printer. I do stuff like that often at work.
BRILLIANT!
I was thinking about doing similar to make engine-bellhousing adapters.
You'd need something with a huge table to do that.
Maybe I'm OTB. In my mind when I think of 3D printing things at home, it's stuff under 3-4 inches square. A bellhousing adaptor, even a drill guide, would require a table at least 24x24 inches.
I also can't see doing it in plastic and reinforcing it without a lot of fettling. Hell, bits made out of cast or weldment need fettling, to get within tolerance. That's why offset dowels exist, just to make OEM mass produced (read: fairly precise) product correct.
you're a bit behind the times in terms of 3d printing capabilities. I just bought a machine w/ a 350mm x 350mm x 400mm build volume for a bit over $500.
You also assume you have to print the entire thing in one go. if all you're doing is creating essentially a drill guide for where to place holes, etc, it can be multiple pieces that are intelligently designed to lock together. also, of course you'd need to check for accuracy, but if your machine is consistent, you can adjust the printing process to compensate.
My first printer, 6 years ago had a 12" x 12" x 12" print volume.
californiamilleghia said:
In reply to JamesMcD :
thanks I will send you a PM
I drew up a disc with the patterns you requested. I'm linking to the .STL below, in case anyone else would like to print one.

This is supposed to be a link to an .STL file.
In reply to JamesMcD :
Thanks , now I need to get it printed......