Linky
Okay, so that link is for an SLA front-end setup for a fox-chassis Mustang. They offer it in both a "normal" vertical strut-style, and a cantilever spring style.
I'm trying to figure out what, if any, advantage there would be for the cantilever setup over the vertical spring version, or the similar front ends offered by Griggs and Agent 47.
The claims are that it reduces unsprung mass, but I don't really understand how that would be, as you're adding more mass "underneath" the spring. My thought is it's also going to decrease responsiveness, as you're going from the LCA directly acting on the spring/strut, to having it go through an intermediary.
I can see it lowering COG and maybe moving it rearward, but only over their own vertical spring version, as that unit appears to be heavier than the analogous offerings listed above.
So... thoughts?
Thats a Pushrod/pullrod suspension. The main benefits are the ability to use a smaller, lighter shock assembly to get more travel out of it..
edit, http://www.f1technical.net/articles/39 <-- thats not a bad article.
It also allows the use of linkage ratios to achieve different goals, same way that motorcycles use 'rising rate' linkage. Cool GIF showing how that works:

The downside I see is a lot of complexity and I don't think I care for that long main 'strut' being in compression rather than tension. If anything bottomed hard metal to metal that sucker would bend...
I Think you'd have a hard time buckling that pushrod. It's really very short, and quite large diameter, it looks to be 1" + round. My guess it's it's solid aluminum drilled and tapped at both ends. Buckling resistance increases with the cube of diameter and is inversely effected by the length of the beam. Also due to the use of rod ends the pushrod is loaded in ideal axial load. I'd really be more concerned with shearing the bellcrank pivots, or the shock mount in a heavy hit rather than bending the pushrod.
If that suspension has any level of travel its' going to have fairly crazy camber curves and a very migratory roll center. that upper A-arm seems to be ~4" long, with the bottom closer to 12. That's a pretty aggressive Short long arm arrangement.
I don't get the current trend to award design praise to things made out of billet aluminum. It's not really the best way to make large structures. Small parts yes, but on large things it's just bling Yo!
Agreed Nocones - everybody wants to show off their machining capability even if its not needed in the particular application. Welded tubular steel would likely be stronger without sacrificing much weight. However, steel would be more prone to flex and also plain old rust. Those parts could be cast out of aluminum rather than CNC'd for a fraction of the cost, but at a loss of bling as well
4cylndrfury wrote:
Those parts could be cast out of aluminum rather than CNC'd for a fraction of the cost, but at a loss of bling as well
Well, if they actually want to sell those things, this is something they should probably look in to. I can't imagine there are many people out there willing to drop ten grand on a unit like this, especially when you can get similar, race-proven units from known manufacturers for less than half the price.
I do a little metal casting as a hobby, and I can say that I could cast out at least 75% of the individual components of that set up if I had a machined piece to start out with, for probably a total of $100 if that. Unless the geometry is proprietary, theres nothing stopping someone from building a similar setup through sand casting, and marketing that. I just personally dont have the skills to build the original from which to cast it.
Heres the idea...
Make a mold with a special mold making sand - acts kinda like clay:
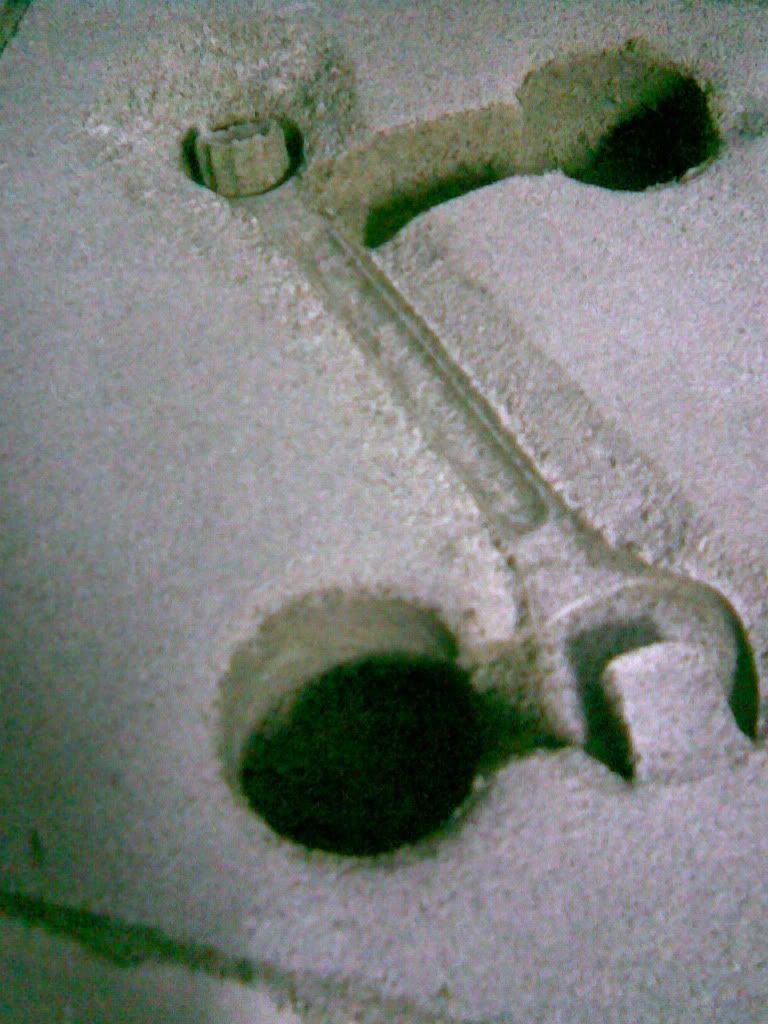
Then melt ya some aluminum (in this case an alloy with Aluminum, Zinc and Copper may be better - higher tensile strength than most off the shelf aluminums, cannot really corrode, and is lighter than steel or iron), pour it in, machine off the parting line, and voila:
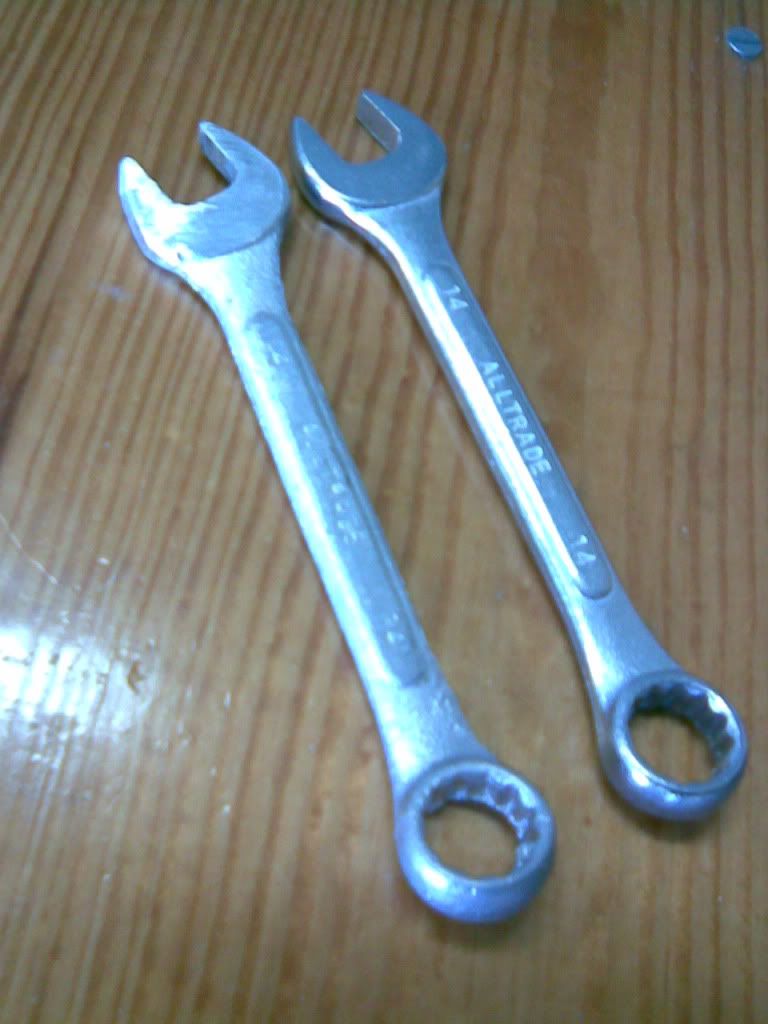
The one on the left is my casting - i know its just a wrench, but it incorporates some tricky casting techniques - casting a compound curve, interior spaces and a void requiring a core (the box end) - not much different than casting the sub components of the rack in the link. If I can do this for pennies in my backyard, i can only imagine what a real foundry could produce - in large qtys - for a fraction of having it machined
Nashco
SuperDork
3/15/10 2:55 p.m.
DIY cast suspension parts? I'm not the lawyerin' type, but that sure sounds like one casting void away from a huge lawsuit. Getting parts cast is actually pretty cheap if you have some reasonable volume (ie. quantities of hundreds or thousands instead of a dozen)...the problem is that so many people are concerned they're going to make 200 kits to sell at $1000 each ($200,000 investment) and not sell it. It's a lot easier to make 2 kits to sell at $6,000 ($12,000 investment) and not sell it. If you are going to make $20,000 selling 200 kits or $8,000 selling 2 kits, this economy tends to favor the less risky and less profitable path.
Bryce
Fair enough Bryce, casting errors do happen, and a relatively high stress part like that would be alikely candidate for failure if an inclusion or void happened. But that billet the part was machined from is just as likely to have inclusions in it too. Im just sayin
...well the metal caster part of me has to stand up for itself sometimes...the car guy part almost always wins, and thats not fair
if you are going to cast those parts.. I would at least go with spin or pressure casting.. forging would be best!
Shaun
Reader
3/15/10 3:44 p.m.
It looks to me like the suspension in the OP's post has a 1 to 1 ratio. That eliminates allot of potential design motives. Reduces un sprung weight? Hmmmmm. The linkage and the coil over still are accelerating and decelerating in this set up with the whole linkage being unnecessary mass compared to a conventional mounting of the coil over damper assy. If the assy was conventionally mounted do the spring and the damper count as part of the un sprung weight anyway? I would venture a guess that some portion of the weight is sprung as it is working and is hard mounted to the chassis so is partially supported. The advantages seem to dissolve. So I say it is bling. At a 1 to 1 ratio, with the addition of a bunch of wear and deflection points and the associated partially sprung mass eating back into any gains made with isolating the weight of the damper cartridge and spring it looks like is blingity bling to ensnare the wealthy hobbyist Larry Ellison types.