oldtin
Reader
4/8/10 12:04 a.m.
Kinda have a wacky idea of actuating a clutch master cylinder by a trigger. Not sure what parts to make this work or a source. Also check some basic assumptions.
Current pedal pressure is around 20-25# - pedal is about a 6:1 ratio - so I'm thinking around 150# of push to the master cylinder with about a 1.5" max stroke. Master to slave gives an extra 25% and the clutch fork gives about a 2:1 ratio - so about 375# of force releasing the clutch. What kind of actuator could work to push/release the clutch master? Trigger could be sort of like a video game trigger - basically a linear rheostat. Any ideas on making this work???
You don't want to use a robot for a few reasons. For one thing, it's a very expensive way to do what you want, there's also the complexity of it all (mounting controllers, actuators voltage convertors/conditioners). I'd be looking at a solenoid for the easiest solution besides.......your left foot. I mean with a solenoid or a spyder monkey you'll not be able to feel what's going on with the pedal. Why don't you want to use your leg?
Anything is possible. I agree though, what you're trying to do exactly is an important part of choosing the right hardware.
Here you go... electrically controlled valve + hydraulic throw-out bearing.
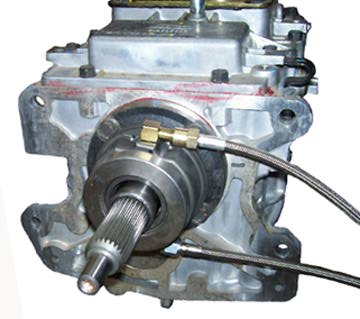
oldtin
Reader
4/8/10 8:49 a.m.
DrBoost wrote:
Why don't you want to use your leg?
Would love to - amputee (rt) - I can drive a stick no prob - but need a better solution for competitive speeds. If I switch to left sided throttle I have gas and brakes in a decent position - move clutch to trigger on gear lever and voila. Turns out you actually dont' feel as much as you think through your feet. It's as much your built-in motion sensor in your head as anything. Was looking for a grm approach to this.
Don49
New Reader
4/8/10 11:10 a.m.
Try looking at the set up on the old VW autosticks. They basically used a solenoid on the shifter and a vacuum diaphragm to actuate the clutch fork. I looked at doing this for a friend who is a paraplegic. The only touchy area appears to be starting from a standstill.
Yeah, the old autostick setup should do what you want. Actuator switch, a vacuum solenoid, a vacuum servo (maybe use an old brake booster?) associated hose and wiring and there ya go. Wire it so the solenoid will only allow vacuum when power is applied (in other words, normally closed). Only drawback is the servo will take up a good bit of room. Maybe mount it below the pedal in a 'pull' instead of 'push' setup?
Come to think of it, you could put something like a motorcycle clutch lever on the shifter and have it go to a variable manual vacuum switch. That way you could slip the clutch as needed, the way dirt bikers do. Do it this way: lever released = no vacuum, the clutch is engaged. Then the manual switch would vary the vacuum to the servo as the lever is pulled, thus engaging the clutch slowly instead of all at once.
Why have people started to call almost any machine a robot?
I'd blame Myth Buster, where apparently anything Grant builds is automatically a 'robot', but I know people were doing it even earlier when they started calling radio controlled cars with weapons robots too.
oldtin
Reader
4/8/10 1:08 p.m.
I blame encyclopedia brittanica
robotics:
Design, construction, and use of machines (robots) to perform tasks done traditionally by human beings.
Feel free to call it animatronics, motion control, remote actuation, linear actuation, rotary actuation, hydraulic, vacuum or any variation thereof. Got any ideas for me?
These aren't exactly cheap, but will move 25# @ 2" per second or 115# at .5" per second. One of these and a servo driver would give you proportional travel and would move as fast or as slow as your lever. That would make starts a lot easier.
http://www.servocity.com/html/heavy_duty_linear_servo__25__l.html
They also have the servo drivers.
Edited for clarity.
Hal
HalfDork
4/8/10 3:24 p.m.
Jensenman wrote: Come to think of it, you could put something like a motorcycle clutch lever on the shifter and have it go to a variable manual vacuum switch.
Why not just use a motorcycle brake lever and MC assembly. Might be tricky to get the proper size, but it would eliminate all the funky electronics, etc. Just plain old hydraulic all the way.
Nashco
SuperDork
4/8/10 4:22 p.m.
Didn't we do this before?
http://grassrootsmotorsports.com/forum/grm/duck-clutch-grm-style/18583/page1/
You keep wanting to do electrical, and that is NOT the cheap way to do this as it requires relatively smart controllers and expensive actuators if you have any expectations of clutch control beyond engaged or disengaged. If you do the controlling and actuating with the free human on board, you can drastically reduce complexity.
Bryce
oldtin
Reader
4/8/10 5:23 p.m.
^
I guess I come back to the electricals - basically the car currently has a lever and hydraulics and still needs 25ish# of force (doesn't sound like much, but it's a lot of finger strength - esp in traffic). Getting the lever down to hand size ends up increasing the force needed to operate it or alternatively, increasing the stroke length or some other gain or assist in mechanical leverage is needed. Everything has it's compromises - hydraulics/valves also need pressure pumps for the leverage gain - or actuators - whether vacuum or electric, etc. Small lever works on a bike using a multidisk setup and smaller forces involved. Multidisk for a car could work - but no doubt would be adding expense too. Anyway, trying to get an idea of the possibilities and alternatives now that it's warm enough to start tackling it.
Compared to the $4000 for the only commercially available duck clutch - pretty much all of the ideas so far sound pretty reasonable.
Nashco
SuperDork
4/8/10 5:52 p.m.
So, if 25 pounds of force is too much and you're full hydraulic now, add a vacuum diaphragm (brake booster) between the lever and the slave cylinder and you'll get good feel with significantly reduced lever effort and without changing throw. You can find a wide variety of vacuum diaphragms on 99% of cars in the junkyard for a few bucks. Use the proper combination of mechanical and hydraulic elements, you can package the diaphragm just about anywhere on the car with very little weight added (<10 pounds). There are vacuum diaphragms on older cars that were in line with the brake plumbing (independent of the master cylinder/pushrod assembly, which was identical for the same model with manual and power brakes) specifically accomplishing the same task you want to. The difference was them using it for a foot operated brake pedal instead of a hand operated clutch lever, but the system schematic would be identical, just slightly different execution for the end-user lever.
Simple. Cheap. Way easier than doing it with electronics. What's not to love about the vacuum diaphragm?
Bryce
4eyes
Reader
4/8/10 6:28 p.m.
I was thinking air/hydraulic.
oldtin
Reader
4/8/10 6:34 p.m.
I'm liking the vacuum approach. Thanks. Also cheap enough to give it go without giving it a second thought