So I've got an intake manifold which would work great... if the throttle body came out of it literally anywhere else, since it currently wants to go through the windshield on the car I'm inappropriately stuffing the engine into. I can't help but notice that it'd be perfectly fine if I did this:
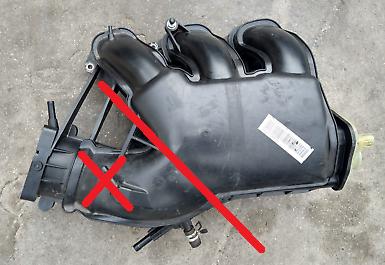
As far as I can google, nobody has done this, probably for good reason, but if anyone has I feel like they'd be here. In theory I could 3d print or fiberglass up some stuff and bond it to my hacked up manifold to get things where I want. Yeah, I could print an entire manifold too, but that's pretty expensive.
Thoughts? Experiences?
I have an intake tube that is slightly off angle that I've been considering cutting and plastic welding back together. It's no where near the stresses of a manifold but I'm interested in hearing about people's thoughts on plastic-ology of it...
i've never done it, but i can't see why it wouldn't work...i assume it's a dry manifold so as long as you can get the joint to be air-tight (which i'm sure could be done with JB weld) you won't have any issues. You might leave a few HP on the table if your joint wasn't super smooth inside, but i'd bed that would be minimal as long as your craftsmanship is halfway decent (and from what i've seen on your other posts, it would be).
I say do it. slice/dice/glue back together and profit
Trent
UltimaDork
10/9/24 12:16 p.m.
Does the intake have a marking anywhere on it that would decode the particular plastic material it is made of?
I too am interested in this but have discounted it not knowing if a solvent or heat welded glass fiber reinforced plastic would hold up to boost pressures.
Mr_Asa
MegaDork
10/9/24 12:24 p.m.
I know that Stampie or Michael did some plastic smoothing of an intake for Darth Nader. Might be a starting point?
I wonder if stir welding would be an option here.
I would lean more towards fabing up an aluminum one, but certainly am interested in seeing where this goes.
Not on an intake but hot staples and adhesives were the name of the game for prototyping lawn mower decks. SLS printed glass filled nylon hot staples nicely to a precision sawzalled polypropylene lawnmower deck. For an intake I'd probably seal with JB Weld or laminate fiberglass on it.

Probably doable.
IIRC the first step would be finding out what type of plastic it is-I think different material types can be "welded" in different ways.
Any markings to indicate what the material is? PTFE, etc.
My thought would be messing up the air distribution inside the manifold to the individual cylinders.
I believe it's PA6-GF30, a glass filled nylon.
I am looking at doing something similar with a 2GR. I want it to come out the middle of the plenum going rearward and am looking at making one out of carbon fiber.
It's actually really easy, you just throw the hole thing out and replace it with individual throttle bodies!
If only this wasn't 2 grand...
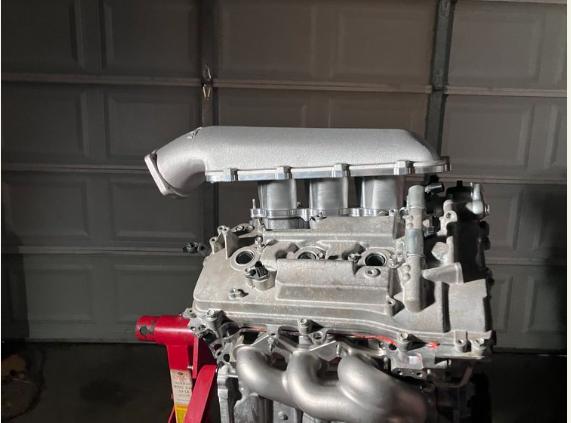
Perhaps you could machine or print a spacer that lets you bolt the stock manifold on rotated 180? The arrangement of the lower plenum holes looks like it would be rotationally symmetrical about the vertical axis by 180 degrees...
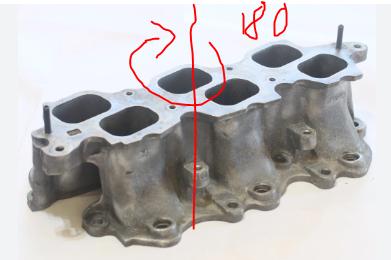
In reply to maschinenbau :
Good idea. Fiberglass reinforced nylon is a printable material, and there's an even higher temperature plastic called Ultem, but since the stock manifold is FG-reinforced nylon that should work fine. CF-reinforced nylon should have the same temperature resistance and is also printable.
If the plenum holes are truly symmetric, and if that packaging clears the hood, this could easily be a sendcutsend part with tapped and countersunk holes. Even if the ports don't quite match up, you could port match with a die grinder. Basically same thing I did with the ITB's on the Rice Rod:
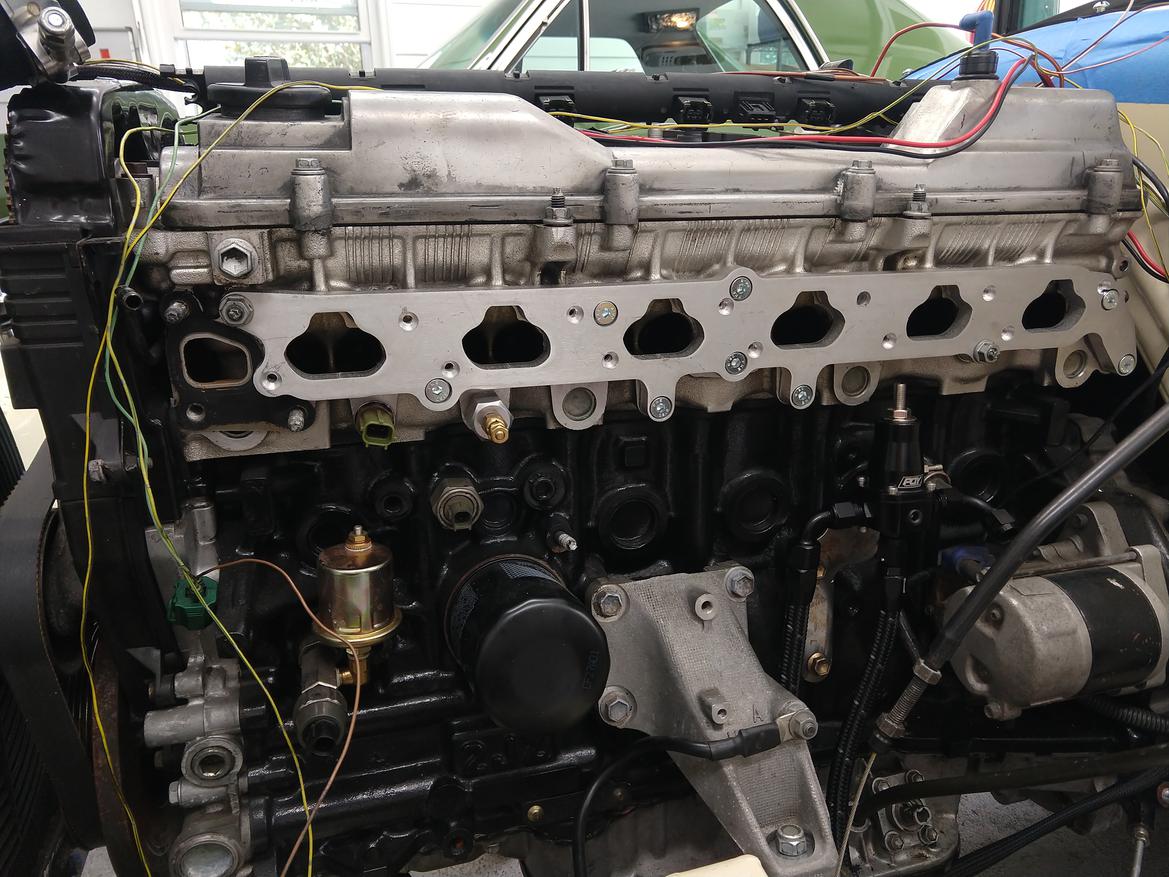
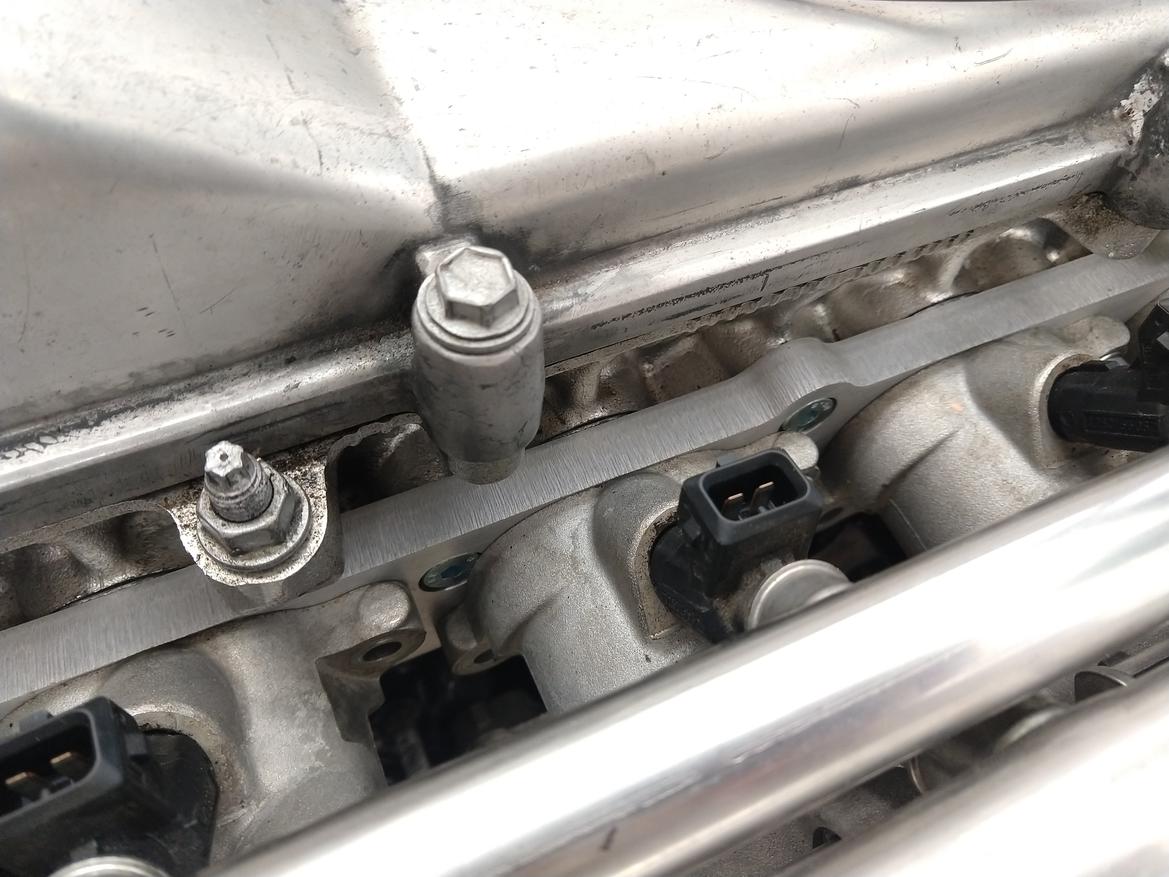
maschinenbau said:
If only this wasn't 2 grand...
It also wants to share space with my windshield and is very tall.
I looked hard at rotating the stock manifold 180, there's a LOT of stuff on the valve cover it interferes with.
Is there another similar plenum that could be bolted on? Or was the same engine used in a different platform that maybe had the throttle body located differently?
I know a Windstar 3.8 plenum was a swap Mustang 3.8 owners would do for relocating throttle body.
How valuable is the stock manifold? If it isn't any good to you in its current form, cut it and start looking at how it's made. Having seen your fabrication skills I am sure you can do this. Sometimes the first cut is hard to do because we want a full plan ahead of time. Once you start working things often become much clearer. One thought I had is that a metal sleeve that is a tight fit in the end of the cut off section the throttle body attached to could be then placed into a hole cut where you want the new location to be. I think you got this! Get started.
DjGreggieP said:
Is there another similar plenum that could be bolted on? Or was the same engine used in a different platform that maybe had the throttle body located differently?
I know a Windstar 3.8 plenum was a swap Mustang 3.8 owners would do for relocating throttle body.
I've searched and searched and it appears there are only a few, very similar, variants. The direct injected versions have different port shapes so those are out, and the larger V6 in the 4runner/tacoma looks similar but is huge.
madmrak351 said:
How valuable is the stock manifold? If it isn't any good to you in its current form, cut it and start looking at how it's made. Having seen your fabrication skills I am sure you can do this. Sometimes the first cut is hard to do because we want a full plan ahead of time. Once you start working things often become much clearer. One thought I had is that a metal sleeve that is a tight fit in the end of the cut off section the throttle body attached to could be then placed into a hole cut where you want the new location to be. I think you got this! Get started.
I do have one I've already lopped at the approximate location shown, I may continue to cut since I have another untouched one sitting here as well.
¯\_(ツ)_/¯ said:
I looked hard at rotating the stock manifold 180, there's a LOT of stuff on the valve cover it interferes with.
How much spacer would it need until it clears the valve cover? Does hood clearance become an issue then?
In reply to maschinenbau :
It's through the hood in that direction by inches no matter what, really just not viable unfortunately.
If it is PA6-GF30, that is a 3D printable material, maybe with a little less glass fiber content (15-25%). If you wanted to CAD up the "right" shape it could be made by one of the commercial 3D printing outfits, or someone here may have a machine with the envelope size and power capability to create it.
In reply to stafford1500 :
I have quoted complete manifolds and they're prohibitively expensive- I'm currently working up a partially printed, partially purchased solution kind of like what those alfa v6s with the shiny intake runners use.
Some (in my opinion, insane) LS swap people smooth/cut/patch the stock truck intake manifold, which is also plastic. I know some even run boost through them, so I'd say your plan would work in theory.
LS Truck Intake Shave Plastic Welding VIDEO "How To" - LS1TECH - Camaro and Firebird Forum Discussion