And how hard was it?
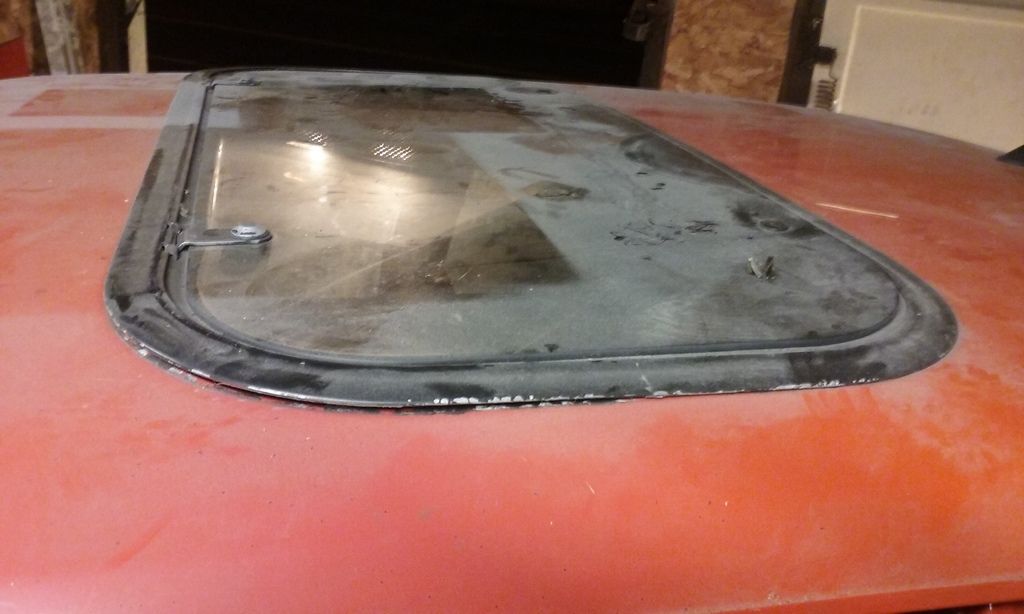
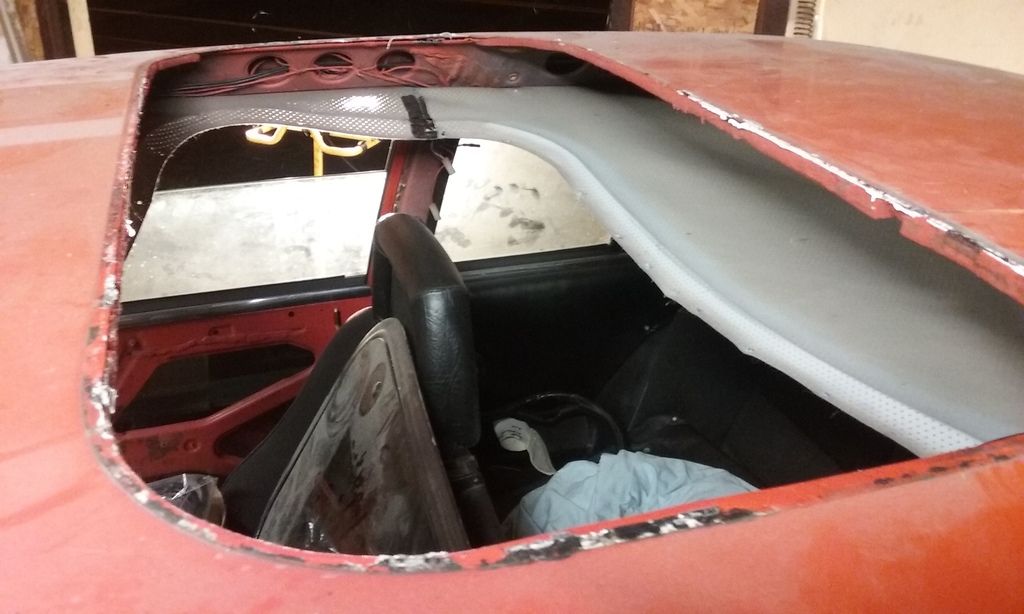
I have a line on a roof that a friend wouldnt mind cutting up on my behalf, but if I go through with something like this I'd really like it to look like it was never there.
Anyone here ever attempt such a thing before? Advice?
Thanks!
-Bill
Easy enough to get a pattern on the size and shape. Add some bracing to the underside and use magnets to keep it flush while welding.
Is there much shape to that section of the roof? The front appears to have more shape while the rear looks more flat.
Left-to-right arch looks subtle and easy enough to match using a barrel-shaped object to shape it.
This is reverent to my interest. We plan on doing the same to the Challenge car for next year.
If you have access to a shrinker/stretcher, turn a flange down on the fill panel. Then use the shrinker/stretcher to get the shape just right and it will hold its shape better during the welding. Otherwise use magnets on the top side to hold it flush as mentioned above.
If it's a common vehicle, go to the pick and pull, cut the roof out of a hard top car, fill the hole.
Make a templet then go to the junkyard and find similar car and cut out what you need (bigger of course than the templet) bring home and trim to fit and weld in pace. Done this several times filling in sun roofs in race cars.
Welding a big flat piece like that will be difficult to do without a lot of warpage. I think you may be better off replacing the entire roof section if you can get it, there's more structural rigidity at the pillars.
ebonyandivory wrote:
Easy enough to get a pattern on the size and shape. Add some bracing to the underside and use magnets to keep it flush while welding.
Is there much shape to that section of the roof?
Left-to-right arch looks subtle and easy enough to match using a barrel-shaped object to shape it.
It's 3-dimensional but "slight" like you said. I can try to get some sort of measurements tomorrow morning for something to go by.
I was thinking I'd match the chopped section to the roof the best I could and cut out a filler panel from there. I'd thought about using some magnets I saw in the eastwood catalog to hold it in place, but hadn't thought about bracing...
Just FYI, this would be my first time attempting such a thing but I do have a TIG that's just dying to be used...
I seem to remember noticing that most of the Spec E30s at the track last time were former sunroof cars with patches over them.
Woops, more replies while I made that last post:
No access to a shrinker/stretcher
No chance of a pick-n-pull find (Alfa GTV6) New panel would be coming from a donor car in Vermont.
Pillars might be an option, but man I'm scared to cut it that far...
In reply to dean1484:
How was the finish after paint? Could you tell it had been patched?
I've seen it done poorly more times than I've seen it done well.
I'd get the donor panel, lay it on top, trace, cut the hole smaller by whatever distance your flanging tool is, flange, drill holes in the panel, spot weld, probably finish weld in small sections if you can control the heat, grind, filler, paint, done!
If it was a car I cared about preserving the original structure I would add a patch piece, but it will be almost impossible to get it to look "right" and will always be an issue down the road. Look up the Centurion Bronco conversions for details on roof mods done wrong.
I would be so much more tempted to cut at the pillars if I wanted it looking like it was never there.
Pull the interior and glass, weld in some braces, measure it up, cut the roof, trim the new roof, tack, measure, finish weld, etc.
You can also toss the heavy glass, tig weld a piece of aluminum to the sunroof frame, and put it back in. Won't weigh much more than the steel panel plus weld and body filler.
mazdeuce wrote:
I've seen it done poorly more times than I've seen it done well.
That's what I was worried about... Being a first timer I'm betting it comes out about half as good as I'd like it to 
93gsxturbo wrote:
I would be so much more tempted to cut at the pillars if I wanted it looking like it was never there.
Man, I don't know if it's just me, but cutting the pillars has me scared to death
oldopelguy wrote:
You can also toss the heavy glass, tig weld a piece of aluminum to the sunroof frame, and put it back in. Won't weigh much more than the steel panel plus weld and body filler.
Nah, I'd be doing it more for aesthetics so if the hole cant be filled then the glass'll probably stay 
Why not leave the sunroof?!
java230 wrote:
Why not leave the sunroof?!
Originally:
it's ugly, looks cheap, it's heavy, and is just a potential leak path.
Now:
That's what'll probably happen 
if anything beyond just putting a panel in scares you, the simple solution is to do the body work with the hole in place and then put the glass back in. As you get more comfortable with the fabrication, you can build a steel panel to replace the glass. That would be the least invasive and quickest way to go without starting a sub project on a sub project... Get the car up and running and then the smaller stuff is less headache (says the guy who is 16 years into a single car project).
This is a non factory sunroof, right? I see why that would bug you. Maybe leave it for last and then see how you feel? Still makes sense to source the panel if you can, there can't be a ton of them just sitting around.
RedGT
HalfDork
10/7/16 3:54 p.m.
In reply to mazdeuce:
Correct. There were factory sunroofs. That ain't one.
They proper way to swap a full roof panel is to find where roof attaches to the pillars and grind or melt away the filler until you expose the spot welds. Separate the panels there, weld the new one in and then fill the gap.
It's also worth noting that there is structural epoxy that has been approved for use in replacing roof panels without welding. Street Rodder magazine did an article on the stuff 10+ years ago, so it's been around for a while.
Pieces of 1/4 square stock (~width of the panel) could be cut and laid on the roof in front of the hole and formed (bent) to match the curvature of the roof and then used for a brace. Same for the rear of the panel. Then two more shorter ones running front-to-back to complete the rigidifying (I made that word up just now).
If it were my car I'd find an entire donor roof panel. On most cars the roof panel is a skin that is spot welded in the glass channels. To fix it right you have to pull all the glass and drill out the spot welds. Most of the time the A and B pillars have a hidden seam somewhere that may be leaded. Burn out the lead to reach the spot welds underneath. It'll take a bit of time to and fiddling fit the new roof skin back and place. Plug welding the spot welds isn't really all that difficult once you have the machine settings right. As much trouble as it is I'd much rather re-skin the roof that try to patch that hole. It'll never look right. Unless this is a track only car that you don't car about. If that's the case then just pop rivet an aluminum panel in place and seal with silicone.
Hungary Bill wrote:
In reply to dean1484:
How was the finish after paint? Could you tell it had been patched?
Acceptable. When welding move around alot and take your time letting thins cool. Grinder the a DA and a very small amount of filler puddy and then high build primer and it was fine for paint. It was not show quality but good. The key is take your time especially with the welding. Hold it in place with welding magnetts and heat syncs along where you are welding can help but your best friend is time between welds and just taking a break for coffe or a soda. Hell I would weld a bit and then go do something else for ten or fifteen minutes. It is when you only have a couple inches of welding left and you know you should stop and let it cool but you don't and then you warp it. Been there done that.