My lexus has 114.3 wheel lug pattern. I'd like to use a set of factory bmw wheels with 112 wheel lug pattern. If I run wheel adapters am I going to have issues with them coming loose or breaking? What wheel adapter's would be best for my application, thanks.
Yes, they are safe, but they're kind of a hassle. Here's what I always do with mine:
- Torque adapter onto hub (same torque spec you would use for a wheel), torque wheel onto adapter
- Drive car
- Remove wheel, re-torque adapter, reinstall wheel
- Drive car
- Re-torque wheel
- Enjoy
Another thing to keep in mind is that if the adapter is thin, and/or your wheels don't have clearance on the hub flange, you'll have to trim your lug studs. Not the end of the world, but going back to stock means installing all new studs.
As long as they're hub centric they're usually ok. The ones without a centering ring that just use the studs to line them up are kinda sketchy.
obsolete said:
Yes, they are safe, but they're kind of a hassle. Here's what I always do with mine:
- Torque adapter onto hub (same torque spec you would use for a wheel), torque wheel onto adapter
- Drive car
- Remove wheel, re-torque adapter, reinstall wheel
- Drive car
- Re-torque wheel
- Enjoy
Another thing to keep in mind is that if the adapter is thin, and/or your wheels don't have clearance on the hub flange, you'll have to trim your lug studs. Not the end of the world, but going back to stock means installing all new studs.
I do the same with the adapters / spacers I have on the Jeep. In general, because of the torque annoyance, I only remove them when I really have to. Otherwise they just get a torque check while I'm in there.
I've had a set of 2" lugcentric bolt on spacer/adapters on my trans am for over a decade. No issues in at least 100k. Even after wrecking it twice. They're not the best way to get wheels on a car but they're not the worst either.
My giant 11k LB RV uses factory hub adapters. It's a Chevrolet Express 3500 and has adapters to make the reverse offset heavy duty wheels work.
Properly installed and made of quality components there is no issue with them.
Obsolete's install method is great.
Saron81 said:
As long as they're hub centric they're usually ok. The ones without a centering ring that just use the studs to line them up are kinda sketchy.
Never had a problem with non hubcentric models.
Anything with tapered lug nuts is already lugcentric, so it d(aw hell here he goes again)
Pete. (l33t FS) said: Anything with tapered lug nuts is already lugcentric, so it d(aw hell here he goes again)
What about cases where the wheel is a tight fit onto the hub for centering, but it also uses tapered lug nuts?
cyow5
Reader
1/24/22 3:27 p.m.
rslifkin said:
Pete. (l33t FS) said: Anything with tapered lug nuts is already lugcentric, so it d(aw hell here he goes again)
What about cases where the wheel is a tight fit onto the hub for centering, but it also uses tapered lug nuts?
Then it is extra centered. Produces negative vibrations from too much centering.
rslifkin said:
I do the same with the adapters / spacers I have on the Jeep. In general, because of the torque annoyance, I only remove them when I really have to. Otherwise they just get a torque check while I'm in there.
Yeah, I just treat the ones I have like part of the hub at this point. Really no reason to remove them unless you're swapping between wheel bolt patterns/offsets frequently.
Pete. (l33t FS) said:
Never had a problem with non hubcentric models.
Anything with tapered lug nuts is already lugcentric, so it d(aw hell here he goes again)
Agreed, hub-centricity is a convenience feature, not a safety requirement.
rslifkin said:
Pete. (l33t FS) said: Anything with tapered lug nuts is already lugcentric, so it d(aw hell here he goes again)
What about cases where the wheel is a tight fit onto the hub for centering, but it also uses tapered lug nuts?
Unless the wheel is a press fit on the hub, it's the lug nuts that center it.
As long as you are not offsetting the tires original location, you are not violating any engineering.
The adapters are probably stronger than the wheel, and certainly stronger than a lot of FWD drive flanges..... 
114 to 112, I might just use wobbe bolts. Assuming you keep hub centricity.
Chris_V
UberDork
1/25/22 10:01 a.m.
fatallightning said:
114 to 112, I might just use wobbe bolts. Assuming you keep hub centricity.
yeah, with a hubcentric wheel or hub rings, that's well within the design spec of wobble lugs (1.15mm. The design spec is usually 2mm). I used them to put 114.3 wheels on a 115 mm bolt circle, but that's barely necessary and could possibly have used stock lug nuts in that case.
In reply to singledownloop :
Just so there aren't surprises down the road BMW is 5x120 not x112. Mercedes, some VW, some Audi are x112..
On subject they are perfectly safe, I've run them well over 200k miles on multiple vehicles
chandler said:
In reply to singledownloop :
Just so there aren't surprises down the road BMW is 5x120 not x112. Mercedes, some VW, some Audi are x112..
On subject they are perfectly safe, I've run them well over 200k miles on multiple vehicles
Not the new stuff. My mother's 2020 x3 is 5x112. It is currently on audi q5 wheels as winter rubber. Which is a pain in the ass because of bmw's 14x1.25 conical lug bolts vs audi's ball seat style. There are too many differing wheel attachment options...
iansane said:
chandler said:
In reply to singledownloop :
Just so there aren't surprises down the road BMW is 5x120 not x112. Mercedes, some VW, some Audi are x112..
On subject they are perfectly safe, I've run them well over 200k miles on multiple vehicles
Not the new stuff. My mother's 2020 x3 is 5x112. It is currently on audi q5 wheels as winter rubber. Which is a pain in the ass because of bmw's 14x1.25 conical lug bolts vs audi's ball seat style. There are too many differing wheel attachment options...
Yup, all of the newer "G" chassis BMWs are 5x112. Pretty much anything older and 5 lug is 5x120 (some older stuff was 4x100, etc.)
In reply to rslifkin :
Wheel adaptors (and wheels) are subject to major high frequency reversing loads, and so fatigue life is a major consideration.
With Steel, there is a fatigue failure stress threshold, under which fatigue life is nearly infinite.
Aluminum has no such threshold, and it will ALWAYS fail ... eventually.
(might be 1 year, 10 years, 100 years, 1,000 years ...)
That's why aluminum airframes are designed with a service lifetime.
That said, adaptors are usually highly overengineered and under stressed.
You don't see standard Aluminum wheels fatigue failing on street cars.
But lighter wheels used in racing should be periodically crack tested, just like any other safety critical item.
In reply to clshore :
Agreed, fatigue life is a concern. But for a well built adapter (as with most non-lightweight wheels in street use), the fatigue lifespan can be described as "a very long time".
In reply to clshore :
Any idea whether there's a significant difference between 6061 and 7075 in fatigue life? I paid a little extra for my last set of adapters to get the 7075 alloy, thinking that since they're only 15mm thick, I wanted the stronger option.
In reply to obsolete :
Stronger does not automatically mean better fatigue life.
Plus, the 6XXX and 7XXX alloys have different tempers that make a difference too.
Fatigue cracks often develop around stress risers, abrupt changes in cross section or load path.
For example, high strength bolts or axles will typically have reduced diameters and gradual transitions where smooth sections change to threaded or splined sections.
Crankshaft fillets between the bearing journal transition to the crank cheeks, larger ones yield better fatique life.
Identifying and mitigating stress risers early in the design is important.
In reply to clshore :
By some recollection, 7-series aluminum tends to crack before it deforms, which is exactly what I would not want in any critical components. True?
Back to original question, I'll have to look, but the aluminum hubs that some RX-7s used are a lot smaller in cross section than any wheel adaptor/spacer is, so I would not be terribly concerned. RX-7 front hub failure is not a known event. I can't see a wheel spacer failing unless it is made from precorroded peanut butter. I HAVE seen them loosen up, but any tapered lugnut needs to be retorqued after it is driven, and having to take the wheels off to retorque is kind of a pain...
cyow5
Reader
1/25/22 2:22 p.m.
Pete. (l33t FS) said:
In reply to clshore :
By some recollection, 7-series aluminum tends to crack before it deforms, which is exactly what I would not want in any critical components. True?
Not true. 7075-T6 yields at about half its failure strain meaning it can deform plenty before cracking. The high yield strength also means it can used more safely than 6061-T6 for many applicaitons. For reference, I usually go to MIL-HDBK-5J. It is a military spec that has since been surpassed but is still very good (and free). It has tons of charts like stress-strain but also temperature and cyclical loading effects. I love 7075-T6 as a structural material, but it certainly has its downsides - cost being a big one. For a wheel adapter though, there's probably no reason to spend the extra for it though over 6061-T6.
cyow5
Reader
1/25/22 2:26 p.m.
obsolete said:
In reply to clshore :
Any idea whether there's a significant difference between 6061 and 7075 in fatigue life? I paid a little extra for my last set of adapters to get the 7075 alloy, thinking that since they're only 15mm thick, I wanted the stronger option.
From MIL-HDBK-5J:
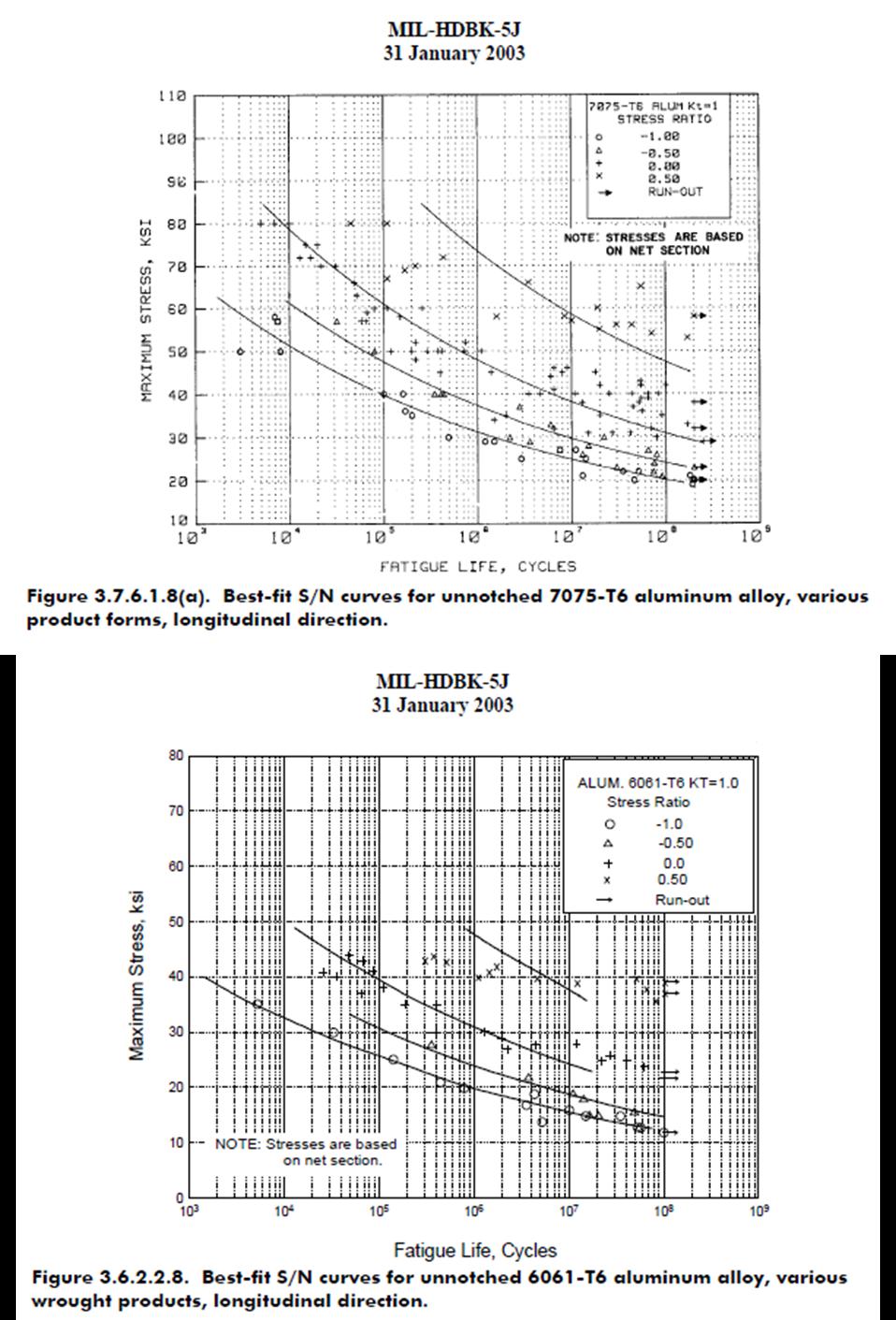
You'll want to look at the stress ratio = -1 points since a wheel space sees fully reversed stress loading.