I had to replace the aftermarket ball joint on Mrs Noddaz 92 Maxima (That had been replace 2 years ago...) and as I was finishing the job up I noticed that the cotter pin hole was basically lined up so when the cotter pin was installed the pin would almost go straight into the knuckle where it was almost not accessible to bend the end of the cotter pin over. But after a few minutes of tapping and twisting the pin is locked in place. Now the question. Does anyone bother to turn the ball joint shaft so the pin hole lines up better? Do you even notice such things? Or are you also laying on your side in the driveway trying to beat the oncoming rain and get the car finished?
Every time. It's a lesson I learned years ago by having to do what you did. Now I always install the ball joint into the control arm and stick a pick in there and rotate the spud until the hole is facing front and rear.
It takes a few seconds, but pays off handsomely when you can access the pin to dress it after torquing everything down.
Always.
Because I'm probably going to be the next guy who has to pull it apart, and cotter pins almost never come out in one piece so sometimes you need access to both sides. OTOH, it's my day job, and not only does pride in workmanship still count for something, but 5 seconds spent now can save 10 minutes a year or two down the road.
This is in stark contrast to how on every car where I have the hood open, I reposition all of the fluid fill caps so they are installed "lined up", locking lug nuts and the manufacturer's name on OWL tires are lined up with the valve stem, etc. That's just aesthetics.
Also note on greaseable ball joints and rod ends, you have to point the puke flap of the boot away from the brake rotor, or poke a hole in it afterwards. Otherwise you grease the front end and wonder why the car doesn't stop for E36 M3 anymore.
Knurled wrote:
Always.
Because I'm probably going to be the next guy who has to pull it apart, and cotter pins almost never come out in one piece so sometimes you need access to both sides. OTOH, it's my day job, and not only does pride in workmanship still count for something, but 5 seconds spent now can save 10 minutes a year or two down the road.
This is in stark contrast to how on every car where I have the hood open, I reposition all of the fluid fill caps so they are installed "lined up", locking lug nuts and the manufacturer's name on OWL tires are lined up with the valve stem, etc. That's just aesthetics.
you are supposed to line up a mark on the tire with the valve stem to minimize the amount of weight needed to balance it..
In the real world, it makes no difference since wheels aren't out of balance by themselves.
In reply to Knurled:
Thanks for reassuring me that even if I'm insane I'm not the only one. All my ball joint cotter pins have the round end face the front of the car and the steering ones all face either front to back or up and down.
And I thought I was anal.
There was a guy here in town who specialized in Model A's, mostly hot rods. On his cars, all the hexes on the bolts were in perfect alignment with the long axis of the car. First time this was pointed out to me, I could not conceive of the time it took to do that.
It doesn't take much time at all and after a while you almost do it unconsciously. I will admit that turning the screws on the switch plates at work so there is a vertical slot is probably a cry for help.
I am just happy people are actually putting cotter pins back!
I'm about the most anal retentive person you'll ever meet.
Example, I recently did a clutch job on my one ton dually work truck. In line with my "might as well" philosophy, I went ahead and freshened up the transmission. Along with my usual bearings and synchro work, I went ahead and powder coated the transmission and bell housing. All new grade 8 hardware too. Yes, that's two stage powdercoat, silver vein base and clear powder topcoat. I'm real sick with the details.



Again, this is an old work truck. This is in no way one of my project vehicles that I really fuss over details on.
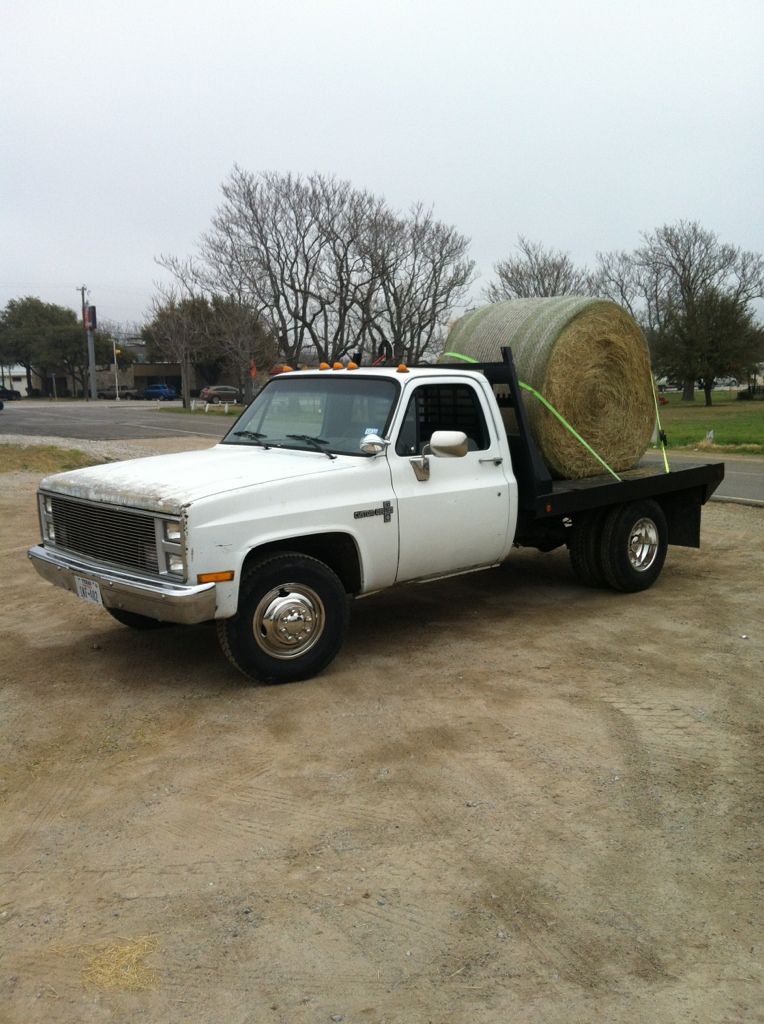
Curmudgeon wrote:
And I thought I was anal.
There was a guy here in town who specialized in Model A's, mostly hot rods. On his cars, all the hexes on the bolts were in perfect alignment with the long axis of the car. First time this was pointed out to me, I could not conceive of the time it took to do that.
The first time I heard of a person doing such a thing, it blew my mind that the car run just fine with every torque spec being wrong.
Wally wrote:
It doesn't take much time at all and after a while you almost do it unconsciously. I will admit that turning the screws on the switch plates at work so there is a vertical slot is probably a cry for help.
That's actually taught in electrician's textbooks.
Ian F
PowerDork
7/29/13 8:03 a.m.
Curmudgeon wrote:
And I thought I was anal.
There was a guy here in town who specialized in Model A's, mostly hot rods. On his cars, all the hexes on the bolts were in perfect alignment with the long axis of the car. First time this was pointed out to me, I could not conceive of the time it took to do that.
I don't think that's uncommon on hot rods. At a show many years ago I was looking at a Willy's coupe and all of the phillips screws (stainless steel, of course) attaching the trim panels in the trunk were in perfect alignment. The car looked flawless and had trophies to prove it.
I don't even use cotter pins anymore. I take things apart often so I just use hitch pin clips. You can use a locking style pin if hitch pin clips make you scared.
Knurled wrote:
In the real world, it makes no difference since wheels aren't out of balance by themselves.
acutally it does. the valve stem hole/stem is the reduced weight that hte tire joint is to be lined up with reducing balancing weight needed.
did a test one day, mounted the dot (seam of the tire) at 3* to the valve stem, and was out of balance by like 30grams. put it lined up with the valve stem, was only 5grams
patgizz wrote:
Knurled wrote:
This is in stark contrast to how on every car where I have the hood open, I reposition all of the fluid fill caps so they are installed "lined up", locking lug nuts and the manufacturer's name on OWL tires are lined up with the valve stem, etc. That's just aesthetics.
no, that's just OCD
and if you've got it real bad, it's CDO because you put the letters in alphabetical order.
I turn mine so they're not directly aimed at the knuckle, but I sometimes forget. If I forget what I usually do is put a flathead in between the wires of the cotter pin and then tap on the head. As I push it in, they usually flare out when they hit the knuckle (at which point I can get some needle-nose pliers on them and properly bend them.)
Of course, most of my stuff is GM and there is a pretty generous distance from the ball joint stud to the knuckle.
v8exocet wrote:
did a test one day, mounted the dot (seam of the tire) at 3* to the valve stem, and was out of balance by like 30grams. put it lined up with the valve stem, was only 5grams
I've seen more variation than that just from removing and remounting the wheel to the balancer.
Plus, the tire's just going to be out of balance after a couple thousand miles, anyway.
And not everyone puts a dot on the tire... or they put two or three on the tire... so what do they mean? IMO as long as the tread is round and square, it doesn't really matter. That's what the balance weights are for in the first place.