peter
Dork
5/24/15 2:23 p.m.
I'm looking to bend several 90 degree brackets in 1/8" steel and I'm looking to do it with some precision (see prior thread).
I know I could clamp the steel in a vice and bash it with a hammer, but I'm wondering if there's a simple way to get a better bend. I'm defining "better" as bend location accuracy, angle repeatability, and leg flatness. Is this just a matter of practice or are there tricks I need to know?
The widest piece I'd be bending is ~2" along the bend.
I'm assuming you're also looking to do it without a brake? Or without fabricating one? Or without welding angle iron to flat sheets?
Maybe make a jig to hold the part then bash it with a hammmer?
peter
Dork
5/24/15 2:39 p.m.
Keith Tanner wrote:
I'm assuming you're also looking to do it without a brake? Or without fabricating one? Or without welding angle iron to flat sheets?
Yes ... something I can do in a friend's garage with no metalworking tools other than a HF grinder/cut-off wheel and the aforementioned hammer and vice. Maybe a propane torch too (have to check).
I've always bent brackets with a mallet and a vise. Use thin hunks of wood if you want to protect the metal from jaw marks.
A sheetmetal brake is one of those things I'd really like to have but there's just no room. And they get much more expensive once you want to get past 16-gauge stock.
If you can deal with the reduced strength, use that cutoff wheel to score the inside of the bend half way thru the material. You get a nice tight bend exactly where you want it.
2" X 1/8" angle iron?
I've used it for seat brackets before. Web for added strength.
Do you have a shop press?
Build a press brake.
What kind of steel? Mild steels will bend, but something like 4340 is a bit more brittle.
What I usually do with flat stock is put it in a vise with a piece of rolled steel between it and the closest jaw. That generates a radius inside the bend (if your plans allow this).
peter
Dork
5/24/15 4:02 p.m.
This will be mild steel, thankfully.
I found these "vice brakes", which would seem to be just the ticket, if they could bend 1/8" steel.
This one from Lee Valley says it'll do 1/8", but it's on the smaller side and I'm not sure if it being cast is a good or bad thing.

Grizzly makes them in three sizes, but only claims up to 14ga steel (1/8" is appox 10ga). The Grizzly looks to be the superior product, can anyone think of a reason it wouldn't bend the thicker material the Lee Valley tool claims to work on?
What are the dimensions of thr bracket you are trying to make? I would start with square or rectangular tubing and cut the bracket out of that. You get the 90 degree bend baked in for you, so to speak 
Add heat and then bend. I have used my brazing torch to heat a line where I want it to bend. Smaller pieces of 1/4 inch plate can be bent with a hammer and a vice this way. Nat as accurate as a press brake but good enough for what I needed.
NOHOME
UltraDork
5/25/15 7:15 a.m.
Rather than flat steel, start with square or rectangular tube and cut/carve the bracket taking advantage of the included angle.
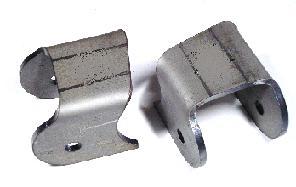
You can get quite creative:

When it is all said and done, it is hard to beat the cost, quality and time savings of just buying from these guys:
https://www.welderseries.com/blog/online-store/

In reply to NOHOME:
O.M.G. I have a new favorite website.
In reply to NOHOME:
Wow, cool stuff there. I'm not so sure about the design of that one though...

A lot of cars have their coilover setups hung out on a single shear bolt or stud. The RX-8/NC Miata did it from the factory. Makes me itch, but it seems to work.
In reply to bgkast:
Believe it or not it works just fine I wouldn't rallycross it or anything, but I have customers who more or less daily drive cars with that setup and the coilover mount is the last thing that is a problem.
(Did you know that ladder bars don't have Heims? Too weak. They just have clevises and you use Nylocs on the bolts that hold them in place, so you don't have to tighten them. Scary and noisy but it works...)
I built this brake with crap from Home Depot. Works great, bends 1/4in up to about 4in long.
https://youtu.be/PjBrUfPzSTk
Make some marks on whatever thickness you'll be using say 1/8in apart, bend in the center, then you can calculate how much was used up in the radius of the bend so you can do multiple bends with some accuracy in the future.
In reply to flatlander937:
What's the top piece made from? Looks like it works well.
peter
Dork
5/25/15 12:00 p.m.
Thanks for the suggestinos folks. It's sounding like vice and a big hammer, or finding a metalworking shop who can throw the bends on there is the way to go.
Apparently using the Grizzly vice brake on 1/8" is a great way to break your vice: http://www.garagejournal.com/forum/showthread.php?t=45960
I should explain that building up the mounts out of angle or tube is not going to be feasible. The Lotus seats mount from two bolts high up on the sides of the seat, plus two up front on the seat bottom. And because I'm mounting these to the stock Miata sliders, I've got to move the seat center over an inch or so from the slider centerline, on the driver's side. So I eventually ended up with this as my rear bracket design. The bend would be along the horizontal line in the middle of the picture, which is approximately 2" across, for reference.

When I've done this sort of bending in aluminum, I've always been careful that I start hitting as close to the bend as possible, or else I end up with bowing in the legs. I'm assuming I should still be careful of this with steel? The youtubers I've watched bash metal in a vice haven't mentioned this, or seemed particularly concerned about it.
I would bend that bracket with a vice;
1. You'll have to put the short end in the vice because the big end won't fit.
2. If you don't want jaw marks on it, you can sandwich it between pieces of scrap, as long as the edge along the bend is nice and straight and parallel with the bend.
3. Heat will help. It doesn't need to glow, but heat it along the bend line with a propane or acetylene torch.
4. Use a hardwood block and a big hammer to make the bend. You can tune up the radius by covering it with scrap and beating on it with the big hammer.
5. Don't sweat it. It's going to be under your seat! If it bothers you, paint it with "hammer finish" paint. ;-)
bgkast wrote:
In reply to flatlander937:
What's the top piece made from? Looks like it works well.
Its a piece of 1/4 wall square tube(I think 2 maybe 2.5in wide?) cut in half(half on top half on bottom), a piece of DOM tubing(to add some rigidity for the next part) that fits the width of the square tube, then some 1/8 angle IIRC.
I made it a long time ago but you get the general idea. The key is using tubing wide enough to fit in the half a square, but narrow enough to touch the angle to help brace it.
I THINK I used a vice to compress one of the angle pieces just a bit so slightly more than 90 deg was possible(to account for spring back).
44Dwarf
UltraDork
5/25/15 7:14 p.m.
http://www.aa-mfg.com/
brackets and parts cheaper then you can buy the stock for.
In reply to 44Dwarf:
A lot of that looks like Allstar. I wonder if they make it for them.