The braking system on SanFord is archaic to say the least. It uses a master cylinder, that actuates another cylinder that is hooked to a vacuum booster, and then 6 wheels cylinders. Two on the front, and 4 on the back. I would love to put a standard vacuum assist master on here, the question is, can I.
The front wheel cylinders are 15/16 bore, but only push from one side rather than both.
The 4 rear cylinders are 1.5" bore, plumbed in series, and push from both sides.
I know there are some magic numbers that work best, but the odd wheel cylinder arrangement is going to throw those off a good bit.
So, HELP!
Can I pull the master and booster off a F450 and use it? I'm at a loss and my research on B600 chassis turns up pretty much nothing.
I have no idea, but I can't wait to read the discussion! Talk about deep in the weeds of archaic knowledge...
A little more digging into generic brake system design.
I have 15.48 sq in of piston surface area.
If I'm understanding things right, I need a 1" bore master with a 6:1 pedal ratio to get 1200 pounds of system pressure. So, could I just buy a generic master with the right bore and a matching booster and have it work?
Call Wilwood. I haven't a clue how to answer this quandary,but no doubt they do. Alternately, I'm sure the GRM brain trust will be along shortly.
2 cents you didn't ask for- my Cummins is weird with vacuum. I know this is a potential direction for you someday. Maybe consider a manual option (will that work for something this HUGE? I dunno). Maybe hydro boost? Maybe vacuum boosted is okay, and my truck is a POS. Best of luck. I always enjoy your posts.
The above numbers are assuming a hot rod or race car. Do the same principals work on a truck?
When you say "push from one side" or "push from both sides", do you mean that in the first case, it's like a normal automotive arrangement with the shoes pivoting at one end and being spread by a two-piston cylinder at the other, while the second case is having a second cylinder where a pivot would normally be?
My first thought was that you meant that each cylinder only had one piston, and used that to apply force between piston and cylinder body, rather than having the body on the backing plate and pistons pointing each direction, but that seems even weirder.
Seems like the relative sizes of the master cylinders play significantly into this equation, too...
Oops, a little slow to post. Don't forget to figure out the volume that's getting moved; if you can sort the pressure you need, you also need to be able to achieve it without six inches of pedal travel.
In reply to Ransom:
It's the weirder setup. The front wheel cylinders only have one piston applying force between the piston and cylinder body.

The rears are more traditional, two pistons in a shared cylinder.
In reply to Ransom:
From what I'm reading, 1200 psi is the magic number for system pressure. The 1" master should make that in 1.5" of travel using the piston surface area. With a 6:1 pedal arrangement, that should mean most braking happens at 4" of pedal and panic stops, at maximum pressure, at 9".
The problem is most of the information is assuming you are building a car, not a bus.
Edit: All the information also assumes disk/drum, or disk/disk, not drum/drum. I assume that changes things, I just don't know what.
Do you have power steering? How about a hydroboost? Or add one and a stand alone pump. They stop big drum brakes quite well.
In reply to bearmtnmartin:
No power steering, yet. That's another issue. Finding a power steering box, for a 60 year old bus, is difficult to say the least.
Hydroboost is a consideration. Again, I'm not certain what system would work. There aren't any truck salvage yards around here to wander through.
RossD
UltimaDork
2/1/17 11:59 a.m.
When in doubt, call Wilwood.
I'm in a similar situation with my cabover IH, except the master cylinder actuated by the pedal is oriented so the cylinder is vertical instead of horizontal. My plan is to run a rod down through the floor and install a van bell crank to a hydroboosted master cylinder mounted to the bottom of the floor so it can tilt with the cab. As to sizing the master cylinder itself, with hydroboost I'm going for as big as I can get, and adding drum brake residual pressure valves right at the master cylinder.
9" of travel for max braking is way too much IMO. At that point, I'd use either a bigger master or a different pedal ratio to reduce the travel and add more boost to get enough pressure.
Hydroboost is probably a better option for this, as it'll still be usable if you ever do a diesel swap in the future. Vacuum stuff would require you to add a pump and reservoir in that case.
You're losing me with talking about pressure in terms of the travel to generate it. The travel should come from moving enough fluid to move the shoes to the drums, plus some for flexing, etc... Otherwise pressure should just be the result of force at the piston over piston area.
I don't think the funny single-piston cylinders actually change anything, as long as the piston is pushing one shoe and the body's pushing the other. The one piston will just move, say 1/8" where each of a pair would have moved 1/16". Unless there's something weird going on like it's anchored to the upright and only pushing one shoe, in which case it would have the same pressure (er, force, I should say) but half the travel.
My impression is that drums generally require less hydraulic pressure, either due to leverage ratios or some of the mechanical servo effect of leading shoes. But that's based on cars, old cars, and my impression that discs rarely work anywhere without a booster, while manual drums have acceptable effort and travel 'til they get hot 
In reply to Ransom:
The way I'm understanding things, system pressure at maximum braking effort should be app. 1200 pounds. That is apparently the goal to shoot for. You want a master that will move enough fluid for the given wheel cylinders as well as enough pressure. That's the fine line between too much cylinder diameter and not enough. To much = hard pedal and a lot of effort. Not enough = not enough fluid to move the cylinders.
Taking the total piston diameter/area of all wheel cylinders into account, a 1" master cylinder will need 1.25" of stroke to move enough fluid for the cylinders and create that pressure. This assumes everything is adjusted correctly. This assumes 150# of pedal force. This assumes a pedal ratio of app 6:1. This is also assuming the area of a caliper piston is the same as the area of a wheel cylinder piston.
Unfortunately I'm making a lot of assumptions, which is what I would like to avoid.
And those front wheel cylinders are mounted on the back plate and appear to only move one shoe.
In reply to Toyman01:
Can you post up a pic of the front brakes? I know more than I'd ever like to admit to about wierd brake systems.
Here is what is under the bus.
Master cylinder.

Booster
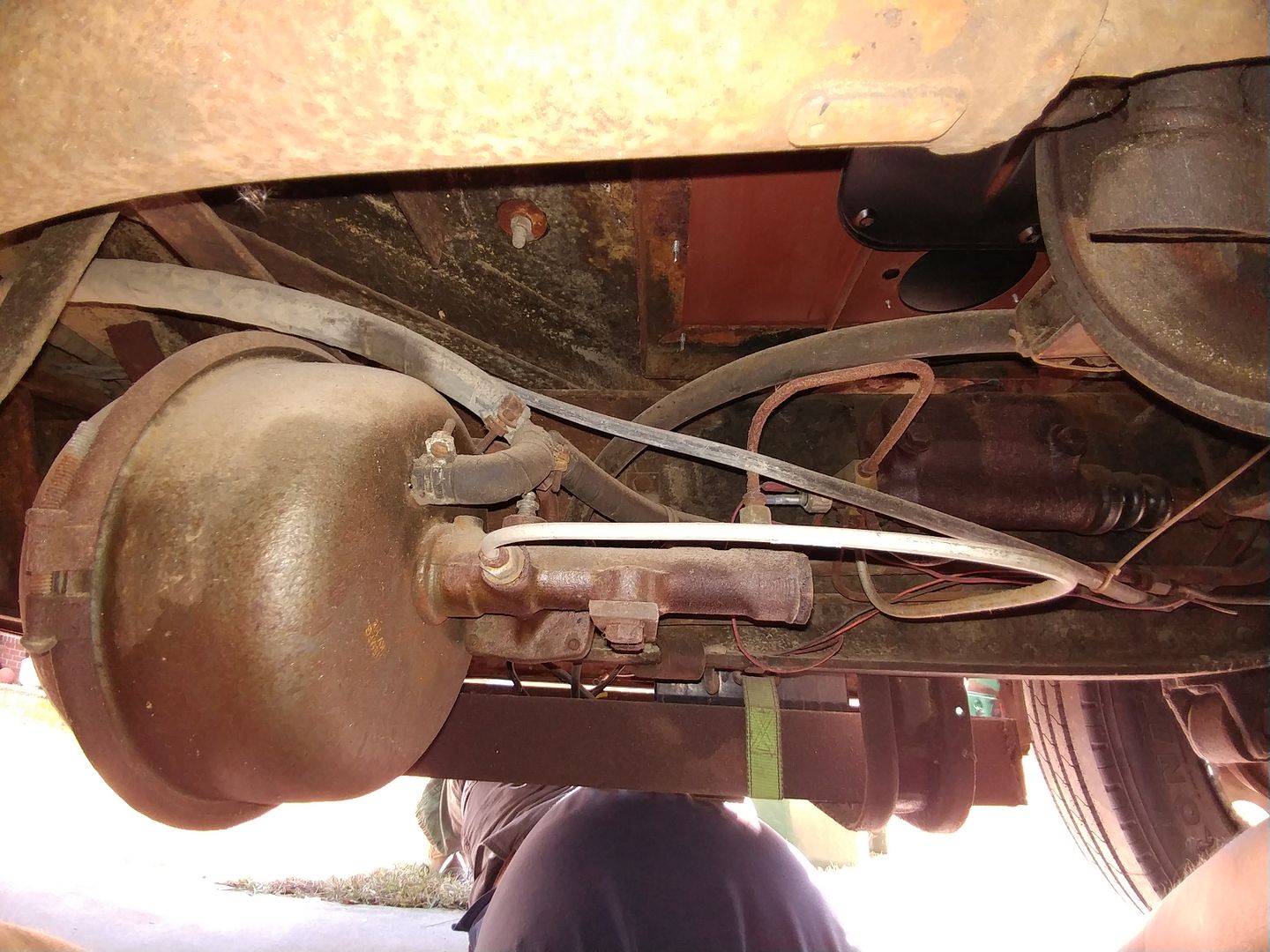
Vacuum reservoir.
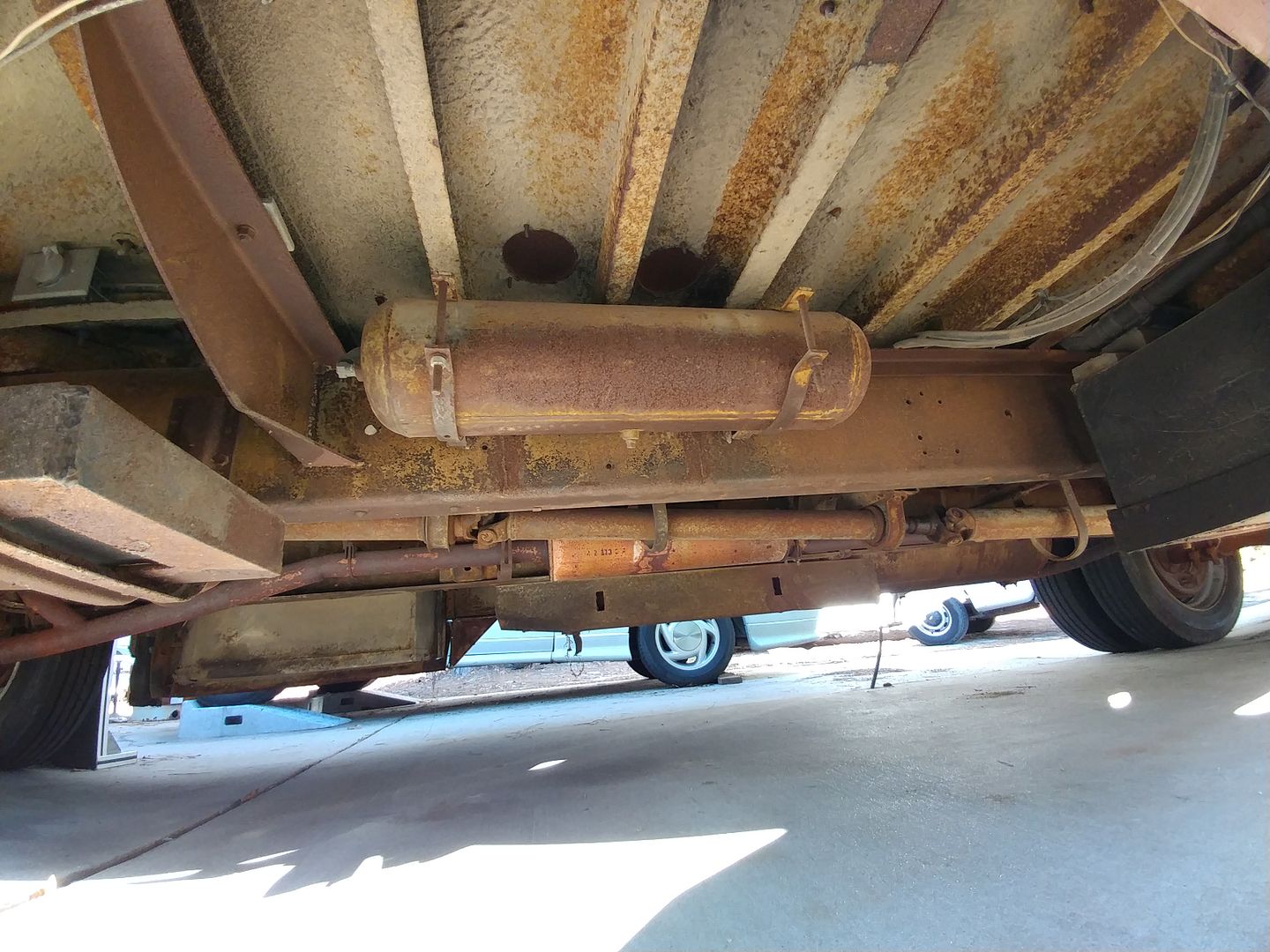
Back plate of front wheel. I don't have any of the brakes torn down at the moment. I'd like to have a plan of some sort before I do.
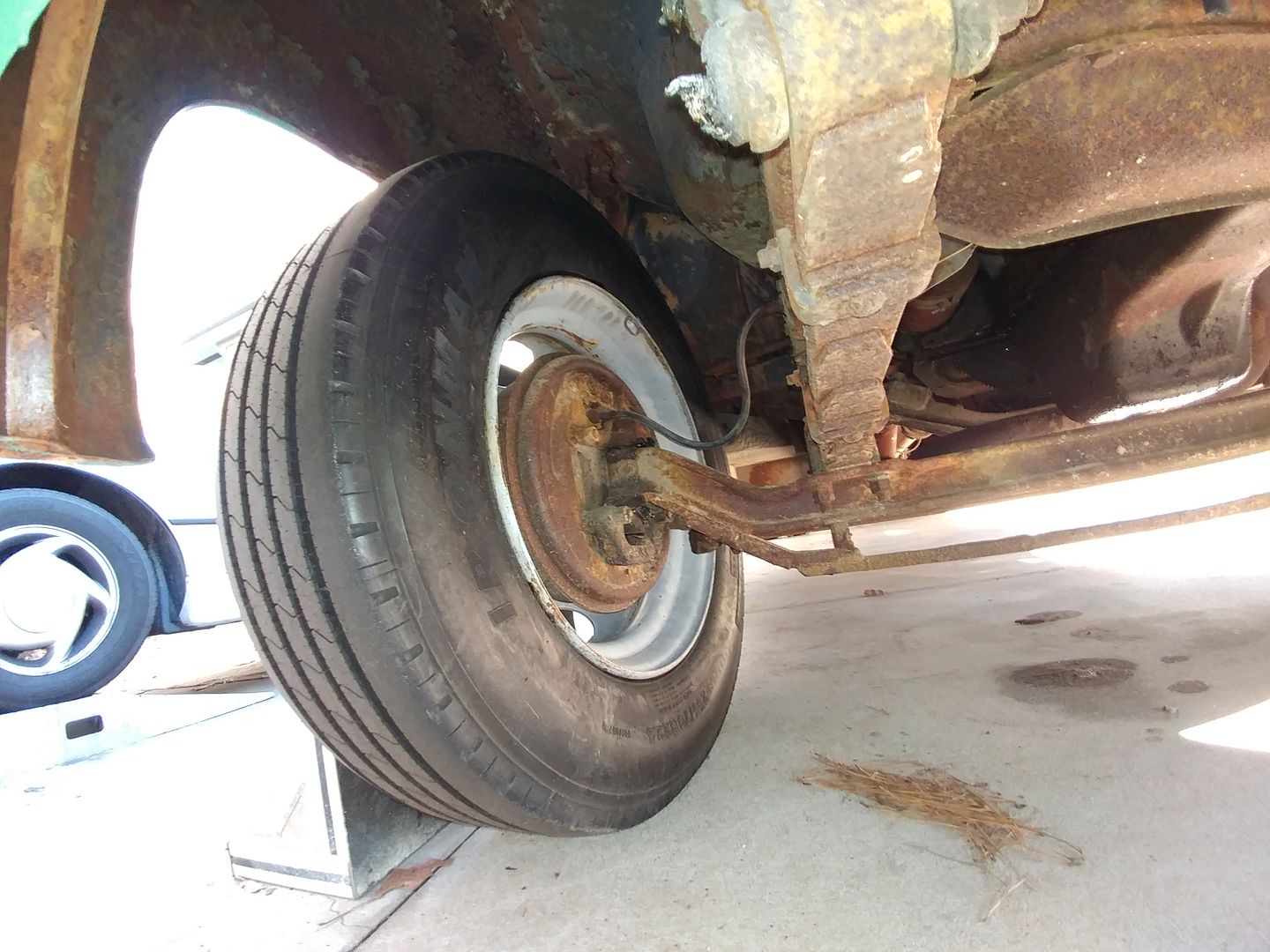
My biggest question is how is this split? It seems that a f/r or a cross split is kind of important from a safety standpoint.
It was the mid-60s before they went with split braking systems. Seems crazy now but that's how it was.
Talking with someone like Wilwood seems like a good idea, there are too many variables in the system for guessing. Either that or seeing what systems are used on class 6 vehicles nowadays or even school buses for ideas. Isn't the rear axle newer than the bus? If so, maybe see what that had for a master cylinder setup. Just a few thoughts.
How about finding a newer front axle with similar spacing on the leaf springs, and swap in some real brakes, that have parts still available? Then you can use the master and booster from that vehicle...
On the other hand, there were an awful lot of hydrovac systems running around the world in the 50's and 60's, and we didn't all die going to school.
This is confusing, it looks like the booster thing isn't doing anything (both lines go to the distribution block) and you really just have a basic single circuit manual braking system. So if you're happy with the current pedal feel just get a dual circuit drum/drum master of the same diameter as the current single master and make a bracket for it.
How well does it drive now? If money were no object you could put new axles with disks and power steering on it but if you're comfortable with how it feels I'd be tempted to just refresh what's there. Growing up we had a soda truck with a similar system and it worked ok. As for the power steering if it's like our old buses once you're moving it's not bad,
As it sits now it's a single circuit system.
It looks like fluid comes off the master cylinder and goes to the booster cylinder. This causes the booster to actuate and push fluid back to the master cylinder distribution block. This pushes the wheel cylinders as well as pushes back on the brake pedal.
My biggest complaint isn't the lack of braking, it's the delay from when the pedal is pressed to when the brakes actually do something and the amount of pedal effort required to get the system moving.
Money no object, I'd buy a new chassis and drop the old body on it, except for one minor problem. The front track is no wider than a 1/2 ton truck, the rest is as wide as a bus. I have had zero luck finding a medium duty axle that narrow. A bus won't work. A medium duty truck won't work. There may be a few RVs out there that will, but I don't know for sure.
My plan for now is to keep what I have and improve it. I have found a vacuum boosted master cylinder conversion for a 56 F350 that looks like it will work. At $190 it's cheap enough I might order one an try it out. The biggest problem is it's set up for automatic transmissions. I'd have to modify the mounting bracket to fit the bus.

If its pushing back on the pedal, the hydrovac cylinder is broken. IIRC from the classes at Tech 38 years ago, you have high pressure brake fluid bleeding back into the low pressure circuit. I like the looks of the one you have pictured.
I think I would retain the vacuum reservoir tank if possible. I can imagine there might be times out on the road where you are going up a grade, and haven't actually created any vacuum for quite some time.