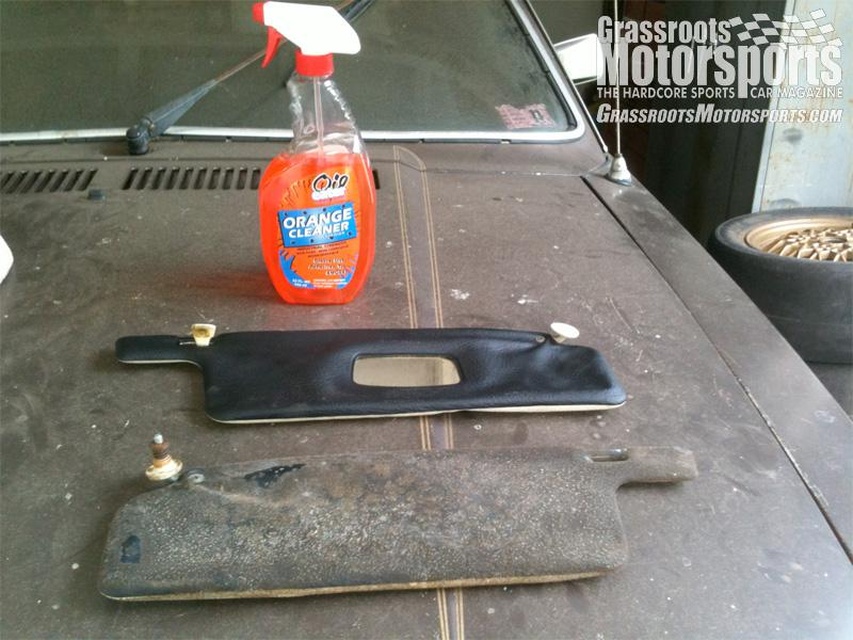
Looking good!
In nearly every car restoration project the same mantra is heard over and over again—Rust is the enemy! Engines can be rebuilt, suspensions can be freshened, but if the tin worm has been at work too long, your treasured machine can become a complete write-off. This problem ranges from Alfa to Zagato, and includes every car in between. Some cars fend off oxidation better than others. Unfortunately, in a rust-away-to-oblivion race, the Mk1 Scirocco is neck and neck with Fiats, Lancias, and early Datsuns. On one hand, this makes nearly rust-free cars like ours a great find. On the other hand, addressing any rust issues becomes that much more important. The great Neil Young told us that rust never sleeps, but we decided to at least give it an extended nap.
While most of our Scirocco is free of rust, the driver’s floor had been “repaired” by the previous owner with fiberglass. Cutting off the old 'glass and removing any remaining rusty areas was the first order of the day. We used an angle grinder for this part of the job and made sure to wear a breathing mask. Fiberglass is great on a Corvette, less great in your lungs. Once the fiberglass was eliminated and the rusty areas cut away, we were left with a gaping hole directly where the driver would sit—Yabba Dabba Doo!
Our welding guru and all around good guy Steve Brozyna stopped by to help with fitting and welding the new floor panel we sourced from rabbitparts.com. Though the Mk1 Rabbit and Scirocco are nearly identical underneath the bodywork, there are minor differences in the floor pans. Unable to find a nice Scirocco pan, we decided our best move would be to slightly modify a Rabbit pan. After all, this repair is on the floor and will be coated with POR–15. Cosmetic beauty and originality on the underside of the car is not paramount.
The hole in our floor was larger than the front pan we had purchased, so we obtained a bit of sheet metal, and after a bit of cutting and fitting had the coverage we needed. Steve may have come over to help, but he believes in the teach-a-man-to-fish philosophy. He helped welding newbie Joe Gearin tack weld his first metal together. The welding became addictive, and before too long the floor was solid, and together. Sure, the welds may look like they were done by a monkey with half a brain, but the floor is solid, secure, and best of all, rust free. There will still be a bit of hammering and fitting needed to finish the floor, but for now we’re just happy to be able to sit behind the wheel and make vroom vroom noises. Thanks again to Steve for his hard work and patience.
With the floor solidly in place, we decided to clean some of the interior parts. The Scirocco has been dormant since 1986; all kinds of greasy funk had found its way onto the car’s upholstery over the years. We had grown tired of soiling our hands and clothing each time we brushed up against a sun visor or door panel. We grabbed a bottle of Oil Eater’s Orange Cleaner spray and it worked remarkably well. The visors were transformed, the door panels came clean easily, and the nice orange scent reminded us of driving down to the Sebring 12 Hour Race. As a bonus, Orange Cleaner is 100% biodegradable and Earth-friendly.
Next on the list for the VW will be the repair of the subframe support beam, and then we are planning on diving into the engine bay. We recently picked up a 2.0-liter ABA engine, which will fit nicely in place of the stock 1.6 liter. We figure 130 wheel horsepower in a 2000 lb. package should do the trick.
i need advice and guidance on repairing passenger side shock tower on a 1982 vw rabbit pick up. i need access to buy a new or usedshock tower, or a better lternative to repair this. i am happy for any knowledge or access to keep this truck on the road. i want this as a daily driver. i want go back to montana this summer and need to make the mini d road worthy. thanks
You'll need to log in to post.