mke
Reader
4/3/19 8:34 a.m.
Here's a graph I found....The engine was sitting at high idle, bottom section redline shows map steady at 45 ksi, rpm around 1400. but the cyan line shows fuel pressure bouncing between about 15 and 60 as the fuel tank was running empty.
Then the black line up top shows the injector time reacting, high pressure low time, low pressure high time and lambda steady.....fuel pressure correction is a nice feature to have.
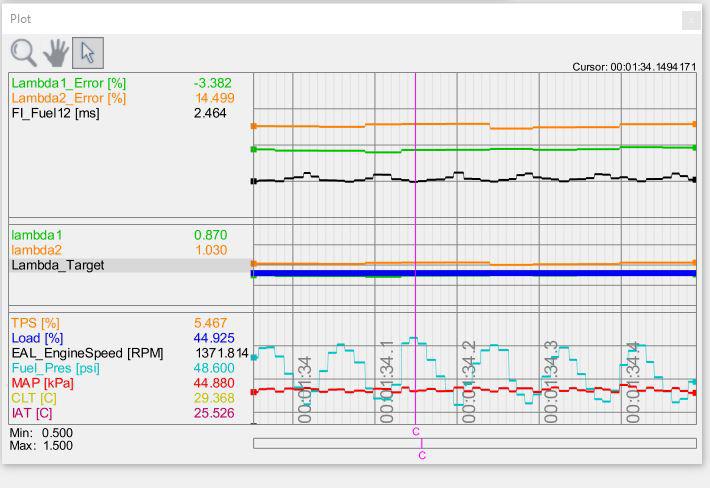
MadScientistMatt said:
I'd run the fuel pump speed control in open loop - more of an "X duty cycle for Y RPM" - and let the regulator handle the pressure control. Having two active control mechanisms going on at once is likely to end up chasing its tail.
Thats how it is at the min. Below 100kpa 70% duty. Above 100kpa 100% duty.
Problem is when it heats up. Its drops 5 psi across the board.
Simply switching the duty in open loop at a set point doesn't fix my actual pressure problem. It helps keep temps down as the pump isn't flat out all the time but thats it.
I'd need to attempt closing the regulator a bit more, lowering my duty even more when setting base pressure then have the head room to increase the duty in closed loop when the fuel gets hot to overcome the pressure drop.
I really dont want to do all this bollocks but i have to try something to make it more stable.
The chasing its tail thing is the only thing I'm worried about. But I can slow down the PID so the mechanical regulator with boost reference connected does its normal thing first .Then the ecu will try exact matching the set psi if it's wrong. It may only have to adjust duty a small amount and i might be able to adjust the amount of correction so its not bouncing around from 0-100 duty and going buck wild. Maybe max of 20- 25% correction on the positive side.
In reply to mke :
Thats all good info on the pumps. I might go get a walbro pump. I'm pushing 30psi boost... Plus base pressure.. Yikes....
Im My opinion the whole issue is, as the fuel heats the pump just doesnt work the same as when it's cold. All the factors that snowball and elevate the fuel temps change the pumps characteristics. It almost sounds different when fuel is hot. I think the pump motor gets stressed as the clearances within the pump get tighter. This in itself then starts to heat the fuel even more..... More snowballing.
Hot day, small tank etc etc etc
mke
Reader
4/3/19 10:23 a.m.
Craigorypeck said:
The chasing its tail thing is the only thing I'm worried about. But I can slow down the PID so the mechanical regulator does its normal thing first .Then the ecu will try exact matching the set psi if it's wrong. It may only have to adjust duty a small amount and i might be able to adjust the amount of correction so its not bouncing around from 0-100 duty and going buck wild. Maybe max of 20- 25% correction on the positive side.
That will make the PID very angry because it ill be looking at wrong information. If you want to run closed loop PID that;s fine but set the regulator above anywhere the PID will ever try to send the fuel pressure so it is getting the correct feedback about what's going on. I don't know what the MS control strategy looks like buy a feedforward term, like an open loop table you've tuned manually so it knows about where the right answer is can often be very helpful but usually not critical, just improves system reaction times and can help reduce over/under shoot.
I'll go back to what I was getting at above with the constant lambda when fuel pres is jumping around post.....its near to impossible to get as steady and responsive fuel pressure from a PID setup as from a mechanical regulator....which is why I'm pretty sure all the OEM vehicles that use closed look use a version on the pressure corrected fuel pulse control I posted. Just somehting to keep in mind as you head down this path.
mke
Reader
4/3/19 10:24 a.m.
In reply to Craigorypeck :
That sounds exactly right to me.
mke said:
Craigorypeck said:
The chasing its tail thing is the only thing I'm worried about. But I can slow down the PID so the mechanical regulator does its normal thing first .Then the ecu will try exact matching the set psi if it's wrong. It may only have to adjust duty a small amount and i might be able to adjust the amount of correction so its not bouncing around from 0-100 duty and going buck wild. Maybe max of 20- 25% correction on the positive side.
That will make the PID very angry because it ill be looking at wrong information. If you want to run closed loop PID that;s fine but set the regulator above anywhere the PID will ever try to send the fuel pressure so it is getting the correct feedback about what's going on. I don't know what the MS control strategy looks like buy a feedforward term, like an open loop table you've tuned manually so it knows about where the right answer is can often be very helpful but usually not critical, just improves system reaction times and can help reduce over/under shoot.
Ive never tried closed loop fuel control but surely its not that different than running closed loop boost control. ? You have two factors at play within a wastegate? The actual back pressure acting directly on the valve and the PID controlled reference to the diaphragm.
I know, completely different right!??
mke
Reader
4/3/19 12:04 p.m.
Craigorypeck said:
Ive never tried closed loop fuel control but surely its not that different than running closed loop boost control. ? You have two factors at play within a wastegate? The actual back pressure acting directly on the valve and the PID controlled reference to the diaphragm.
I know, completely different right!??
Its the same idea.....but fuel pressure in more like throttle control which is again similar. The difference is system reaction time and rate of change. With a boost controller the system doesn't react very fast and you want to over damp it a bit, so it eases into the number with no overshoot which could break stuff. The system is pumping a compressible fluid too so that means it has built in capacitance that smooths things a bit.
With fuel the fuel flow basically needs to follow the throttle pedal, ramp the throttle, MAP shots up, the fuel flow needs to go with it or you're lean until it catches up so quick response and that means allowing it to over shoot by a bit....while ideally the ECU is adjusting the injector pulses up or down to deal with any pressure lag or overshoot and keep the mixture at target, like the graph I posted.. Then fuel is not compressible and metal or braided lines doesn't expand so there is very little capacitance to smooth things out....its just harder than boost control. Which is why I say its more like throttle control.
I think once you get yourself a pump that can handle your flow needs you won't have a pressure issue and fuel temp management will be a nice to have. I think the fuel cooler is a good idea there. Then the open loop pump speed setup is probably all you need. That's all I run, mine has voltage correction and looks at MAF so high MAP but low RPM is still low pump speed so more resolution but low/high will get you maybe 80% of what's possible.
mke said:
Craigorypeck said:
Ive never tried closed loop fuel control but surely its not that different than running closed loop boost control. ? You have two factors at play within a wastegate? The actual back pressure acting directly on the valve and the PID controlled reference to the diaphragm.
I know, completely different right!??
Its the same idea.....but fuel pressure in more like throttle control which is again similar. The difference is system reaction time and rate of change. With a boost controller the system doesn't react very fast and you want to over damp it a bit, so it eases into the number with no overshoot which could break stuff. The system is pumping a compressible fluid too so that means it has built in capacitance that smooths things a bit.
With fuel the fuel flow basically needs to follow the throttle pedal, ramp the throttle, MAP shots up, the fuel flow needs to go with it or you're lean until it catches up so quick response and that means allowing it to over shoot by a bit....while ideally the ECU is adjusting the injector pulses up or down to deal with any pressure lag or overshoot and keep the mixture at target, like the graph I posted.. Then fuel is not compressible and metal or braided lines doesn't expand so there is very little capacitance to smooth things out....its just harder than boost control. Which is why I say its more like throttle control.
I think once you get yourself a pump that can handle your flow needs you won't have a pressure issue and fuel temp management will be a nice to have. I think the fuel cooler is a good idea there. Then the open loop pump speed setup is probably all you need.
I'm hoping the same thing!
That's all I run, mine has voltage correction and looks at MAF so high MAP but low RPM is still low pump speed so more resolution but low/high will get you maybe 80% of what's possible.
Thanks for the info.
In reply to mke :
I also stumbled upon an other idea that pwms the pump.
A pressure sensor is plumbed into the return line. There's a restrictor in the return line and the return line is closed loop pwmd to remain at say 5psi. The regulator just does its thing. Migth try this kinda set up...
mke
Reader
4/7/19 6:51 a.m.
A restrictor will have a pressure dop that varies with flow...flow^2 i think but I'd need to look it up but its not linear. Then the regulator is assuming 0psi in the return line, so any psi caused by the restrictor will be added to the regulated pressure.....so really the regulator is establishing a min pressure sort of but the actual pressure control is the PWM that is trying to maintain the 5 psi. I'm not sure you're helping yourself in any way.
There are fuel flow gauges tht are fairly low restriction that might give you the signal you're after without changing the pressure.
In reply to mke :
Bear with me here.. If someone was using a stock return line in an uprated fuel system and the return line was less than optimal there would be a back pressure in that line. So if the pump is pushing 45psi of pressure against the fpr and there's 5psi in the return line the fpr is maintaining the other 40? The fuel rail pressure will still remain constant at 45 psi even though the return is restricted to varying degrees under operation. Could be 2 psi or 10psi. Total at rail still 45psi.
Only problem would arrise is if the return line was creating more pressure drop than the actual fpr. Then the fpr is doing nothing. That could be an issue in a low pressure carbed setup but in higher efi surely not?
Here to learn.
mke
Reader
4/7/19 3:48 p.m.
In reply to Craigorypeck :
Ok, let me think.......hmmmmm
The gauge is reference to atmosphere, so it reads right. No issue there
The regulator is referenced to atmosphere or the intake, so it should also be ok as long as the return line restriction doesn't get close to the control pressure.
The pump...its pumping against the regulator, that's ok.
So its ok I guess now that I really think about it its probably ok as long as the pump controller reacts fast enough to to prevent pressure drops. A PID will get confused if you hit the limit of the pump flow (100% PWM) so you'll want to be sure to clamp the I term to prevent integral windup its call where the I term just keeps growing and the system then can't react in the other direction until the I term unwinds itself, a clamp value stops that.
You'll need to play around to find the right restrictor....maybe just a small return hose? Something like a carb jet wil work and the fuel should be clean....but small holes can get plugged. I'd guess you'd want maybe 5 or 10 l/min at 5psi? On a product I designed some years back that was a problem and using the hose as the restrictor solved it since I could use something like a 1.5mm ID hose in place of a 0.2mm jet or about those numbers....but fuel should be clean so.....
I saw you talked about intake hose, have you picked a new larger pump?
You have to have a stable pressure at the injector, you can boost reference the regulator but that is stable and repeatable by manifold pressure which will correlate to your VE table.
You cant have different fuel pressures at the same manifold pressure, that will yank your fueling around as you have found. It's like changing the ReqFuel number mid stream. The MS uses that as a constant for fuel calcs
When a second pump comes on or the PWM goes to full smoke the fuel pressure should not change the pressure regulator has to deal with that or your fueling will go bonkers.
The only way fueling will tolerate different fuel pressures at the same manifold pressure is to table switch. Which in my eyes is a kluge unless you are doing something big like NOS.
Another thing that drive fueling bonkers is a heat soaked MAT sensor.
I prefer to avoid the razzle dazzle stuff in favor of a simple predictable system. I swear by KISS
But if you are going to use PWM fuel pump control pump output cannot affect injector rail pressure. In other words you cannot slow the pump so much that the output pressure is less than the rail pressure being commanded by the regulator.
Theoretically you could use a fuel pressure sensor and feedback to the PWM control to regulate fuel pressure but not sure that can be implemented with a MS3. If it is it would also have to tie into the MAP signal as well so the pressure at a certain MAP level is always the same.
mke
Reader
4/7/19 5:42 p.m.
bentwrench said:
The only way fueling will tolerate different fuel pressures at the same manifold pressure is to table switch. Which in my eyes is a kluge unless you are doing something big like NOS.
All modern ECUs use a table for injector flow vs fuel pressure and will deliver the correct amount of fuel over a very wide range of fuel pressures. They also use tables for dead time vs Vbat and Fuel pressure and another table to deal with the non linear or short pulse region. I have no idea what MS3 allows, but good ecus are basically fuel pressure insensitive. When my fuel pump was failing my fuel pressure had dropped from 58 to about 10psi before I even realized there was an issue....I posted the log that showed the fuel pressur eboncing 15-58 as the tank ran dry and lambda was steady, its just a non-issue with a proper ecu. I added low fuel pressure to the items that light the warning light on the dash and fuel pressure to all my tuning screens so next time I'll know before it becomes critical, modern systems almost work too well.
Yes I'm going with a walbro 450 pump.
Just reading compare stuff online between different pumps regarding flow, amp draw etc.. And they mentioned that the pump I'm using began to heat fuel very quick. Anyway....
I'm going to just install the sensor in the return line and see what back pressure its currently got. Although it's all an6 there's a couple of 90s and the fuel cooler will be in there. I'm not looking for massive restriction like a carb jet. In thinking a small section of an4 will suffice. Just need to play around with it. I probably don't want the pump running too little either.
Regarding the pid control, it doesn't have to be perfect. The regulator will just do its job. As the post fpr pressure goes up or down it just needs to keep up.. Even if its behind it even over shoots the fpr will look after it.. Within reason of course.
mke
Reader
4/7/19 8:14 p.m.
In reply to Craigorypeck :
Sounds fine. You can drop a slug.plug into the hose with a small hole drilled to get the pressure you want.
bentwrench said:
Theoretically you could use a fuel pressure sensor and feedback to the PWM control to regulate fuel pressure but not sure that can be implemented with a MS3. If it is it would also have to tie into the MAP signal as well so the pressure at a certain MAP level is always the same.
Yes ms3 pro cross references map and base pressure to keep rail pressure where it should be in boost.
Alternatively I think close looping the return line pressure is a good way to control the pump speed. Id only be working with a simple steady rate pressure. No worries about boost reference.