RE: Revaz Bmw
Yes I am making a log style manifold. Again I am using the Callaway one in the photo above as a starting point. I know that a true header style would be better for that last bit of performance, and who knows if I get it up and running I may try it, but for what I am building a log or hybrid log style as I like to call my elbow only design should do the trick. They are just so simple to make.
Looking closely at the Callaway design you will note that there are no T sections. It is all elbows directing the flow into the pipe. For lack of a better description I would call it a “mini header” style as opposed to a log. I guess you could call it a hybrid log style. I think that this is very important to the functionality of this style of header. Many log style headers use T sections of pipe on the middle cylinders (2 &3 in my case). Although this makes the fabrication very simple I can see where letting the exhaust out into a T would result in it going both directions in the manifold hindering flow on the cylinders up stream. This would result in alt of back pressure especially in the upper RPM’s. I also see there being a big wave bouncing back off the wall opposite where the exhaust gases are let in to the manifold resulting in some weirdness in the combustion chamber. Put this all together and my very simple minded analysis of the log header is that you should reduce many of the problems associated with log style headers by eliminating the use of T’s in the construction and instead using elbows to direct the flow into and through the header/manifold to the turbo.
Here is a better photo showing the Callaway one.
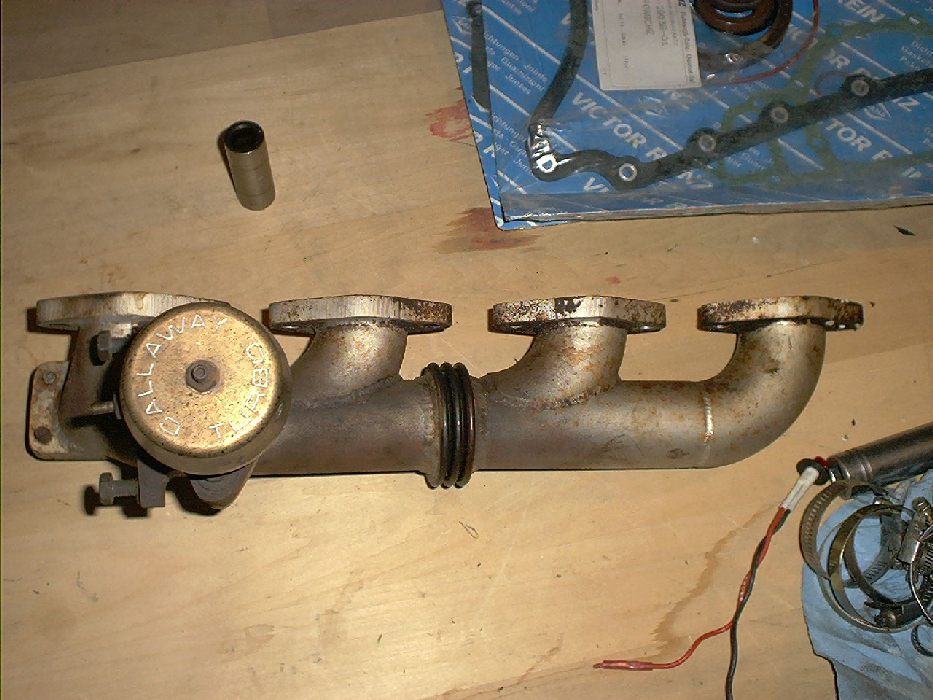
Versus the standard log with T's
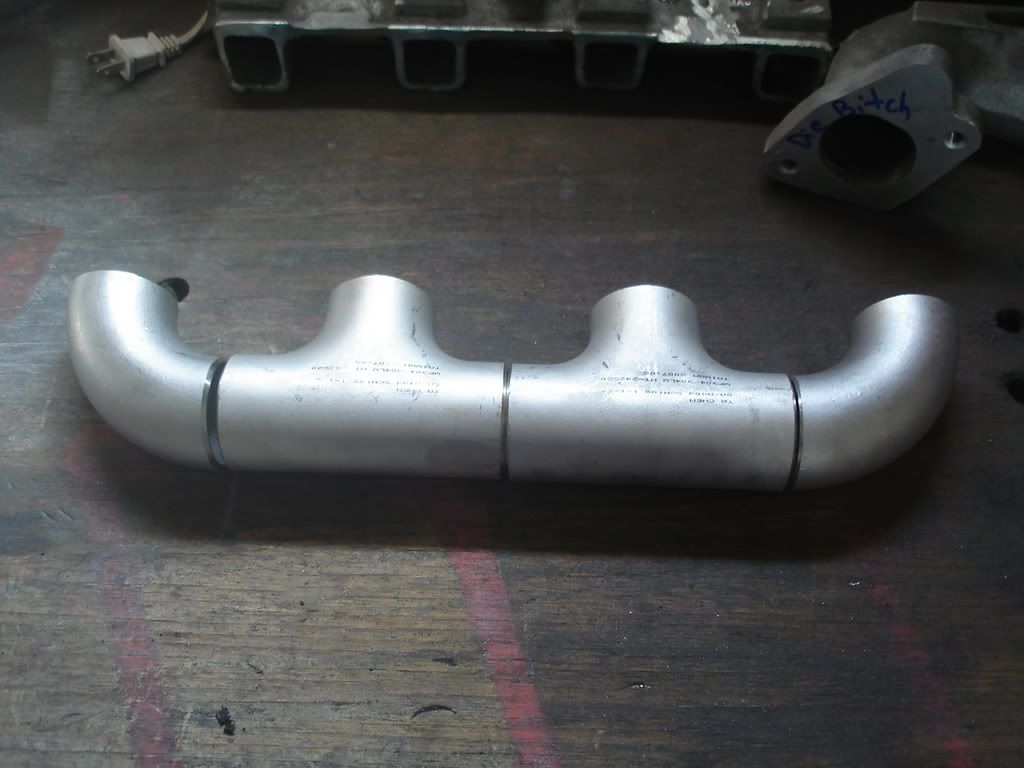
So my header is going to be made of 90 deg elbows into a strait piece of pipe. (Again the Callaway does this) I have to order the pipe, elbows and flanges. Before I did this I wanted to make sure that the turbo would actually fit in there. Since it looks like it will this will be next on the list.
The issue is that the space between block and the sheet metal at/above the frame rail is very tight. Basically draw a vertical line ¾ inch outboard of the motor mount strut and that is all the space I have. Also there is a cam tower on top of the head that I don’t have in place at the moment. That further limits space above the turbo.
The clearance between the intake and the motor mount is actually very good. I can push the unit back another 1/2 inch.
What I think I need to do is rotate the hot side housing about 30 deg clockwise kicking the waste gate lever up a little so I can push the housing back closer to the block. I also need to rotate the cool side counter clockwise so the outlet is at or just past vertical. This will / should allow it to clear the sheet metal in the engine compartment and still have enough room to get the pipe up between the manifold/cam tower. The other option is to spin the cold side so it is facing at about 7 o'clock (about 180 from where it is in the photo above) I could then just run the pipe under the motor and up on the other side in to the top mount IC (where the air box is) and then in to the intake. I am going to have to look at this. I think the best thing is to get the hot side mounted as close to the block as possible so that the WG lever works and then play with the cold side. The bad is that this will put the BOV diaphragm that is on the cold side of the turbo very close to the header and it may actually cause the turbo to be clicked out from the block some. Thinking about it putting the outlet from the turbo down and running it under the motor away from the manifold (heat rises) would be a better in terms of heat.
I had actually thought of flipping the whole thing 180 putting the exhaust exit facing forward. I would then have a pipe with a 180 deg bend exiting the hot side of the turbo and run the exhaust out that way. This way I could very easy plump the intake up to the area where the battery is (at the base of the windshield). This would also make running the pressurized side from the turbo under the back of the motor between the oil pan sump and the clutch housing easier. There is about a 3 inch gap there. Then again back up to a top mount IC and in to the intake on that side of the motor. The issue I have with this it puts the exhaust inlet on that side away from the block making actually fitting the turbo in place a challenge
Like I think I said it is a 3d puzzle. Change one thing to make it better and it changes something else or you run in to some other issue.
Ok time to take it apart re clock the housings again and see what we get. I think I am going to end up re clocking this about 10x before I am happy. I need to build/weld up a holder for the center section that is fixed to the engine stand. This will allow me to make these changes fast. This suspending thing with bailing wire is not the best.
Then I have to think standalone ECU for the fuel. Since I am already using a programmable EDIS based ignition system (MJLjrt from Autosport Labs) I was thinking of just going with the basic MS-I V2.3 modified to “play nice” with EDIS. I hope to make this a PIP deal by gutting a old DME I have. That way I should not have to hack up the harness keeping the experiment reversible.
More on the other stuff later. I really need to start a documentation thread on this build. Ya I know the readers rides section will be tossed at me by someone and yes I could but I like the format of a thread better. Seems to have more conducive to ideas/opinions and getting answers to things from others.