A buddy of mine recently sold his chassis dyno. Afterwards we started talking about him building a dyno to replace it. Something on a budget.
I got to thinking about trying to build my own small dyno. Something relatively cheap that I could use to learn.
I found a ton of scrap steel and started ordering parts.
I set of a MAX budget of $500. I had a working model at just $400.
This is a hydraulic dyno that uses a torque arm and load cell for its readings.
I bought a cheap(ish) hydraulic pump, hoses, fittings, chain, sensors, etc.
Everything is controlled by an Arduino Nano. I'm using a 30 kg load cell, Bosch weather sensor for SAE correction, and an AEM wideband.
A stock GM 24x LS crankshaft sensor measures RPM of the engine.
The concept is fairly simple. The engine drives a hydraulic pump that is moving hydraulic fluid.
The pump has a 12" torque arm attached directly to it with a load cell on the end.
You use a needle or gate valve to close off the exit of the pump and build pressure, making the pump harder to turn.
When it gets to a point where it can maintain a constant RPM, the load cell with have a reading in pounds. With a 12" torque arm, 1 lb is 1 ft-lb.
I read RPM to convert TQ to HP. A wideband also graphs AFR for me.
I've done lots of testing, and I'm finally getting everything nailed down where it needs to be.
With the extra $100 I have left on the budget, I'm adding automated load control via a stepper motor controlling the valve.
I'm also purchasing some software to help graph the data.
Here is what I have so far:
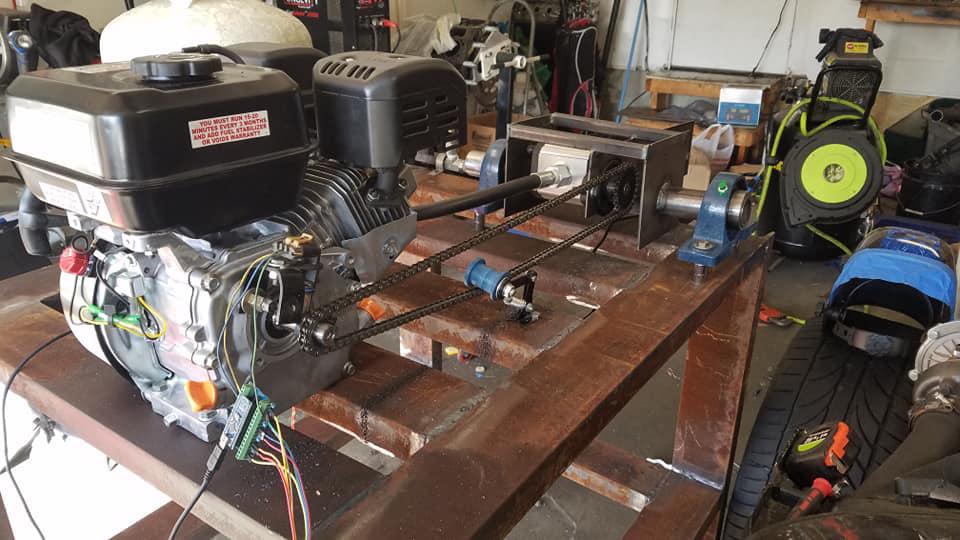
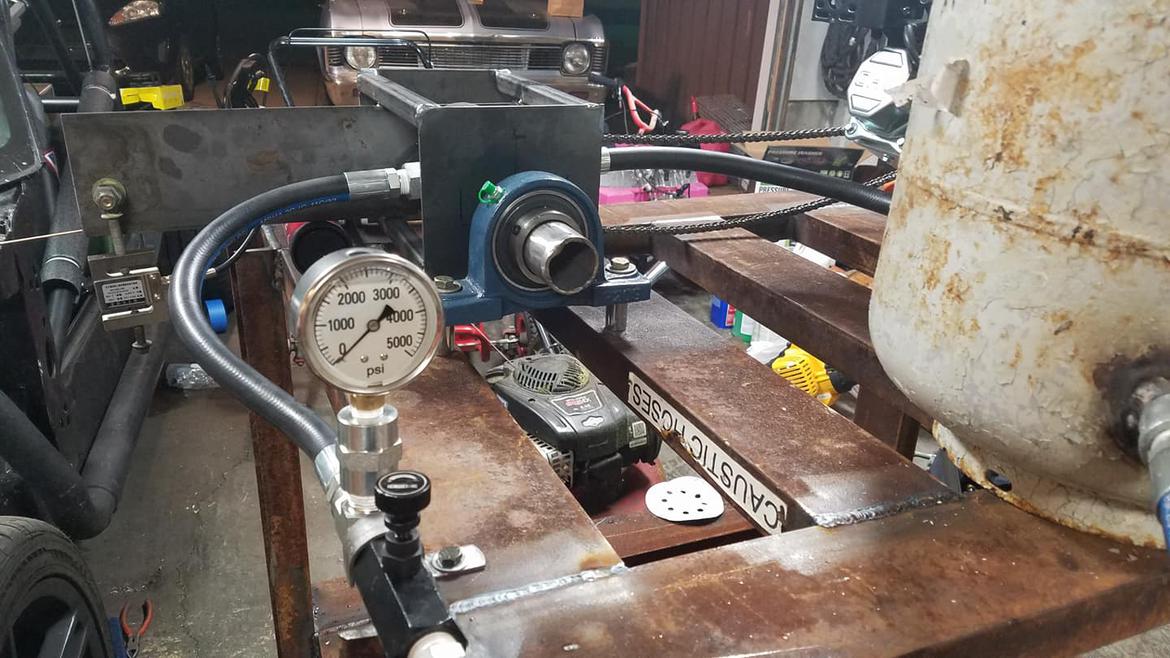
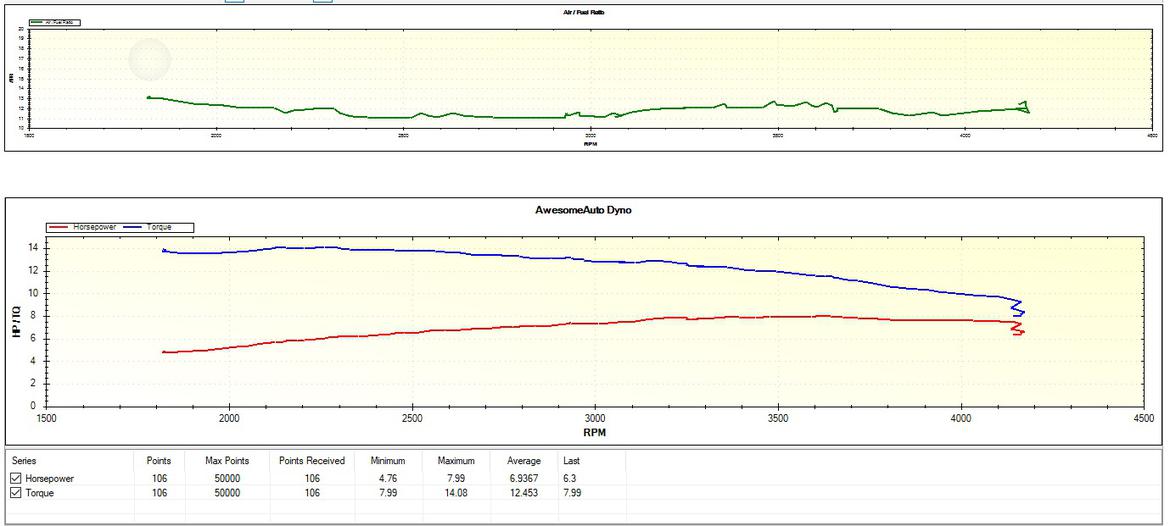
The end goal is to use it as a learning tool. I'm mostly dealing with $99 harbor freight engines.
I want to test various fuels. How much of a jetting increase they need, how much extra power they make. How much cleaner they burn.
I'll try out basically anything recommended to me. So far on the bill:
-87 Octane
-93 Octane
-C16 race gas.
-Methanol
-E85
-Nitromethane
-Acetone
-Mineral Spirits
-Isopropyl Alcohol
-Brake cleaner
-Lighter fluid
-Starting fluid
-Carb Cleaner
-Diesel
-Plus whatever else I can find in my garage that burns.
I also planned on testing various air filter designs, carburetors, headers, compression ratios, oils, oil additives, etc.
I'll attempt to post back when I get more data.
In reply to AwesomeAuto :I’m very impressed at what work scrounging, intelligence, and creativity you’ve displayed.
Well done!
Wow, impressive!
Id love to see you hook up with the Cars and Cameras guys with this!
ebonyandivory said:
Wow, impressive!
Id love to see you hook up with the Cars and Cameras guys with this!
I recently had a guy put his engine on it, claiming to have copied their "20 HP" recipe (which they've never dynoed).
It made 13 horsepower. Air/fuel ratio was WAY off, and it was getting massive spark knock. He couldn't say for sure what gasoline he had in it at the time.
Part of my reason for wanting to make this is all of the speculation I see. Lots of numbers, but zero proof or reasoning behind them.
I also plan to do a turbo 212. Something seemingly nobody else has managed to pull off just yet.
Luckily for me, not only are turbos my specialty, but I've identified almost every aspect of the failed attempts, and I should have FAR more luck than them.
44Dwarf
UberDork
10/27/18 9:53 p.m.
The kart shop a friend works at uses similar unit but the pump fits the crank directly so no chain loses and no worry of busted chains going flying around at max torque.
I need to break out my water brake bike chasis dyno and upgrade to electronics and data logging.
Please don't try burning brake cleaner it can be deadly it can make deadly nerve gas (phosgene gas)
Please don't try burning brake cleaner it can be deadly it can make deadly nerve gas (phosgene gas)
That's chlorinated brake cleaner, non-chlorinated is more common these days.
Non-chlorinated brake cleaner only. No worries.
The problem with fitting it directly to the crank is the RPM. I entertained the idea for a while, but the range of pumps I'm using was intended for diesel powered heavy equipment, so RPM is typically limited between 2600 and 3600 RPM. I gear down the ratio with sprockets to keep the pump RPM below the maximum recommendation.
This is the first design I came up with. The 2nd design will face the engine 180 degrees of the pump and run a MUCH shorter chain. Even with the current design, a chain guard is being designed that will keep it in check in the case of a breakage.
Pump and chain inertia are accounted for in the code, so no real losses there, either.
I've thought of "almost" everything. There are still a lot of fine tuning issues I need to deal with.
One being engine temperature. I've noticed that even with SAE J1349 correction factor, I've picked up a full horsepower (now reading ~8 horsepower) in the last few breezy 50 degree days as opposed to the 6.75-7 horsepower readings I was getting on 70 degree days. It appears that although oil temperatures are consistent, the rest of the engine is staying much cooler.
It looks like any direct comparison tests I do will have to be conducted in a single day if I want to maintain a level of accuracy.
I've purchased some sensors that will allow me to measure engine/oil temperature before dyno pulls.
AwesomeAuto said:
ebonyandivory said:
Wow, impressive!
Id love to see you hook up with the Cars and Cameras guys with this!
I recently had a guy put his engine on it, claiming to have copied their "20 HP" recipe (which they've never dynoed).
It made 13 horsepower. Air/fuel ratio was WAY off, and it was getting massive spark knock. He couldn't say for sure what gasoline he had in it at the time.
Part of my reason for wanting to make this is all of the speculation I see. Lots of numbers, but zero proof or reasoning behind them.
I also plan to do a turbo 212. Something seemingly nobody else has managed to pull off just yet.
Luckily for me, not only are turbos my specialty, but I've identified almost every aspect of the failed attempts, and I should have FAR more luck than them.
This magazine already did dyno test most of the common fuels.
What they missed was testing of boosted ( turbo’d ) engines where the benefits of alcohol really shine
When I read the title and first couple paragraphs I thought there was no way you could do this. But I must say, WOW, that is very ingenious. I never would have thought of using a hydraulic pump. You seem like an engineery type and you say you thought of almost everything. I'm just wondering if you also account for heating of the hydraulic fluid on longer runs and becoming less viscous. Do you incorporate a fluid heat exchanger? Or do you monitor fluid temp and compensate in the calculations? Or is the temp rise pretty negligible?
Oh man. Where were you a year ago when I was building my 5hp Briggs powered drift trike. I ported the thing and used a pit bike carb. It certainly felt like more torque...
Very cool project. The thing is it doesn't necessarily need to measure some calibrated horsepower level, as long as it's repeatable so you can tell if you are getting gains or losses from one test to the next.
In reply to AwesomeAuto :
I’m VERY interested in the 212 turbo. I just bolted a new one on one of our go karts and I’m impressed by how well it pulls with my 250lbs aboard. A well-running turbo would be crazy.
Brotus7
HalfDork
10/28/18 8:47 a.m.
ebonyandivory said:
In reply to AwesomeAuto :
I’m VERY interested in the 212 turbo. I just bolted a new one on one of our go karts and I’m impressed by how well it pulls with my 250lbs aboard. A well-running turbo would be crazy.
I now have the desire for a turbo 212 predator wheelie machine. You know...for the kids.
stuart in mn said:
Please don't try burning brake cleaner it can be deadly it can make deadly nerve gas (phosgene gas)
That's chlorinated brake cleaner, non-chlorinated is more common these days.
Also chlorinated brake cleaner doesn't burn, that's one of the reasons why it was popular.
In reply to codrus :
Well that, and it cleans better in my experience.
This is a great build. I would love to have a chassis version to test karts but I don't have the expertise to attempt a build like that
stuart in mn said:
Very cool project. The thing is it doesn't necessarily need to measure some calibrated horsepower level, as long as it's repeatable so you can tell if you are getting gains or losses from one test to the next.
I had a dyno at the end of my garage. A steep hill that I’d do a rolling start on for consistency. When I crossed the chalk line I’d start my stop watch. The line at the top of the hill I’d stop my stop watch.
Whatever was faster I’d try more of until the stop watch said I was slowing down.
Round and round the block I’d go, stopping in the garage to make adjustments. I’d hit the first chalk line at 5 mph ( 2000 rpm ) and be around 20 mph ( 5000 rpm ) at the second chalk line. Since the car was muffled nobody knew I was doing Race tuning.
Great build !
What compression ratio are you running and is it easy to change it up or down for testing ?
freetors said:
When I read the title and first couple paragraphs I thought there was no way you could do this. But I must say, WOW, that is very ingenious. I never would have thought of using a hydraulic pump. You seem like an engineery type and you say you thought of almost everything. I'm just wondering if you also account for heating of the hydraulic fluid on longer runs and becoming less viscous. Do you incorporate a fluid heat exchanger? Or do you monitor fluid temp and compensate in the calculations? Or is the temp rise pretty negligible?
Temperature rise isn't a factor. Traditional hydraulic dynos measure power by Flow and pressure, so fluid temperature and viscosity play a role.
That's not the case here. The only thing that matters is the load that is created on the engine and therefore the pump housing, so things like fluid temperature are irrelevant. If it becomes less viscous, I simply increase the pressure to get back to the amount of load required.
frenchyd said:
stuart in mn said:
Very cool project. The thing is it doesn't necessarily need to measure some calibrated horsepower level, as long as it's repeatable so you can tell if you are getting gains or losses from one test to the next.
I had a dyno at the end of my garage. A steep hill that I’d do a rolling start on for consistency. When I crossed the chalk line I’d start my stop watch. The line at the top of the hill I’d stop my stop watch.
Whatever was faster I’d try more of until the stop watch said I was slowing down.
Round and round the block I’d go, stopping in the garage to make adjustments. I’d hit the first chalk line at 5 mph ( 2000 rpm ) and be around 20 mph ( 5000 rpm ) at the second chalk line. Since the car was muffled nobody knew I was doing Race tuning.
That ties in with my next project. I've purchased a bunch of IR beams to setup a makeshift drag strip for go karts.
I've done slow-motion video before just to see how inaccurate stop watches can be.
So I'm going to setup 6 beams. 2 at the start, 2 at the middle, 2 at the end.
The start beams work somewhat simliar to a drag strip. You pull up until you are tripping both beams. When you launch and are no longer tripping the 1st of the 2 beams, the timer will start.
2nd set of beams will be time and mph at half track. You trip the first of the two and it starts a timer. When you trip the 2nd (an inch later), it gives your ET and stops the timer the previous beam started to give you a MPH. (Distance/Time).
3rd set works the same exact way. Trip the first one and it starts a timer, trip 2nd and it gives you ET and mph from the first one.
Fully automated drag strip, zero chance for stop-watch error. 100% repeatable data for testing. I haven't decided if I want to use cheap IR beams or the beams used on garage doors (these are looking promising).
Will probably have to limit the track to 330' MAX assuming I can find an appropriate space.
californiamilleghia said:
Great build !
What compression ratio are you running and is it easy to change it up or down for testing ?
These stock engines are 8.5:1 from my understanding.
I'll also be building a high compression version to show the benefits of octane and cooler burn between a compression ratio where it isn't needed and one that it is.
Wow, that thing is cool. I'm looking forward to seeing some of your experiments.
Doc Brown said:
Wow, that thing is cool. I'm looking forward to seeing some of your experiments.
Thanks. I'm trying to lay out what tests I'm going to do first, since most of them will have to be grouped into a single day.
I'll likely start with something sensible. A test for those who just bought a fresh engine.
The first thing you do when you take it out of the box, before it can be ran? Oil.
I'll test cheap conventional vs conventional with additives vs synthetic vs synthetic with additives.
In reply to AwesomeAuto :
Wouldn’t it be great to see if a 6.5hp Predator is actually 6.5hp?
Somewhat off topic but I have a 13hp B&S for one of my Karts. Can’t wait
ebonyandivory said:
In reply to AwesomeAuto :
Wouldn’t it be great to see if a 6.5hp Predator is actually 6.5hp?
Somewhat off topic but I have a 13hp B&S for one of my Karts. Can’t wait
On an average day, I was getting 6.78 horsepower pretty consistently with them.
When its 40 degrees in the garage, I get 8 horsepower. This is WITH an SAE J1349 correction factor. The air cooled engine was just able to stay much cooler with a cold breeze.
Another major factor I noticed was the air/fuel ratio was quite a bit different in the colder weather. This is one downside of using the carbureted engines on the dyno. There isn't any temperature compensation in the fueling.
That is why when I do a series of testing for say, different oil types or different fuel types, I want to do as many of them as I can in succession to make sure the weather conditions are equal.