[Editor's Note: This article originally ran in the June 2013 issue of Grassroots Motorsports.]
New cars are great. They take advantage of all the latest technology to squeeze out maximum performance, all while providing the appropriate street driving experience for the intended market.
In the case of econoboxes, that usually means great mileage, good handling and a quiet cabin—but only …
Read the rest of the story
I'm in process of making some exhaust for my car right now, so when I read the title for this article:
"Fabricating a Custom Exhaust Header"
I got excited, looking for some meaningful tech tip. But I leave disappointed that the extend of tech tips begins and ends with this phrase from the article:
"Our car rested at the race shop for several weeks as the parts arrived and the crew built our header between their other projects."
sigh.
Best tech tip? Get some header lego like the stuff from Iceengineworks. It'll let you build stuff like this.
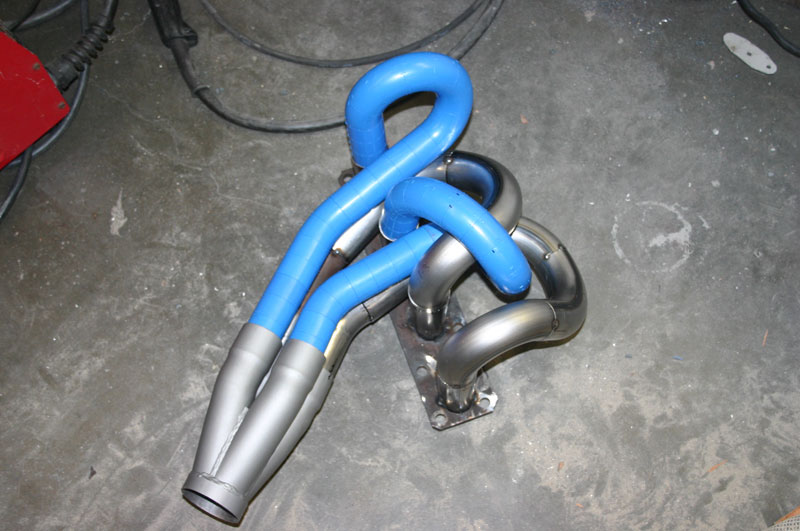
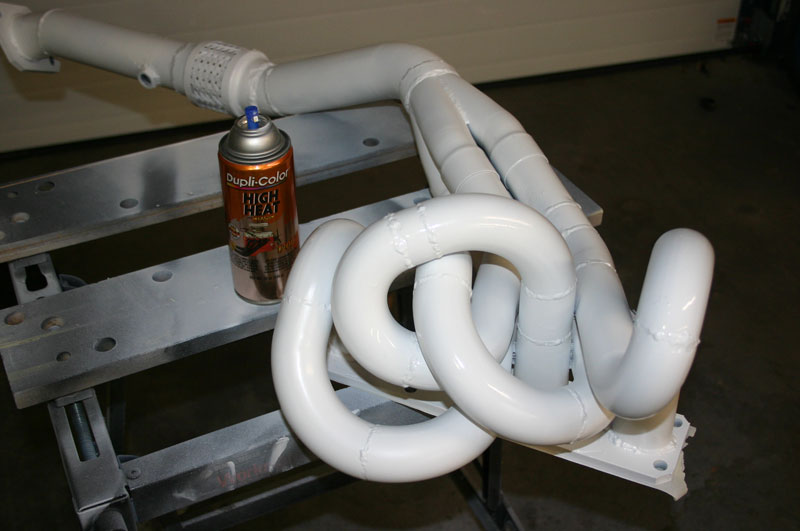
There are stl files out there so you can 3D print your own, but make sure that each segment is equivalent to 1" of tube length and has indexing marks - some of the ones I've seen miss out on these important factors.
Less extreme. This one was heavily space-constrained so equal length runners weren't going to happen.
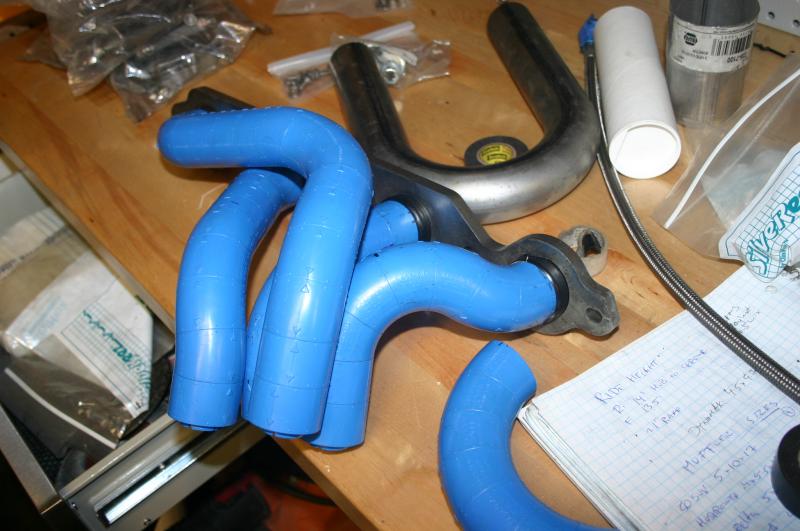
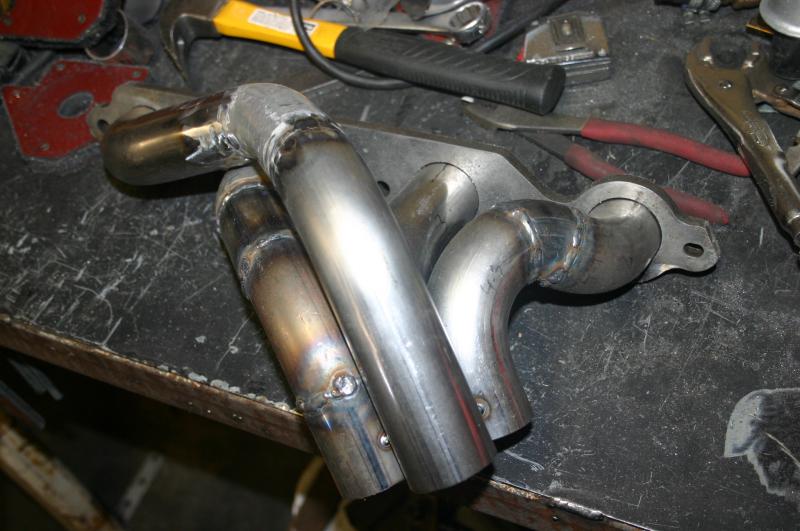
At the typical RPM used on the street there will be almost zero impact in power output.
If you build it for racing you might gain 4% at near peak RPM. But you can quickly kill even that with mufflers and Catalytic converters.
The Biggest gains are typically reserved for V. Engines. V6-8 where there is room to put pulses out 180 from each other.
Frenchy, no. You need to spend some time on a dyno.
Here's that first header I showed in a straight A/B test against an off-the-shelf Racing Beat part on an inline 4 cylinder with a muffler and cat.
http://www.targamiata.com/images_lrg/RB_vs_Keith_header.pdf
In reply to Keith Tanner :
How much power did it gain at 2000 rpm?
If you can't afford to buy or borrow the ICE stuff (which is amazing!) you can use vacuum hose (like for a vacuum) and zip tie welding rod to the outside to get it to hold shape to match your mandrel bends. I have found this method to work "well enough" and you can cut the hose ahead of time to get equal length sections to then try different configurations without cutting into your pile of $ tubing.
What i did: bought a set of used headers. Cut them apart to make them mandrel bends and straight pieces.
Took some 3/8 plate and a lot of time to make flanges for the headers based on exhaust gaskets.
Placed mu collector in the car which was a piece of exhaust tubing.
Bolted the flange to the head. Started connecting the two with the mose cramped tube run. I held the pieces of tubing together during mockups woth painters tape. When i got happy, tacked everything and test fit repeatedly. Adjusted as necessary, numbered and witness marked all the peixes, welded together.
Paul_VR6 (Forum Supporter) said:
If you can't afford to buy or borrow the ICE stuff (which is amazing!) you can use vacuum hose (like for a vacuum) and zip tie welding rod to the outside to get it to hold shape to match your mandrel bends. I have found this method to work "well enough" and you can cut the hose ahead of time to get equal length sections to then try different configurations without cutting into your pile of $ tubing.
I usually start with blue pool hose to get an idea of the rough layout. I did one by beginning with pool hose then using welding rod to come up with the shape. I didn't attach the rods to the hose (good idea, that) but just left the right amount of clearance from tube to tube. I can post pictures if anyone's interested.
Agreed, the name of this article should probably be "How to outsource building a custom header". Maybe add a pic of just the completed header alone lower down too?
The comments section has lots on the subject! Good idea for the welding rod and flexible hose.
It is also smart, if you want to actually mount them on an engine, to put bolts and sockets in the mounting holes as you engineer where the tube go.
I have been known to slot the lower holes so you can fit the gasket and the bolts most of the way on, so you can drop it over the inaccessible ones and only have a turn or two to finish tightening them down. I got this idea from Ford Group A turbos that had three slots and one hole, so service only had to remove one bolt and loosen three. Volvo whiteblock intake manifolds are also set up this way.
I've done a couple. I use tig rods to get a basic layout. The ice Lego things would be great but they are so bloody expensive. Mine come out reasonably well but take a damn long time to get right.
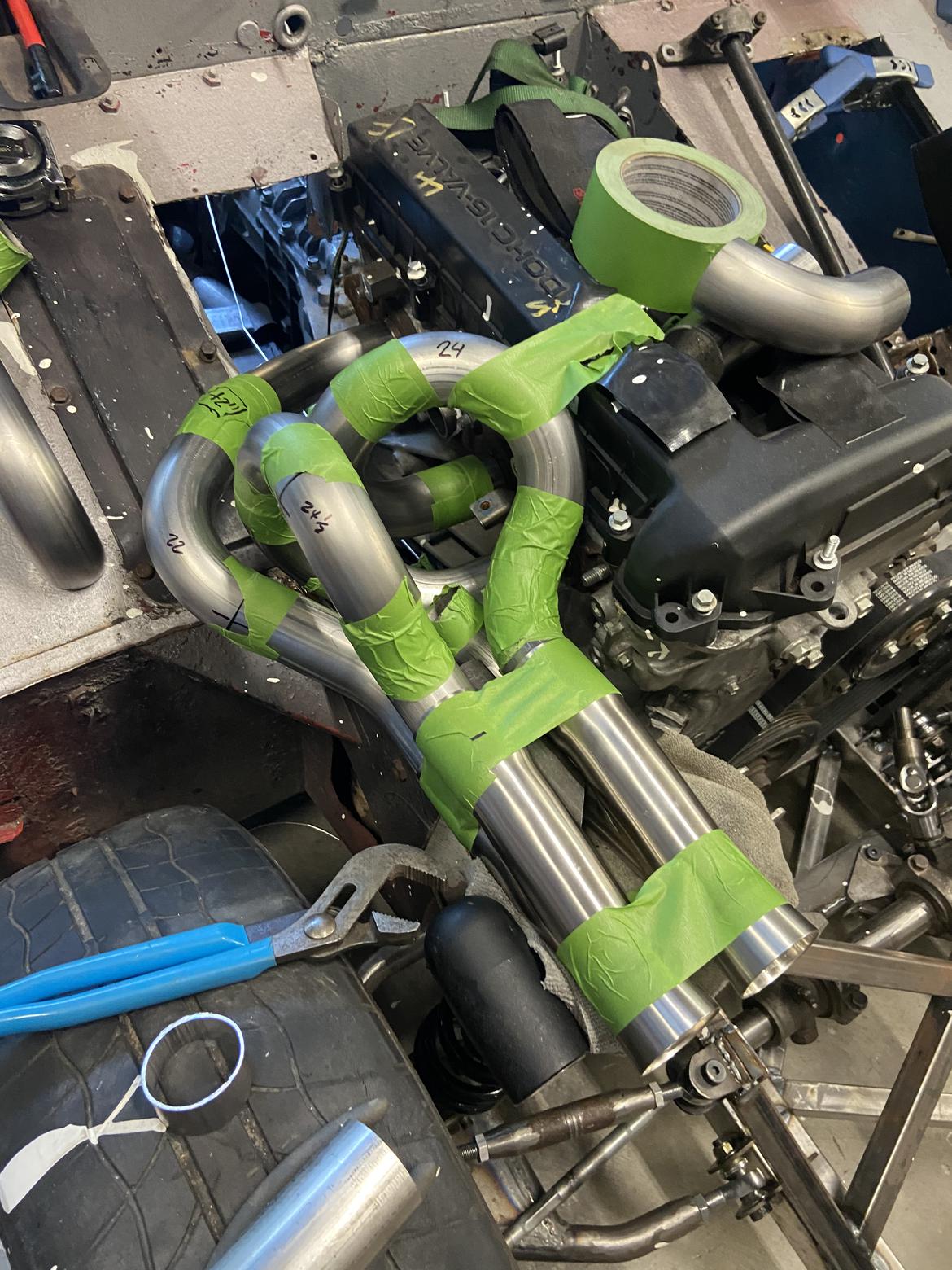
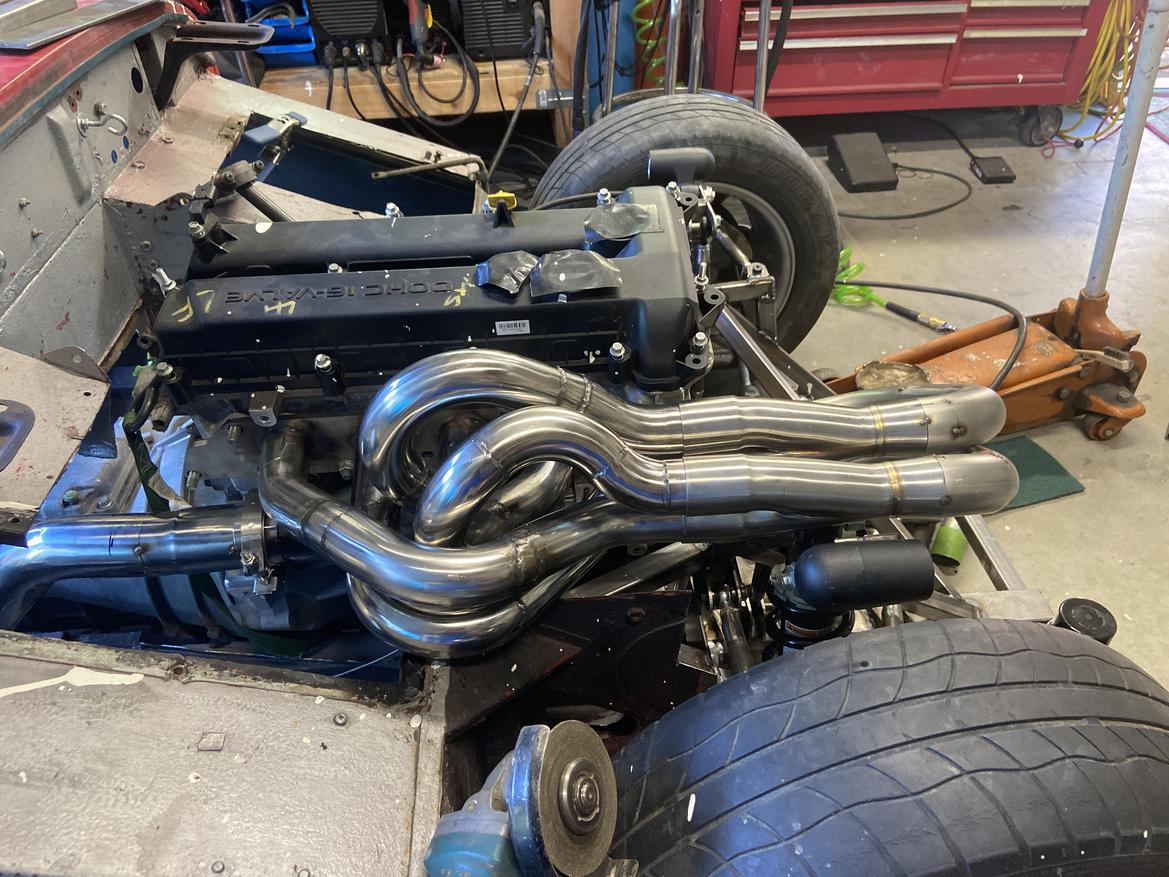
In reply to Teh E36 M3 :
That's a neat way to get around a clearance problem!
GaryC83
New Reader
1/27/22 6:52 p.m.
Another vote for the ICE or printing your own. They work awesome.
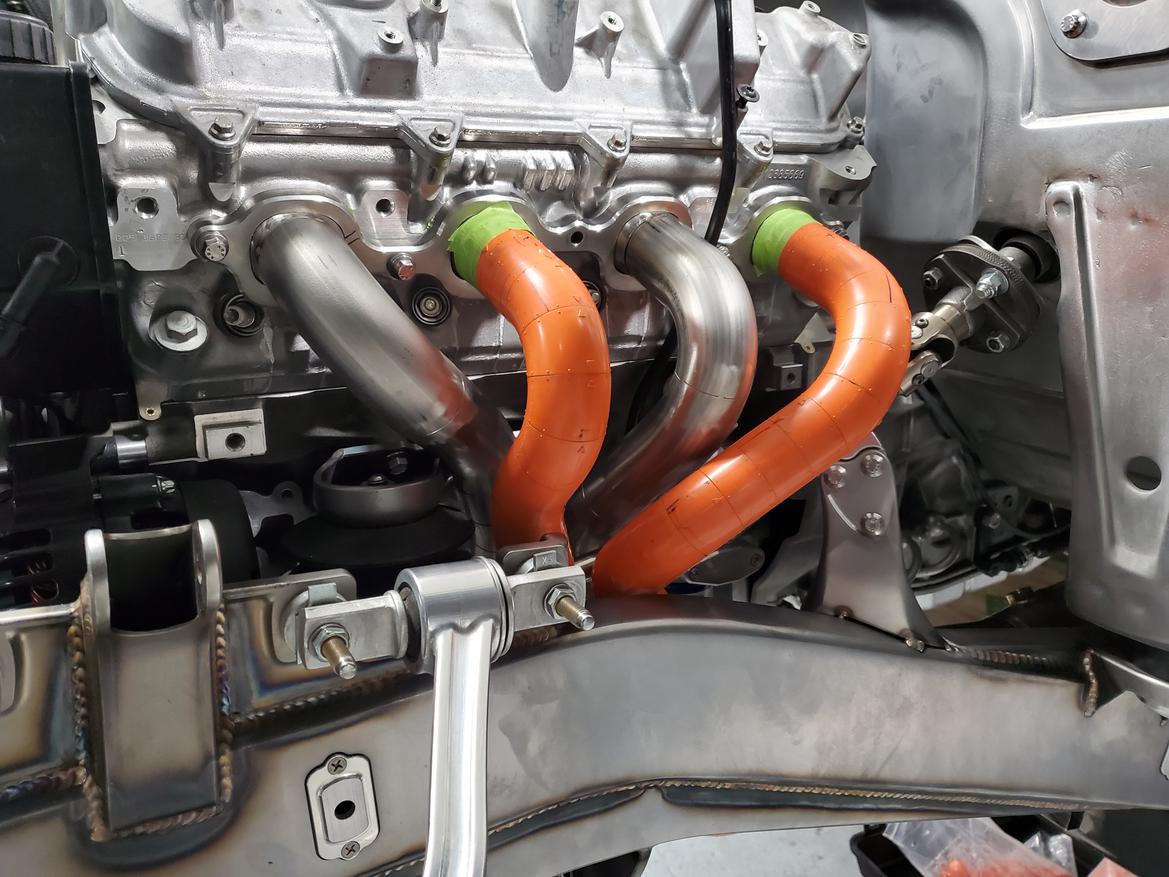
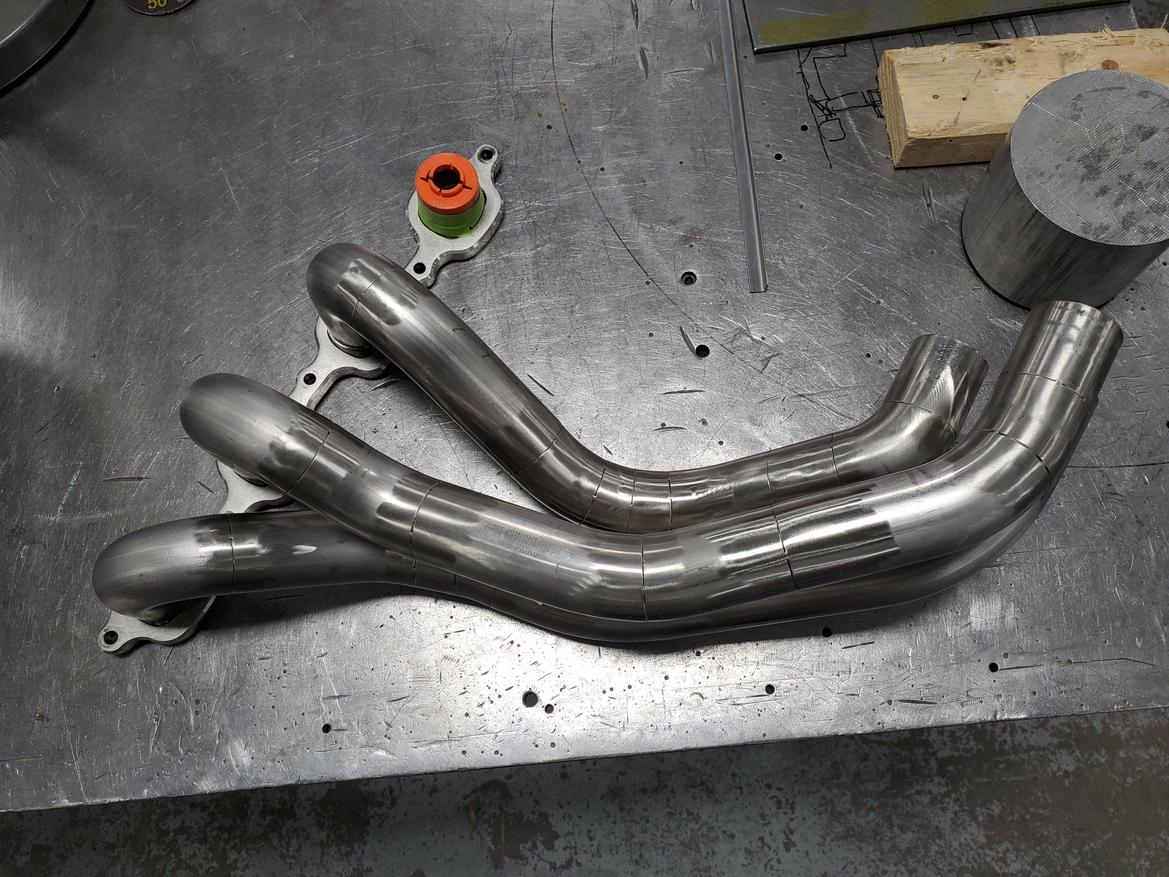
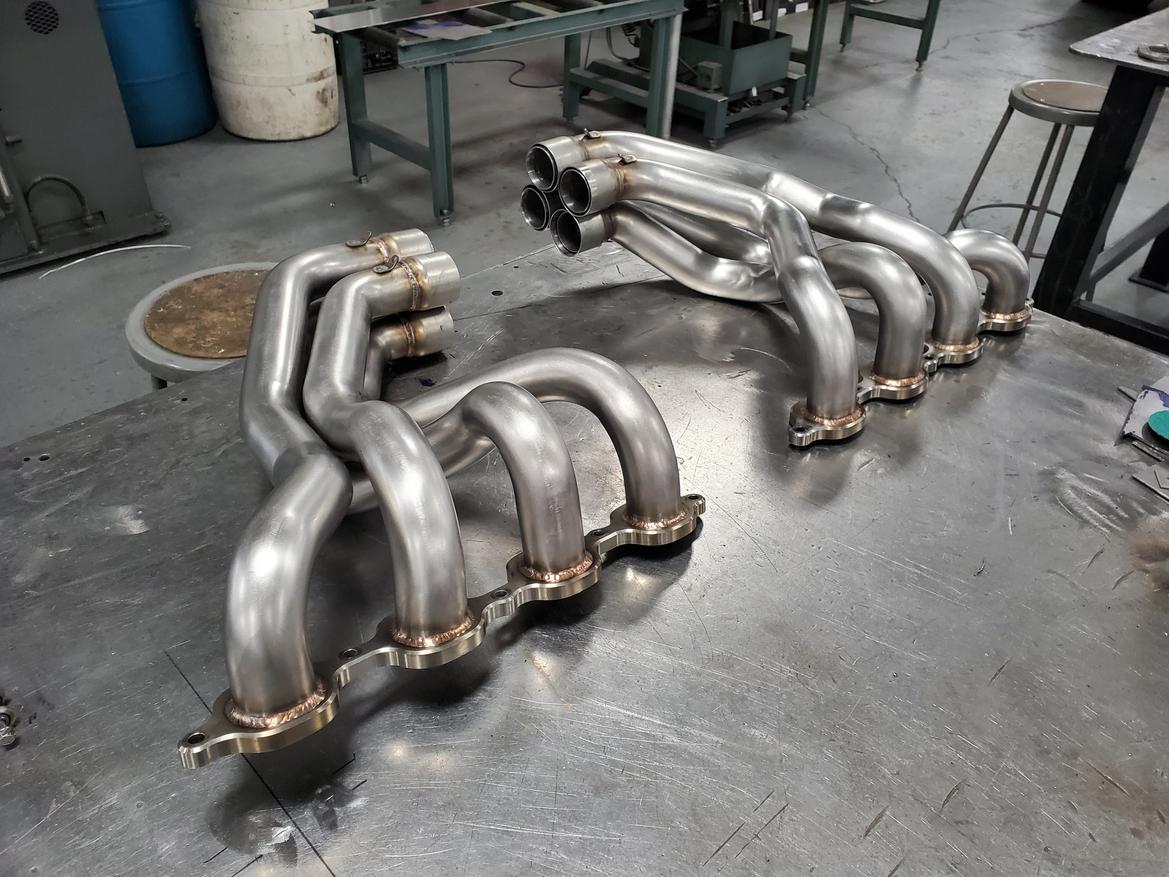
We use them all the time. those are a 'spare' set of tri-Y merged headers i did for a stroker LT1 that went in a 41 chevy We built at the shop. We also fabricated a set of polished 180's for it as well.
God, Gary, lots of pretty welds on that project. Nice work.
Teh E36 M3 said:
The ice Lego things would be great but they are so bloody expensive. Mine come out reasonably well but take a damn long time to get right.
That gets into the "time is money" discussion. If you're doing this for other people, buying the expensive tools can save you a lot of cash.
The cost of the ICE has dropped quite a bit since the initial release, it's worth checking them again. They have some nice touches I haven't seen on all the DIY 3D printed ones - each piece is 1" long so you can easily meet your calculated lengths, and they have index marks on them so you can easily clock them. No reason those couldn't be in the printed version of course, so I'd look for those attributes if you're going to make your own.
The sexy header stakes in this thread have been raised considerably.
GaryC83
New Reader
1/27/22 7:22 p.m.
In reply to Teh E36 M3 :
Thanks. Firewall forward is all pretty much custom fabricated. We start with AME rails and modify the hell out of everything. I built pass thrus and inner bracing into the frame kick outs I did for radiator clearance. Built the steering support, frame braces, we CNC'D the upper control arm mounts and I relocated them back and in for more caster and camber. I built the upper coilover mount for running longer travel coils than they come with from AME. This one runs TracTiv electro-hydraulic shocks. And on and on. Its a nice piece. Quick little link on the car. Adam worked magic on the sheet metal and everybody else at the shop had a big hand in it as well. It was a very large project, to say the least.
https://fuelcurve.com/goodguys-2021-classic-instruments-street-rod-of-the-year/
Wow man. Wow. I hope the owner drives the ever loving E36 M3 out of that, but I suspect it will see mostly shows.... can't blame them for that either, I wouldn't want to screw up that art.
Keith Tanner said:
Teh E36 M3 said:
The ice Lego things would be great but they are so bloody expensive. Mine come out reasonably well but take a damn long time to get right.
That gets into the "time is money" discussion. If you're doing this for other people, buying the expensive tools can save you a lot of cash.
The cost of the ICE has dropped quite a bit since the initial release, it's worth checking them again. They have some nice touches I haven't seen on all the DIY 3D printed ones - each piece is 1" long so you can easily meet your calculated lengths, and they have index marks on them so you can easily clock them. No reason those couldn't be in the printed version of course, so I'd look for those attributes if you're going to make your own.
The sexy header stakes in this thread have been raised considerably.
100% Keith. I'm not doing production, nor am/was I on a time schedule for that. Also, I found the problem solving quite fun. Getting them as pretty as a real shop is a real challenge and I failed every time, but perfection, unattainable, pretty good, not too hard, and maybe get a little better every time.
GaryC83
New Reader
1/27/22 7:33 p.m.
Teh E36 M3 said:
Wow man. Wow. I hope the owner drives the ever loving E36 M3 out of that, but I suspect it will see mostly shows.... can't blame them for that either, I wouldn't want to screw up that art.
Quite the opposite. He's already driving the hell out of it. He's one of the best sources for feedback on what works and doesn't work chassis and engine development wise. The 40 we built for him, he has 50k on. He drives the wheels off the stuff. Most of the stuff we build gets driven to E36 M3. It's part of why I jumped at the chance to work here... world class cars, meant to be and actually driven. Its not unusual for us to put 500-1000 shakedown miles on them before they go home. Honestly.
Double badass! You never know, and it would be a shame to put a ton of work into an excellent suspension to only have it parked. So while I probably will never be able to afford the kind of work you do, I'm glad those who can drive them.
In reply to GaryC83 :
wow dude that thing is beautiful!