Machine shop went a bit too aggressive on this flywheel. I had told them to turn it down to the diameter of the clutch housing. They went about 1/4" further. As a result, the clutch housing overhangs the flywheel mating surface, and the bolt holes & dowels are really close to the edge. They did balance & surface it.
Would you run this?
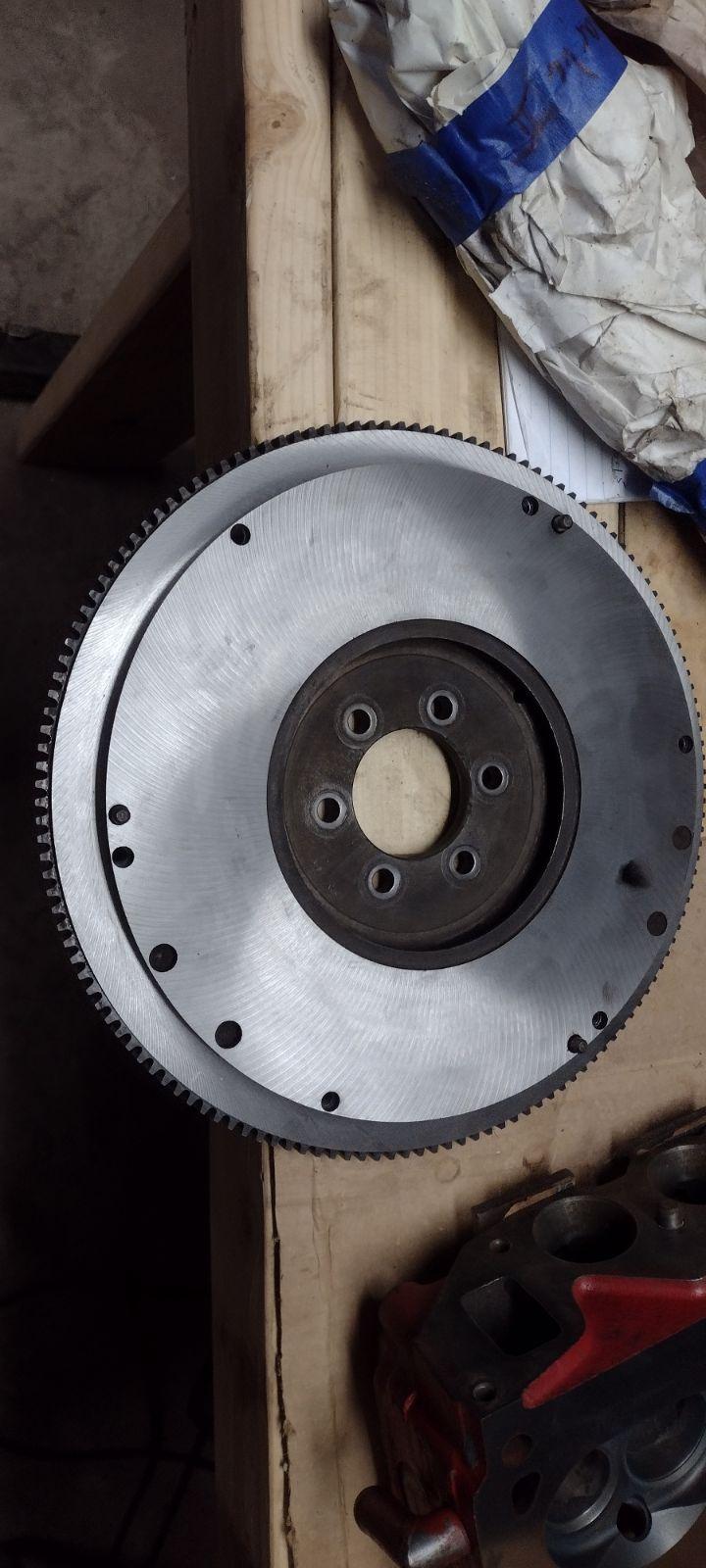
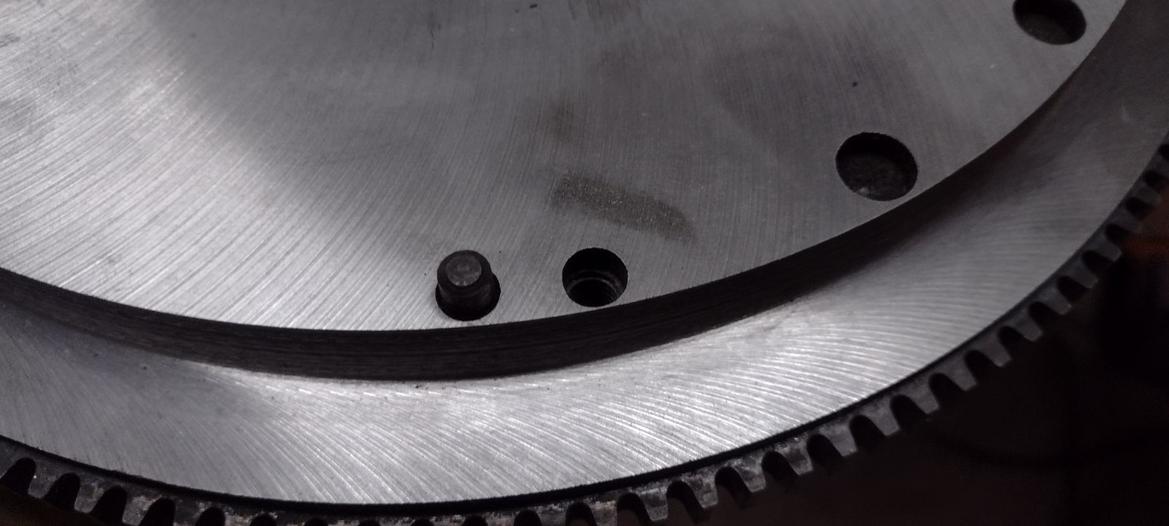
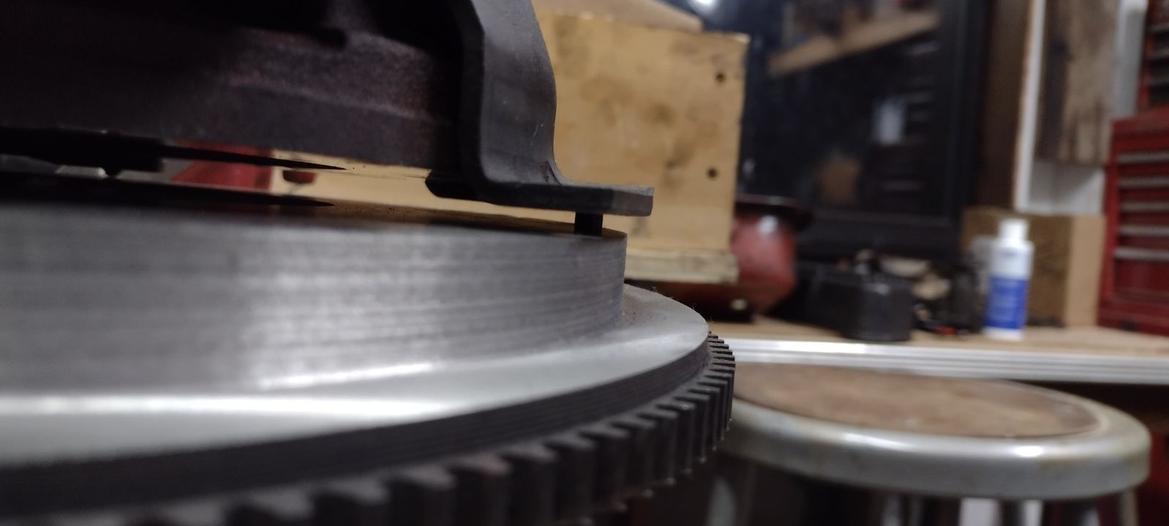
Personally, unless I'm broke, I'd get another. The bolt holes will crack when you go to torque them.
Where the vertical and horizontal edges meet on the cut areas, is a tiny radius. Stress concentrator. You want a generous radius so cracks don't have a place to start.
As a (mechanical) engineer: Unless you're putting uber power through it or revving it to the moon, I'd run it without giving it a second thought.
In reply to BA5 :
ME here myself. I generally use the rule of thumb that you leave at least half the hole's diameter worth of "meat" between the edge of the hole and the edge of the part. In this case, the hole is 5/16", so I wanted 5/32" of meat. That being said, I realize that almost all of the forces on the bolts and dowels will be circumferential, not radial. My main concern is, as Ranger50 said, that something cracks when it's torqued.
Maybe I just need some longer bolts, to grab more threads.
In reply to volvoclearinghouse :
I wish it had a c hair more meat. What about a dbl ended stud with some red loctite?
In reply to Ranger50 :
Me too. I'm going to check and see if I can tap the hole deeper. IIRC it goes thru the flywheel, so I could maybe tap it into the meatier part of the flywheel.
I would run it but tap the pressure plate mounting holes all the way through just for good measure. Honestly I wouldn't give it a second thought.
Driven5
PowerDork
2/21/24 12:04 p.m.
After drilling and tapping through, and adding sufficient length bolts, if that creates enough additional engagement you could also drill out the threads in the step to keep the stress out of that area.
The bolt forces of concern are axial, rather than radial or circumferential. They only serve to provide the clamping that creates the friction that the rest of the forces are reacted through. The dowels are for alignment only and should not be seeing any forces of concern.
I have no idea what the vehicle is or what it will be used for.
A couple of the ideas here sound workable in a fairly light duty application.
Have you heard the sound of a clutch dismantling itself?
Do you have a scatter shield?
Do you want to think about the what ifs as you are driving the vehicle?
Driven5 said:
After drilling and tapping through, and adding sufficient length bolts, if that creates enough additional engagement you could also drill out the threads in the step to keep the stress out of that area.
I had the same thought. Thanks for confirming.
L5wolvesf said:
I have no idea what the vehicle is or what it will be used for.
A couple of the ideas here sound workable in a fairly light duty application.
Have you heard the sound of a clutch dismantling itself?
Do you have a scatter shield?
Do you want to think about the what ifs as you are driving the vehicle?
Volvo Amazon. 2 liter engine, ~130 HP.
Used for LeMons racing.
I've never had any sort of a clutch failure on any car.
No scatter shield. Max RPMs about 6000.
In answer to the last question.....an emphatic NO!
Driven5
PowerDork
2/21/24 12:30 p.m.
Is the flywheel forward of your feet in the car?
Follow up question: Do you want to hear the sound of a clutch dismantling itself at 6000 rpm?
I had a 4 cylinder roundy round race car for a while. The track required a scatter shield. The prior owner made an inexpensive scatter shield by bolting some very thick rubber to the bell housing.
Would a replacement flywheel cost more or less than a scattered clutch?
I'd get a new flywheel. That one is weaker plus that 90 degree cut is a stress riser attractor.
Something flies apart at 6000 rpm and your feet may be in the trajectory of the flying parts.
Driven5
PowerDork
2/21/24 1:34 p.m.
On the one hand, getting the threads below the step *should* alleviate the issue, and I know there have been, are, and will be way sketchier lightened stock flywheels being used in other (including race) cars out there without apparent failure.
On the other hand, racing is exponentially harder on flywheels than street use, and they are very dangerous if they do let go.
For a street car, I'd probably run it with the noted changes. For a race car, replacing it seems like cheap insurance.
Mostly, I'm irritated at the shop for not adhering to my instructions. I have spare flywheels, I've asked them if they will redo it correctly.
volvoclearinghouse said:
Mostly, I'm irritated at the shop for not adhering to my instructions. I have spare flywheels, I've asked them if they will redo it correctly.
I think this is the way. Yours doesn't look to have a whole lot less meat around the bolts than mine, but that plus the lack of a radius on the lightening cut doesn't inspire confidence. You want to feel good about the buzz saw by yer feet.
If they're redoing you could also take a little off the inside of the flywheel, too. Much less important than the outside but it's there.
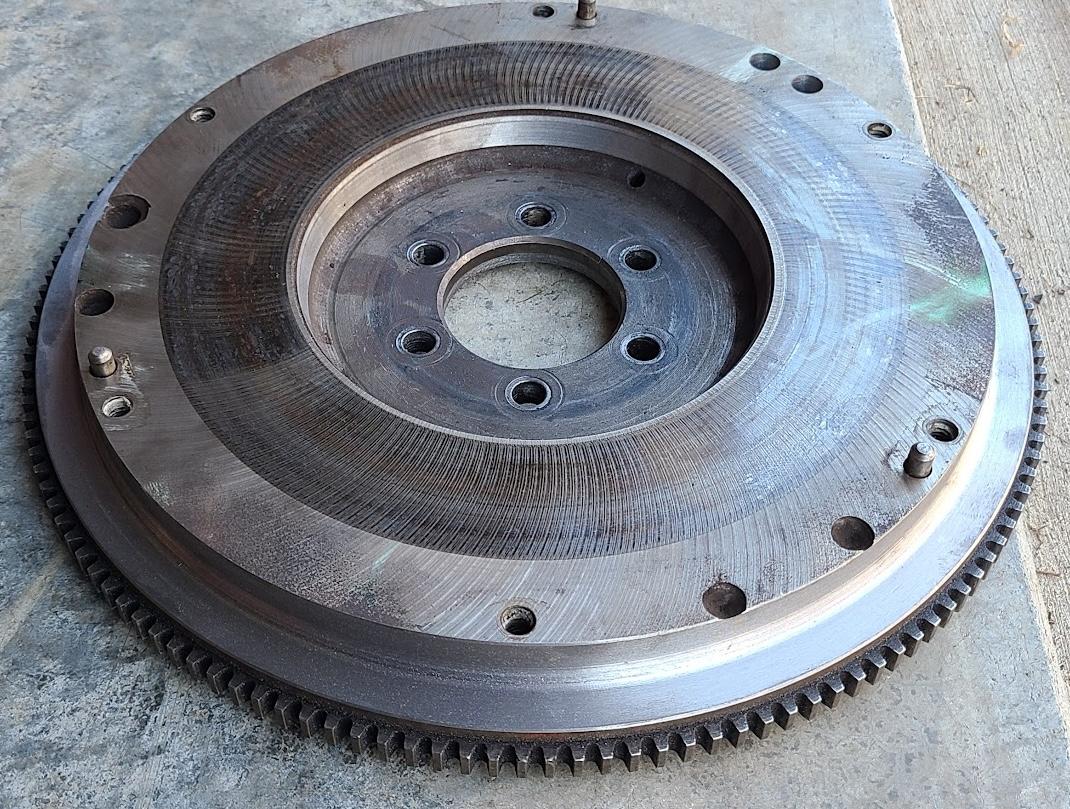
Scatter shield was my first thought.
Last night I put a bolt in one of the holes. Man, it's close. The bolt really shows you how close.
Haven't heard back from the machine shop yet. I'll ping them again tomorrow if I don't hear back. It is lucky I have a bazillion spare flywheels laying around, or I'd be more pissed than I am.
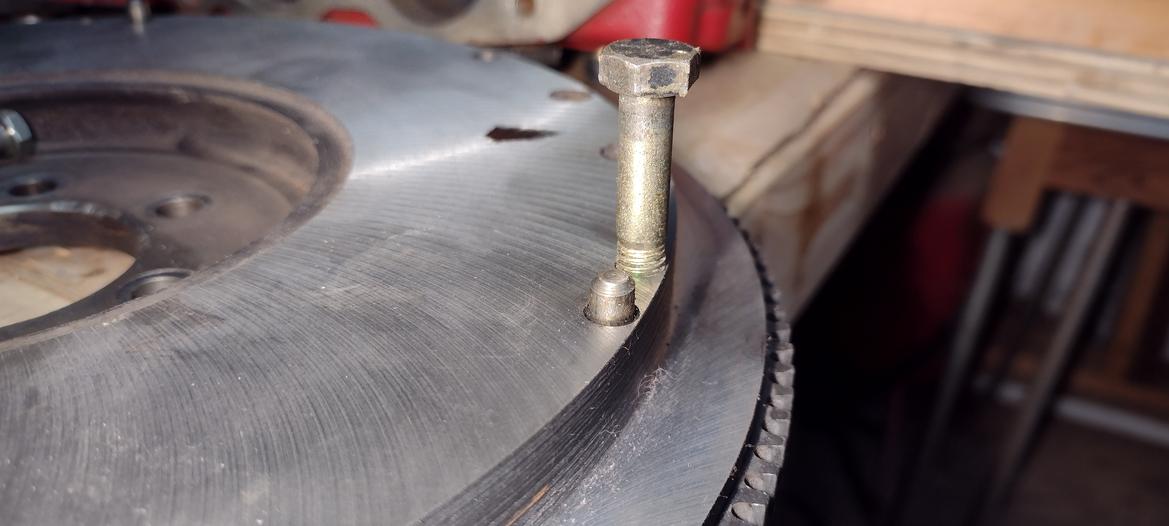
In reply to paddygarcia :
I could live with yours. There's at least something between the edge of the hole and the edge of the flywheel.
tuna55
MegaDork
2/22/24 10:20 a.m.
I don't think I would run that, but I am a bit of a pansy. You could maybe redrill the bolt pattern inboard another 1/4" in another clock location, rotate it all axially by fifteen degrees, but that would require the same from the mating parts. I'd likely only do that if this was precious. If not, paint it gold and hang it from the window of the machine shop that did it for shame.