Ian F (Forum Supporter) said:
In reply to Tom_Spangler (Forum Supporter) :
Did you do a moisture test on the concrete? I did one years ago on my ex's garage floor. It failed badly. She still wanted epoxy and bought a bunch of DIY kits and went through all of the processes to prepare it. It looked great for a while, but eventually failed in spots. She doesn't care that much "with a few chips, it just looks like a well-used garage.... and it still keeps the dust down and is easier to clean."
Under-slab moisture will eventually cause epoxy to fail. Sometimes a deep-penetrating seal coating prior to the epoxy will help. Sometimes not.
No, I didn't. Maybe that would have helped, though there is one area where water tends to pool when you park a wet or snow-covered car, and that part is still holding up fine. I would think the moisture would be the worst there. Though, I suppose if it's coming up from underneath, it wouldn't make much of a difference.
SV reX
MegaDork
2/21/24 10:38 a.m.
In reply to Tom_Spangler (Forum Supporter) :
Makes a big difference.
Water on the surface is where it is supposed to be. It will evaporate, and will not affect the epoxy bond.
Water coming up from below is not supposed to be there. It is trying to evaporate but can't. The epoxy acts like a vapor barrier and the moisture is stopped right before it is able to evaporate out of the concrete EXACTLY where it can eventually effect the epoxy bond to the concrete. It will remain there until the epoxy is compromised and the moisture can get out.
Yeah, that makes sense. Surprised that this didn't come up in my research, but yeah.... 
Ah yes, moisture. I got lucky, we has a typical July-August drought, my fresh concrete and yard was crispy dry. Zero failures so far, the concrete failed in one spot but that was my fault, epoxy was still attached.
Tom_Spangler (Forum Supporter) said:
Yeah, that makes sense. Surprised that this didn't come up in my research, but yeah.... 
I stumbled across it years ago on the Griot's website for their epoxy floor kit. They used to have a dedicated web page for it, but now it's part of the instructions PDF. My WAG is most epoxy vendors are in the business of selling epoxy and if everyone actually did a test, they wouldn't sell as much. On the original Griot's web page basically said they are more concerned about making sure you're happy with the product than selling you something that doesn't have a chance. It was a separate "read this first" link instead of just being part of the instructions.
Anyone know about Swisstrax or the other lattice tile products? My garage has epoxy on it from many years ago, it's beat. Wife wants to do epoxy again but I don't love the idea based on what I'm seeing here.
docwyte
UltimaDork
2/21/24 10:58 p.m.
I have a swiss trax knock off. They're perforated, which is great because they're not slippery during the winter or when wet. However, that makes them *impossible* to clean. Pressure washing them just lifts up the dirt underneath. If I had to do it again, I'd pick the solid plastic tiles, that way I'd be able to pressure wash them and then squeegee them off. Or just do an epoxy...
I have a plywood floor in my shop. It is a coverall building that was supposed to be temporary but it has done amazingly for 17 or 18 years now. I poured a 10 by 15 slab in the doorway for heavy equipment and the rest is poly under 2x4's laid flat and infilled with 3/4 inch cracked rock, covered with 4x8 x3/4 inch sheets of D grade plywood. Right now my 32,000 pound Wanderlodge is in there and it will not compress a bit. And it is very easy on my knees which is a bonus.
I ended up going with the Flex Nitro Tiles for my almost 1000 sqft garage. I did it for a few reasons. I didn't need to completely empty my garage to do it, easy to DIY in a weekend, and if a tile gets damaged cheap and easy to replace. I haven't sealed it yet but so far very easy cleanup and it isn't slick. It was $2.67/sqft so fairly inexpensive for the quality and look I was going for. I'll go into more detail in my garage thread soon.
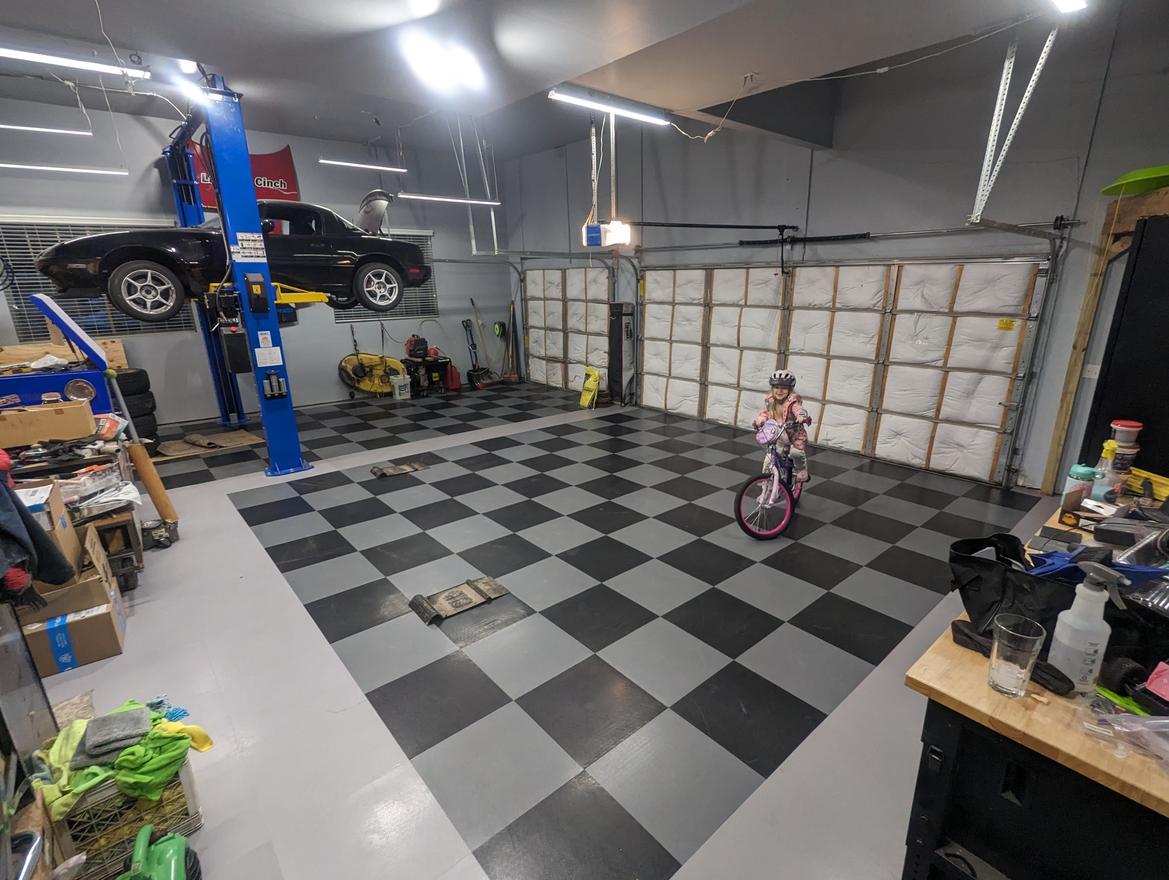
For a garage that old I would keep the budget low. 30 years ago I put Behr sealer on and then a stain. It was a new floor and extremely smooth surface, the guys spent an hour polishing it. Not the floor is pretty beat up but no peeling or lifting despite all the years of abuse. Not sure what the prep for an old floor would be but I trust these guys to do it right.
I may tile my house garage, not ideal for a working environment but to park on looks good and cheap it's a win. Down side is the install. Am I wrong?
SV reX
MegaDork
2/22/24 8:05 a.m.
In reply to akylekoz :
You're right. Downside is definitely the install.
(and the filthy grout after a year)
In reply to bearmtnmartin (Forum Supporter) :
That sounds similar to what I want to do in my garage to "recess" my two scissor lifts. 2x wood under the heavy load areas and foam board insulation in between. Then covered with 3/4" plywood and topped with either another layer of plywood (painted white or gray) or perhaps some brand of high-traffic laminate flooring system. This should get the finished floor high enough that I will not longer need long ramps to drive over the lifts. My garage isn't very big, so cost isn't the biggest deciding factor other than I nixed the idea of creating pits for the lifts.
SV reX
MegaDork
2/22/24 8:15 a.m.
bearmtnmartin (Forum Supporter) said:
I have a plywood floor in my shop. It is a coverall building that was supposed to be temporary but it has done amazingly for 17 or 18 years now. I poured a 10 by 15 slab in the doorway for heavy equipment and the rest is poly under 2x4's laid flat and infilled with 3/4 inch cracked rock, covered with 4x8 x3/4 inch sheets of D grade plywood. Right now my 32,000 pound Wanderlodge is in there and it will not compress a bit. And it is very easy on my knees which is a bonus.
Infilling between the 2x4's with rock is a great idea!
SV reX said:
bearmtnmartin (Forum Supporter) said:
I have a plywood floor in my shop. It is a coverall building that was supposed to be temporary but it has done amazingly for 17 or 18 years now. I poured a 10 by 15 slab in the doorway for heavy equipment and the rest is poly under 2x4's laid flat and infilled with 3/4 inch cracked rock, covered with 4x8 x3/4 inch sheets of D grade plywood. Right now my 32,000 pound Wanderlodge is in there and it will not compress a bit. And it is very easy on my knees which is a bonus.
Infilling between the 2x4's with rock is a great idea!
And the plywood floor would be far softer, and nicer on your feet! I remember learning about old factory floors (like 1900 old) would use the charred ends of wood pieces chopped into tiles. Something about standing on the wood with the grain gives it flex.
Old factories had hard wood blocks stacked tight with the end grain facing up. Very durable, just don't let water set on it for an extended period of time, it will pop up and never go back again.