So here is my 3rd attempt at building a Mold from which I can create carbon fiber composite warm and cold air intakes. This one will be model specific,as I am just getting my feet wet. But if it works out the way I plan, I will be able to make kits that can be used universaly similar to arranging different degree mandrell bent tubing to build custom intercooler setups etc. So far, I have only gotten this done, but you gotta start somewhere right
I will update with more pics as she rolls along
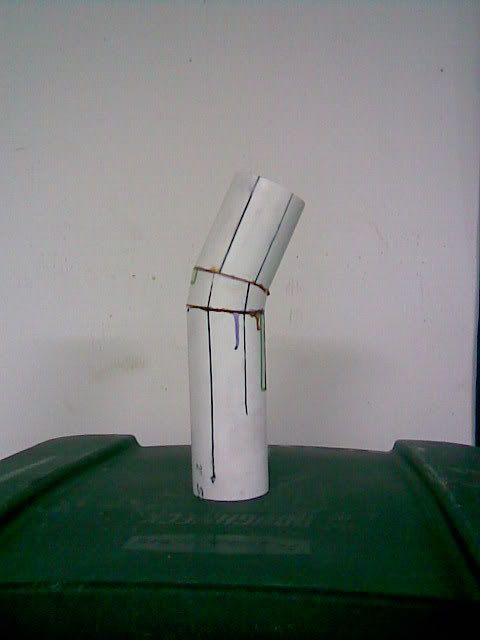
mw
Reader
2/26/09 10:22 a.m.
Do you have to destroy the mold to get the part off?
A few years ago on either discovery or PBS there was a show about amateur rocketeers- pretty cool to be a rocket scientist as a hobby...
Anyway, they did a profile on one group that quickly put a carbon fiber rocket together- they wrapped a clean used carpet cardboard tube with the fabric and correct epoxy, and then looked like they wrapped it a few times in a mylar like material- when heated, it compressed the mat incredibly tightly onto the tube.
Put into a home made "oven" which was a long box with reflective insulation and a bunch of heat lamps, and let it cure. Basically, it was just like vacuum bagging in a autoclave (I think)- and it came out perfect. To get the mold out, a few hours in a pool dissolved the cardbord.
It was pretty sweet fabrication for a carbon fiber rocket. And very, very grassroots.
I would imagine that a similar mold made out of uncured plaster (that would dissolve in water, but not cure at the baking temp) would work quite well.
Something to think about...
Eric
At first, I experimented with trying to create an inflatable mold (kinda like a water toy or the like) that could be deflated and removed once the piece was cured...indescribable failure. I also tried to make a straight beice, and cut out wedge shaped sections leaving only a "backbone" that when bent, created the curve, and then laying up more glass around the cuts. More failure, and incredibly time consuming. Also, the real killer is that multiple layers trying to dry at once causes gass bubbles between the layers that look horrible (form is as important as function to me...horespower only slightly better than eye canby where composites are concerned
), so vacuum bagging or similar is definitely needed.
Then I came up with a little more feasable plan...This mold is just PVC pipe...cheap, easy to cut, and epoxy doesnt bond well making it a great mold material(also, rubbing with a bit of carnuba is an grassroots mold release technique Ive seen used a lot), . I will wrap only 1 or 2 layers of epoxied (wet) fiberglass cloth around this, wrap in large heat shrink tubing, and let it cure, then slice longitudinally through the piece with a razor blade. It will be flexible enough to remove without damaging the piece, and still be rigid enough to hold its shape, and the mold will be fine if not for a few lil razor marks. Then use a lil More epoxy to seal up the slice.
Next, wrap the piece with actual carbon about 5 layers...epoxying each layer with a roller, and apply. once again, wrap with large heat shrink tubing to remove unecessary epoxy, and let cure. Once its done, trim edges, insert bungs for EGR equipment and epoxy into place. Bam... done GRM style
I would like to subscribe to your newsletter.
Umm...so would I. Thanks for offering to keep us posted on this!!
If you are going to make multiple copies of the part, then make a mold off the pipe using fiberglass and cut it in half with a bandsaw. Then pop out the PVC and use the fiberglass form to make a 2 pc female mold. Have it bolt together or clamp together. Fill the fiberglass mold with a liquid expandable foam (kinda like the spray Great Stuff you get at Home Depot). Make sure that it is a foam that is solvent dissolveable and fairly ridged when cured. Then use a wet layup on the carbon fiber and after it is cured, pour some solvent into the foam and then wash it up.
I have been working with a composites quite a bit with the Formula SAE. We have been using machinable wax to make composite parts. It is great. It is amazing as you can machine it into any shape you want and once you have melted it out you can reuse it.
For tubes, you can get CF sleeving. Wet it out inside a tubular split mold and inflate a polyurethane condom in it...
Thanks for all the suggestions. I have looked into many of these Ideas. Ive thought this out a lot and the idea of the dissolveable(foam) and meltable(wax) ideas were intriguing, but very labor intensive. same with the 2 piece bolt up mold idea. This is my 3rd attempt at this idea, and Im learning a bit each time. I get a new idea from each failure (reminds me of those Dyson commercials where they say they actually like failure because they learn something everytime an idea doesnt work). So Im going to try this current itteration and see where it gets me.
I have seen the composite sleeves, and definitely plan to utilize this in the finishing, but its cheaper to use fiberglass cloth initially since I can just go down to advance-o-zone and buy a 2'x4' piece, cut into strips, and wrap it around the mold like a cast on a broken arm. That was actually my inspiration...broke my arm about 10 yrs ago, and remember the cast being cut off and holding its shape. After about 2 layers of fiberglass, slit the side, remove the cast, epoxy the seam, and wrap with about 4 carbon sleeves. The retailer I plan to use is Soller Composites (google them, very simple website, but very knowledgeable and good tech info on their site). They also sell fiberglass sleeves which will be great for cost savings durring R&D.
I will definitely keep everyone updated, I should have an update as I will have some time to put into it this weekend. Stay tuned friends, same bat time, same bat channel.
I've bought fiberglass sleeving from McMaster Carr as well. Dirt cheap for what it is and makes great exhaust wrap too (after the stank cooks off)
Squeeze a bunch of gold silicone onto the cut/frayed end and squeegie the excess out. It will stop it from fraying and holds up well to header or downpipe temps.
OK, here is a new update...I know its been a while, but you cant rush perfection right?
. My thin first layer idea worked like a charm. Separated easily from the mold and held its shape perfectly. Here is the first layer. Im gonna try to wrtap it again tomorrow and have some more pics once its all cured up, probably in a few days.
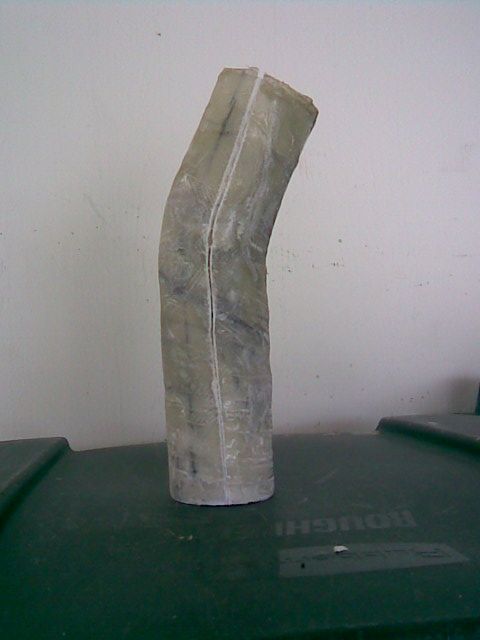
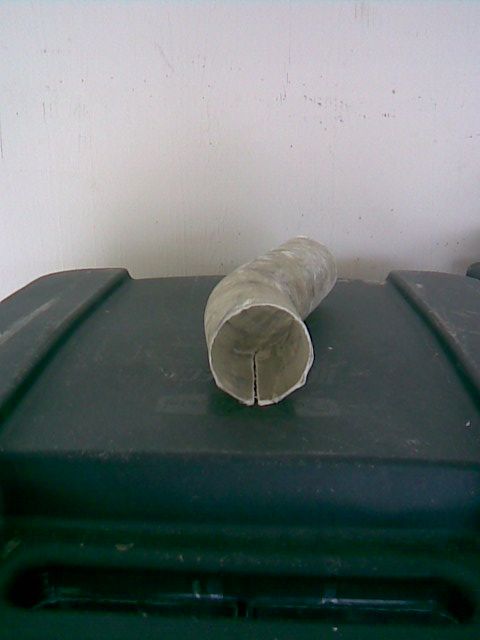
The black lines are from the sharpie I used to get my straight line to cut the strips with, I can make those go away pretty easy, so dont pay em any attention.Also, I really need to use some large heatshrink tubing to get the finish a little more regular. I tried to cut costs with this prototype by cutting some plastic sheeting into strips and pulling it tight around the wet fiberglass, but that was difficult and I dont think it did too much to help. A little more sanding is in order, but better finish wont be too hard.
andrave
New Reader
4/9/09 10:03 a.m.
Hey just a helpful tip, the guys at tapplastics are amazing as far as giving great tech support and insight on the proper use of composites. I've ordered a lot of great stuff from them over the years. I, took, think you could get a much smoother final product from wrapping around something that was dissolvable/meltable... then you wouldn't have that slit you are putting in your current product. Are you designing these pipes solely for CAI, or for possibly forced induction use as well?
Yeah, I have looked into the lost wax idea for casting, and may get to that if my opperation takes off, but for now, PVC is cheap for one off stuff. I wouldnt mind having the opportunity to just have one production cycle that results in a finished product, rather than wraping one layer, wait for cure, cut, wrap more layers, and wait to cure again. Its a good idea, but cost/benefit isnt right for me right now.
And as far as your second question, I will probably just make these for NA for now, Im not sure how many layers I would need for x amount of boost. Plus, I dont want to deal with having to replace parts I sell people if they try to run the turbo out of an Abrahms on their EK civic with my tubing
.
Back in 2002 a friend of mine who was on one of the Carnegie Mellon Buggy teams (think soapbox derby for nerds, 60+ mph gravity pods made entirely of hand-laid CF) invited me to the shop to see if there was anything cool we could make out of the scrap pieces. A battery tie-down seemed like a natural choice. Not sure if any of the steps will help in your application, but I figured I'd throw up the link to my old site:
CF Battery Tie-down
If memory serves, we used six layers of CF, four weave and two straight sheet laid at 45 degree angles. It's still perfectly functional after more than 7 years.

In the above link, Scott Lear wrote:
"Thanks again to the Fringe folks for letting us use your scrap CF! Carbon-fiber hood, here we come!"
Umm...so why havent I seen an article in GRM about that hood?
ha ha
Seriously though, thanks for the link, I also have some little knick knack engine bay hullabaloo swimming around in my grey matter too. Im always imagineering some kinda whatchamadoohickey
If you are going small enough parts, a food saver kit makes amazing vacuum bags. 
andrave
New Reader
4/9/09 11:33 p.m.
Why would you make a gravity powered soapbox type car out of carbon fiber?
Gravity being what it is, I'd think you would want the heaviest car possible.
Maybe craft the body out of lead and the driver out of mcdonalds cheeseburgers or something....
andrave wrote:
Why would you make a gravity powered soapbox type car out of carbon fiber?
Gravity being what it is, I'd think you would want the heaviest car possible.
Maybe craft the body out of lead and the driver out of mcdonalds cheeseburgers or something....
Things that are lighter accelerate faster, yeah everything falls at the same speed regardless of weight (in a vaccum). So a lighter soapbox car will get down the hill faster. lighter wheels will turn faster than heavier ones so on and so forth. plus carbon fiber is cool. uh am I on the right track, sometimes I'm not so bright.
lightness in a soapbox wouldn't affect acceleration. FMI is right, "everything falls at the same speed regardless of weight (in a vacuum)". Inertia and acceleration only vary between 2 objects of varying weight when all else is equal when the 2 objects are grossly different in weight and friction is involved. EX. Mythbusters did an experiment between a hotwheels viper and a real viper in neutral on a slope. The hotwheel took off much faster than the viper...all that axle/diff/driveshaft is a lot to get up and moving in comparison to a tiny toy car with only 4 moving parts. but there is a lot of friction etc involved, so that point is also kinda moot.
Where lightness would be a benefit is friction between wheel and axle. a lighter driver/car has less friction on the wheels and axle, so the car will accelerate faster, all else equal
only on this forum could a thread about a cold air intake end up describing physics in toy cars with no motors
Carson
HalfDork
4/12/09 11:09 a.m.
My question is why would you need a battery tie down on a gravity car?
Carson
HalfDork
4/12/09 11:09 a.m.
Oh, I need to slow down when I read. I see now, made from scraps.
Yeah that's what I meant sheesh
96DXCivic wrote:
If you are going small enough parts, a food saver kit makes amazing vacuum bags.
Damn, I just helped my wifes grandma sell her unopened box foodsaver in a garagesale for 6 bucks...it came with like 40 10 qt bags...that would be more than large enough for half the cooked up stuff Im always dreaming up
I always wondered if they would work...Thanks, even if youre like 7 months late
!
Well, the main reason you want the buggies to be light is because they have to take a corner and then a relay group comprised of team members has to push them back up a LONG hill. Also, there's a right-hand sweeper they take at a pretty good clip. Aerodynamics and low rolling resistance play a key part. It's a pretty awesome engineering exercise, and the races are fun to watch.
Here's an example of the Fringe buggy lineup, along with a typical driver. Again, the buggies aren't very big, and that hill is LOOOONG, so petite freshmen women are typically accosted by the teams early in the semester and convinced that piloting a carbon fiber insane-o-tube would look good on their fledgling college resume. My friend Janice was one of the Fringe drivers back in the day.

EDIT: note, the buggies are on blocks because teams are SUPER clandestine about their wheel choices until the race is on. In many ways, they take secrecy more seriously than McLaren and Ferrari at an F1 race.