Ok, so the other day (in the rain) I pulled on my jag's wiper switch and it felt like it broke internally. Wipers stopped immediately in a non-parked position. Doh.
Last night the kids and I took the switch out, and pieces of copper and plastic were just falling out of the dash. Hmmmmm
After close inspection I figured out the problem. The switch itself is a spring loaded plate that has "mountains" on top so when you move the lever up and down the lever pushes the plate in and out perpendicularly to the action of the stalk. Much like a key in a lock cylinder. The contacts on the switch are fixed, but the plate itself has different copper pieces in funny shapes so that when the plate moves in and out, different contacts are connected.
And my switch hadn't broken at all, but instead the spring action had pushed the case apart. I put it back together and plugged it in, wipers work better now than before. It is clear to me that before the switch finally broke, it was already pushed apart a little bit, and the connections weren't correct. I think this also might have been why the wipers were not parking correctly.
Anyway, that all sounds good, until you see the problem. The case is held together by the metal side having posts that extend through the plastic and then are mushroomed at the top to hold. After the backing plate has already been pushed off once, the holes in the plastic are now bigger. I tried to use the round head of a rivet to remushroom the posts a bit, but I'm not super confident about the hold. How would you hold these pieces together?
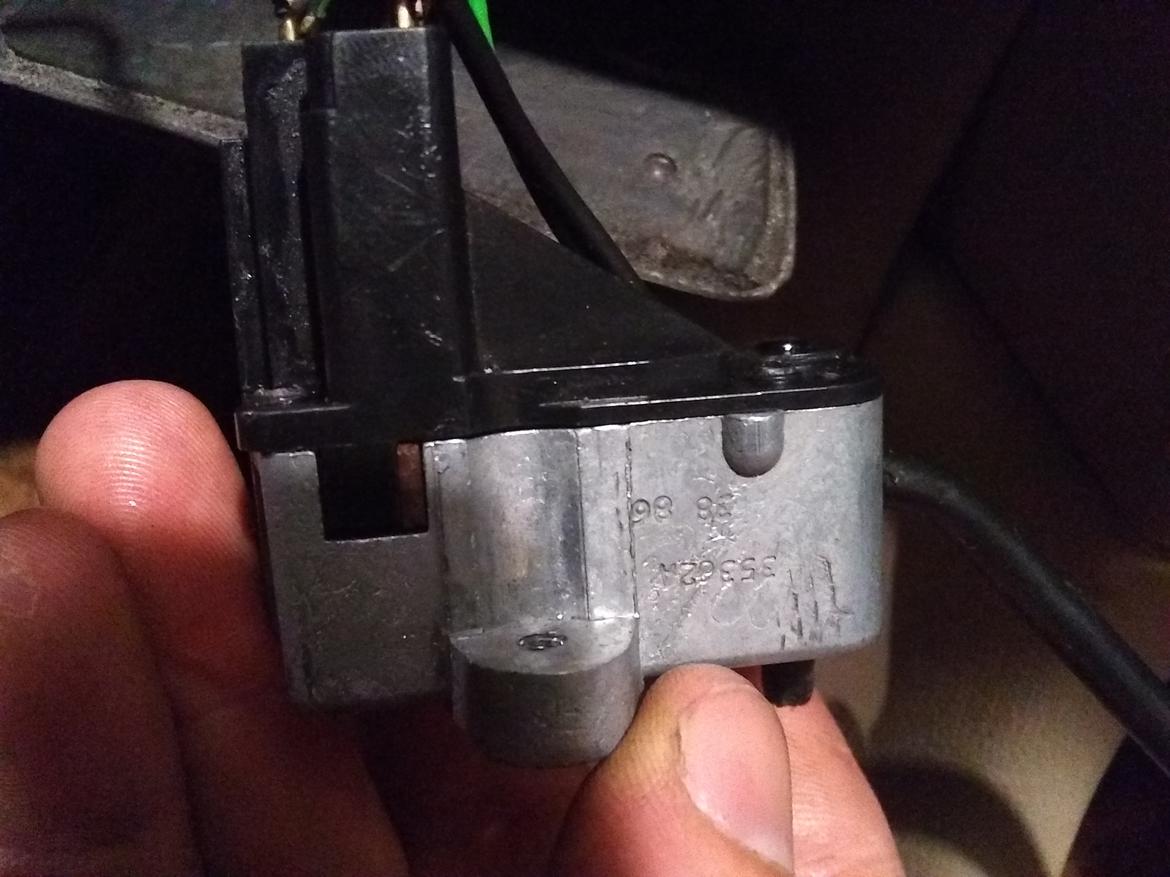
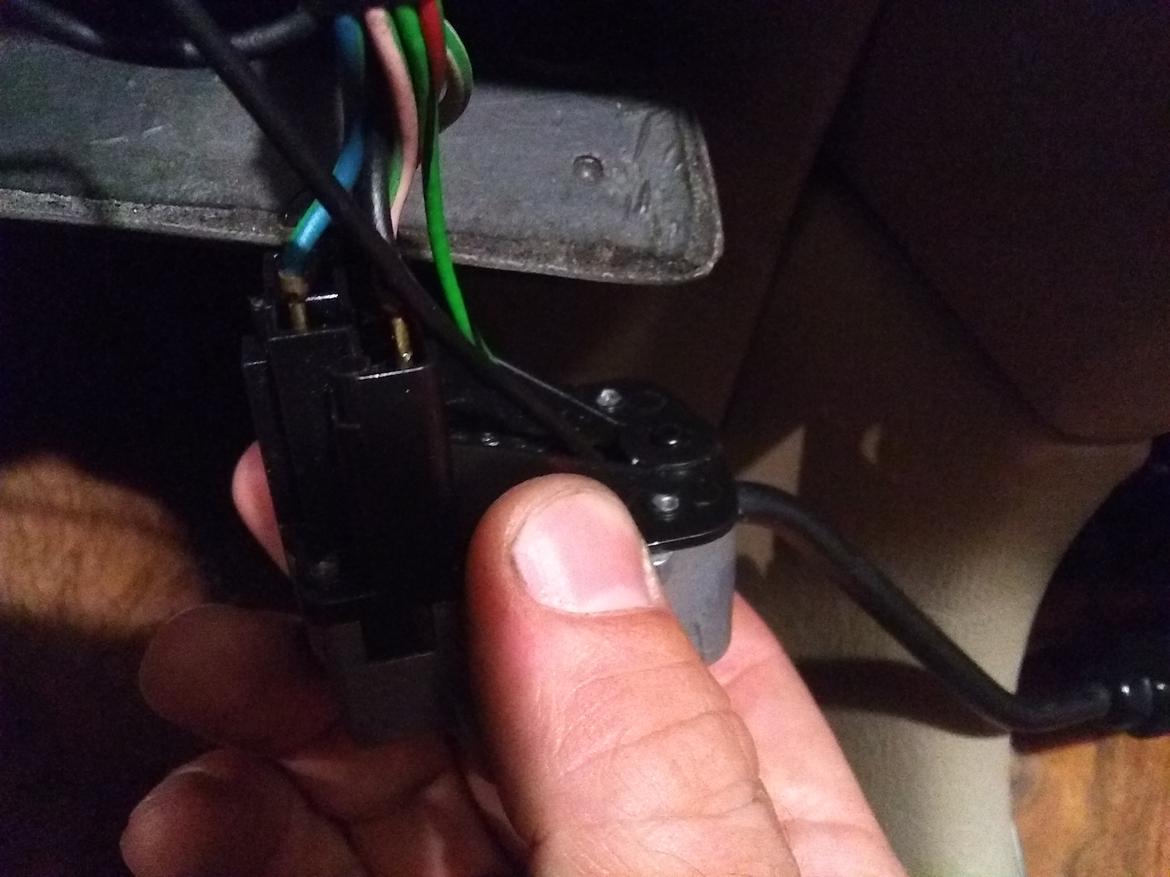
if you can get a washer that just fits over the metal stud, then you can flare the stud further with a small hammer and drift. Maybe even an o-ring would work, depending on the spring load involved.
Another option, and maybe the better one because it is reversible, is to add silicone or an epoxy at teh stud end to hold the plastic case. Since the stud is mushroomed over, it should give a fairly solid mechanical hold.
I was thinking about glueing it back together. But it is full of dielectric grease, and assembly isn't exactly easy because of the spring loadedness of the whole thing. I'm unsure I could keep the parts that need glue clean from grease and vic versa on assembly.
Is there a specific tool or shape to best flare these studs? I can probably make something on the grinder if needed.
I think I would knock the studs off, make then into holes with threads, add screws or rivets.
In reply to Robbie (Forum Supporter) :
Who is your go-to guy for Jaguar parts? Mine used to be Bill Terry from Terry's Jags but lately it's Strandberg Auto up in Centuria Wisconsin
Just tell them what you need and it appears on your doorstep in a few days.
Then start watching Craigslist and Facebook etc for a parts car version to hide under a tarp in the back yard. I caution you about that last step. Stored Jaguars have a habit of rabbit like activity. You can often acquire one for less than the last parts order. "Gee look dear this one has the little picnic tables in the back of the front seats, " or some other desirable doo-hicky.
Hose clamp? Zip ties? Make C-shaped metal spring do-dads that clamp over it?
Is there any room on the front (metal) part to slip something between it and the dash?
Encase the whole mess in JB weld?
frenchyd said:
In reply to Robbie (Forum Supporter) :
Who is your go-to guy for Jaguar parts? Mine used to be Bill Terry from Terry's Jags but lately it's Strandberg Auto up in Centuria Wisconsin
Just tell them what you need and it appears on your doorstep in a few days.
Then start watching Craigslist and Facebook etc for a parts car version to hide under a tarp in the back yard. I caution you about that last step. Stored Jaguars have a habit of rabbit like activity. You can often acquire one for less than the last parts order. "Gee look dear this one has the little picnic tables in the back of the front seats, " or some other desirable doo-hicky.
It's a shame to pay for a new or used switch when mine seems to be working just fine other than holding itself together.
re: screws, I thought that too but the posts are tiny. Like 1/16th or smaller. Not sure I could drill and tap with anything that small without destroying the posts. Maybe I could remove them all together and replace with a machine screw that goes all the way through...
re: external support, can't easily do it because the assembly fits very tightly into the column. So while the switch would stay together, it wouldn't bolt back into the column.
In reply to Robbie (Forum Supporter) :
Could you use a coat of something like JB weld and clamp it together while it dries
they make these wood clamps this brand is called Quick Grip by Irwin in even smaller sizes.
I'm thinking of a skim coat around the top encasing it. If it winds up a little too thick a Dremel tool would make quick work of the excess.
In reply to Robbie (Forum Supporter) :
Is there a specific tool or shape to best flare these studs? I can probably make something on the grinder if needed.
If you can get a washer on there, and the top of the posts are already center drilled, then almost anything that pushes the edges out/down will work. Most likely a rounded over punch or a screw/bolt that has been rounded on the grinder. Basically, make use of the drilled center that already exists to help with the deformation. The original tooling probably used a radiused bit in a press to make the mushroom shape.
Just to round this out - I used a nail set that had been used probably incorrectly in the past and was flattened on the tip a little. and I also increased the size of my hammer. It seems to be holding for now, so I reinstalled and we will see if I need to get back after it later.