ShawnG said:
I learned something today.
The "burning slower" is what was explained to me in tech school.
The speed of the burn is primarly set by the composition of the fuel.
A term used in chemistry is Activation energy, usually noted as Ea. When you look at a graph of an exothermic reaction (like fuel burning), it looks something like this:
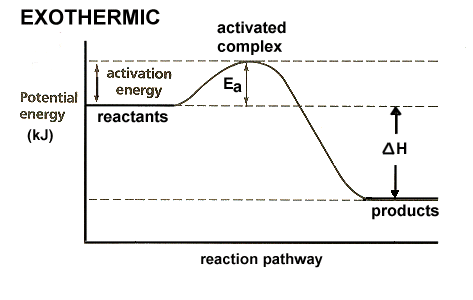
In the case of a spark ignition, the Ea comes from two sources. 1) the compression stroke condenses the heat energy and raises the temperature to a point just before it would ignite, and 2) the spark plug sets things off at just the right time. For a given fuel composition, the downslope (expulsion of energy) after ignition is relatively fixed.
In the graph above, if you increase compression, you are adding to the temperature and concentration of heat energy before the spark and you risk adding enough Ea to ignite the fuel before the spark happens. So, if you can picture grabbing the very top peak of that graph and lifting it slightly, that is what increased octane rating does. It reduces the risk of the compression stroke adding enough energy to the mixture that it ignites before the spark.
In truth, that isn't exactly how it works, but that was the easiest way I could think to describe it. Upping the octane rating effectively prevents the surrounding heat energy from causing ignition before it's supposed to.
Now, using that same graph, imagine grabbing the far right end of the curve and dragging it further right to lessen the steepness of the slope. That would be Avgas and represents a slower burning fuel. In this case, you still get the same amount of energy from the reaction, it just burns slower. Now grab that right side and drag it out even further, AND grab the line that says "potential energy" and raise it up a little. That might vaguely represent diesel. More energy content and an even slower burn.
The slower burning Avgas works with slower-spinning engines like aircraft. As you spin an engine faster, you have less time for the fuel to do its work. If you spun an airplane engine to 6000 rpms, half of the fuel would still be unburnt when the exhaust valve opens because it's taking its sweet time. The other added benefit to slower burning fuels is (if properly engineered) greater torque production. If you think about it, the cylinder pressure has its greatest mechanical advantage on the crank when the rod is at a 90 degree angle to the crankshaft. Depending on the rod/stroke ratio, that usually happens somewhere between 20-30 degrees ATDC. If you match a fuel burn rate to the intended RPM range of the engine, you can tailor when cylinder pressures peak and therefore effect the greatest torque on the crankshaft.
That's also why you don't see many 10,000 rpm diesels :)
So, back to the airplane vs car thing. There are so many things happening with the heat during the compression stroke. The one we're going to focus on is how much heat energy escapes through the chamber surfaces and makes its way to the cooling system. If you have liquid coolant in the head, a lot of heat gets wicked away from the compressed charge. If you have an air cooled airplane engine, the air's ability to remove heat is reduced by a LOT compared to a liquid coolant. Far more heat energy is retained inside the combustion chamber which makes it far more likely to pre-ignite in an airplane engine compared to a car engine. This is also why aluminum heads on cars can tolerate (read: require) higher compression to make the same power. The aluminum is more efficient than iron at absorbing and releasing heat energy, therefore more heat energy "leaks" out before ignition.