So in the world of welding I am but a novice, only mig experience over here, but I can wrap my head around most processes and how they work.
After finally cleaning my exhaust manifold I got a good look at how bad the crack on it really is. All the audi 10vt manifolds seem to crack here, most people just run em till they can't anymore but I'm a little more inclined to do something about it. So whats the best way? I have heard mixed opinions about it, some say run it, others say tig it, and others say it will just crack worse if you try. So what does the GRM community have to say about it? here are some visual aids because we all love pictures 
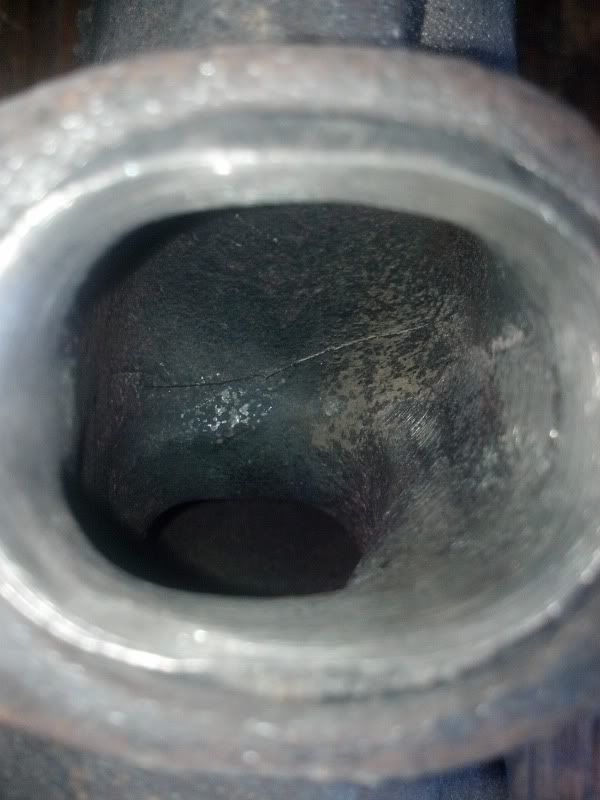
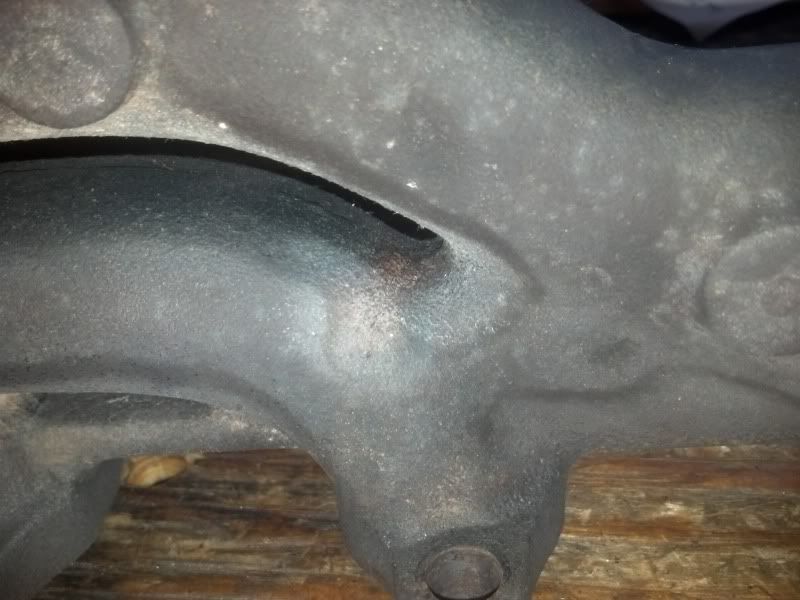
the crack is center frame on this one, not that cobweb on the right
I think brazing is often used for repairing cast iron (one of the exhaust manifolds on my '61 Pontiac was brazed probably 45 years ago and is still working fine), but in general cast iron can be tricky to fix - I'd find a good welder locally who is experienced in this sort of thing.
that is one process I know little about. . . i have thought about subbing it out though, just scared of the price
Wonkothesane wrote:
I haven't done it, but from what I've read, the trick to welding cast iron is to get the iron really hot (in an oven) before you try to weld it..
I am also no pro by any means, but I have heard this as well. LOTS of pre-heat.
Drill out the ends of the crack. Clean. Preheat. Weld with nickle rod. Reheat the area with a rose bud torch tip. Put back in the over to cool down overnight. Buy new manifold.
that a good article. . . bookmarked 
I may have to sub it out after reading that, since my oven only goes to 500. absolute bottom of the reccomended temp for welding it.
I work with some insanely good welders, and wanted them to weld up a cast piece. Most of them didn't want to, but the one that did used those steps, drill out ends, PREHEAT, PREHEAT, and then heat some more, weld, then slowly cool it down. So far no problems.
good to know. . . I have a good friend who is an amazing welder, even he turns stuff like this down. . . haven't asked him about it yet. 
been watching videos on it, wish I had a torch. . .
I just had my cast iron manifold welded before this past year's GRM Challenge.
It wasn't cracked or anything, but i had a steel flange adapter welded to it because i was sick of the bolts backing out.
Dude just cleaned it up good, torched it, used nickel rod, and was done. It's held up perfectly since then.
viking
New Reader
3/27/13 2:08 p.m.
Look for a welding shop in the country. Talk to the old guy who has worked on farm equipment for years-----piece of cake-----
I think a turbo or hard worked manifold will get too hot for brazing to hold up. I would be tempted to just stop drill, tap and plug the holes. It doesn't look like a leaker.
well, I thought the same thing before cleaning it, but just this morning I saw the smallest spec of light thru the lower portion of the crack so if it isn't leaking yet . . . it will.
whenever I see a cracked manifold I think of a good friend of mine who had an '88 ranger 2.3 way back when. . . . it always sounded bad but one day it sounded really bad. . . no power. . . we finally decided it was time to take it apart, after removing the heat shield that directed hot ait into the airbox we found a hole in the manifold almost as big as a dollar bill folded lenghtwise. it was raming hot exhaust right into the airbox with so much force the flat air filter resembled a cone. . . good times. 
stuart in mn wrote:
I think brazing is often used for repairing cast iron (one of the exhaust manifolds on my '61 Pontiac was brazed probably 45 years ago and is still working fine), but in general cast iron can be tricky to fix - I'd find a good welder locally who is experienced in this sort of thing.
Not on a turbo manifold!
(they can often run red hot, braze material will melt out)
Don49
Reader
3/27/13 4:57 p.m.
Dr. Hess had it right. I have done this numerous times over the years with no failures. It is important to drill holes at the end of the crack and bevel all along the crack. I have a vise I repaired years ago that I repaired the broken slide and still use it clamping as hard as I want with no issues.
We had a cracked manifold on our Merkur that I tried welding without preheating a few months ago - it would just re-crack immediately as it cooled, even with very good surface prep and weld penetration. Definitely need to stick it in the oven and get it real hot before hand, then let it cool slowly.
old_
New Reader
3/27/13 6:29 p.m.
ask Keith Fenner
http://www.youtube.com/user/KEF791
the guy is simply amazing
I'm going to be the bad guy here, and say that anything you do to repair that crack will only make it worse, and cost you money.
I'd run it as-is.
Go onto motorgeek.com and post the question, or just do a search there. There are audi guys that have been adressing this dilema for decades. Cracked MC1 manifolds have been a problem since they were new. The MC2 had a flex section in the middle which eliminated the problem and I think also improves performance.
Once repaired, pay attention to your state of tune as sometimes high exhaust gas temps can cause the cracks.
yeah I have seen what alot of the motorgeekers have done, but thats why I posted here. . . motorgeek is. . . well. . . most people over there have the mentality of: spend thousands of dollars or your doing it wrong. and don't even bother bringing up something like megasquirt to that crowd, it frightens and confusses them because they spent so much more for the same thing. If I posted this exact thread over there i would either get A. no response, B "USE SEARCH GAAWWWD" or C, "Just buy another manifold" cuz they are so readily available. Besides, mine is actually one of the best I have seen, as far as cracks go. It seems like that place used to be alot cooler 6 or more years ago when you read the old posts.
I just like the attitude over here better. . . lean into the problem. . . try to figure it out before throwing money at it.
Thanks for all the input guys, thats why I love this place.
I agree with your comments about the geek site. But the experience there dealing with cracked manifolds is much better. You can learn from their experience. And there seems to be 2 groups on the site. One is like you said, high dollar high horsepower. There are some that are trying to do it on a budget and need help. I was in that category for a few years. As in all forums, spend an hour in search mode first. You will see who knows their stuff and you can always PM them.
As far as cracks go, many people have run manifolds with cracks for years. Some have said all MC1 manifolds have cracks, they just haven't been found yet!
Yeah you broke down the motorgeek demographic much better than I did. There really are two groups over there and I shouldn't lump them all into the same catagory, Just seems like the rich jerks are the first to post naysaying comments lol. then again they usually stay away from the 10valve content since it's an engine thats not worth spending 200 dollars on in thier eyes.
welcome to the internet right?? haha
44Dwarf
SuperDork
3/28/13 4:31 p.m.
Hess has the steps but on manifolds theres one extra step. Start off by going to the hardwear store get a 5 lbs bag of "Playground sand" Heat this sand up as hot as you can toss your cleaned part on the top of the sand while you preheat, leave sand in oven weld and then cover welded manifold in the sand close oven with heat still on for 1 hour then turn off heat and walk away untill next day. The hot sand help slow the post cool.
I've had my best luck with Norma-cast but turbo maybe better off with Super NI-Cast
https://www.forneyind.com/store/detail/601/arc_welding_electrodes/5011/nickel_welding_rod_55_nickel_super_ni-cast_332_12-lbs/