OK, so... I have a 90 year old drill press with a short pipe for mounting to a bench. I wish to convert it to a standup model. The ID of the head and foot are 2.495.
The only affordable option for a 6' pole was 2.5 OD DOM. It is 2.505. I need it to slide snugly into a 2.495 bit of cast iron. It won't fit in my lathe. I need to polish .0060 of diameter - or - .0030 of surface material evenly around the first 1' and last 4" of a 6' pipe without the lathe.
I don't want to polish my huge thick pole by hand. I don't want to pay someone to polish my pole either.
Provide proper, powered pole polishing perogatives, pretty please?
Cut the original pole in half and weld the new pole in the middle? 
Not as sexy as what you had hoped for I am sure.
DrBoost
UltimaDork
11/22/16 5:25 p.m.
I can't type anything that won't get me banned.
84FSP
Dork
11/22/16 5:30 p.m.
Pole polishing pro tips anyone?
Wouldn't it be easier to embiggen the cast iron bit? Or are you concerned about being able to go back the other way?
I've seen a couple examples of this over on the Garage Journal board. The general method is to rig up some supports out of casters, skateboard wheels, or similar to support the tube, then fabricate a cone or something that you can put on the end of a hand drill and then plug into the end of the tube to spin it.
Toss the pole outside on a cold winter's day - pro tip: don't lick it - then toss the base/head into the over on 350* for a few minutes, and reassemble?
stuart in mn wrote:
I've seen a couple examples of this over on the Garage Journal board. The general method is to rig up some supports out of casters, skateboard wheels, or similar to support the tube, then fabricate a cone or something that you can put on the end of a hand drill and then plug into the end of the tube to spin it.
3 cheap casters from HF and a wooden triangle ... will look like some Gilligan's Island E36 M3 but it might work if I can rig up something to spin it without too much wobble. Maybe I can actually use the lathe to drive one end and just make a stand-alone steady rest five feet from the headstock.
Google brought me to this freakin' cool solution but... I could buy 3.5 more dill presses for that kind of coin.

In reply to Huckleberry:
Sure, but that seems like the kind of tool every man should own.
Assuming it's like any drill press I've ever seen and those parts need a sliding fit you need more like 0.012 taken off, not 0.006. This is a job for a big lathe.
BrokenYugo wrote:
Assuming it's like any drill press I've ever seen and those parts need a sliding fit you need more like 0.012 taken off, not 0.006. This is a job for a big lathe.
THe head and foot don't need to slide. The work table moves but it's a threaded pinch fit and already slides over the 2.5 OD. SO... the rest can go together as tight as is possible to do manually exactly once.
Lube, lots of lube.
Or you may get a callus on it!
I would try this.
1. Clamp in vice.
2. Chuck up holesaw in drill.
3. wrap holesaw in friction tape.
4. turn beltsander belt inside out.
5. Put one end of belt on your shaft the other around your drill.
6. Turn on and move the drill in big circles so the belt sands your shaft.
44Dwarf
UltraDork
11/22/16 7:44 p.m.
I used to have this unit at a place i worked at. great for this with a set of pipe rollers.
linky
In reply to Huckleberry:
Is it bad that I'm jealous of that man's pole polisher?
Grind it til it fits!
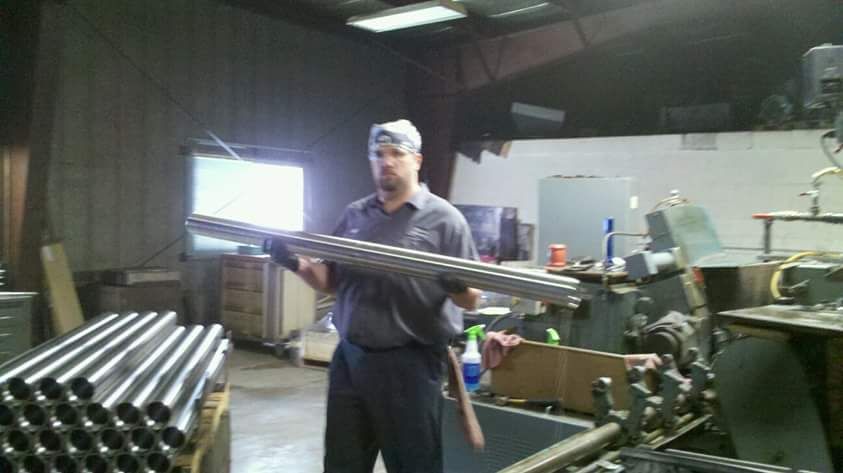
I could do that for you, if you were closer.
"Polishing" will take a berking long time. Centerless grinding, while not as efficient as turning on a lathe, could get that down in an hour or less.
codrus
SuperDork
11/23/16 12:11 a.m.
Forum says you live in PA? Close to Pittsburgh? If so, you could get a techshop membership and use one of their lathes.
http://www.techshop.ws
mndsm
MegaDork
11/23/16 12:19 a.m.
I hear a pole will shrink in the cold. Laws of thermodynamics and such.
Have access to a pipe machine?
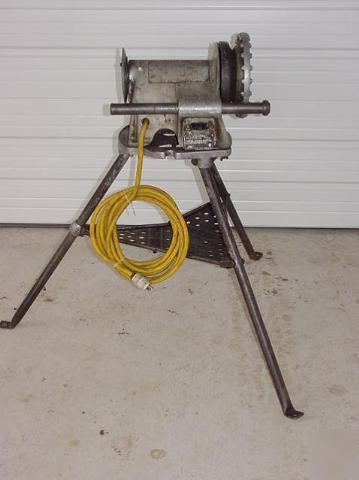
Chuck it up, hit w/ disc sander coarse to fine and or finish w/ DA. Check dia. w/ calipers. It'll work.
In reply to fasted58:
I could rent one of those for a couple bucks
codrus wrote:
Forum says you live in PA? Close to Pittsburgh? If so, you could get a techshop membership and use one of their lathes.
http://www.techshop.ws
Unfortunately I am as far from Pittsburgh as a person can get and still be in PA
Removing .003 of material is way beyond polishing. If you've ever tried to slip a bearing over an axle with a small nick in it, you'll recognize that any tiny imperfection will shoot you in the foot.
But that's not helping....
Describe the female area of the cast iron. It's 2.495 diameter, but how deep is this area? Just a collar at the top or is it the entire depth of the stand? My thinking is removing material from cast iron with a fly cutter mounted on a buck drill or some other method would be less problematic than turning a few feet of pipe to be smooth, concentric and straight.
Dan
Huckleberry wrote:
codrus wrote:
Forum says you live in PA? Close to Pittsburgh? If so, you could get a techshop membership and use one of their lathes.
http://www.techshop.ws
Unfortunately I am as far from Pittsburgh as a person can get and still be in PA
I wouldn't call that unfortunate at all
914Driver wrote:
Removing .003 of material is way beyond polishing. If you've ever tried to slip a bearing over an axle with a small nick in it, you'll recognize that any tiny imperfection will shoot you in the foot.
But that's not helping....
Describe the female area of the cast iron. It's 2.495 diameter, but how deep is this area? Just a collar at the top or is it the entire depth of the stand? My thinking is removing material from cast iron with a fly cutter mounted on a buck drill or some other method would be less problematic than turning a few feet of pipe to be smooth, concentric and straight.
Dan
The base could be done with a hone or fly cutter but the headstock is 9" of solid bore with 2 set screws. It's a 90 year old monstrosity in decent shape I picked up for $25 and fitted with a new motor (not really, but a working motor I also found). I thought it would be a cool, easy restoration to use in the shop but it's becoming a royal pain. At this point the 6' of DOM I bought is twice what I have in the thing and I could double my money scrapping out the cast iron. LOL.
So... I am either going to take the pole to a machine shop and see if a six pack or a $20 will solve this or I'm taking 80lbs of cast iron to the scrap yard and putting the $ toward a mill drill :)