I have been known to have really bad ideas, so I'm wanting to ask the GRM Hive just HOW bad this idea is before I commence with it.
Backstory: I found what I thought was a smoking deal for two RB25DET heads on eBay ($425 + tax, shipped for both). I purchased them right away and was giddy with excitement until the first one arrived. It turns out they are missing cam caps.
"Okay, no big deal" I says, I'll just order some new ones, some plastigauge and some hardware, see how they fit. I've had similar success with OHC Subaru heads, and a couple others.
The mass consensus in the RB world is that I bought really expensive paper weights, as replacing cam caps is next to impossible. It is agreed that line honing (Align bore? Line bore?) the cam caps is an effective method, but the cost of machining makes it unrealistic. I've made some calls around and nobody in my area is even set up to handle a job like that.
So my question is: How screwed am I? Can I DIY a work around using one of the factory cams or similar sized PVC or pipe? If I plastigauge my tolerances and they are all in spec, do I have additional reason to worry?
In the past, I've just hit the "Send" button and went for it. I never had any issues with the heads that I've done this on, but the reception from the RB world is making me doubt myself.
I do not have the magic skills of MKE, or similar, so I wanted to ask you all for input. Thanks in advance.
I've thought about getting everything lined up then through-drilling the caps for new dowel tubes.
Line bore is the way to go. You can cut the caps with out touching or "just brushing" the head side. A Tobin-ARP line bore machine could do it. Long as the bores are over 1" dia (the size of the tooling shaft).
Honing on cam bores pretty much requires a special tool for that specific head to even attempt an ok job (not a realistic option and lots of risk)
As a DIY setup here's how I would attempt it: Assuming you have lathe and mill access
Get a solid 1" chrome shaft that is at least a few inches longer than head. Machine 3 or 4 brass bushings that fit the cam bore exactly (zero fit) and have .001 clearance to the shaft. Cross drill the chrome shaft in locations where a 1/4" or 5/16" tool bit and be placed to cut each cam cap... or if you got an extra long chrome shaft then one hole should be able to cut multiple caps. You'll need one or two threaded holes for set screws perpendicular to the tool bit hole. Need to source/make a tool bit as well with a flat in line with the cutting edge (to orientate it correctly in your chrome shaft). Now you can setup the chrome shaft in the brass bushings and place it in the head. At first you'll need to hold down the bushings with something other than the caps and torque the cap(s) you're going to cut first. Set the tool height for the cut, there are tools for this or can match to head (very carefully....you do not want to cut the head side...only the cap and match it to the head side). Now you can slow and steady spin the shaft and feed the tool bit through the cam cap. Once done you can remove everything and verify the bore/fit. Adjust the tool bit if necessary and recut. If its good move a bushing into that bore and torque the cap down to hold it in place and cut the next cap, and so on.
With out a mill/lathe:
Old cam available? cut the flanges and lobes down or off so that it can move back and forth far enough to get all the journals from one side of the head/cap to the other. You'll need a way to hold the cam into the head without caps such as a nylon block. Holds it down but lets it rotate. Notch a cam journal into a cutting edge. it'll be hard to start but turn it by hand (or some kind of tool for leverage) and slowly feed it through a cam cap bore to cut the cap. Repeat of the others. Disclamer: I've only ever done this on V8's that had a messed up cam bore. Use the notched cam to clearance the tight cam bearing so it was always soft material to cut away....No idea how well it would work on aluminum.
On the outside chance that the cam bore is a common standard size to which you can locate and purchase a reamer with an extended strait shank (long enough to be in 2 bores while cutting a 3rd) you could then have 2 bushings made, clamp in same method as above and use drill to run the reamer through the cap/head bore. This method likely requires you to have 7 horseshoes tattooed on you keister and your middle name be lucky...
this is what the VW guys use to line bore a crank case ,
the 4 aluminum pieces have a cutter on the edge to bore the hole,
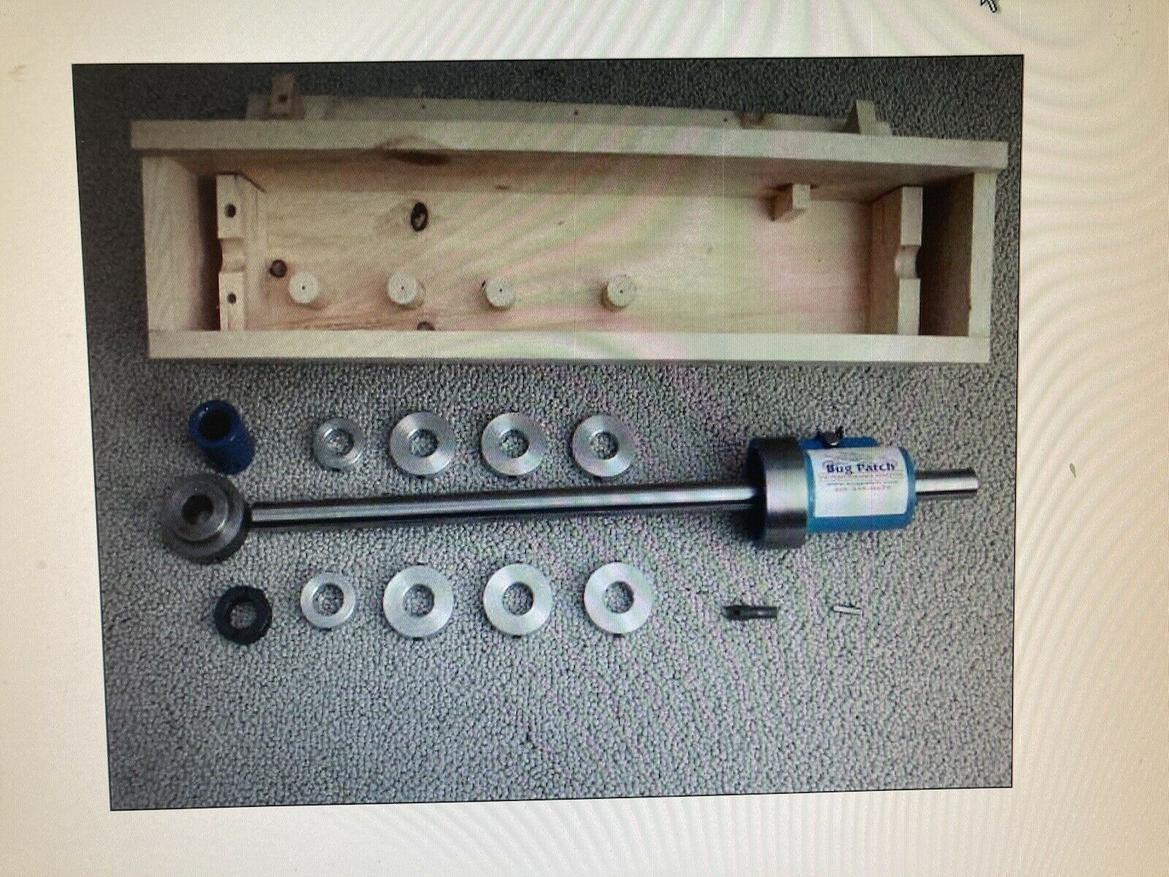
The tricky part will be finding anybody in the universe with a line boring machine that will go down to the size of the camshaft,
I'm voting for "Big Aluminum Paperweights."
Or, dispute the Ebay thing and return the paperweights.
My local shop here in Texas has done it for me several times. They've even line bored the cam journals and machined them for insert bearings. Hopefully you can find a shop in your area to do it.
Honsch
Reader
11/18/21 9:09 p.m.