So. On the swapped S10. Crate 350. I had installed a harmonic balancer which needed to be removed due to it being the incorrect one. Here is where the fun happens. I remove the old one. Seated the new one. And walked it onto the crank with a new bolt. It went exceptionally smooth no problems. I get it to the point it needs to be and then I go to remove the bolt. The bolt starts binding. Really confused I try to take it easy so as not to break it. But the son of a bitch broke anyways. So now I'm stuck with this.
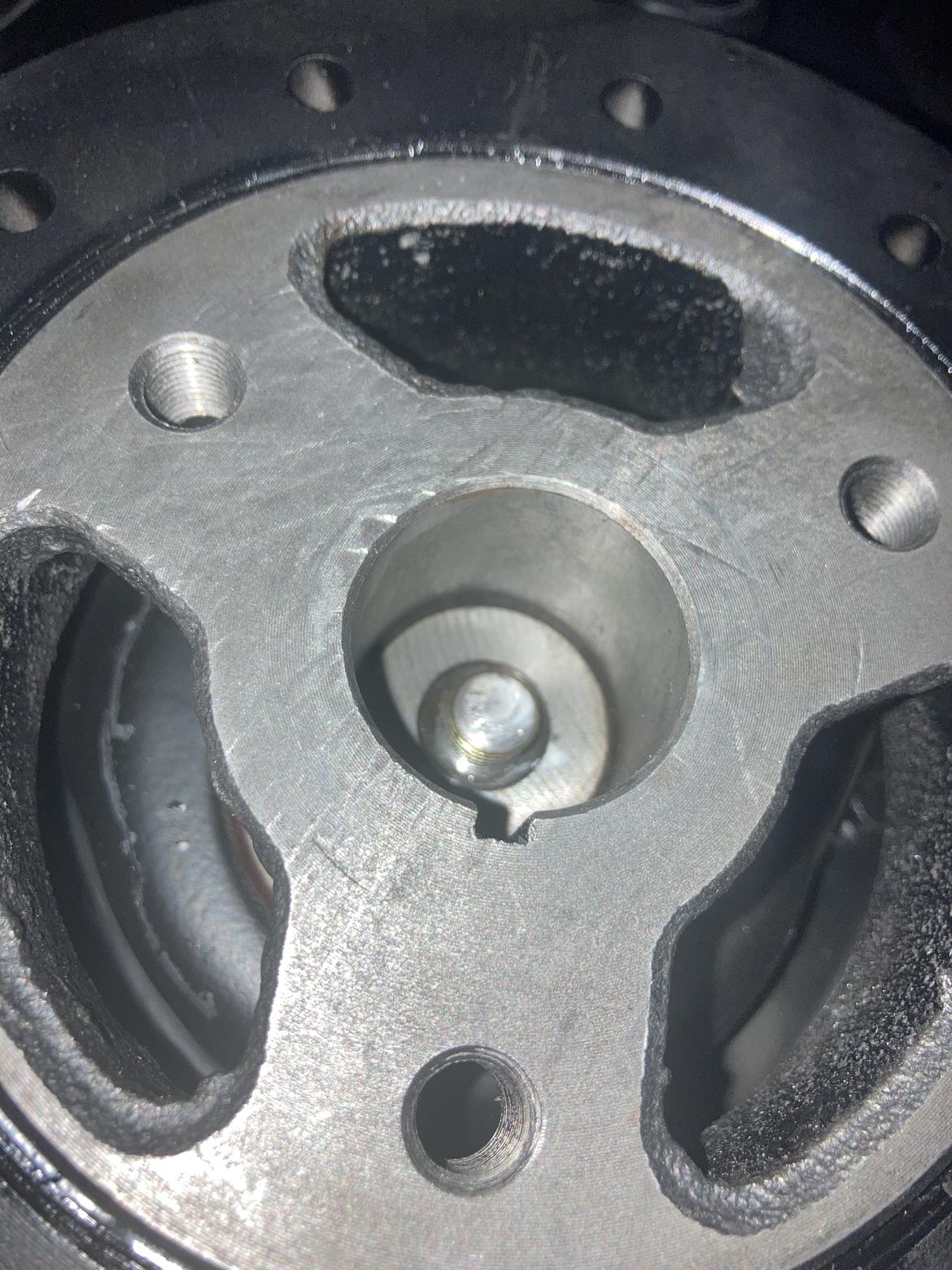
so I really don't know what to do. I could attempt to do the following.
1. remove the pulley using the puller and smash whatever is remaining of the bolt making it near impossible to put a nut onto it to weld and remove.
2. Same as above but this time I try to drill the bolt out. Then depending on the thread condition I either clean the threads up or re-tap it. I have heard interesting things about what you can do with that apparently the designer of the small block Chevrolet planned for that eventuality.
3. most small block Chevrolet's up until the late 60s didn't even have a bolt in the crank they were pressfit. So assuming that my balancer is fully seated, which it looks to be and everything is tight elsewhere, I could just send it. I have heard people doing this and having no problems even to the point of people having no crank bolt and never knowing they were missing it.
really need some suggestions here boys
I apologize for the lack of punctuation and capitalization I am doing this talk to text because I'm a bit pissed off right now LMAO
If you are sure it has the timing sprocket pinched properly, send it. Otherwise, drill and dremel for most very long time.
I left the chunk in the 350 on the el camino. Worked fine for years. Truck got totalled.
Mr_Asa
PowerDork
3/17/22 7:28 p.m.
Drill it out, weld it closed, when the weld cools it should shrink it some. At that point drill and tap for a left handed bolt? Drill and weld again to shrink more?
Not that it helps now, but I only ever see this when someone uses the bolt as an installer.
Make a spacer for the puller? Something that fits up against the face of the crank but has a blind hole in the middle for the stub of the bolt to fit into?
A lot of Chevy engines in that timeframe did not even have a bolt there.
That ain't coming out without a huge fight and possibly half a machine shop. It probably galled because the threads stretched while using it to pull the damper on. Best practice with backyard tools is to snug the bolt, then whack the damper with a hammer (I like to use a large socket that fits over the bolt, to hit the center of the damper) snug some more, etc.
I mean, a damper installation tool is the PROPER way, but who actually uses those? 
Use an old socket to go around the bolt and then use the puller against the socket. This will keep you from mashing the bolt. Old sockets or cheap sockets make great spacers. Then you'll have what's left of the bolt to remove.
Right. Though gentleman the big question is this.
should I attempt the repair or should I just send it right now it looks like most are leaning towards sending it.
Everything looks lined up I'll check it tomorrow to make sure
I'd send and keep an eye on it. If I am right about what happened, getting it out is going to involve a lot of metal work and may require removing the crank. And since it broke while trying to remove the bolt...
Mr_Asa
PowerDork
3/17/22 9:20 p.m.
bonylad said:
Right. Though gentleman the big question is this.
should I attempt the repair or should I just send it right now it looks like most are leaning towards sending it.
Everything looks lined up I'll check it tomorrow to make sure
If you send it I would take several measurements from different spots, with photos and maybe a scratch mark or paint pen on the balancer so you know where they are, then set up a schedule to remeasure everything. How much you measure to will be up to you, but I'd max out at a sixteenth?
No Time
SuperDork
3/17/22 9:27 p.m.
Pete. (l33t FS) said:
I mean, a damper installation tool is the PROPER way, but who actually uses those? 
I actually bought one, mainly because I was changing the damper on the Ram in a hotel parking lot and wanted to minimize drama.
But I've also been trying to be better about using the right tool (including torque wrench) for the job so my 18yo son doesn't pick up bad habits before he enters the work force (graduated from Voc school auto tech program) this summer.
No Time
SuperDork
3/17/22 9:38 p.m.
AnthonyGS (Forum Supporter) said:
Use an old socket to go around the bolt and then use the puller against the socket. This will keep you from mashing the bolt. Old sockets or cheap sockets make great spacers. Then you'll have what's left of the bolt to remove.
This is the approach I'd take.
Did you judge it was seated by measurement/markings, or because the bolt stopped turning so it felt like it was bottomed it? Do you know how far the bolt is threaded into the crank?
I'm guessing the bolt bottomed out in the crank causing it to bind up and snap when trying to back it out. If I'm right, then damper unlikely to be bottomed out on the timing sprocket and will allow things to move around if left the way it is.
Once you get the bolt to move a little, so it isn't bottomed out, then it should come out easy.
In reply to No Time :
It is a small diameter bolt and fairly weak. I doubt that it bottomed out in the hole, given that the bolt is generally a very specific bolt for the application and SBCs are not exactly uncommon.
No Time
SuperDork
3/17/22 9:55 p.m.
In reply to Pete. (l33t FS) :
If it was the original/correct bolt for the damper then what I said above can be ignored.
I read the original post and how the bolt was being removed after installing the damper. Based on that assumed it wasn't the actual crank bolt that broke, but a different longer bolt with more threads to be able to pull in the damper.
In reply to No Time :
It was a specific bolt for the dampener. This is of course my fault and I assume that failure for not using the tool needed. I of course have gotten away with it before but in this case, well. I didn't. Regardless it's the right bolt for the job and I just got lucky before I guess.