I am mounting an ECU on the inner fender liner of my S10 project. I have a mounting plate with 3 holes in it. One of the holes can be bolted right onto the liner, but the other 2 will be standing off from it a decent distance. My original plan was to take some flat steel, drill and bend it to the correct shape, then weld in some gussets to keep it from fatiguing. Maybe there is a better/easier way. Anyone used plastic or some other material to make stand off brackets? Or an easier method than what I am planning? I'll try to post a picture later.
SV reX
MegaDork
5/9/22 11:07 a.m.
Use the mounting plate you have with small pieces of tubing as bushings slid over the 2 bolts to create stand-offs for them and call it a day.
Depends on "how curved" but I would do what svrex says, or if the curve is large then I would bend a piece of flat stock in the shape of a Z since the tabs at either end can be bent to match the curved shape easily.
If you put the flat direction of both Z pieces at 90 degrees to each other, you won't need any gusseting.
SVRex, I may have some delrin bushing stock tyhat could work for that, if I can find it.
Robbie, it is pretty steeply curved. Here's a couple crappy pictures:
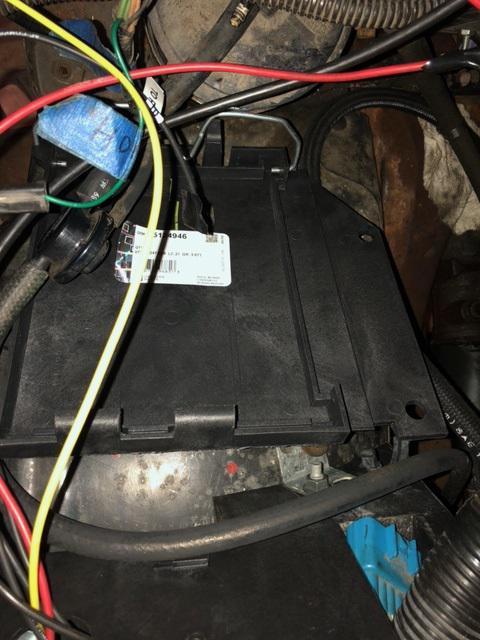
On the above picture there is a mounting hole on the right that I will be able to directly bolt to the fender, I think it is covered up by the emissions line right now.
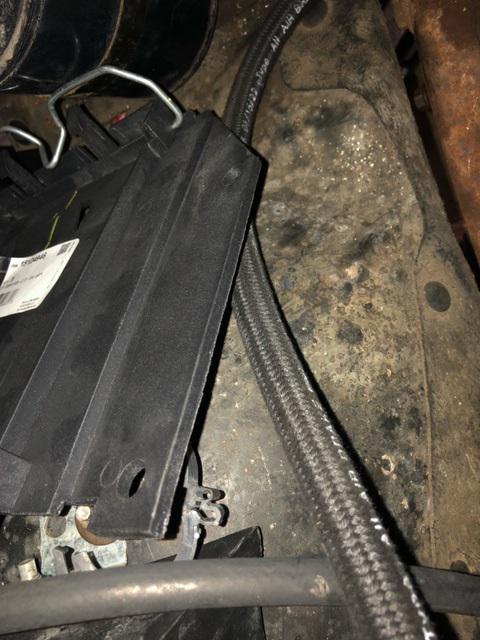
Slightly different angle. Depending on how far up it is mounted, the distance of the mounting holes from the fender line are about 3-5"
SV reX
MegaDork
5/9/22 12:18 p.m.
In reply to eastsideTim :
I may have confused it a little calling it "tubing".
I meant metal tubing. A small diameter sleeve that fits over the bolts.
SV reX
MegaDork
5/9/22 12:24 p.m.
Like this:
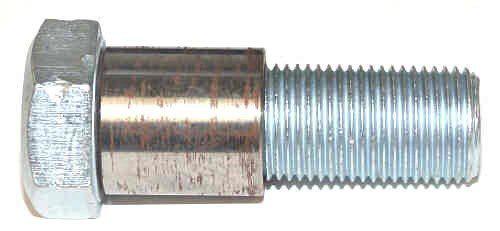
You could also use a threaded connector with bolts from each side, if you can find one exactly the right length:
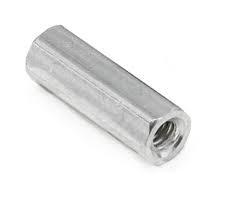
In reply to eastsideTim :
Use Cad. Cardboard aided design.
Take a pair of scissors and cut up a sheet of cardboard until you like what you've done. ( it's easier if you don't use corrugated)
I do a rough cut first to ensure it fits and then using straight edge and protractor etc I make a final template.
Then I transfer it onto the metal using a sharpie. Once I've cut it out I use files to smooth the lines.
it takes a little more time than cutting it out directly but pays off in spades by looking very professional.
SV reX said:
Like this:
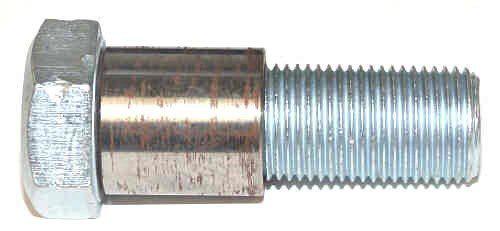
You could also use a threaded connector with bolts from each side, if you can find one exactly the right length:
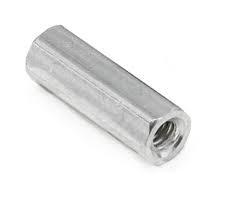
A bushing..or ferrule. Good solution since it lets water drain out from behind the ECU once it is mounted.
With the curvature, I think the bushings would work, would just require cutting them at the angle of the curve, then using the offcut on the other side, so the nut and bolt are lining up flat against the surface of the fender liner. This is the kind fo thing I wish I had a bandsaw for.
Hopefully, drainage will not be an issue, there sholdn't be much (if any) water getting to where the ECU is, and the angle it will sit at will promote any getting there to run off.
OHSCrifle said:
SV reX said:
Like this:
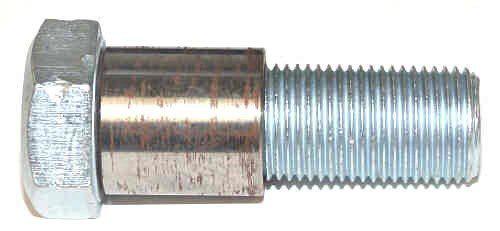
You could also use a threaded connector with bolts from each side, if you can find one exactly the right length:
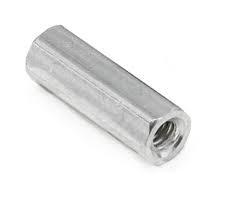
A bushing..or ferrule. Good solution since it lets water drain out from behind the ECU once it is mounted.
Which I refer to as 1/2" schedule 40 pipe nipple. Cut to whatever length you need.
For something light like an ECM, PVC works just as well as black steel pipe.
eastsideTim said:
With the curvature, I think the bushings would work, would just require cutting them at the angle of the curve, then using the offcut on the other side, so the nut and bolt are lining up flat against the surface of the fender liner. This is the kind fo thing I wish I had a bandsaw for.
Hopefully, drainage will not be an issue, there sholdn't be much (if any) water getting to where the ECU is, and the angle it will sit at will promote any getting there to run off.
People often forget how good you can do with a hacksaw and a vice.
In reply to Robbie (Forum Supporter) :
That is my usual method to make more precise cuts than I can with an angle grinder, was just wanting to see if I was missing any better possible ideas.
Flat plate of 22 gauge or similar, 90 degree bend down to the curve, bend up a lip on the end that will through-bolt to the inner fender.
Or just use one bolt 
eastsideTim said:
With the curvature, I think the bushings would work, would just require cutting them at the angle of the curve, then using the offcut on the other side, so the nut and bolt are lining up flat against the surface of the fender liner. This is the kind fo thing I wish I had a bandsaw for.
Hopefully, drainage will not be an issue, there sholdn't be much (if any) water getting to where the ECU is, and the angle it will sit at will promote any getting there to run off.
I can't help but to think like an architect. Water will get everywhere - you just have to plan to let it get out.