Wondering if anyone in the Harrisburg area has a mill who can help me, or if you can point me in the direction of what I can do on my own.
If you take a look at the photos below you'll see what I'm doing. I'm replacing the wheels on my 94 Mazda B4000 with ones from an 05 Ranger. They both have 70.5mm hubcentric bores, but the newer wheels were meant to fit on trucks without a big external 4x4 hub, so they have a lip on the outside of the centerbore that prevents the old-school hub from fitting through.
I contacted three machine shops and they heard "aluminum wheels" and all said "heck no... liability... won't do it"
It doesn't need to be precision since I'm not changing the diameter of the hub bore, I'm just removing a lip from the outside of the hub bore. From what I can tell it needs to be about 65mm (but I can measure more accurately before I cut).
Can't I just get a correctly-sized milling bit and stick it in my drill press? I thought about a die grinder but I don't want to just hog it out. That would look ugly and take a long time.
When I'm looking for the right bit, what do I search for? I looked for 65mm boring bit, 65mm milling bit, but they come up with a bunch of wood bits that are 65mm long not diameter. It did come up with some 65mm Forstner bits.
Like I said, it doesn't need to be pretty, but I want it to be round.
Old wheel:
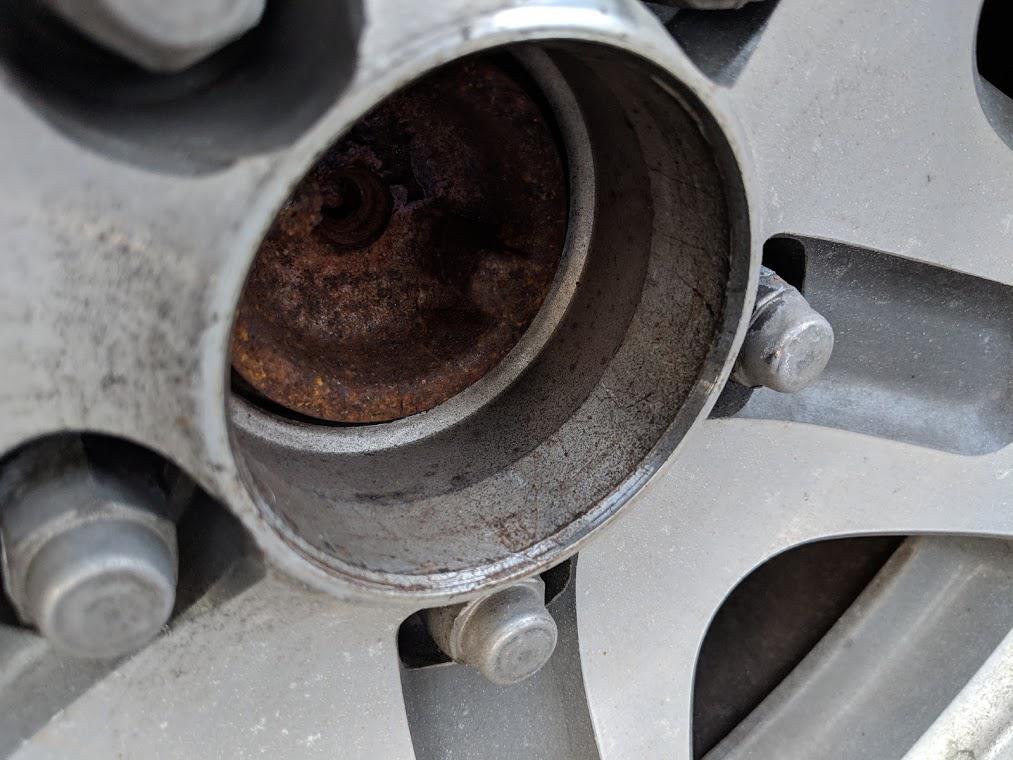
New wheel:
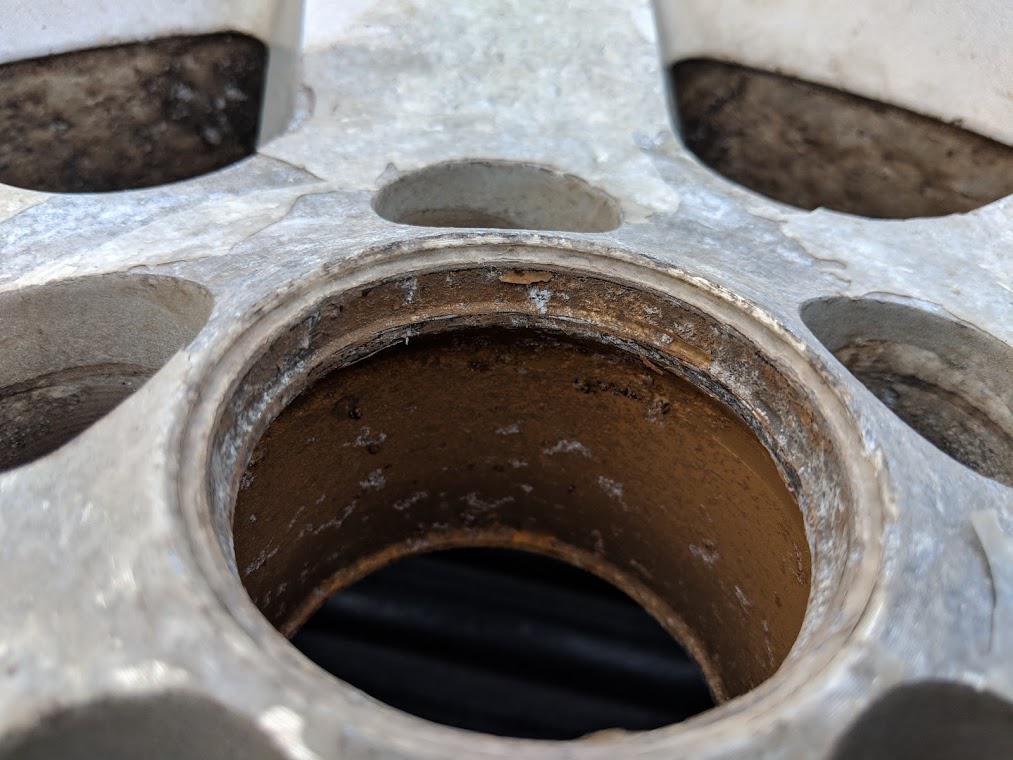
Do not try in drill press. The way this would be done in a milling machine involves a boring head which has adjustable diameter. The die grinder and carbide burr really is your best DIY approach, done carefully it will be invisible. Final finish with a sanding roll. That said, if you really want to pay machine shop prices, keep trying more local shops, not everyone is stupidly risk averse. I know my former employer would take the job, but it would be about $50.00 per wheel, because each wheel needs individual set up in the mill. Alternately, someone with a really large lathe could do it much quicker.
contact Rickson Truck wheels in Hunt Valley, MD ask for Dan
In reply to TurnerX19 :
Just curious... why not a drill press? Cause I'm thinking even a good bi-metal hole saw with the wheel clamped to the table might do the trick.
Cooter
SuperDork
2/7/19 12:45 p.m.
70.5mm is just a tick over 2 3/4"
I would just get a large (1.5"-2" abrasive cylinder or cone on a 1/4" shaft and chuck in up in my drill. Should be near-effortless, and no one would be the wiser.
Curtis said:
In reply to TurnerX19 :
Just curious... why not a drill press?
'cuz if you don't get it precisely centered, the cutter is likely to dig into the offset side and grab the wheel resulting in either a broken cutter or a broken wheel or a broken Curtis or a combination of the three. DAMHIK...
The best way to do this would be in a BigAss lathe, holding it with a hub adapter. Or a regular size CNC mill centering it on a hub adapter bolted to the bed.
A hand mill, AKA the die grinder would probably be fine, just not as sporty as a real machine operation. If you have a 1/4" collet air grinder, use a 1/2" single cut burr at a reduced speed and lots of bar soap. Grind the soap to start and hit it about every 10 seconds or so of wheel grinding. The soap will keep the burr from loading up with aluminum.
Take your time and use center caps when you mount the wheels. Nobody will know you did it by hand. Unless you do a really good job, then don't cover them and you've got a good story.
If you were closer, about 2500 miles closer, I'd be happy to set it up on my mill. Unfortunately, I'm in San Jose and you are not.
GLWF...
rdcyclist said:
Curtis said:
In reply to TurnerX19 :
Just curious... why not a drill press?
'cuz if you don't get it precisely centered, the cutter is likely to dig into the offset side and grab the wheel resulting in either a broken cutter or a broken wheel or a broken Curtis or a combination of the three. DAMHIK...
The best way to do this would be in a BigAss lathe, holding it with a hub adapter. Or a regular size CNC mill centering it on a hub adapter bolted to the bed.
A hand mill, AKA the die grinder would probably be fine, just not as sporty as a real machine operation. If you have a 1/4" collet air grinder, use a 1/2" single cut burr at a reduced speed and lots of bar soap. Grind the soap to start and hit it about every 10 seconds or so of wheel grinding. The soap will keep the burr from loading up with aluminum.
Take your time and use center caps when you mount the wheels. Nobody will know you did it by hand. Unless you do a really good job, then don't cover them and you've got a good story.
If you were closer, about 2500 miles closer, I'd be happy to set it up on my mill. Unfortunately, I'm in San Jose and you are not.
GLWF...
I guess I'll try some sort of abrasive. I can't imagine a 1/2hp drill press with a loose belt breaking anything. I'm just imagining a very long process with abrasive.
The rears have a center cap that mimics the front hub, but the front hubs just stick through the bore and they ARE the center cap.
Just seems like lathe and mill are overkill for something that doesn't have to be exact. I just need to hog out a hole. Let me see what I can find with abrasives at HF and HD. I have to go to HD anyway.
BITD guys used a regular old router with a carbide cutter and WD 40 to recut the ID on H2 wheels so they fit on Dodge Rams. You could do similar. Makes an awful noise, wear hearing protection. But it works good and cuts fast and precise.
Use the carbide or high speed steel burr with soap first, much quicker than abrasive. Another reason to not use the drill press is that it's lowest speed is probably much too fast for 2.75 diameter tool.
I recently cut a similar lip off some aluminum wheel spacers with a die grinder and carbide bur. It didn't take long, it would have been even faster if i had the proper bur for aluminum.
Router with a flush cutting bit and a bearing will knock that out in a minute. I have a bit with different bearings that i keep specifically for aluminum wheels
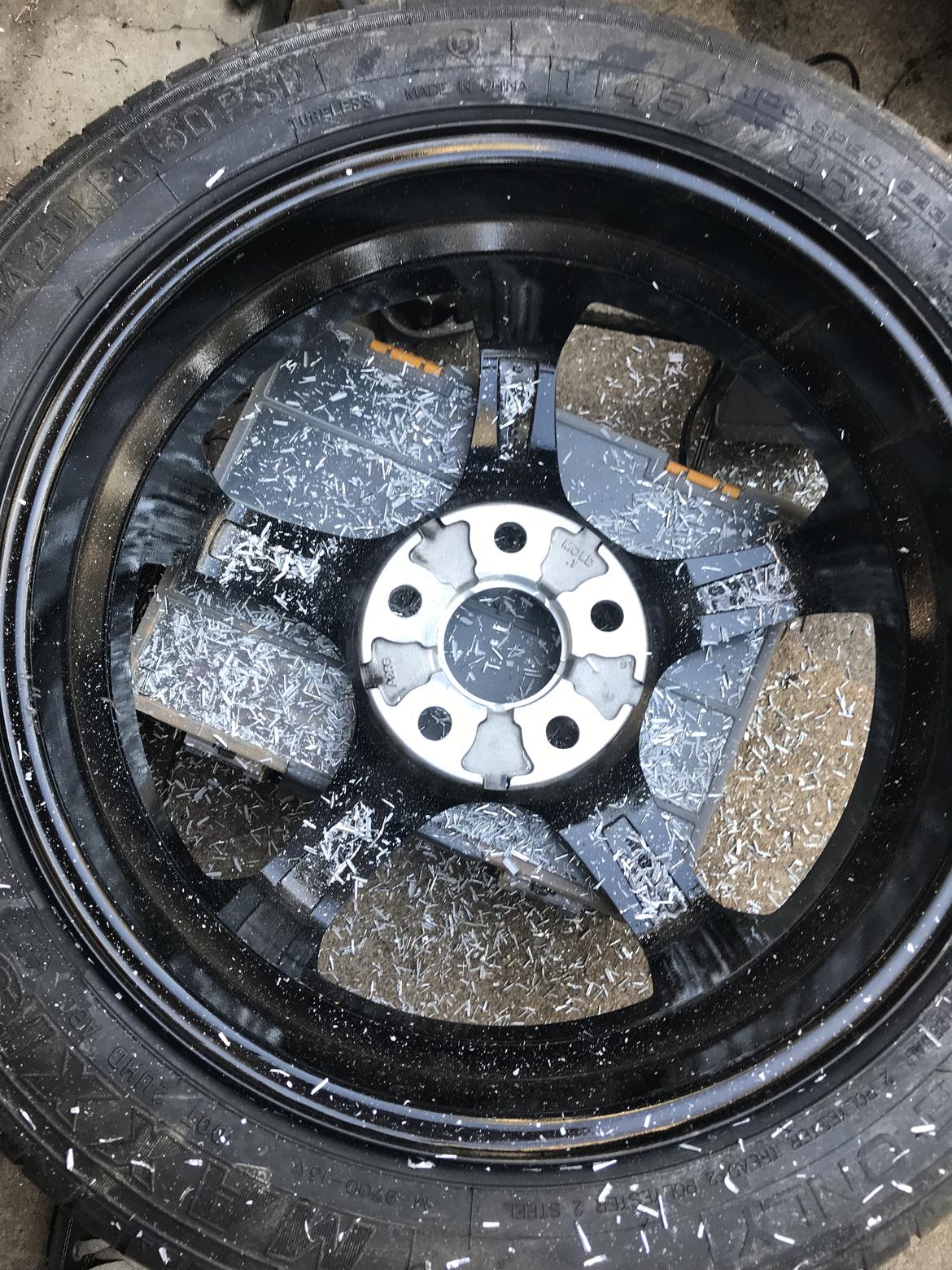
pirate
Reader
2/7/19 1:25 p.m.
A 2 3/4 inch diameter end mill will be expensive and possibly be hard to find. A drill press unless industrial grade would not be rigid enough to make a plunge cut with out a lot of chatter. What is needed is a lathe or a vertical mill with an adjustable boring head or a CNC vertical mill and circle interpolate the diameter. Shouldn’t be too hard to find a small local machine shop to do it. A pretty simple job with minimal setup time.
STM317
SuperDork
2/7/19 1:52 p.m.
Maybe a brake lathe? I've turned down Ranger hubs before using a brake lathe, but it seems like you might be able to do the wheel with the right setup.
In reply to Patrick :
Great solution! I'm gonna keep that one in mind. Well, for as long as I remember it: I have a good memory, its just short.
In reply to Patrick :
I've been wanting to try a router to open up some 54mm centers to 56 or 57. I'll have to give it a go.
Carbide bit in a Dremel tool would knock those out before your beer got warm.
Hell, it would probably take me longer to find my Dremel and Carbide, than it would to chew that lip off. 
All these mechanical tools to accomplish something that can be done with a simple "half round" hand file and a "flap" sanding wheel for finishing. That last work would require a hand drill.
jimbbski said:
All these mechanical tools to accomplish something that can be done with a simple "half round" hand file and a "flap" sanding wheel for finishing. That last work would require a hand drill.
Perhaps the picture doesn't show scale very well. The lip that needs to be removed is about 1/4" deep and 5/8" thick. I don't feel like hand rasping that much aluminum.
93gsxturbo said:
BITD guys used a regular old router with a carbide cutter and WD 40 to recut the ID on H2 wheels so they fit on Dodge Rams. You could do similar. Makes an awful noise, wear hearing protection. But it works good and cuts fast and precise.
wait...wait.... what kind of flush cut router bit has the hardness to do that?
Seems like my flush cut bits (which I use a lot at the theater) go dull on Luan after 5 uses. This really has my interest, but what bit do I get to cut aluminum?
mke
Reader
2/7/19 3:57 p.m.
Die grinder with a single cut carbide bur, same bur in a drill press works, a router would work or pop out and use my mill, elverson so about an hour away. ...but you'd be done in less than the drive time with the other options. As long as it's just clearance and not to align anything just have at it.
Came to say router too. Trick is mineral oil in a squirt bottle and small passes. I've seen some nice work done with a couple of plywood circles that wedge into the back of the rim and have holes that position the router for small passes. Then you can use regular carbide bits for most of the work and finish with the fancy bit.
Edit: there's a YouTube video out there somewhere of a guy who carefully attached a bucket lid to his router and added layers of masking tape to the outside to get the right size too.
mke
Reader
2/7/19 4:09 p.m.
I like WD40 for cutting aluminum...it does a great job.
Ok. I'll see how many flush cut bits I can ruin 
mke
Reader
2/7/19 5:39 p.m.
Aluminum cuts pretty well with wood tools....the problem is most are a bit too high rpm so the tools don't last like they could....lots of lube helps but it will smoke a bit. Hold on tight!
Your pictures almost completely show the solution. If I were doing that, I'd do this:
Gather die grinder and carbide burr of your choosing. I have a Dremel, so I'd use that, but a chainsaw sharpener motor would probably be better, because it uses 1/8" bits. Install wheel on rear, like in picture 1. With rear axle securely on jack stands, start vehicle and put in low gear. Use carbide burr to machine round hole in wheel, while it slowly turns. Pat self on back.
Of course, you may want to have a person in the driver's seat to increase the safety.