mke said:
Aluminum cuts pretty well with wood tools....the problem is most are a bit too high rpm so the tools don't last like they could....lots of lube helps but it will smoke a bit. Hold on tight!
... and the one router I have with variable speed had a motor bearing seize.
snailmont5oh said:
Your pictures almost completely show the solution. If I were doing that, I'd do this:
Gather die grinder and carbide burr of your choosing. I have a Dremel, so I'd use that, but a chainsaw sharpener motor would probably be better, because it uses 1/8" bits. Install wheel on rear, like in picture 1. With rear axle securely on jack stands, start vehicle and put in low gear. Use carbide burr to machine round hole in wheel, while it slowly turns. Pat self on back.
Of course, you may want to have a person in the driver's seat to increase the safety.
This is just crazy enough that I might try it. I could even put it in 4-low without the front hubs engaged if I needed to.
mke
Reader
2/7/19 8:15 p.m.
Curtis said:
snailmont5oh said:
Your pictures almost completely show the solution. If I were doing that, I'd do this:
Gather die grinder and carbide burr of your choosing. I have a Dremel, so I'd use that, but a chainsaw sharpener motor would probably be better, because it uses 1/8" bits. Install wheel on rear, like in picture 1. With rear axle securely on jack stands, start vehicle and put in low gear. Use carbide burr to machine round hole in wheel, while it slowly turns. Pat self on back.
Of course, you may want to have a person in the driver's seat to increase the safety.
This is just crazy enough that I might try it. I could even put it in 4-low without the front hubs engaged if I needed to.
No, no, no.....you DO NOT put you hands near a moving wheel. You also DO NOT run a car in gear on jack stands.
Router - fine, just hold on
Die grinder- fine
Drill press - ok if you bolt the wheel down if you're using a drill bigger than about 1/2"....a 5/8 bur or sanding drum is fine.
Mill- fine, make the drive and I'll set you up with what you need to do the job safely
Running the car in gear on stands while you sit there with your hands hold tools on the wheel is not fine.
If I hadn't done it myself, I wouldn't have believed it. Chucked up a flush cut bit in the router and used a slightly larger bearing on it to leave a wee lip for the center caps to clip in.
I used cutting oil (didn't have any WD40 around). Very little smoke and the bit was just warm to the touch after cutting. I'm darn near speechless.
A note if you try this at home: Check your collet torque frequently. Twice during cutting my collet came loose and the bit nearly fell out. That is not something that typically happens with this router, so I'm assuming it was the extra vibes from the harder substrate. Also, check frequently that your bearing is still there. Mine disintegrated and fell off but fortunately I noticed it before I messed things up. I put a new one on and did my cutting while watching through the router window so I could see the bearing. Safety goggles, gloves, and hearing protection a must.
I also suggest pausing frequently to hit the lip of the bore with some 60 grit on a D/A. The routing leaves little burrs protruding up and it is hard to smoothly slide the router around the bore.
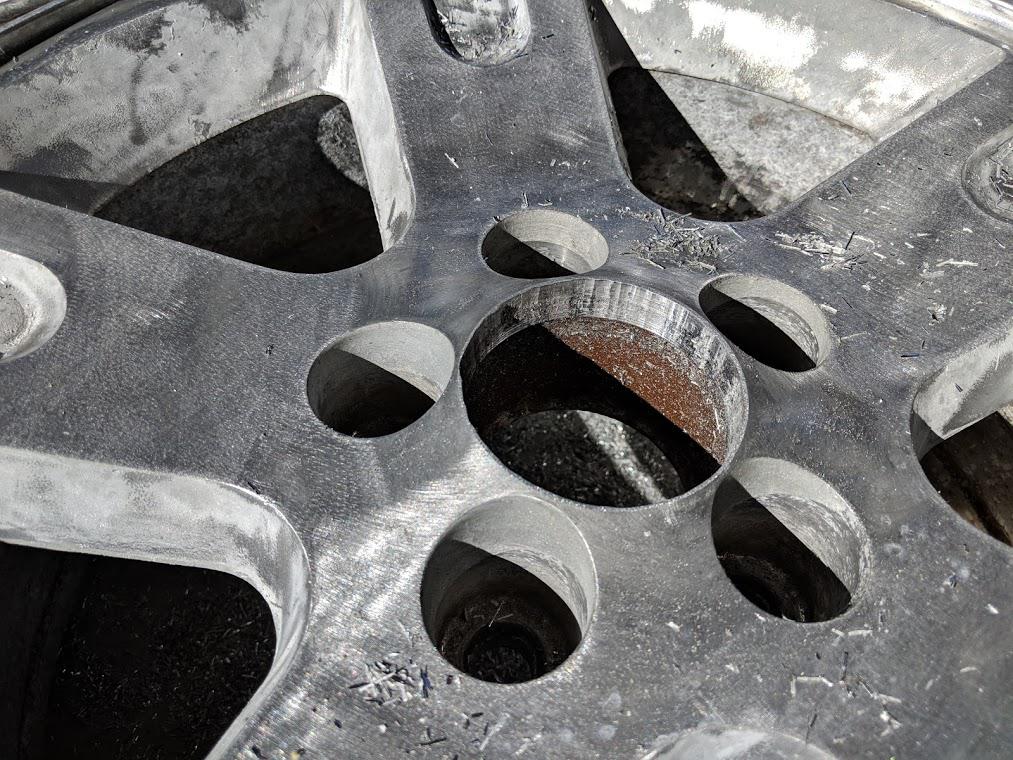
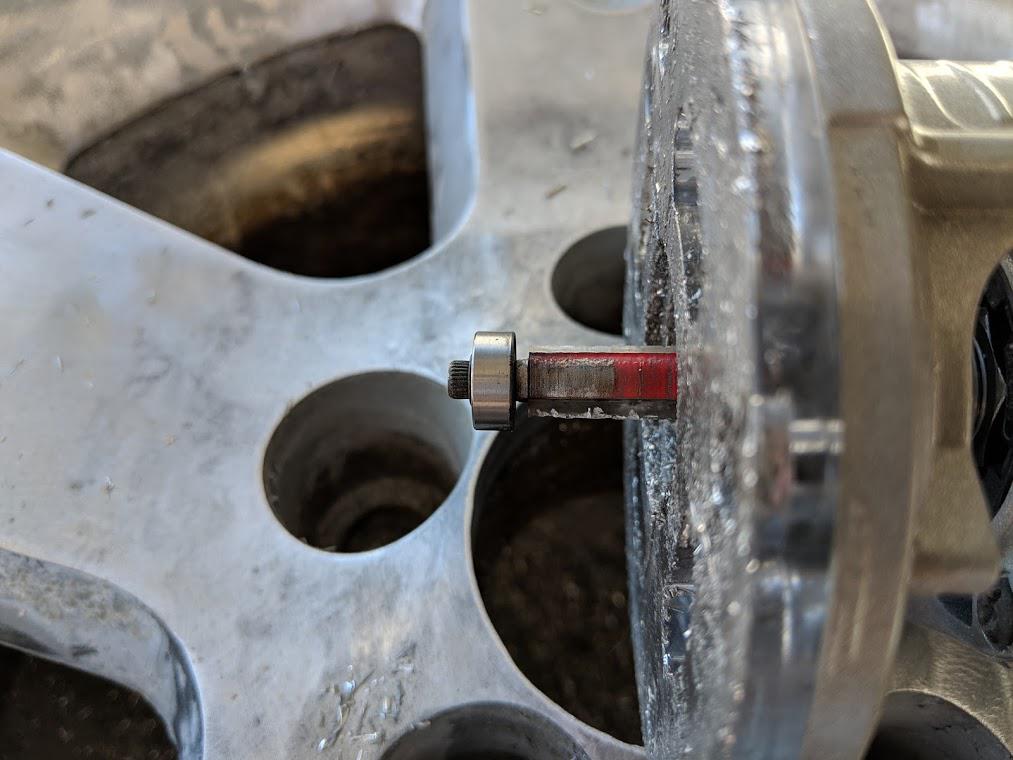
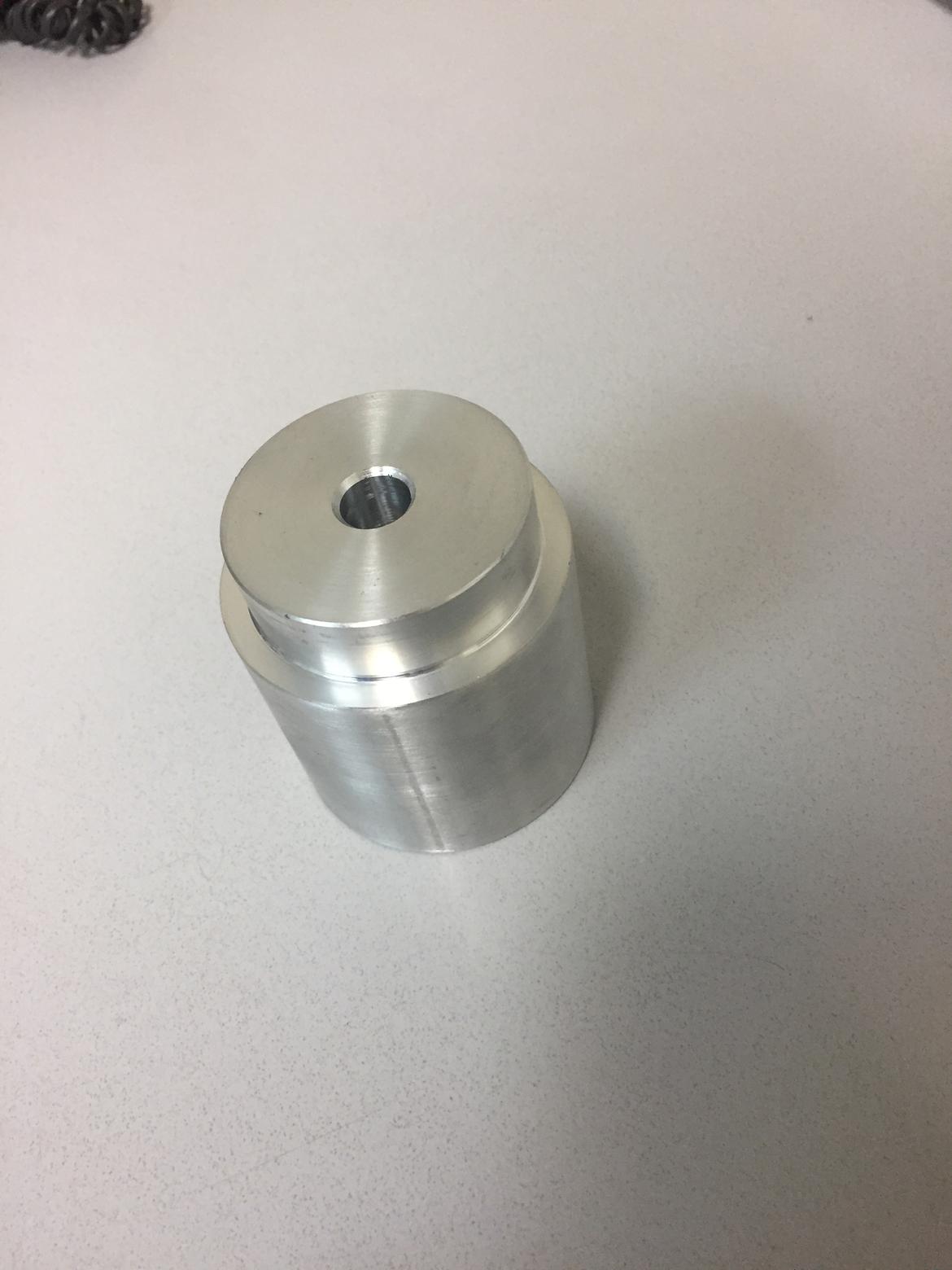
I made this to eliminate setting up for each wheel. This side has .500 reamed hole, I line that up with a dowel in the collet. The other side is threaded, I tighten it down into the T-slot in a mill. Once I'm set up for the first one I can just remove one wheel then plop the next one on. This is using a boring bar to open up the hub side while centering on the cap side. I had eight wheel to open up so I figured it was worth the effort.
First coat of flat black flashing off right now.
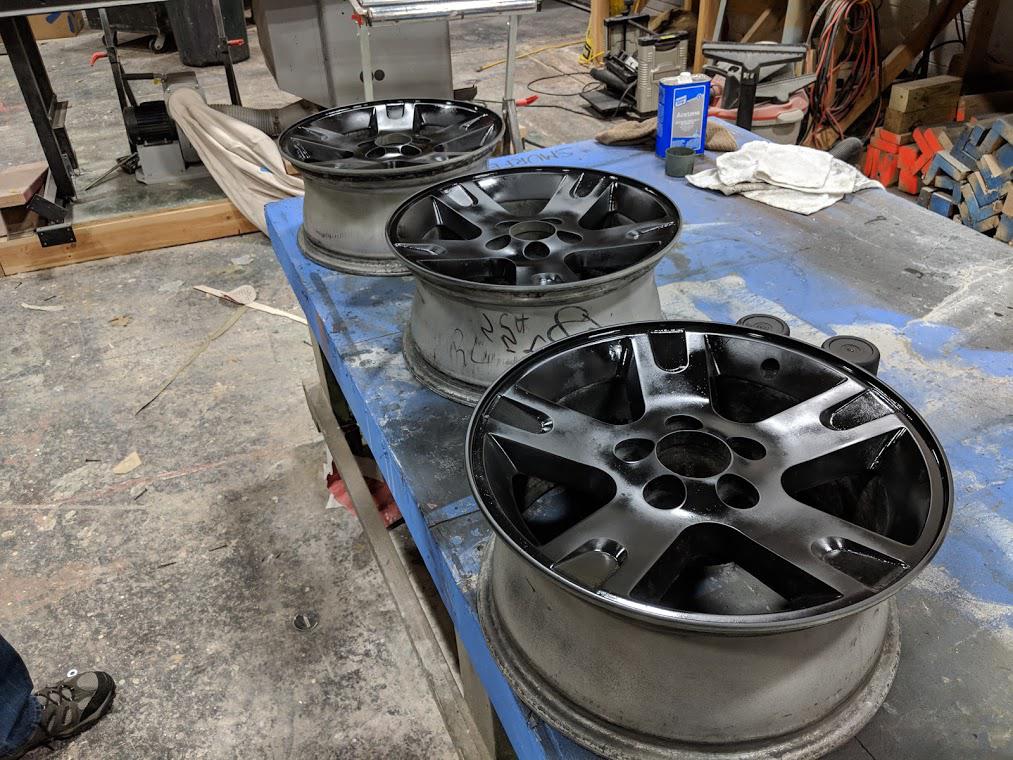
mke
Reader
2/8/19 3:51 p.m.
Winner winner chicken dinner!
Nice job.
I may or may not have done the same to some aluminum panasport style wheels made for an MG Midget and a hand held router...
Yeah, the router thing scares me a little. Those things turn crazy fast. As noted above, hold on tight!
The router bits for sale in the big box store are crap. I have found that solid carbide bits from Whiteside Machine in NC are pretty awesome. I suspect they could help you find an appropriate bit.
https://www.whitesiderouterbits.com/collections/flush-trim-spiral-bits
I started with a previously well-used Diablo bit from a big box store. When I was all done, it felt pretty sharp and it never got hot. It also never slowed down during the cutting. I'm tempted to try it on wood again.
I also didn't get a ton of kickback from it. No more than routing oak or bamboo or any other really hard wood. Not sure I'd recommend it to someone who doesn't have a lot of experience with routers, but I use one about 3 times a week. I found it to be pretty easy.
I expected to get 1" into cutting and have it stop and just smoke and chatter, but it held on like a trooper. All four wheels were done in about 15 minutes.
Told ya so. 
generally speaking woodworking tools will work on aluminum.
mke
Reader
2/9/19 9:58 p.m.
Curtis said:
I started with a previously well-used Diablo bit from a big box store. When I was all done, it felt pretty sharp and it never got hot. It also never slowed down during the cutting. I'm tempted to try it on wood again.
A beer says if burns wood now....I've never had any lock going back to wood once Ive cut aluminum even a little. Drill bits of milling cutter running at the correct cutting speed hold up well and will cut wood fine after metal, but wood tools at run WAY above the correct cutting speed and while it works it damages the cutting edges. A skill saw with fine carbide blade does a good job cutting aluminum plate up to about 1/2".
So can cut stuff like concrete block and stone with carbine wood tools too for what thats worth. diamond blades/cutter last longer but a worn carbide skill saw blade still has 30 minutes or so of block cutting left in it and I routed the travertine counter top on the patio island with a plain old router bit with no issues.
With my budgets at the theater, most of my bits burn wood. I have a bunch of drawers with drill bits. They are labeled Tiny twist, small twist, medium twist, big twist, huge twist, and "rotary smoke generators." That last one is when I finally wipe out a bit and it goes in there to be sharpened. Once they get so short that they're useless, they become trash or get cut down for dowel pins for some unforeseen project.