So I taped a slab of cardboard over the grill of my Miata as an aerodynamic experiment. Long story short the car wants to overheat....duh.
Anyway I can get the temp down to 200F by keeping the heater on full blast and turning on the cooling fan. I suspect I'll need more air flow to the radiator. For the purpose of aerodynamics should I enlarge the current holes or add more holes?
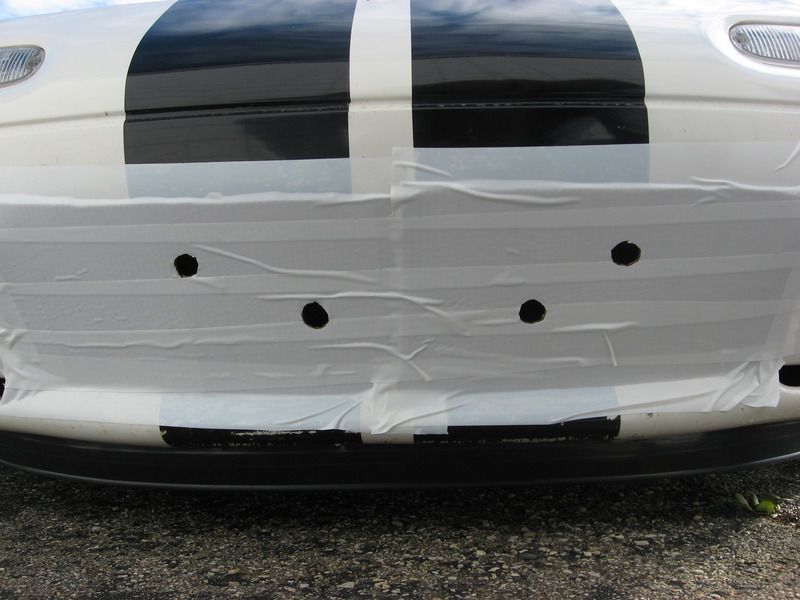
Theoretically, there should be enough cooling to run the car just under the fan coming on under normal conditions.
So open it up until you are between 195-200.
Open area is what is important. But number vs. bigger- that's a style question, if you ask me. Is there a Mazda grill that you like a lot? Start with that shape in the middle.
What about radiusing the holes like intake trumpets rather than just a sharp edge?
Or totally block off the front and put a couple of NACA ducts on both the upper and lower more horizontal surfaces and duct those to the rad?
In terms of cooling, more vs. bigger is a style question, but in terms of aerodynamics it's a functional question...I'd think one opening of an appropriate size would be best aerodynamically.
Edit: Having radiator ducting in place will improve radiator efficiency by making the best use of the air going in.
Start with more holes. Then you can open/close them off as the ambient conditions change with the season. Adding a radius from the leading edge inward will help , but not as much as the number of holes. Increased hole size means locally high flow instead of distributed flow of many holes. As was mentioned, if you can get the car to stabilize just about where the fan comes on, you will have the right amount of opening (and that will change with ambient conditions).
Put on a splitter, that'll probably help. And work on getting air out of the underhood area - the more of a pressure differential you have, the more airflow you'll have. Everyone always focuses on the high pressure side, but it's the low pressure side that makes the big differences.
Also, check out the Supermiata noses. They use very small radiator inlets and brake cooling inlets, but they can keep cool due to the shape of the nose - with less drag. Even then, they're using much larger openings.
NACA ducts require attached laminar airflow. Not great for the nose.
Required reading if you haven't seen it: https://hanchagroup.wordpress.com/2013/01/29/splitter-or-air-dam-which-design-is-best/
I guess I should mention the car has a dinky 63 HP engine with a stock Miata radiator. The car tends to run cold this time of the year 170-180F. The four little holes got the engine up to 215F in about five miles.
A few more holes added for the evening trip back to headquarters.
eventually I want to build a shutter type grill that opens and closes with electric motors.
So instead of the above drawing, perhaps a single opening that can open and close?
Remember that holes create a ton of turbulence, which means drag. I'd suggest one contoured bigger opening instead of lots of little openings.
In reply to Keith Tanner:
The link to the Miata air dam analysis was something I was looking at a few days ago. The full nose treatment with a splitter appears best for a high speed and looks cool but would that be overkill for street use with a top speed of 70 MPH?
Ah, you changed your username. Didn't know it was you.
Air is still there below 70 mph. Ask a cyclist
And look at the drag levels on the various noses - your real goal is low drag with enough cooling to keep the engine alive. I'd still be looking at addressing air evacuation, because that can help with downforce and drag and help you minimize your openings in the nose.
If covering up the radiator helps your engine come up to temp, I'd be looking to see if the thermostat is working.
RossD
UltimaDork
11/19/15 10:18 a.m.
DeltaP=C_o * p_v
- DeltaP is the total pressure loss (inches of water)
- C_o is the local loss coefficient
- p_v is the velocity pressure (inches of water)
p_v=[(velocity in fpm)/4005]^2

In reply to RossD:
......And this thread just went over my head.
Java230, the post by RossD is the effect of radiusing the inlet of a hole. The 'drag effect gets smaller as the radius to hole size gets bigger. Basically big inlet radius equals lower 'drag' or pressure loss.
To Tom's comment, the turbulence of having the holes may actually help with the flow distribution on the radiator face - better cooling at the cost of a little drag.
RossD
UltimaDork
11/19/15 10:38 a.m.
In reply to java230:
Oh you want more? Lets say he's only 33% efficient on making that 63hp. He's rejecting twice that to the radiator. Roughly equal to 28,000 btu/hr. Guess a 20°F air temperature rise across the radiator and we have around 1,250 CFM needed. Of course if the DeltaT is greater there can be less air flow.
(btu/hr) = 1.1(CFM)DeltaT
That's for sensible heat.
I found that an area the size of a license plate,12x6 or 72 sq.in. worked well on my ZX2SR.
The hive mind is trending toward a single opening...
So...
Version 2.0 is ready for this evenings trip back to headquarters.
I wonder if an old AC vw's thermostat would work instead of door lock motors. If you could find a way to make it get warm enough on the radiator, it could be used to force open a small flap in your closed off grill to allow air in.. simple mechanical actuation, no electrics
In reply to RossD:
Once I establish a suitable opening, can I decrease the size by including a bellmouth?
In reply to Keith Tanner:
The thermostat issue has been a constant battle with this car. Everything seems to run too cold. I finally punted and modified a small block Chevy unit.... it works but its still on the cold side.
Faster warmups plus less drag is sort of what I'm after.
Because of the pressure profile of the cooling system a full bellmouth will not get you much cooling advantage but will help the drag a little bit. The radius can be on the INSIDE of the opening and still get the benefit.
A lot of cars these days have grill shutters- but you really need to do a job making sure that they have a real aero benefit when closed.
Seems like your method of changing the surface would be better than having the shutters 6-8" in as the air still goes into the hole and deadheads.
RossD
UltimaDork
11/19/15 12:40 p.m.
In reply to El Cheapo:
I'm more of a duct work system kind of air analysis kind of guy, and even then it's something I don't do on a per 'edge' or per 'transition' basis, so hopefully I'm not neglecting some critical piece.
So if we use the above figure even though it's not completely accurate:
- r=0 (no entry radius) and d=3", we would see pressure loss of 1.26 inches of water (for 1250 cfm)
- r=0.25" and 2.5", we would see pressure loss of 0.63 inches of water (for 1250 cfm)
So just by decreasing a half inch of hole opening, and slapping on a 1/4" radius to the opening, we reduce the pressure drop by half. In this instance at least. There are a lot of things going on for a car compared to ductwork.
If your opening is 3" by 16" we get .333 square feet. Use the 1250 CFM (this number is more of a starting point than what the radiator is actually doing/needs) The speed of the air required is (1250/0.3333) 3750 fpm. That's about 43 mph for a full load situation. Use the hydraulic diameter D__h=4 A/P in place of the typical diameter for the above diagram. (A is area, and P is perimeter) and get D_h = 7.4"
- p_v is (3750/4005)^2 = .8799
- C_o is 0.5 for no radius which translate to a DeltaP of 0.44 inches of water
- C_o is 0.31 roughly for a 0.25" radius which translate to a DeltaP of 0.27 inches of water
Thanks Ross! That is a lot to absorb but very interesting.
In reply to mad_machine...The AC VW thermostat would be perfect for an active system but I forgot to mention the car has a fully functional air conditioning.
Just for grins, I took the car out for a short run at lunch time. I captured a datalog for inquiring minds. Probably something like an 8 mile trip. The local temperature is 50F
The yellow squiggly line on top is the CLT. The first part of the datalog is traveling west into a head wind. The middle is where I turned around and the rest is traveling east with a tail wind.
Looks like almost no thermostat cycling. Usually I'll see some bumps. I think I'll close the hole a bit more and see what happens this evening.
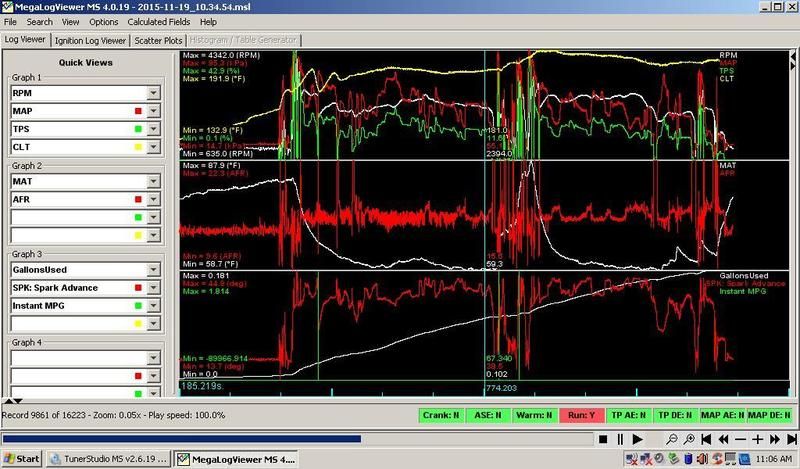
I would not expect the thermostat to cycle. It's there to make sure that the engine is warm enough, not to keep cold.
What you want to avoid is the fans turning on and off. A 191 F max is pretty good.
In reply to alfadriver:
The cooling fan on this car is controlled by a toggle switch. Usually I don't need the fan but the folks at Tim Hortons seem to take forever to fix a cup of coffee. Don't get me started on that rant...
Anyway the datalog was without the fan or heater blower running and it looks pretty good. Tonight i'll get a file with the heater on.
In reply to El Cheapo:
You are running MS, right? You should be able to make it control the fan. That way you don't have to worry about it while waiting for your morning coffee and doughnuts.
That also lets you turn it on when the a/c is on.