Long story short, I want to drill holes in a fan shroud to fit a fan motor that doesn't have exactly the right mounting pattern. The stock shroud has metal inserts for the screws to go through (they don't thread into the shroud, they pass through and clamp the motor onto the shroud). Would it be a bad idea to drill new holes in the plastic and use those? If not, should I make the holes bigger than the screw so that the threads don't touch the sides of the hole, or slightly smaller so that they thread in?
Edit: BTW this radiator fan will be going on an offroad vehicle, possibly long-term.
Can you use bolts and back them with big washers?
what about speed nuts....???
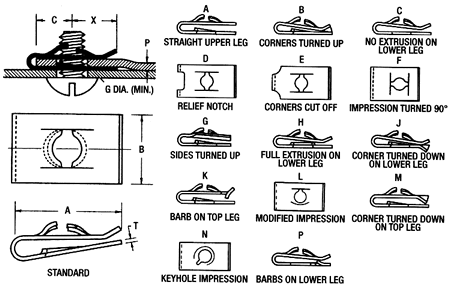
Woody wrote:
Can you use bolts and back them with big washers?
Actually no, the threaded part is in the motor housing. So you put the screw through the shroud into it. I could put washers on either side of the shroud.

What about a 'griff-nut' or a 'flower-nut'? I see both pretty regularly at hardware stores.
oldeskewltoy wrote:
what about speed nuts....???
Something like this might work, I only have 1 layer of material to work with though.
Edit: And it would have to be bigger than the screw so it doesn't thread in, the screw has to pass through the plastic to thread into the motor housing.
rcutclif wrote:
What about a 'griff-nut' or a 'flower-nut'? I see both pretty regularly at hardware stores.
Same problem as above, I should have mentioned that the screw threads into the motor housing in my first post.
GameboyRMH wrote:
oldeskewltoy wrote:
what about speed nuts....???
Something like this might work, I only have 1 layer of material to work with though.
Edit: And it would have to be bigger than the screw so it doesn't thread in, the screw has to pass through the plastic to thread into the motor housing.
This is what they normally use on the splash guards in the wheel wells on f 150s fyi.
Dave
New Reader
12/8/14 12:18 p.m.
Metal zip ties can work for stuff like this.
I have some metal zip ties but I don't think there's any way I could mount the fan with them. These fan mounts are just slightly different to what I need, so I'll be drilling holes close to the originals (almost like a 4x100+4x114 spacer).
If the bolts/screws aren't threading into the plastic I see no reason this wouldn't work just fine. As in, passing through the plastic and threading into something else.
You might experience some cracking over time. A washer on either side would help prevent that.
OK I'll drill the holes oversized and put washers on it. Gotta get my Samurai running and I don't really have any money to spend on it. A shop might have the proper replacement motor in with their next shipment, I want to get a new motor in there that won't give me trouble for a long time.
Heat up an awl or a Phillips screwdriver to melt holes through instead of drilling. That way you build up a thicker area surrounding the hole to resist cracking.
Using a thinner instrument (small screwdriver or just the tip of the awl and "reaming" around will give you a nice, thick area built up around the hole.
(Ok, that last part made me miss my wife
)
ebonyandivory wrote:
Heat up an awl or a Phillips screwdriver to melt holes through instead of drilling. That way you build up a thicker area surrounding the hole to resist cracking.
Using a thinner instrument (small screwdriver or just the tip of the awl and "reaming" around will give you a nice, thick area built up around the hole.
(Ok, that last part made me miss my wife
)
I like this idea. The metal bosses are likely there to keep the screw from crushing and fracturing the plastic when it is tightened down.
ebonyandivory wrote:
Heat up an awl or a Phillips screwdriver to melt holes through instead of drilling. That way you build up a thicker area surrounding the hole to resist cracking.
Using a thinner instrument (small screwdriver or just the tip of the awl and "reaming" around will give you a nice, thick area built up around the hole.
(Ok, that last part made me miss my wife
)
Now that you mention it, last time I tried this (to make a hole for a switch in a dash) it made a pretty serious amount of...uh...sleeving...around the hole. Maybe that would be good in this case. 
In reply to GameboyRMH:
Sleeving! Yes!
It always happens when I do stuff like that and I have to grind/sand it off but this would just be a "happy accident".
OK well I half-burned and half-drilled the holes (my plastic-melting soldering iron was dead, needed to use a nail heated with a candle) and then just put the screws in because the screw heads already took up as much surface area as any washer could. The new motor's way more powerful, guess I'll see how it holds up tomorrow.
In reply to GameboyRMH:
I hope it holds up for ya. I always root for a Samurai-guy!
GameboyRMH wrote:
Woody wrote:
Can you use bolts and back them with big washers?
Actually no, the threaded part is in the motor housing. So you put the screw through the shroud into it. I could put washers on either side of the shroud.
If it threads into the MOTOR, just do it to it!
The fans in my Mazda are from a 300M. Well, two 300Ms. When one motor goes bad, you replace the fan/shroud assembly. Happened to have two assemblies with one bad left-side motor each, so I swapped the good right from the one with a broken shroud into the other one. The bolt patterns are different for some weird Mopar reason. One bolt lined up, the other two I had to redrill or egg out. That was forever ago and no problems yet.
I rallycross the everloving E46 M3 out of the car, which is why I needed such beeftacular fans. I break radiator mounts but the fans are just fine.
Drill the holes by spinning the drill bit backwards. Won't crack the plastic that way. The hardware store should have metal sleeves and rubber washers, maybe even rubber bushed sleeves.
Once the sides of the drill bit into the plastic, it went through like butter. No problems getting to work this morning, which included driving on some bad roads at near-highway speeds. The new fan can drop the engine temp much faster.