Ok I fell into a hole. My brain hurts, but I think I've made a google sheet that simulates a swing axle rear suspension.
Ploting the intersections and figuring out pivot geometry is "easy". Except Google Sheets is not as flexible as MS Exel for making charts. To make a XY chart in Google sheets each "series" has to be a different column, BUT different columns cannot reference the same "X" values they have to have their own X values, so your Chart data input ends up with this silly waterfall look.
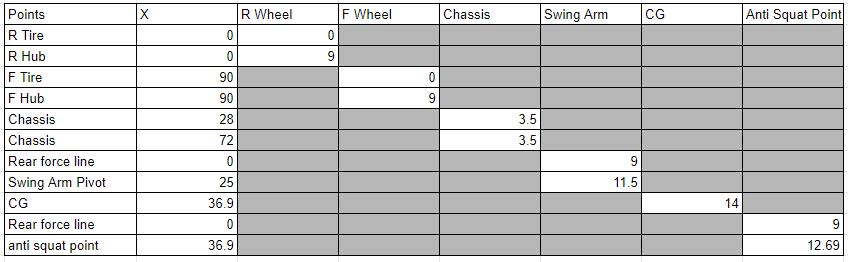
which makes this chart
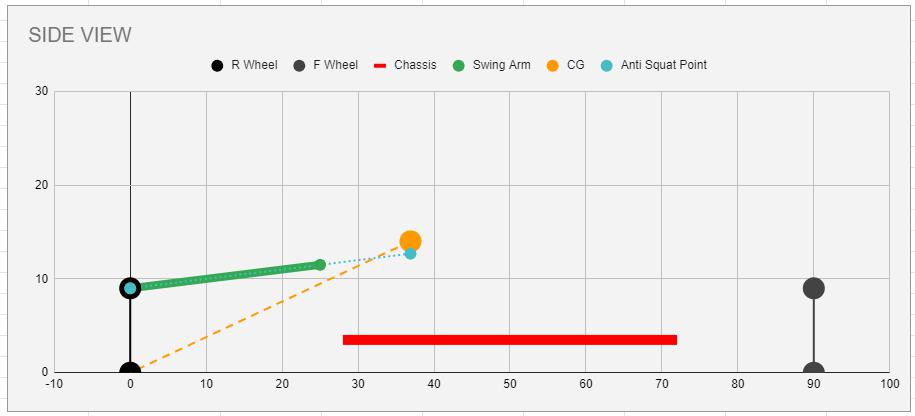
It took me a while to get my arms around "Anti-squat". I will start with this is my understanding and I easily can be wrong (Same thing with all the math in this spreadsheet). If you figure out that I am please tell me.
I will try to draw something to communicate but this chart does a decent job. So Imagine that we are accelerating the car. Lets assume for a minute that the car is a rigid body with no suspension. The rear tire pushes on the ground and the ground pushes back. This force acts on the vehicle CG through the orange line. This force from the ground through the orange line has both a horizontal and vertical component because it is a vector at an angle from the tire to the CG. The CG acts on the rear tires along this vector in the direction opposite the acceleration. As this is the rear tire of our vehicle Horsepower makes us go Right, and the CG tries to move left pushing back with traditional F=MA acceleration, but also DOWN at a magnitude determined entirely by the geometry of the vehicle. This downward force is ONLY due to acceleration, and it is in addition to the static force the CG applies due to gravity. In a fully rigid car (Say FDAT 2020) this doesn't matter, this force just goes into stress in the chassis along the orange line (remember car is rigid) and the vertical force UP from the ground perfectly balances the DOWN from the CG.
Ok so now our vehicle has suspension. This downward force caused by Acceleration acts on the suspension. We have to think about the forces in the chassis in 2 ways; 1. The force the CG imparts on the ground (This force is along the Orange line with Horizontal and vertical components); 2. The force the suspension imparts on the CG. This force has to EQUAL the force along the Orange line, however the way the suspension imparts it on the chassis is a function of geometry.
This is where the n line from Driven5s charts plays a roll. If we could have our suspension impart a equal UPWARD force that matches the downward force due to acceleration WITHOUT using the springs we could have a rear suspension that would not compress on acceleration. By orienting the suspension linkages to ensure that the force from the wheels (Through the Green line on the chart) matches the angle of the orange line we could make this happen. Different suspension types handle this differently with the biggest difference being how the torque driving the wheels is reacted. For chassis mounted differentials (Dual A-arm IRS, Swing axle, DeDion, Transaxle, Multilink) there is no torque loading into the suspension. The force from the ground acts on the suspension at the wheel bearing. For vehicles with suspension mounted differentials (Solid axles with any kind of linkage) the torque reaction results in the force coming into the chassis at the ground.
Look back at our chart. For a swing axle this means that that Green line would have to be parallel to the Orange line to get to an equivalent upward force. In fact that is exactly what 100% anti squat is.
So in the chart you can see that the green line is in fact not parallel to the orange, so we do not have 100% antisquat. By math we have approximately 25%, which means that 25% of the downward force due to acceleration is reacted by the upward force from the swing arm. The remaining 75% has to be balanced so it would go into compression on the springs. If the forward pivot was lower such that the green line was Horizontal we would have 0% antisquat and 100% of the downward force would go into the springs. You can imagine if the swing arm pivot was BELLOW the hub and therefore declined the suspension would introduce a DOWNWARD force on the chassis, which would be called "Pro-Squat" and would result in a >100% force being sent to the springs.
As an aside solid axles are crazy superior to IRS for "squat" geometry. Since the force comes along the ground through the "Virtual Swing Arm" instant center a 4 link or Multi link Solid axle can have 100% anti squat and still have a very low Instant center. A IRS design always winds up with a very high instant center, which results in other bad compromises for handling so antisquat use is limited.
Ok so I rambled a lot and I haven't even gotten to the rest of the sheet.
Using very basic geometry I layed out the Top and Rear view of the swing arm to figure out where the pivots would be. These are entirely based on inputs that set up the geometry. I selected the outer swing arm pivot height/width and position along the wheelbase. The desired VSAL length is selected and roll center height, and the spreadsheet calculates and plots the geometry, picking the inboard pivots and I get these charts.
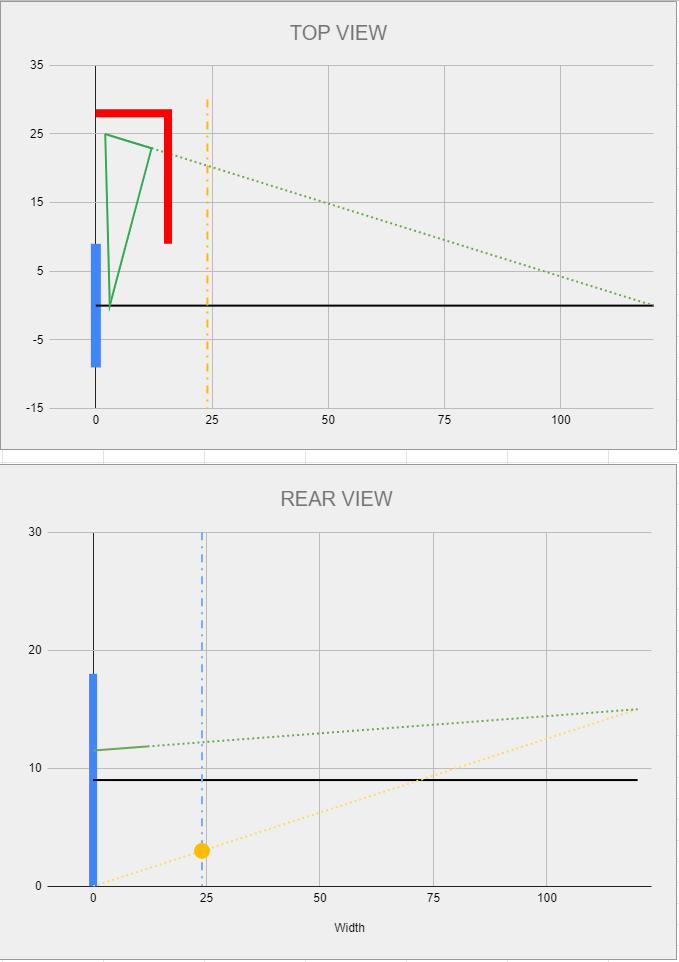
This is what the overall sheet looks like
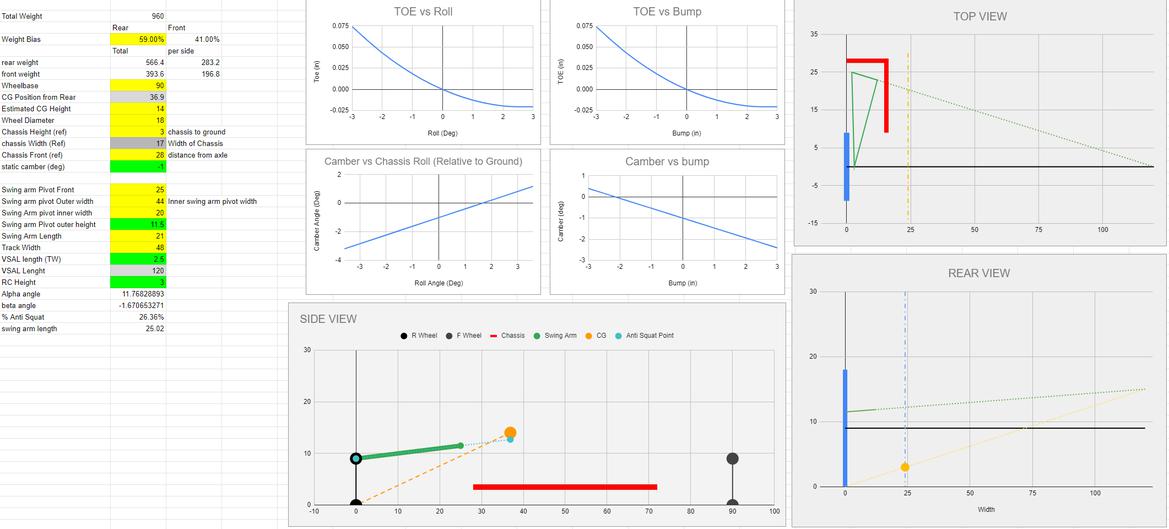
The next step was the hard part that I spent way to much time over the past 3-4 days working on. Looking at the Top and Rear view you see that the swing arm is not perpendicular to the car in either view. I called these angles Alpha and Beta and they are super annoying and I hate them. Determining the side view geometry and anti squat is the easy part. Beyond that it got wierd and I probably made errors.
I was primarily interested in evaluating camber/toe. I know that Susprog3D can do this. I don't own it. I can't validate how they did their calculations. I searched for a different free alternative and I couldn't find one so I made one. I initially tried the calculations shown on the following link: http://www.e30sport.net/tech_articles/susp-tech/rear_curves/index.htm
This gentleman did a good amount of work and produced formulas that consider the top view angle (frustratingly I called it Alpha and swingarm rotation Theta and he used them backwards) which for an E30 are apparently 12-15 deg. His camber equation worked fine. I modified it to include the "beta" angle from the rear view. A3 is Swing arm Displacement, F1 is the Alpha angle, H1 is Beta.

This equation produces logical results for camber for Alpha angles from 0-90 degrees and for Beta angles from 0-90 degrees.
So camber was settled (ish, again more at the end). Then it was time for Toe and it was horrible. The simple equation in the E30 evaluation did not work. If I set the alpha angle to 0 or 90 it did not produce logical results. It may of done a fine job estimating at 15 degrees but I wanted flexibility.
I'm not going to attempt to explain in detail how I developed the equation. Eventually I will re-draw my geometry that led to it's development but it's basic geometry. The basics of the Toe equation is that as the arm rotates the hub moves up and in. The wheel is fixed relative to the swing arm so it rigidly rotates and intersects the pivot axis at the same point irregardless of travel when viewed from above. Geometric evaluation can then be made comparing the "0" travel line (which is at static toe of 0) to the horizontal plane projection of the post travel line which would now be at a more open angle. The location of this projection can be determined based on the lengths and angles and you get this doozy of an equation.. I applogize for the aweful notation here.
Here C11 is swing arm length, F11 is the Alpha angle, A16 is vertical displacement, I11 is Beta. And then there is B22.. OH B22.
I got my equations all done and developed curves then had a realization. The Swing arm is not level at 0 travel. It is at completely random angles. Sure the asumption of it being level is probably fine but I wanted more accuracy and flexibility. So my strategy was to alter the analysis to determine the Swing Arm length from the 3D geometry of the inboard, outboard pivots and hub location. Then from that length and the initial vertical distance from the pivots to the hub at static ride height, I could detemine the initial Theta angle that the swing arm has at rest. This rotation angle was subtracted from the equations above and the results "zerod" to 0 travel by subtracting the 0 travel equation result from itself. This rotation is B22.
To calculate swing arm length I determined the length of the 3 sides of the triangle made by the swing arm using the 3D pathagorean theorem (Inner, outer, hub vertexes). I then used Heron's formula to calculate the Aera of this triangle. I then was able to divide 2* the area by the length of the side that represented the rotation axis.
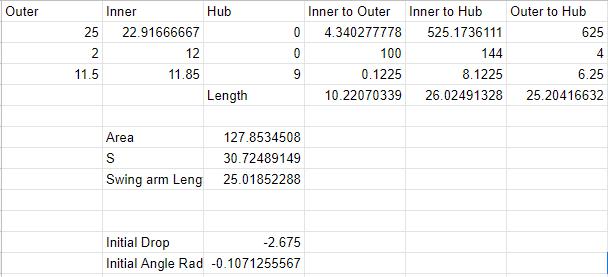
So the bad toe equation from earlier became this:

The result of this doesn't impact camber, as camber is a very linear function for a swing arm, but for Toe it has a strange result. Since the arm is not level at 0 ride height the result is that the curve Shifts to where 0 toe change occurs when the swing arm is level. Since I "Zero" toe to 0 travel you can see that the toe actually has "toe in" for 2" of bump before being to have "toe out". Roll toe is simply converting the "bump" displacement to a roll angle based on the Track width.
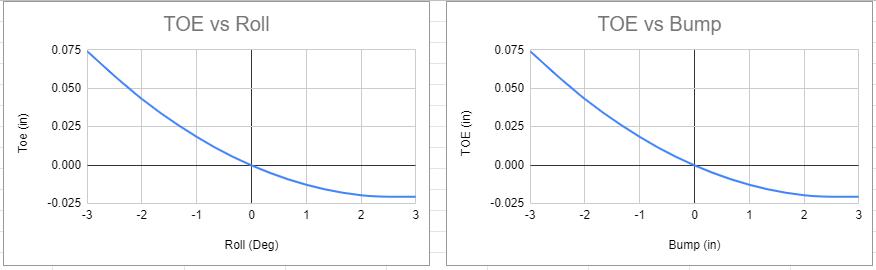
So that is the spreadsheet I have developed. I used a lot of input from the forum and some google searching. I know this is another one of my overly rambly super technical posts. I'm sure almost no one will follow it. I'm just hoping someone can take something away from it, if nothing other then solving frustrating problems with lots of math you forgot from highschool/college.
I think this maybe accurate. We will tweak on the numbers some before we build.
For the true masochists the spreadsheet is available here.
https://docs.google.com/spreadsheets/d/16ly8wVNajQMgKwzJaJ4sKamicb4A4F7TA3pK40vOS8s/edit?usp=sharing
PLEASE FOR THE LOVE OF FSM MAKE A COPY ON YOUR GOOGLE DRIVE. NO this isn't the only one, I have backups. I believe you will be able to edit if you save a copy. I currently have it "View Only" I believe you can download it. I have not "protected" any cells. So It would be pretty easy to mess it up.
But, the chart inputs all auto populate as does all the calculations. If you just deal with the colum of green/yellow texts on sheet 1 you should be able to play with it and make it work for other cars. Different Track widths, tire diameters, swing arm pivot locations, CG's, Wheelbases all should work and give you camber/toe/antisquat.
So I guess now is about the time we decide to do Dual A-arms or something not Semi Trailing Arms.