buzzboy
SuperDork
9/5/22 10:18 a.m.
I'm to a point in my engine swap where it's time to build engine mounts. I've made the engine side pads and I've got the engine hanging in the car on my hoist with a leveler. I've got the transmission jacked up. Now what?
When I google about setting engine angle and building mounts people love arguing about angles. When I google about engine swaps people gloss over the part I want to see.
How do you dial in the exact placement and hold the drivetrain in place while building mounts? Does anybody have photos of this part? Are we doing wood blocks? All thread? Ratchet straps? I feel like a moron not getting this simple thing but my brain doesn't like working in 3 dimensions sometimes.
FWD or RWD?

For FWD I set a straight edge across the top of the fenders, removed the upper intake manifold so I had a flat surface, and used a digital angle meter to make the two numbers match.


Then for the front/back alignment I tied a string across the top of the strut rods, and measured from two points that were equal on the engine. In my case, I used the front and back of the fuel rail


For the 3rd angle (engine leaned forward or backward) I used the intake manifold flange again.
For RWD I'd imagine it's similar, probably easier. Front to back in the engine bay is dictated by clearance, or if you're trying to use an existing driveshaft. Side to side you probably want it centered, unless you need to offset it for clearance somewhere. The angle of the engine is easily changed by shimming the transmisison mount so that's probably the easiest.
Hopefully your engine has a flat surface parralel to the crank. I'd use intake manifold flanges, carb flanges, oil pan rails (assuming they're straight), or straight edges across valve covers. For the car use frame rails, fender lines to find centers. Might be worth tossing a tape measure across the hood openings to see if the car is resonable square first.
buzzboy
SuperDork
9/5/22 11:00 a.m.
Rear wheel drive.
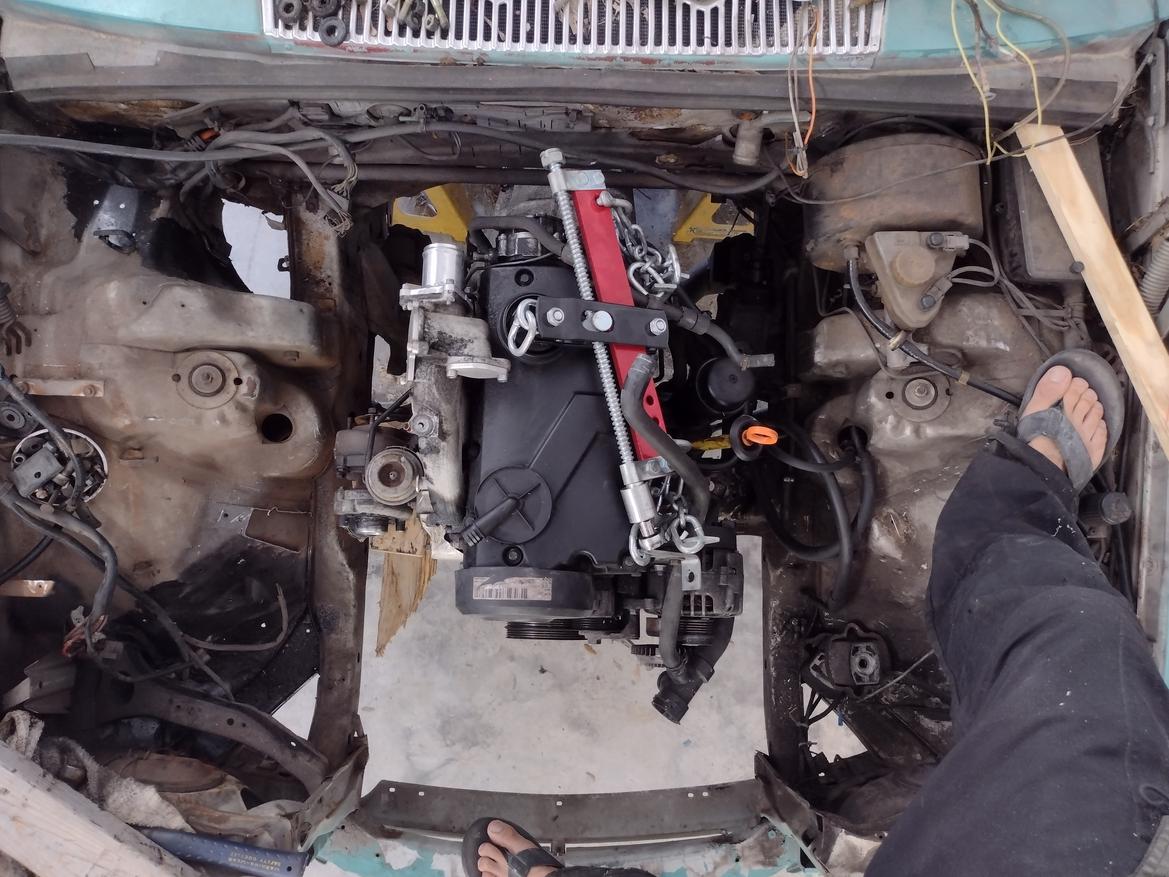
I know how to measure the angles. I've read plenty about what angles I need to keep my u-joints happy. I know how to position the engine in the bay.
What I'm missing is how to get it into that spot and hold it there while building the mounts.
Floor jack, wood shims, ratchet straps. Ive done it that way for four or five builds now.
Its like a monkey berkeleying a football while building a ship in a bottle.
I wouldn't stress too much about engine angle with EFI. I mean, don't go crazy, but there isn't much to worry about. Oiling works fine if you're driving up or down a 10% grade which is about 9 degrees, and the main reason that carbureted cars had a specific angle was because the carb wanted a certain angle so it didn't slosh the fuel away from the jets during acceleration or braking.
The real critical part is the driveline angle. Match the pinion angle and you're probably spot on.
JBinMD
New Reader
9/5/22 3:05 p.m.
First, always be vigilant about NEVER putting any body part where it can be injured if one of your temporary engine supports fails. Also, if using any kind of hydraulic jack to support part of it (engine hoist, floor jack, bottle jack, whatever) always plan for it to slowly leak down, like by putting a jack stand or blocks of wood just below a sturdy/stable part of the engine.
With that said, you two ways of doing it are either 1) from above with an engine hoist, or something like a 4x4 across the strut towers with ratchet straps or all thread pulling both sides of the engine up, or 2) from below with a jack/jack stands/blocks of wood and shims supporting it. IMO the "from above" method is the easier one to keep everything stable and to adjust height with long bolts/threaded rod.
I have a stack of foot-long 2x4 pieces I've been using for years for stuff like this. Just buy a couple of studs and cut 'em up. They'll help you build engine mounts, exhaust systems, suspensions, whatever . . .
I use a couple of modified leveling screw jacks. Typically one on the tail shaft of the trans and then I support the oil pan with a modified one with a large lifting pad and use shim stock to get the side to side level correct, and all your front / back & height is done with the screw jacks. Works for me. Done it ona plethora of cars, including completed painted ones getting re-powered.

FWD it won't matter so much, other than to get the diff output cups in the right range so you don't have an extreme axle angle. Oh and getting the hood to close is pretty important. I've leaned a few motors forward or back to help and it's not caused secondary issues.
In reply to GaryC83 :
That's a great idea, thanks for posting it.
SV reX
MegaDork
9/6/22 11:14 a.m.
Bolt a small piece of angle to an available threaded hole or port on the engine. Remove a bolt if you have to.
Then clamp the angle to any fixed point on the car.
Add 1 or 2 more.
The clamp will let you adjust small differences to keep the engine where you want it.
Once you are happy with the positioning, build your permanent mounts.
buzzboy
SuperDork
9/6/22 11:50 a.m.
Ahhh, thank you friends. I'm formulating a plan with the junk I keep in my garage. Screw jacks... wish I had a set.
This will answer your next question.... how to match the pinion angle to the output angle. https://www.youtube.com/watch?v=Idk3BVDVHq4
They need to be parallel, but not a straight line. That is to say, if the pinion points 2 degrees up, the transmission output needs to point 2 degrees down. If you get it installed and find that there is zero angle at the U-joints, you'll likely want to find a way to raise pinion/lower transmission, or lower pinion/raise transmission. You want between 1-4 degrees at the U-joint.
I'm different. When I build a chassis, I work those things out before I cut a chunk of metal. Slide things around on the table (. I used to work off the floor but old age has stopped that.).
I shim everything. That way I can check and double check everything before I fabricate anything
IRS is different from a live axle.
SV reX
MegaDork
9/6/22 7:50 p.m.
In reply to buzzboy :
Those screw jacks are easily available in any RV supply, and they are inexpensive.